
Выборгский Судостроительный Завод
---
Оригинал взят у
a_beskotti в Выборгский Судостроительный Завод

Увидеть Выборг с необычной точки, побывать на борту строящегося ледокола, увидеть, как собирают корабли и суда, а так же этапы этого строительства, познакомиться с представителями редких профессий- всё это ждало участников проекта “Закулисье редких профессий”, который уже не первый год открывает двери самых разных предприятий, заводов и фабрик.
На этот раз мы отправились на http://vyborgshipyard.ru/ru
В прошлом году я побывал на Балтийском Судостроительном заводе, где собирают корабли и суда по полному циклу: от разработки, создания комплектующих, до передачи заказчику, что отличает завод от верфи, где суда лишь собираются из готовых блоков.
Отчет о том памятном событии здесь:
Было интересно сравнить два завода, тем более, что с 2012 года они входят в одно Акционерное Общество: “Объединённая судостроительная корпорация”.
2.

Сам Выборгский судостроительный завод был основан в 1948 году.
За это время завод построил более 210 судов различного класса и назначения.
Среди них и ледоколы, и суда ледового класса, и суда снабжения, и рыболовные траулеры. Полный список можно посмотреть здесь: http://vyborgshipyard.ru/ru/products
Особой гордостью завода стали буровые платформы, их изготовлено девять.
3.

И единственный в мире http://sea-launch.info изготовлен так же на Выборгском судостроительном заводе! Для меня этот факт был приятной неожиданностью!
Раньше завод был сильно ограничен в размерах судов, ведь его сухой док имеет ширину всего 18 метров.
4.

Но к июлю 2013 года завод сам для себя постоил полупогружную баржу-стапель размерами 130Х35 метров и теперь большинство ограничений по ширине сняты.
5.

Всё это сейчас производит завод, который в 90-е годы прошлого века фактически выживал на заказах по ремонту судов. Отличный темп развития!
При этом, всё разнообразие работ обеспечивается персоналом, численностью около 1700 человек! Повторю: это и разработка, и изготовление всего, из чего будет сделано судно и того, что будет на судне, а так же сборка и обслуживание самого завода, внешние контакты, поиск заказов, развитие.
О людях здесь, кстати, заботятся. И работа устроена хорошо, и своя медицинская часть с медиками узких специальностей, и обучением персонала занимаются, и школьников-студентов подбирают, готовят. А для иногородних даже большую часть проезда к месту работы компенсируют. Да и зарплата рабочего в среднем составляет 52 тысячи рублей.
Кстати, по согласованию с пресс-службой, можно организовать экскурсию для групп учащихся!
По территории завода нас провезли на автомобиле, ведь он занимает площадь более 44 гектар. Потому-то здесь очень много велосипедов, рабочие предпочитают передвигаться по заводу именно на них.
6.

Я очень хотел познакомиться с представителем профессии “чертёжник плаза”. Но эта профессия теперь стала действительно редкой, ведь на плазе чертёжник в натуральную величину вручную переносил все линии из чертежей на металл. Все изгибы и углы. Сейчас это делает компьютер.
Деревянные шаблоны направляются в цех, где на больших прессах заготовке придаётся нужная форма.
7.

Некоторые из прессов просто огромные
8.

Некоторые поменьше
9.

с соответствующей оснасткой
10.

А для закруглений большого радиуса используется вальцовочный пресс.
Но прежде, чем гнуть металл, его надо подготовить. Его обрабатывают на дробеструйном аппарате с помощью специальной стальной дроби, которая пролетая с большой скоростью, отбивает всю ржавчину и загрязнения.
11.

Сама дробь:
12.

Далее листы металла направляются на разметку и резку. Заместитель начальника корпусного производства Роман Медведев рассказал нам, что большинство разметочных и разделочных операций автоматизировано.
13.

Вот такой аппарат способен самостоятельно разрезать металлический лист по заданным координатам.
14.

При необходимости, он и фаску снимет, для того, чтоб было легче готовить детали к сварке.
15.

Прямолинейные разрезы можно делать и аппаратом попроще: этот полуавтомат плазменной резки может самостоятельно двигаться по проложенным направляющим.
Одновременно разрезая и снимая фаску.
16.

Деталей, кстати, огромное количество, я не представляю, как рабочие с ними разбираются, как находят, где и что лежит! Хоть я и сам работал на заводах, но у нас, всё же, деталей было куда меньше.
17.

Вот здесь документация лишь на маленькую часть судна
18.

Постепенно все детали передаются на участок сборки.
19.

Сварщиков на заводе много. Ответственная работа, от прочности и точности сварки зависит, как в последующем состыкуются крупные модули при сборке судна на стапеле.
20.

Видов сварки, кстати, много. И обычная дуговая, и сварка полуавтоматами, и в защищённой среде, и под флюсом.
21.

А вот что это за сварка, при которой используется такой специальный костюм и маска- я не спросил. Кто-нибудь знает, для чего это используется?
22.

Через некоторое время цеха опустели, настало время обеда. Тишина!
23.

Работа работой, а обед по расписанию!
24.

Краны и тали застыли, тоже отдыхают.
25.

А мы фотографируемся на фоне опустевших цехов.
26.

Пока мы рассматриваем всё, ходим по цехам- время пролетает незаметно и предприятие вновь оживает, пора снова приступать к работе.
27.

Постепенно вырастает часть корпуса судна.
28.

Собрана, проверена-- добро пожаловать на окраску.
29.

Швы модуля не просто прокрашиваются,они в обязательном порядке проливаются специальной краской, чтобы снизить скорость коррозии.
Масштабы покрасочной камеры не идут ни в какое сравнение с автомобильными!
За окрашенным модулем приезжает специальная многоосная машина- трейлер.
30.

Возить может грузы огромного веса и размера, его водитель, Владимир Михайлов, говорил про 300 тонн и 12 метров в высоту!
31.

Водителей таких машин очень немного. Тоже редкая профессия. Кабин у такой машины две, с обеих сторон, для удобства маневрирования и чтобы не разворачиваться.
О своей работе, если она любимая, можно рассказывать долго и удивлять слушателей!
32.

Вот и эту часть корпуса скоро повезут на сборку. Строится ледокол “Андрей Вилькитский”
33.

Тросы.
34.

По цеху, кстати, для удобства перемещения модулей проложена железная дорога.
35.
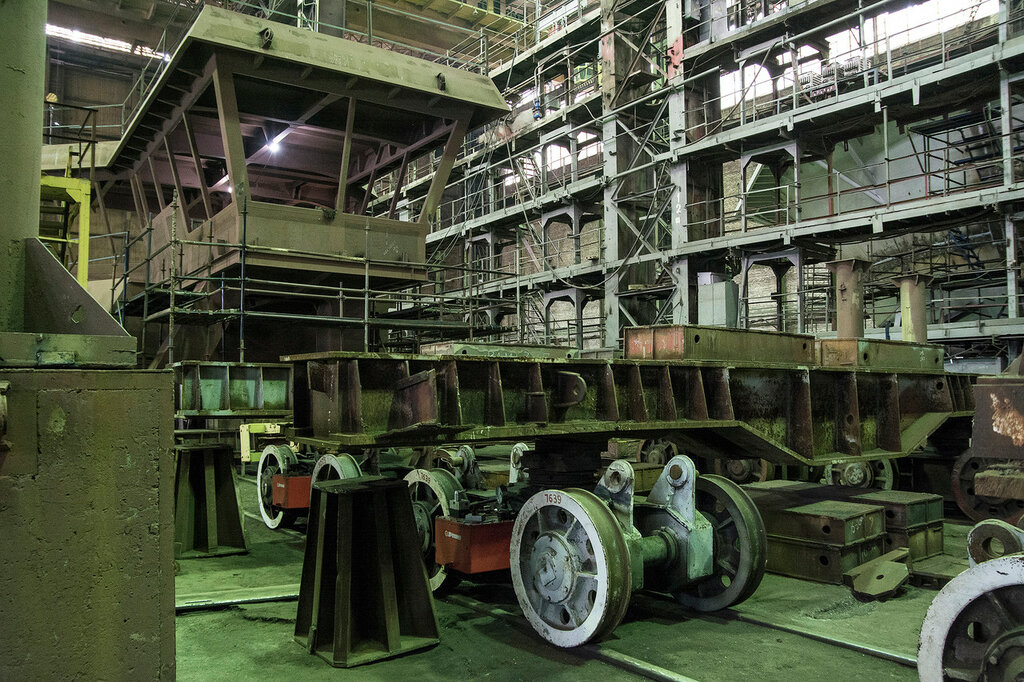
То же судно, вернее, его часть, с другой стороны. На переднем плане кранцевая защита
36.

Очень хотелось посмотреть, как вручную плетётся эта штука- кранец!
37.

Дальше наш путь, в соответствии с технологической цепочкой, лежит к сборочной площадке и причалу. На плавучую полупогружную баржу-стапель пройти возможности не представилось, зато нам разрешили подняться на борт строящегося ледокола Александр Санников, порт приписки Мурманск.
38.

Ледокол весьма большой по своим размерам, а вот на его борту проживать и работать смогут всего 36 человек, настолько велик уровень автоматизации и механизации рабочих процессов.
39.

Бдительная охрана не ограничивается пересчётом “по головам”, записывает прибывших. На входе и выходе работает досмотровая рамка. Для безопасности, говорят нам.
40.

Поднимаемся на борт. К ледоколу тянется множество электрических кабелей, сварка продолжается и на уже спущенном на воду судне.
41.

Провода везде, надо ступать с осторожностью.
42.

Здесь заканчивается монтаж главной силовой установки. Чтобы всё это собрать правильно, надобно представлять все чертежи в своей голове, представляете сложность работ?
43.

Ещё одни вид на помещение ГСУ
44.

Коридоры. Конструкция судна предусматривает, что моряки минимум времени будут проводить на “свежем воздухе”, потому, что температуры в северных широтах едва ли можно назвать комфортными большую часть года.
45.

Для этого даже палубу, на которой находятся якорные и швартовые лебёдки, обычно открытую всем ветрам, закрыли щитами.
46.

Выданные нам каски пару раз послужили по назначению и уберегли головы от повреждений.
47.

Поднимаемся на уровень выше. Здесь вертолётная площадка, способная принимать вертолёты МИ-8.
48.

Смотрим, фотографируем, обсуждаем.
49.

Неплохой вид на грузовой порт Выборга. За подъемными кранами видны башни Святого Олафа и Часовая.
50.

А это вид на завод.
51.

С другого борта- вид на Выборгский залив и бухту Ховенлахти
52.
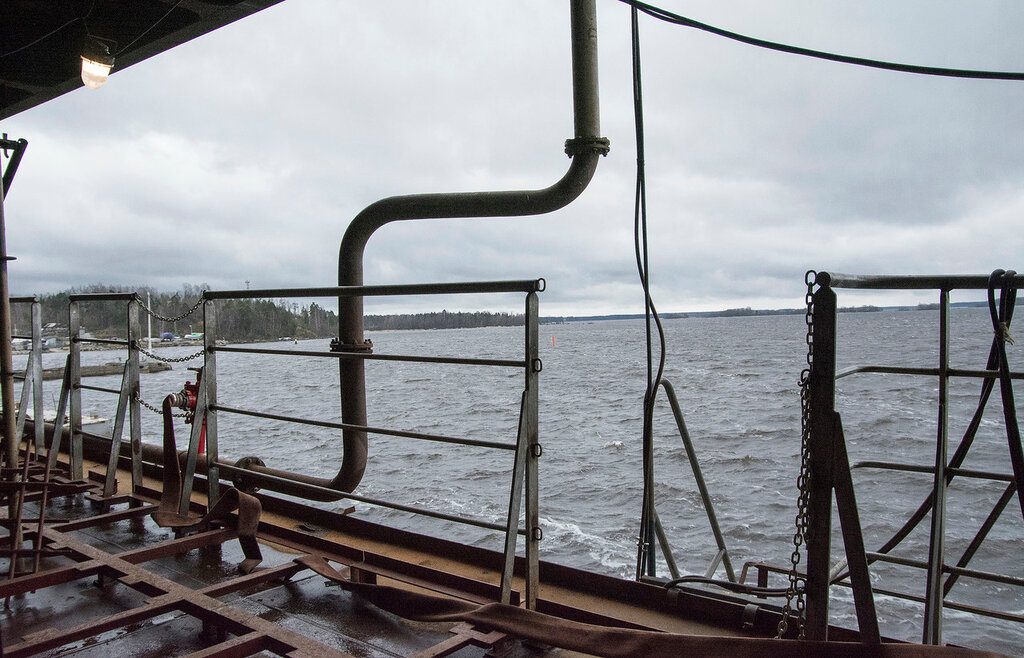
Ещё один коридор и пора спускаться, чтоб не мешать производству работ на судне.
53.

Ну а как же без котиков, правда?
54.

А это наша команда в сопровождении Анны Панфиловой, специалиста по связям с общественностью, очень симпатичной и приятной девушки. Котика увидели? :)))
55.

Знакомьтесь: азиподы. Или Винто-Рулевые Колонки. Внутри этой гондолы расположены высокомоментные судовые электрические двигатели, передающие крутящий момент непосредственно на винт. Отказ от промежуточных валов и подшипников существенно упрощает и облегчает конструкцию.
56.

Вся эта гондола подвешивается под днищем судна на подшипниках и может вращаться на 360 градусов вокруг своей оси, что помогает судну многократно увеличить манёвренность по сравнению с судами классической компоновки. На Александре Санникове будет установлено четыре таких азипода.
57.

На этом снимке видно, что ледокол стоит у причальной стенки с дифферентом на нос. Передние азиподы установлены и судно загружают балластом, чтобы приподнять корму, на которую будут устанавливать азиподы прямо с воды по уникальной технологии.
58.

Ну, а нам пора возвращаться из Выборга в Санкт-Петербург.
Выборгский судостроительный завод оставил самое приятное впечатление, даже холодная погода со снегом и дождём не смогла испортить нашу встречу!
Хотелось бы вернуться через некоторое время, увидеть, как воплощается в жизнь очередной большой проект в области судостроения. Уверен, таких проектов у завода будет много!

Увидеть Выборг с необычной точки, побывать на борту строящегося ледокола, увидеть, как собирают корабли и суда, а так же этапы этого строительства, познакомиться с представителями редких профессий- всё это ждало участников проекта “Закулисье редких профессий”, который уже не первый год открывает двери самых разных предприятий, заводов и фабрик.
На этот раз мы отправились на http://vyborgshipyard.ru/ru
В прошлом году я побывал на Балтийском Судостроительном заводе, где собирают корабли и суда по полному циклу: от разработки, создания комплектующих, до передачи заказчику, что отличает завод от верфи, где суда лишь собираются из готовых блоков.
Отчет о том памятном событии здесь:
Было интересно сравнить два завода, тем более, что с 2012 года они входят в одно Акционерное Общество: “Объединённая судостроительная корпорация”.
2.

Сам Выборгский судостроительный завод был основан в 1948 году.
За это время завод построил более 210 судов различного класса и назначения.
Среди них и ледоколы, и суда ледового класса, и суда снабжения, и рыболовные траулеры. Полный список можно посмотреть здесь: http://vyborgshipyard.ru/ru/products
Особой гордостью завода стали буровые платформы, их изготовлено девять.
3.

И единственный в мире http://sea-launch.info изготовлен так же на Выборгском судостроительном заводе! Для меня этот факт был приятной неожиданностью!
Раньше завод был сильно ограничен в размерах судов, ведь его сухой док имеет ширину всего 18 метров.
4.

Но к июлю 2013 года завод сам для себя постоил полупогружную баржу-стапель размерами 130Х35 метров и теперь большинство ограничений по ширине сняты.
5.

Всё это сейчас производит завод, который в 90-е годы прошлого века фактически выживал на заказах по ремонту судов. Отличный темп развития!
При этом, всё разнообразие работ обеспечивается персоналом, численностью около 1700 человек! Повторю: это и разработка, и изготовление всего, из чего будет сделано судно и того, что будет на судне, а так же сборка и обслуживание самого завода, внешние контакты, поиск заказов, развитие.
О людях здесь, кстати, заботятся. И работа устроена хорошо, и своя медицинская часть с медиками узких специальностей, и обучением персонала занимаются, и школьников-студентов подбирают, готовят. А для иногородних даже большую часть проезда к месту работы компенсируют. Да и зарплата рабочего в среднем составляет 52 тысячи рублей.
Кстати, по согласованию с пресс-службой, можно организовать экскурсию для групп учащихся!
По территории завода нас провезли на автомобиле, ведь он занимает площадь более 44 гектар. Потому-то здесь очень много велосипедов, рабочие предпочитают передвигаться по заводу именно на них.
6.

Я очень хотел познакомиться с представителем профессии “чертёжник плаза”. Но эта профессия теперь стала действительно редкой, ведь на плазе чертёжник в натуральную величину вручную переносил все линии из чертежей на металл. Все изгибы и углы. Сейчас это делает компьютер.
Деревянные шаблоны направляются в цех, где на больших прессах заготовке придаётся нужная форма.
7.

Некоторые из прессов просто огромные
8.

Некоторые поменьше
9.

с соответствующей оснасткой
10.

А для закруглений большого радиуса используется вальцовочный пресс.
Но прежде, чем гнуть металл, его надо подготовить. Его обрабатывают на дробеструйном аппарате с помощью специальной стальной дроби, которая пролетая с большой скоростью, отбивает всю ржавчину и загрязнения.
11.

Сама дробь:
12.

Далее листы металла направляются на разметку и резку. Заместитель начальника корпусного производства Роман Медведев рассказал нам, что большинство разметочных и разделочных операций автоматизировано.
13.

Вот такой аппарат способен самостоятельно разрезать металлический лист по заданным координатам.
14.

При необходимости, он и фаску снимет, для того, чтоб было легче готовить детали к сварке.
15.

Прямолинейные разрезы можно делать и аппаратом попроще: этот полуавтомат плазменной резки может самостоятельно двигаться по проложенным направляющим.
Одновременно разрезая и снимая фаску.
16.

Деталей, кстати, огромное количество, я не представляю, как рабочие с ними разбираются, как находят, где и что лежит! Хоть я и сам работал на заводах, но у нас, всё же, деталей было куда меньше.
17.

Вот здесь документация лишь на маленькую часть судна
18.

Постепенно все детали передаются на участок сборки.
19.

Сварщиков на заводе много. Ответственная работа, от прочности и точности сварки зависит, как в последующем состыкуются крупные модули при сборке судна на стапеле.
20.

Видов сварки, кстати, много. И обычная дуговая, и сварка полуавтоматами, и в защищённой среде, и под флюсом.
21.

А вот что это за сварка, при которой используется такой специальный костюм и маска- я не спросил. Кто-нибудь знает, для чего это используется?
22.

Через некоторое время цеха опустели, настало время обеда. Тишина!
23.

Работа работой, а обед по расписанию!
24.

Краны и тали застыли, тоже отдыхают.
25.

А мы фотографируемся на фоне опустевших цехов.
26.

Пока мы рассматриваем всё, ходим по цехам- время пролетает незаметно и предприятие вновь оживает, пора снова приступать к работе.
27.

Постепенно вырастает часть корпуса судна.
28.

Собрана, проверена-- добро пожаловать на окраску.
29.

Швы модуля не просто прокрашиваются,они в обязательном порядке проливаются специальной краской, чтобы снизить скорость коррозии.
Масштабы покрасочной камеры не идут ни в какое сравнение с автомобильными!
За окрашенным модулем приезжает специальная многоосная машина- трейлер.
30.

Возить может грузы огромного веса и размера, его водитель, Владимир Михайлов, говорил про 300 тонн и 12 метров в высоту!
31.

Водителей таких машин очень немного. Тоже редкая профессия. Кабин у такой машины две, с обеих сторон, для удобства маневрирования и чтобы не разворачиваться.
О своей работе, если она любимая, можно рассказывать долго и удивлять слушателей!
32.

Вот и эту часть корпуса скоро повезут на сборку. Строится ледокол “Андрей Вилькитский”
33.

Тросы.
34.

По цеху, кстати, для удобства перемещения модулей проложена железная дорога.
35.
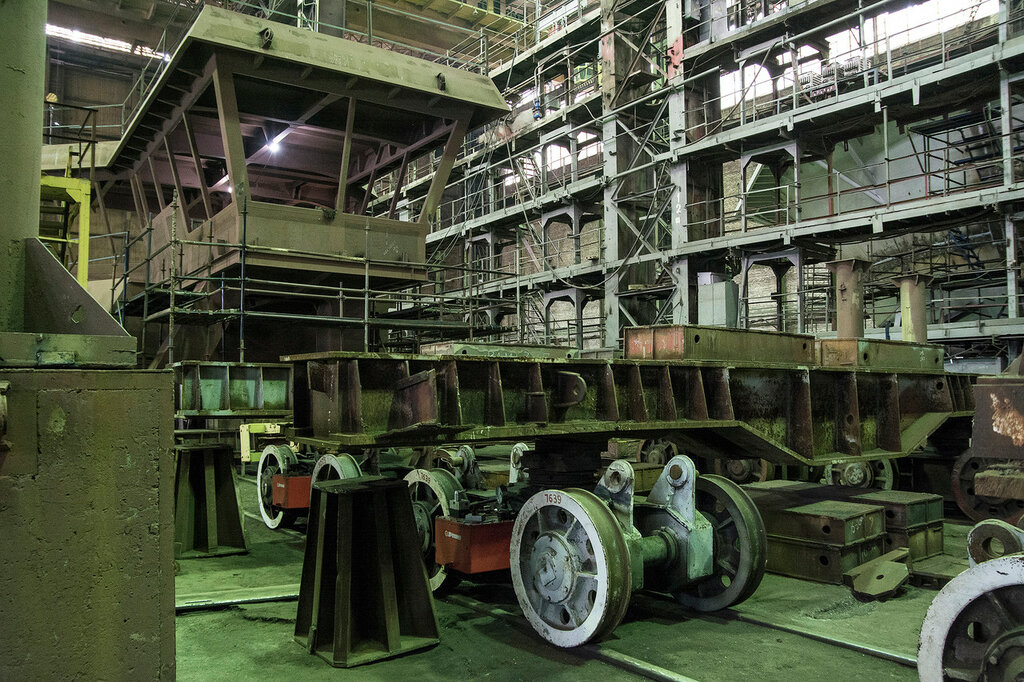
То же судно, вернее, его часть, с другой стороны. На переднем плане кранцевая защита
36.

Очень хотелось посмотреть, как вручную плетётся эта штука- кранец!
37.

Дальше наш путь, в соответствии с технологической цепочкой, лежит к сборочной площадке и причалу. На плавучую полупогружную баржу-стапель пройти возможности не представилось, зато нам разрешили подняться на борт строящегося ледокола Александр Санников, порт приписки Мурманск.
38.

Ледокол весьма большой по своим размерам, а вот на его борту проживать и работать смогут всего 36 человек, настолько велик уровень автоматизации и механизации рабочих процессов.
39.

Бдительная охрана не ограничивается пересчётом “по головам”, записывает прибывших. На входе и выходе работает досмотровая рамка. Для безопасности, говорят нам.
40.

Поднимаемся на борт. К ледоколу тянется множество электрических кабелей, сварка продолжается и на уже спущенном на воду судне.
41.

Провода везде, надо ступать с осторожностью.
42.

Здесь заканчивается монтаж главной силовой установки. Чтобы всё это собрать правильно, надобно представлять все чертежи в своей голове, представляете сложность работ?
43.

Ещё одни вид на помещение ГСУ
44.

Коридоры. Конструкция судна предусматривает, что моряки минимум времени будут проводить на “свежем воздухе”, потому, что температуры в северных широтах едва ли можно назвать комфортными большую часть года.
45.

Для этого даже палубу, на которой находятся якорные и швартовые лебёдки, обычно открытую всем ветрам, закрыли щитами.
46.

Выданные нам каски пару раз послужили по назначению и уберегли головы от повреждений.
47.

Поднимаемся на уровень выше. Здесь вертолётная площадка, способная принимать вертолёты МИ-8.
48.

Смотрим, фотографируем, обсуждаем.
49.

Неплохой вид на грузовой порт Выборга. За подъемными кранами видны башни Святого Олафа и Часовая.
50.

А это вид на завод.
51.

С другого борта- вид на Выборгский залив и бухту Ховенлахти
52.
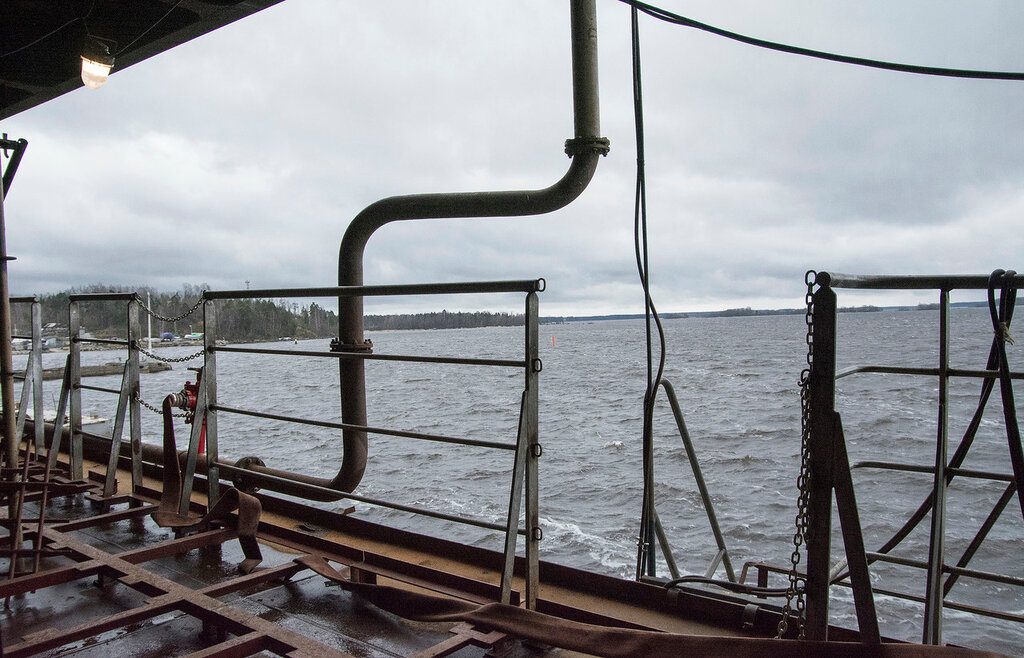
Ещё один коридор и пора спускаться, чтоб не мешать производству работ на судне.
53.

Ну а как же без котиков, правда?
54.

А это наша команда в сопровождении Анны Панфиловой, специалиста по связям с общественностью, очень симпатичной и приятной девушки. Котика увидели? :)))
55.

Знакомьтесь: азиподы. Или Винто-Рулевые Колонки. Внутри этой гондолы расположены высокомоментные судовые электрические двигатели, передающие крутящий момент непосредственно на винт. Отказ от промежуточных валов и подшипников существенно упрощает и облегчает конструкцию.
56.

Вся эта гондола подвешивается под днищем судна на подшипниках и может вращаться на 360 градусов вокруг своей оси, что помогает судну многократно увеличить манёвренность по сравнению с судами классической компоновки. На Александре Санникове будет установлено четыре таких азипода.
57.

На этом снимке видно, что ледокол стоит у причальной стенки с дифферентом на нос. Передние азиподы установлены и судно загружают балластом, чтобы приподнять корму, на которую будут устанавливать азиподы прямо с воды по уникальной технологии.
58.

Ну, а нам пора возвращаться из Выборга в Санкт-Петербург.
Выборгский судостроительный завод оставил самое приятное впечатление, даже холодная погода со снегом и дождём не смогла испортить нашу встречу!
Хотелось бы вернуться через некоторое время, увидеть, как воплощается в жизнь очередной большой проект в области судостроения. Уверен, таких проектов у завода будет много!
Взято: zavodfoto.livejournal.com
Комментарии (0)
{related-news}
[/related-news]