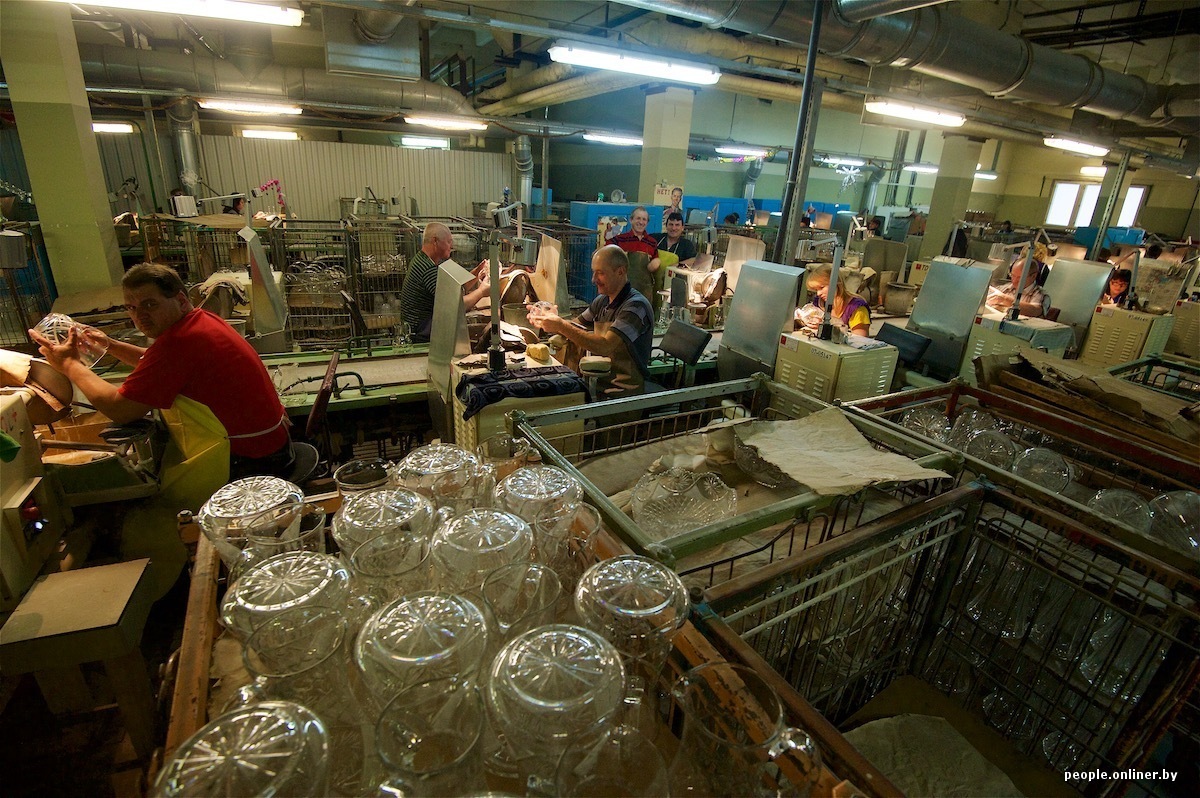
Как в Беларуси делают хрусталь
---
В Березовке совсем немного населения — 10 553 человека. Из них 1844 заняты на стеклозаводе «Неман». В будний день вокруг него тишь, первый долгосрочный снег и стоянка велосипедов, популярных не из хипстерских, а из практических соображений.
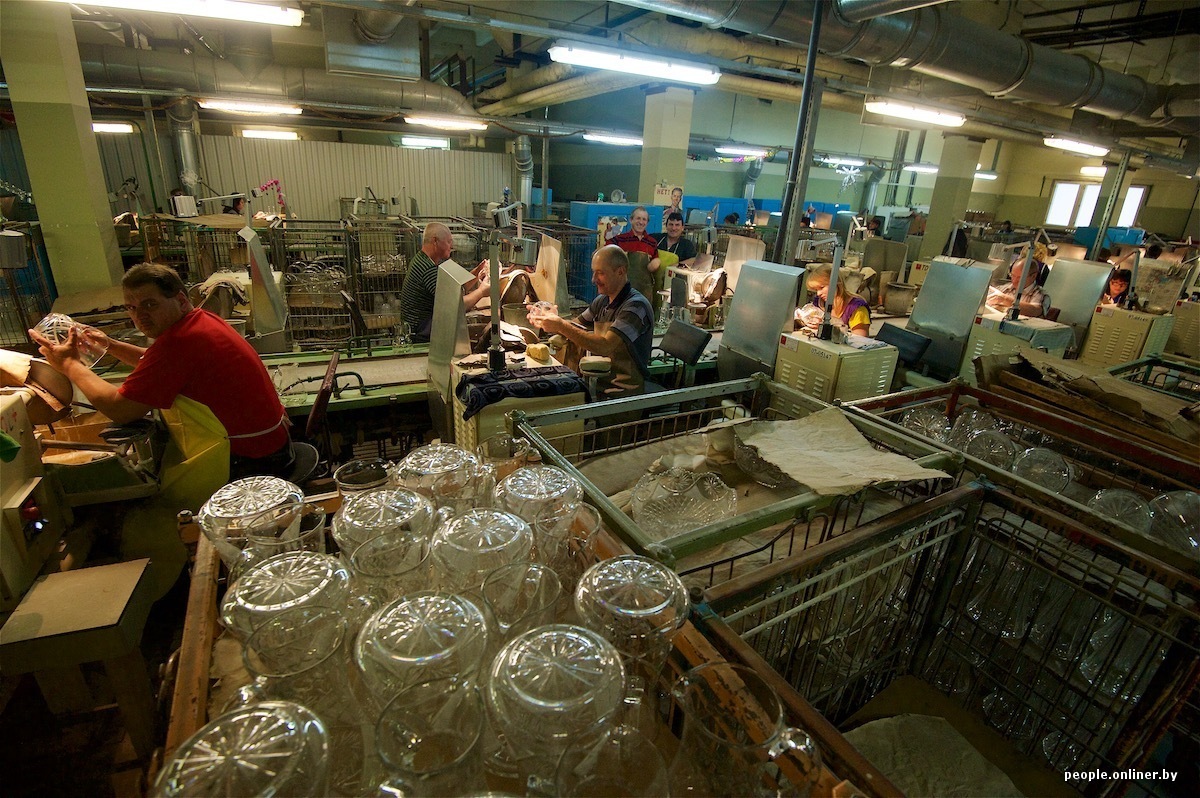
Производство хрусталя начинается в пыльном цеху, где сочиняется шихта. Шихта — сумма песка, поташа и оксида свинца. В хрустале завода «Неман» 58% кварцевого песка и 24% свинца. Остальное — добавки. Песок украинский. В белорусском много железа — стекло получается зеленым. Песок очень-очень мелкий — отсюда и пыль.
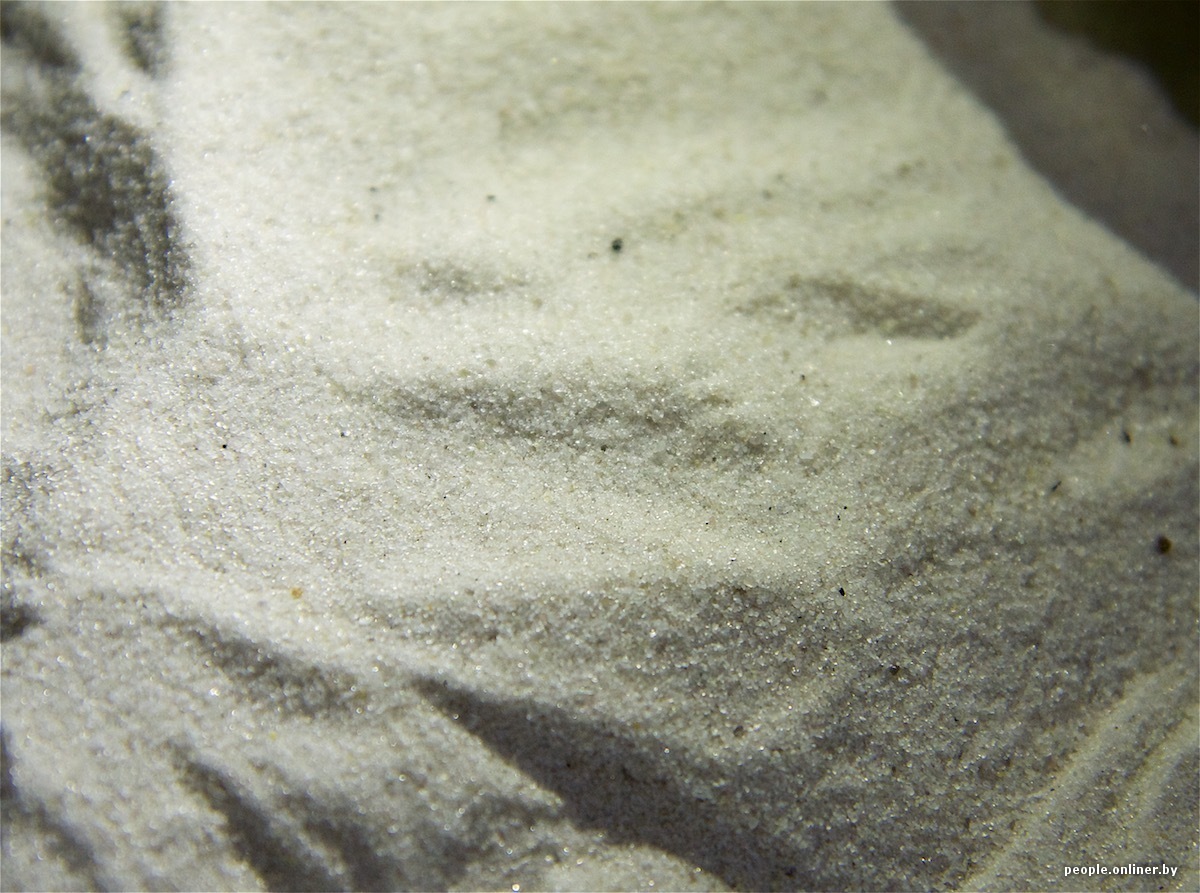
В двухэтажном помещении все зависит от компьютера, который настраивает дозаторы согласно рецептуре. Нужное количество сырья опускается на ленту конвейера и едет к контейнерам, перемешиваясь в однородную массу.
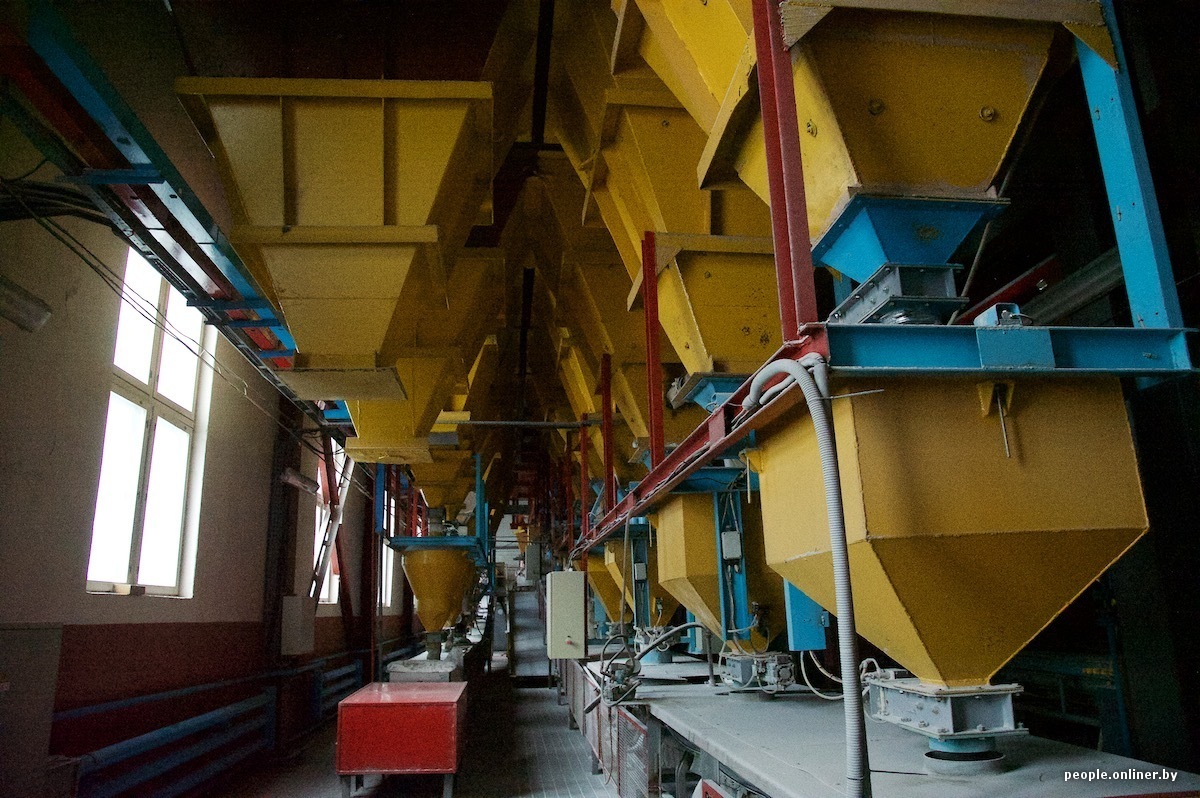
В принципе, стекло и хрусталь — это одно и то же. Правда, в хрустале есть свинец, который окрашивает здешние бочки в оранжевый «вырви глаз» цвет.
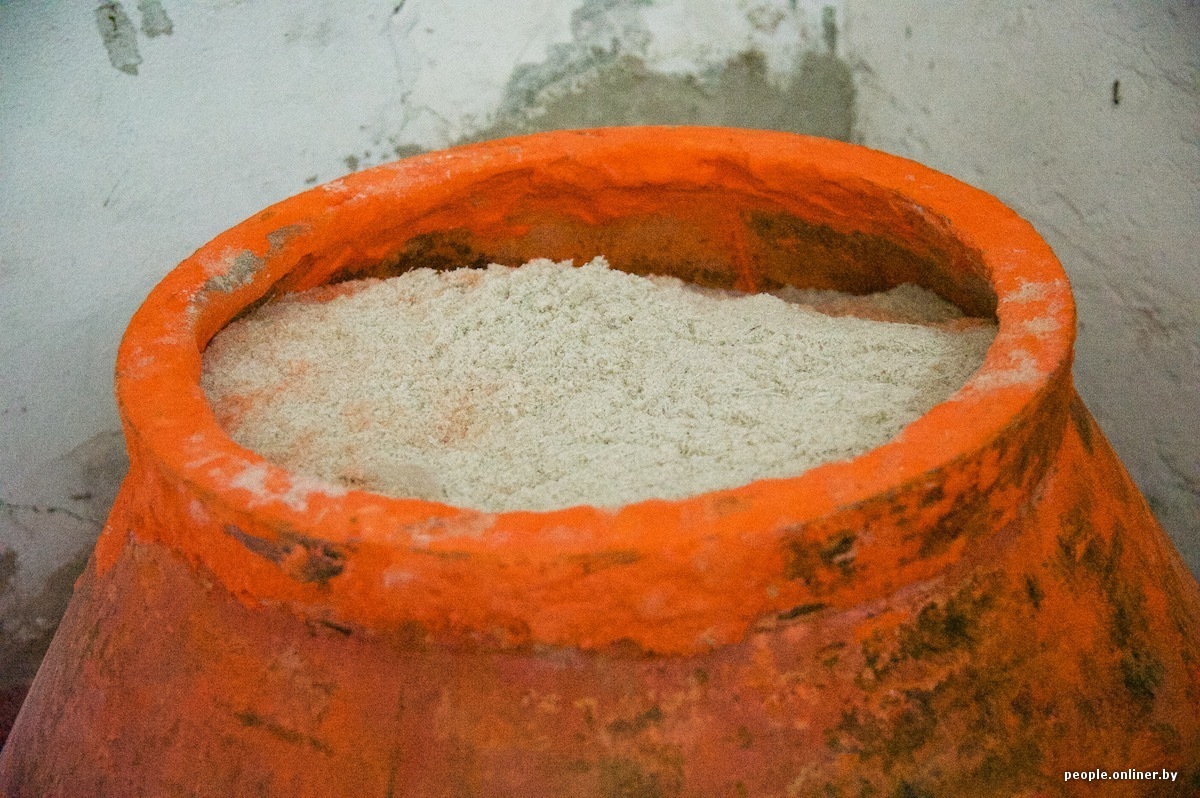
Заготовленная шихта счастливо попадает в самый эффектный цех завода. Прямо декорации из клипов зрелого Rammstein. Тут все пышет жаром. Печей в цеху две. Раньше, говорят, было больше десятка. Печи — почти что вечный двигатель. Паузы делают только вынужденные — c отвлечением на ремонт. Срок непрестанной работы — пять-семь лет.
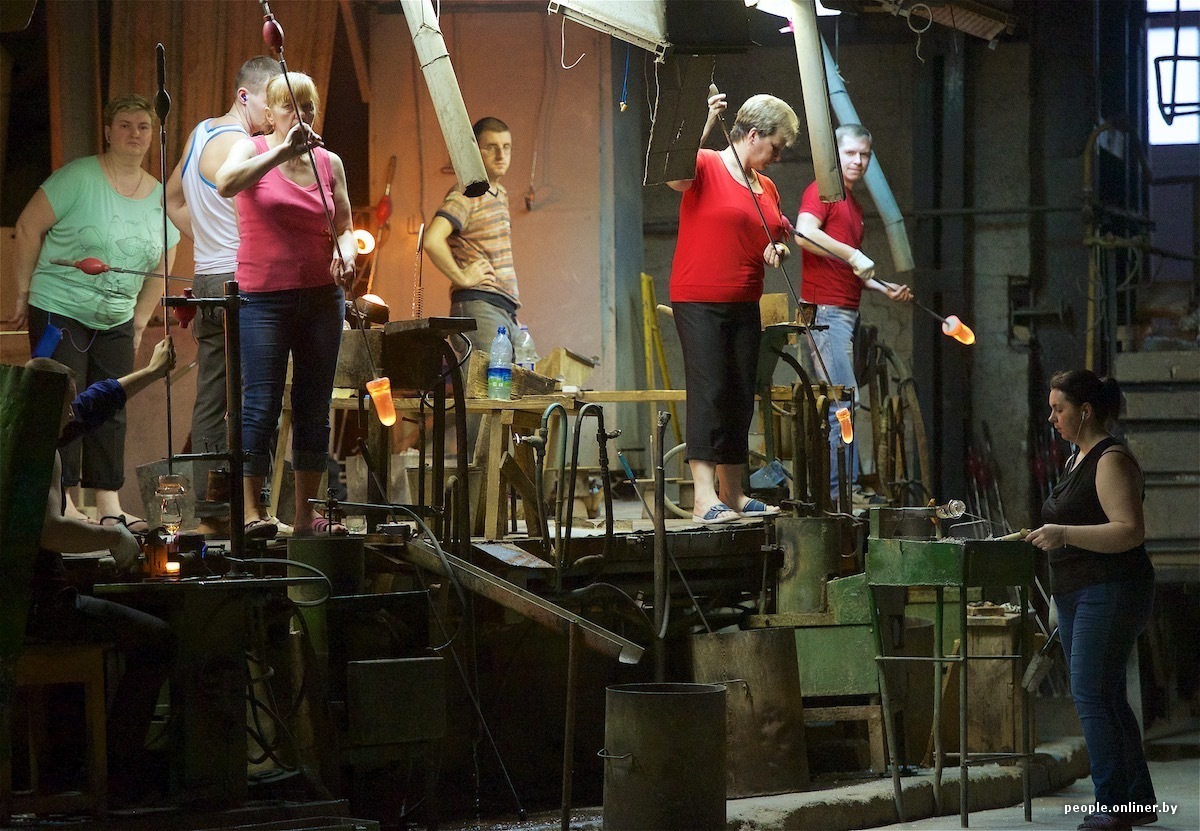
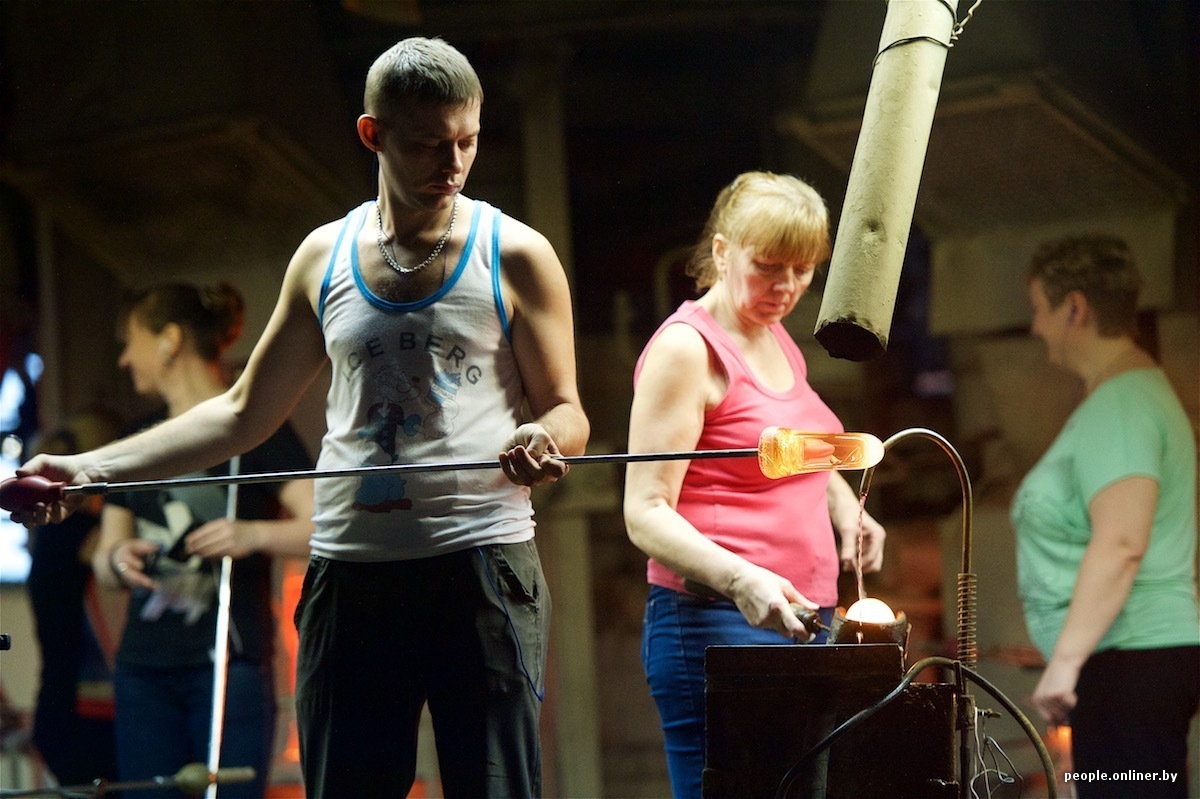
Оттого стекло здесь делается в три смены. Первая — 8:00—16:00, вторая — 16:00—0:00, третья — 0:00—8:00. Рабочий день предполагает получасовой обед и два «перекура» по 15 минут. График у здешних тружеников стекольной отрасли скользящий.
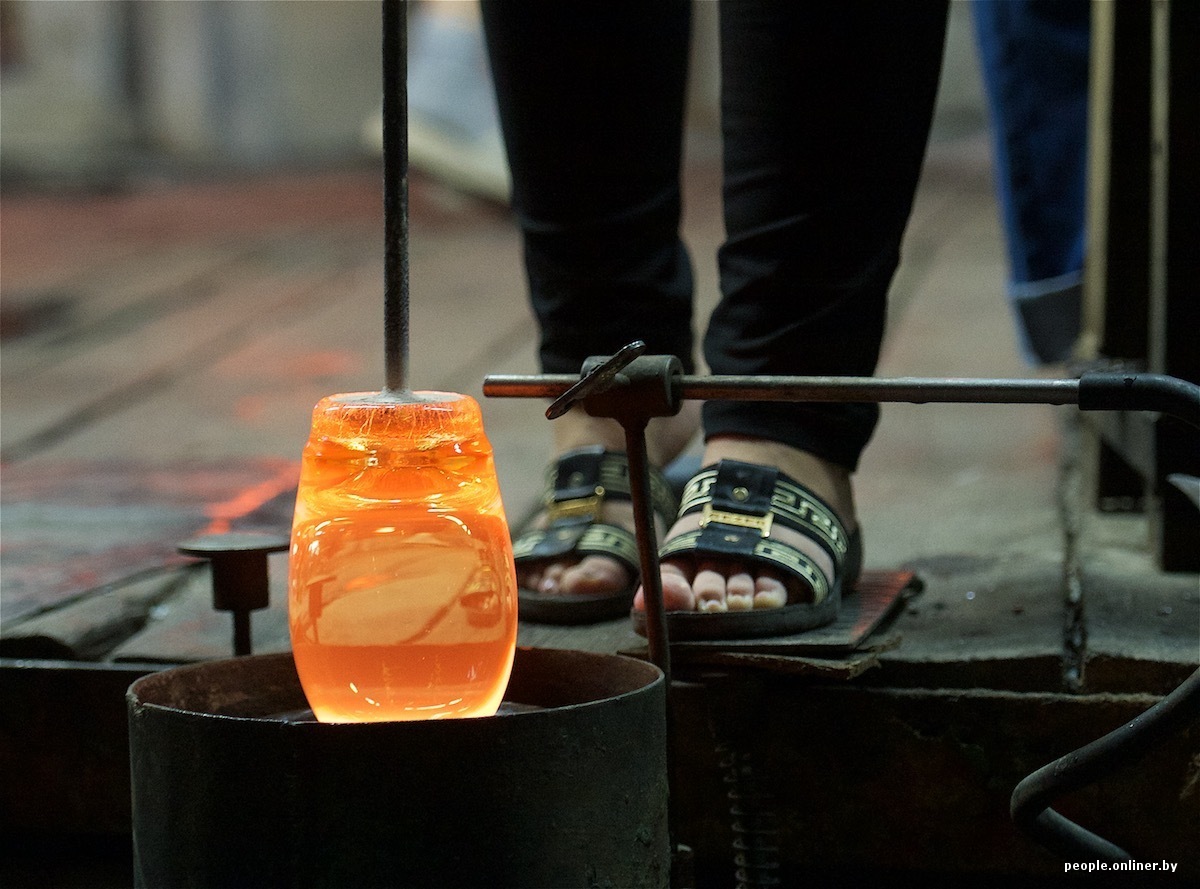
В цеху ощутимо жарко. Участники бригад челночат между печами и чанами с водой в достаточно домашнем виде — майки, сланцы. Говорят, им предлагали униформу, но идея не получила поддержки.
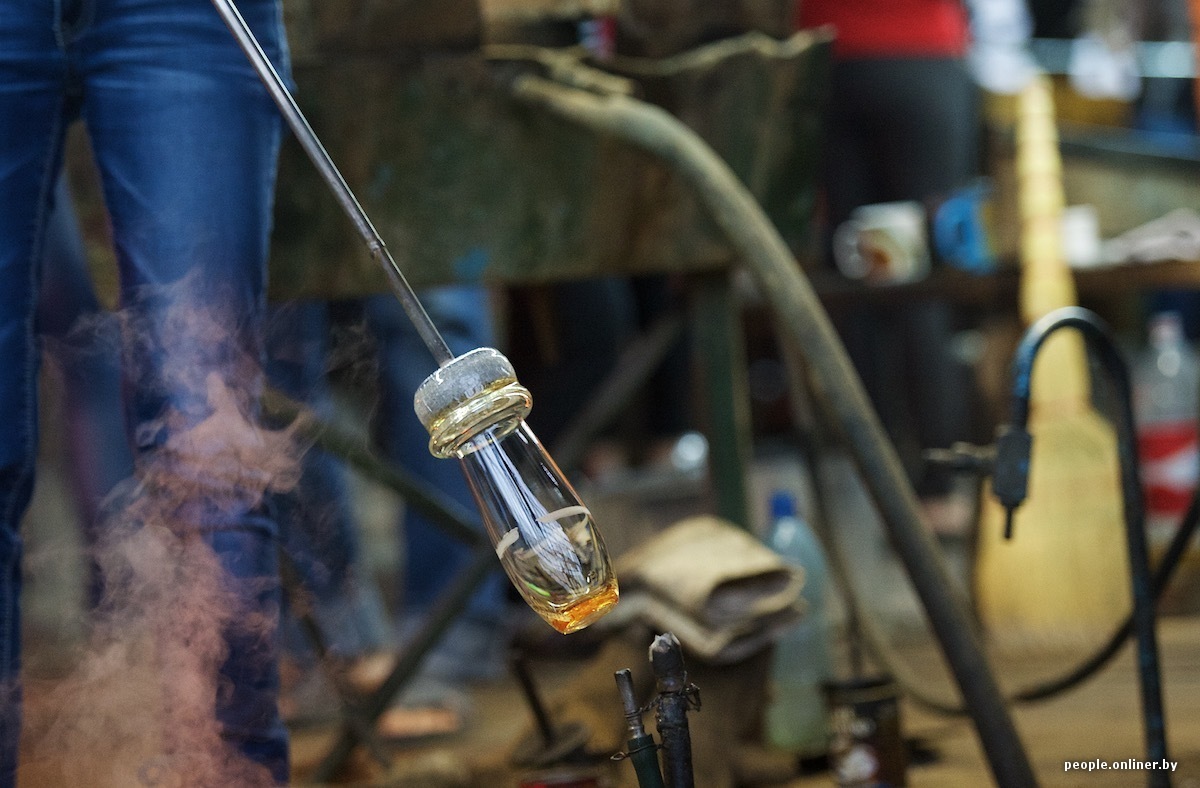
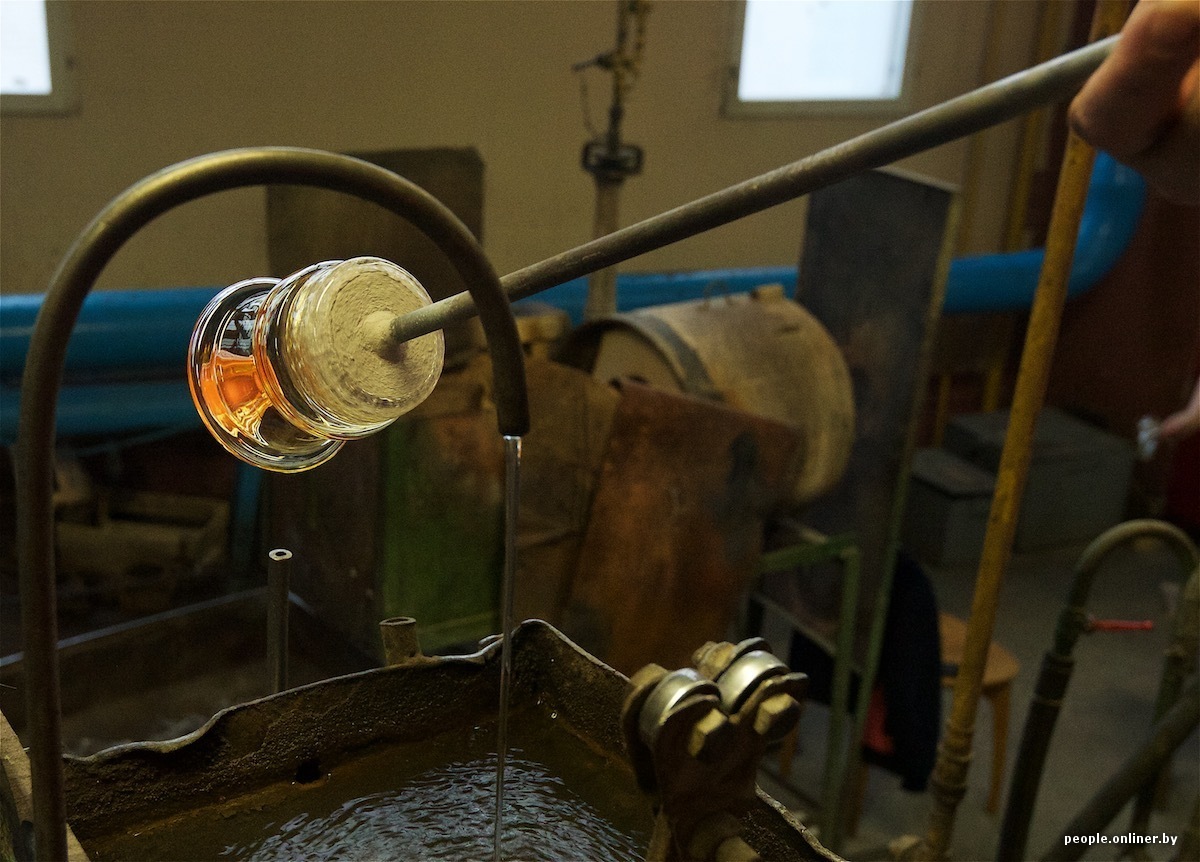
Температурный «Ташкент» дополняется интенсивным шумом. Кто-то просто его не замечает. Кто-то понижает наушниками.



Работники поделены на бригады. В каждой по шесть человек. Два выдувальщика. Это люди с «волшебными палочками», которые придают раскаленному стеклу необходимую форму силой своих развитых легких. Они делают пойло — верхнюю часть бокала. К выдувальщикам добавляется пара наборщиков. Первый подает сырье для ножки, второй — для донышка. Дополняют бригаду прессовщик и бригадир, заодно занятый еще и шлифовкой.
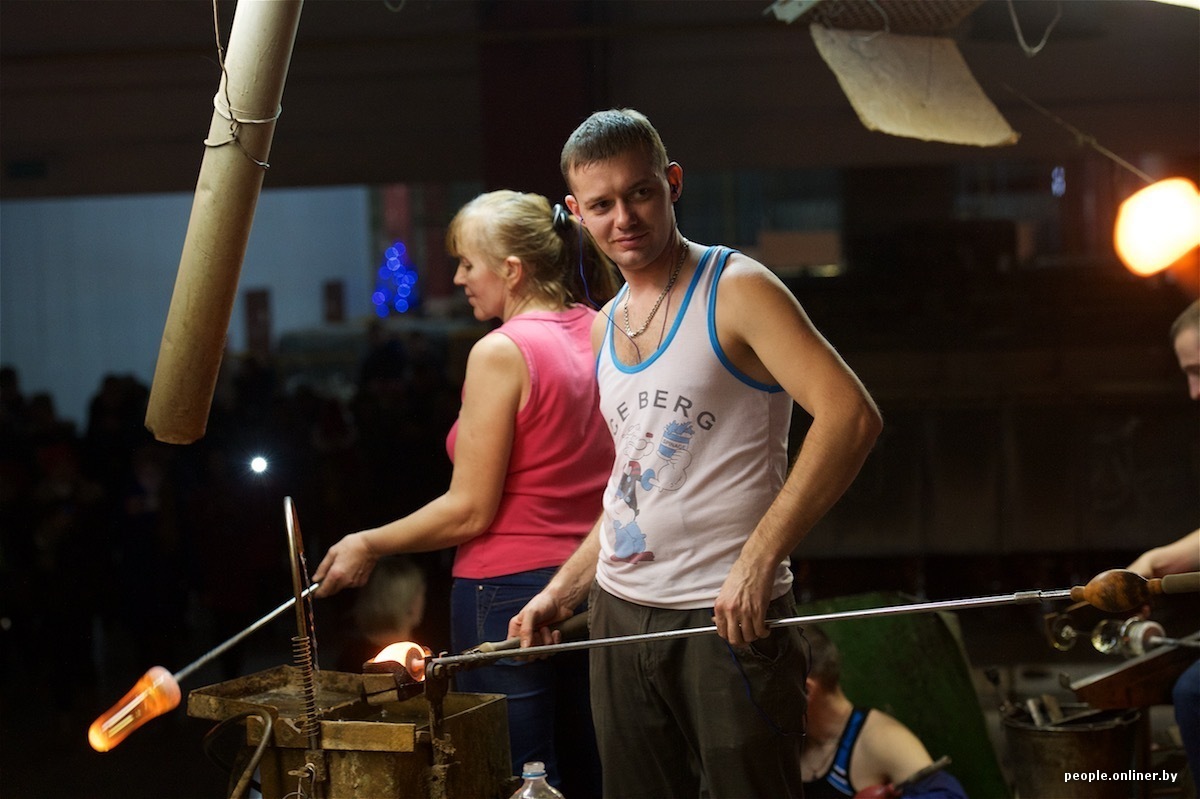

Выдувальщик — топовая профессия на заводе, которая предполагает самую высокую вредность. Человек, получивший семь лет «горячего» стажа, имеет право уйти на пенсию раньше. Женщины — в 45 лет, мужчины — в 50.
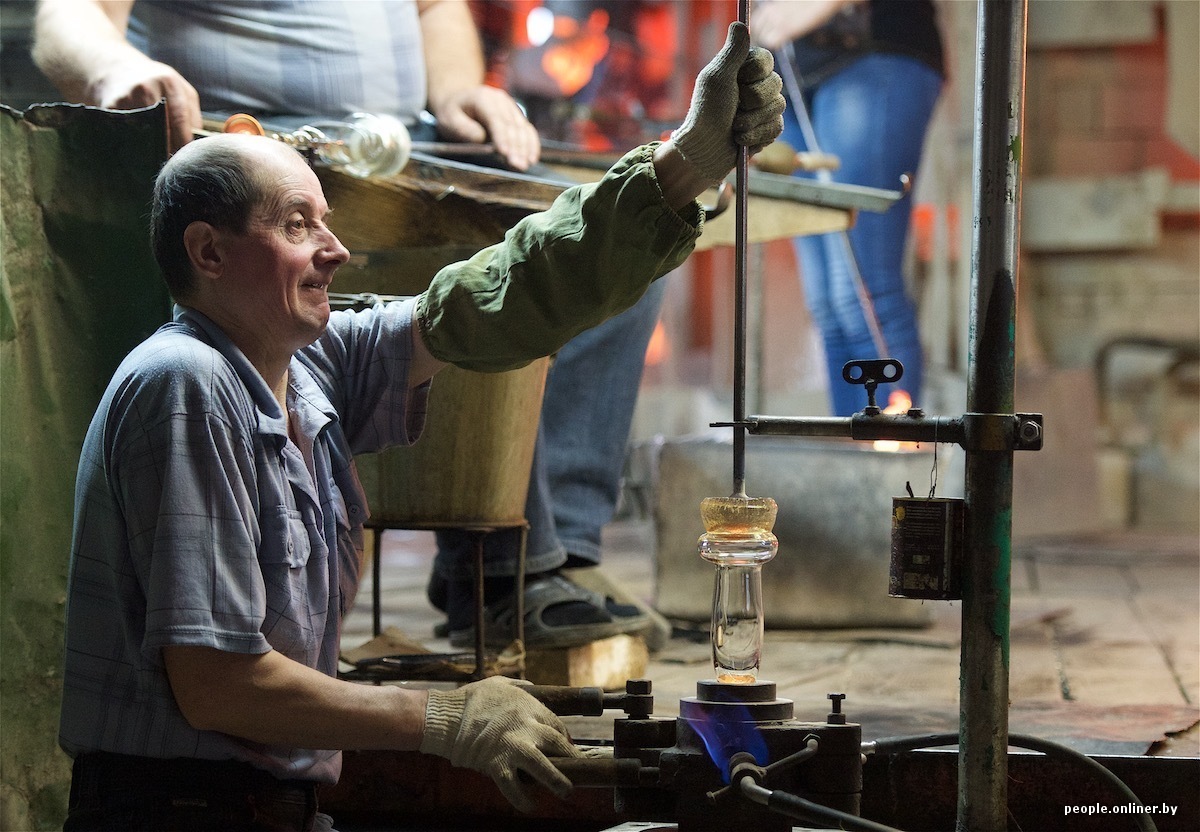
Заготовки будущих изделий попадают с горячего производства на широкую ленту конвейера, который направляет их в намного более тихое и прохладное помещение.
Там с будущих бокалов, ваз и прочей заводской продукции снимается напряжение, чтобы стекло не растрескалось. Плюс заготовки остывают.
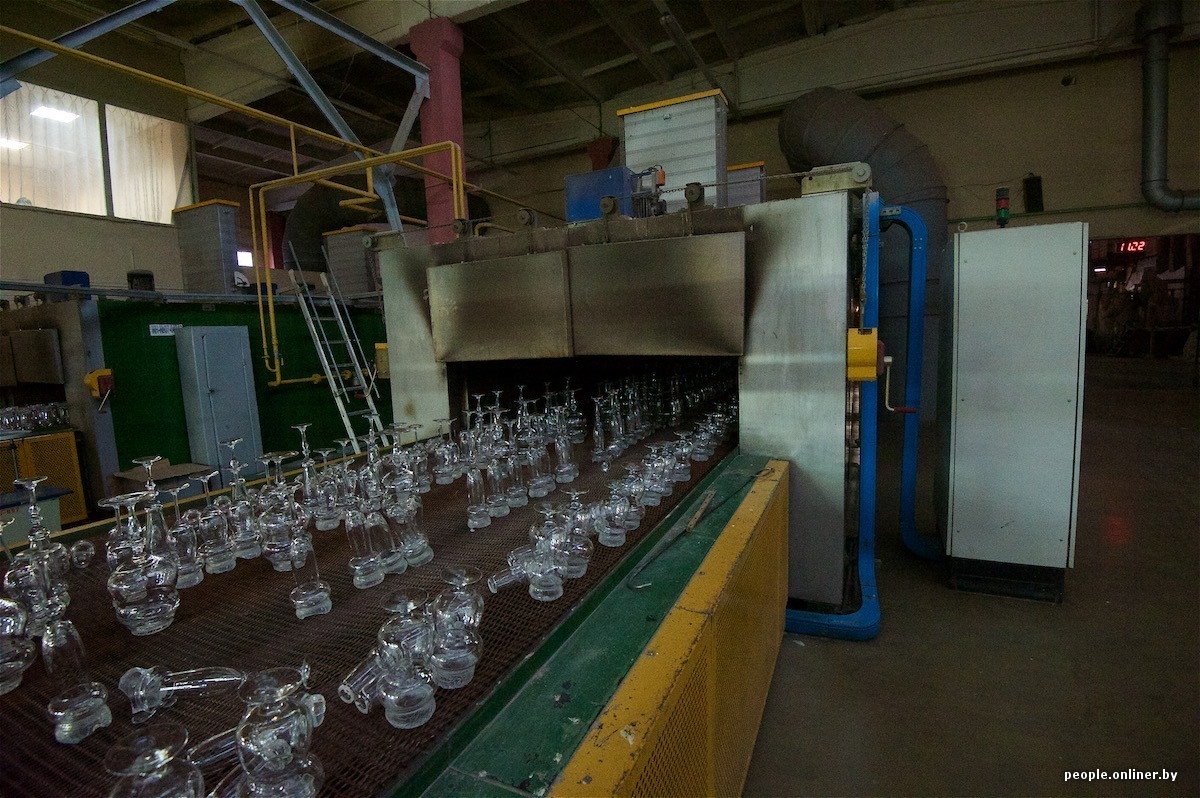
У каждого изделия своя высота резки. Сперва наносятся необходимые метки. По ним с помощью газовой горелки осуществляется резка. Все остатки попадают в контейнер, затем измельчаются на специальной мельнице и снова становятся сырьем.
Здесь же находится первый отдел товарного контроля (ОТК). Наличный брак отправляется на переплавку. К слову, когда-то работникам приходилось расплавлять и хорошо выполненные изделия. Просто в СССР начали бороться с алкоголем, и оттого поступило указание отправлять в огонь все рюмочные и другие формы, связанные с выпивкой. В итоге из графинов делали вазы для фруктов.
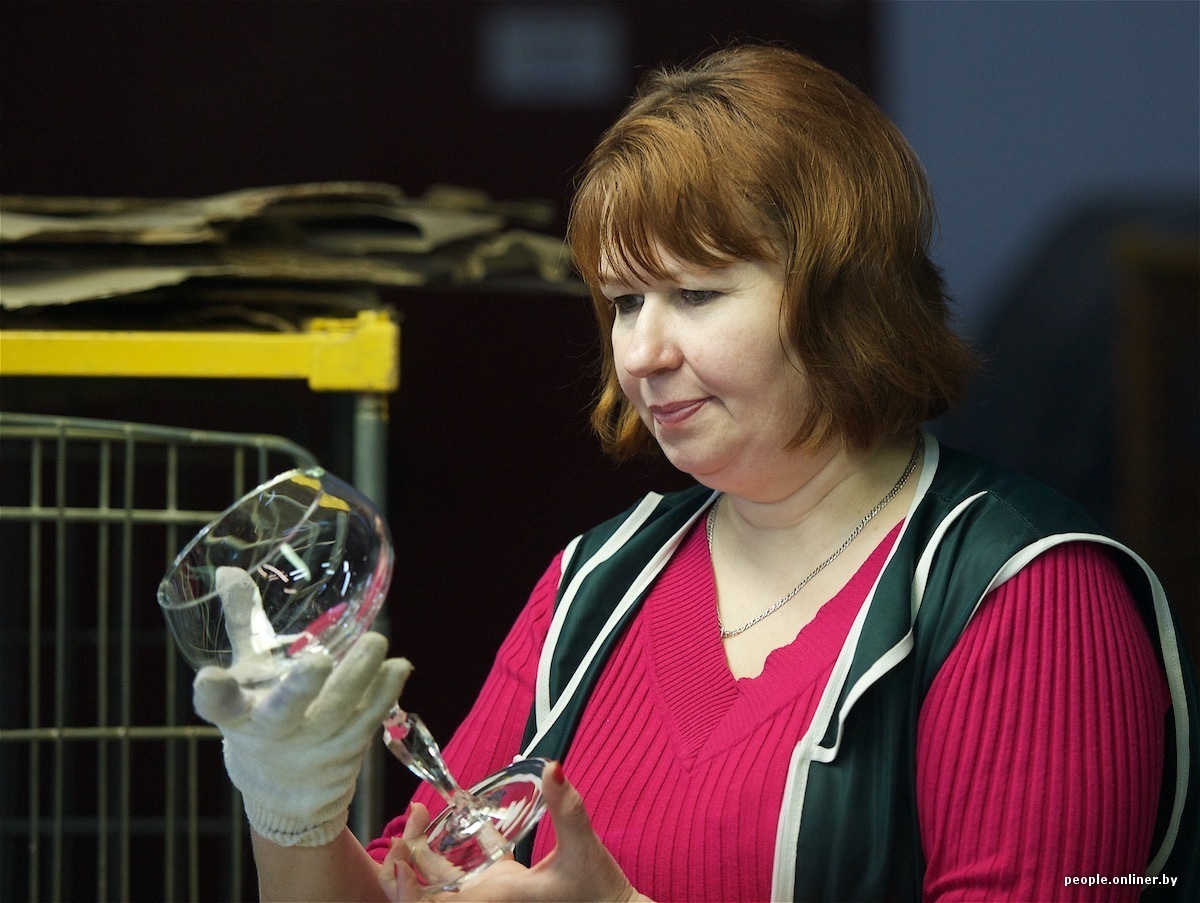
На ленте виднеются почти что вазы — бокалы каких-то нереальных размеров. Оказывается, это заказ из Азербайджана. Вообще, 65% продукции отправляется на экспорт.
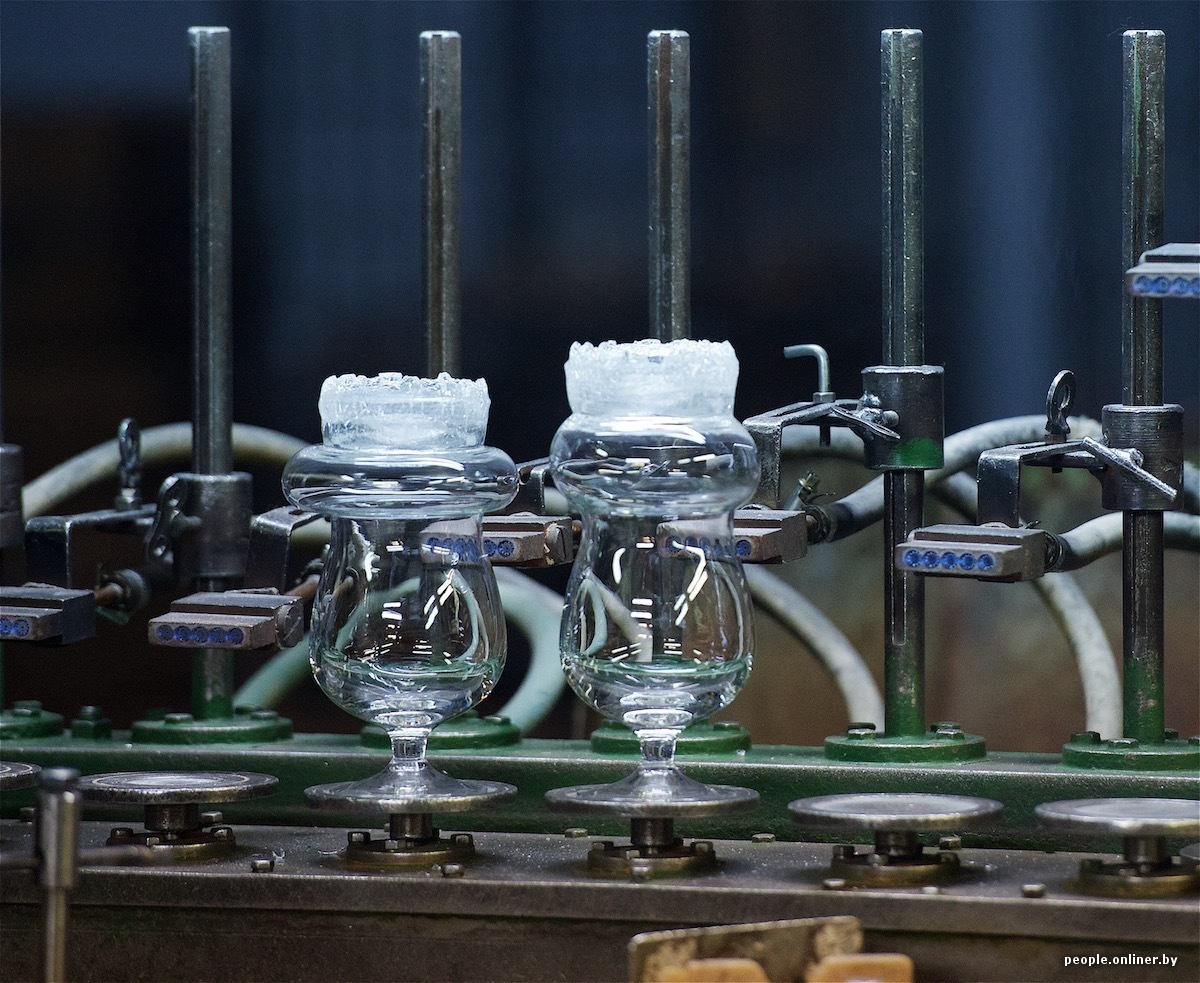
— У нас этот хрусталь покупают даже американцы, — хвалятся работники.
Продукция доставляется из Беларуси в США в контейнерах. Более всего в ней заинтересована компания North American Crystal, с которой стеклозавод сотрудничает примерно десять лет.
После первого контроля качества некоторые бокалы/стаканы/рюмки аккуратно упаковываются, некоторые поступают в специальный станок для шлифовки острых краев. Чтобы никто не порезался. Процесс называется «отопка».
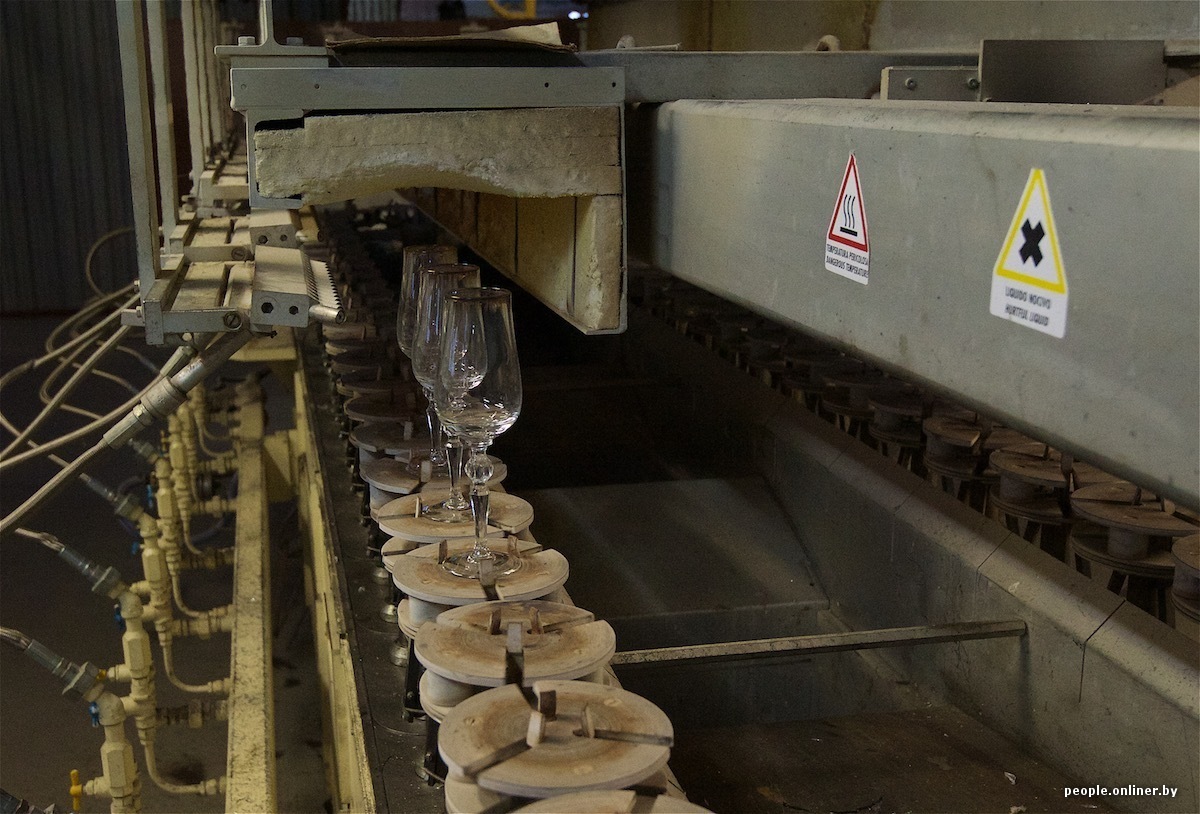
По завершении отбивки и отопки стакан попадает в цех обработки. Тут на него глиной наносятся необходимые метки. Все делается руками при помощи кисти. Затем размеченное изделие уходит к резчикам по ленте конвейера. Каждый из них знает, что нужно взять в работу. Здесь же находится второй пункт контроля качества.
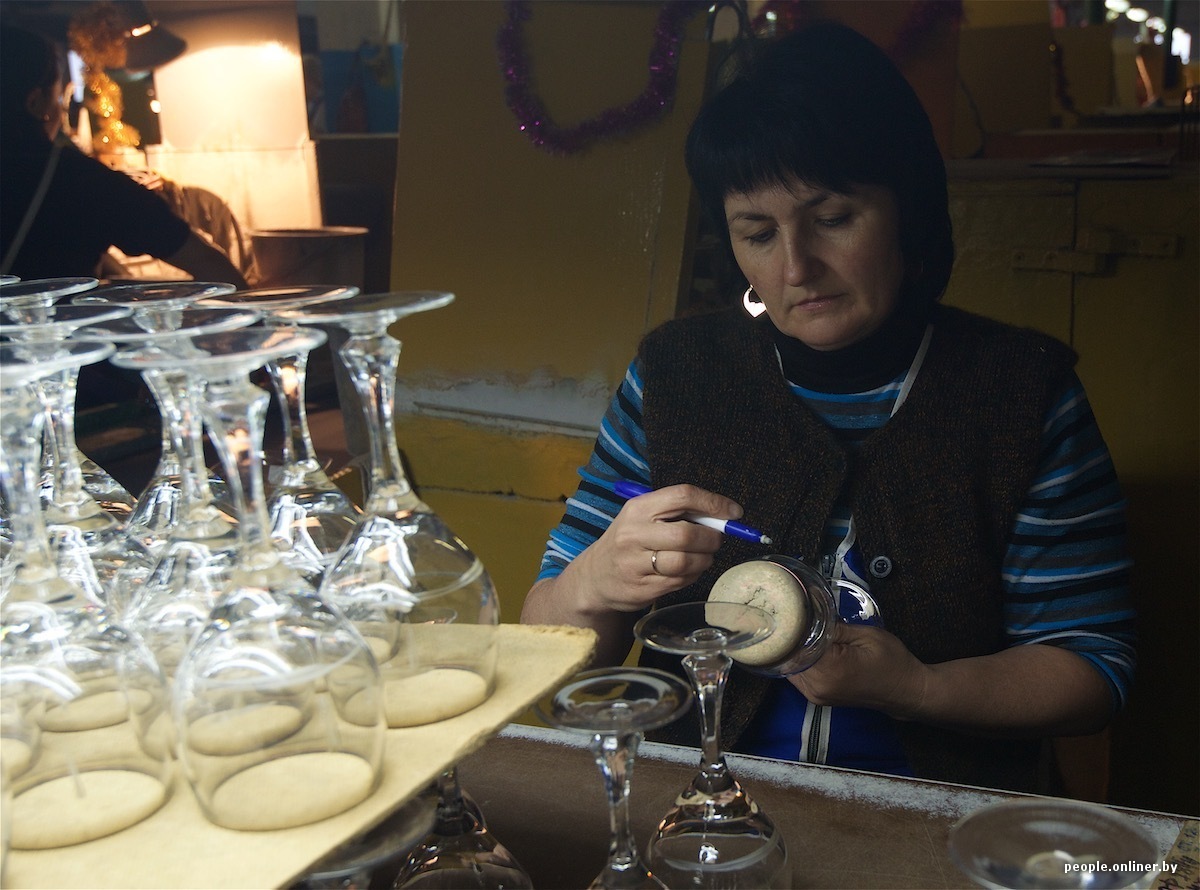
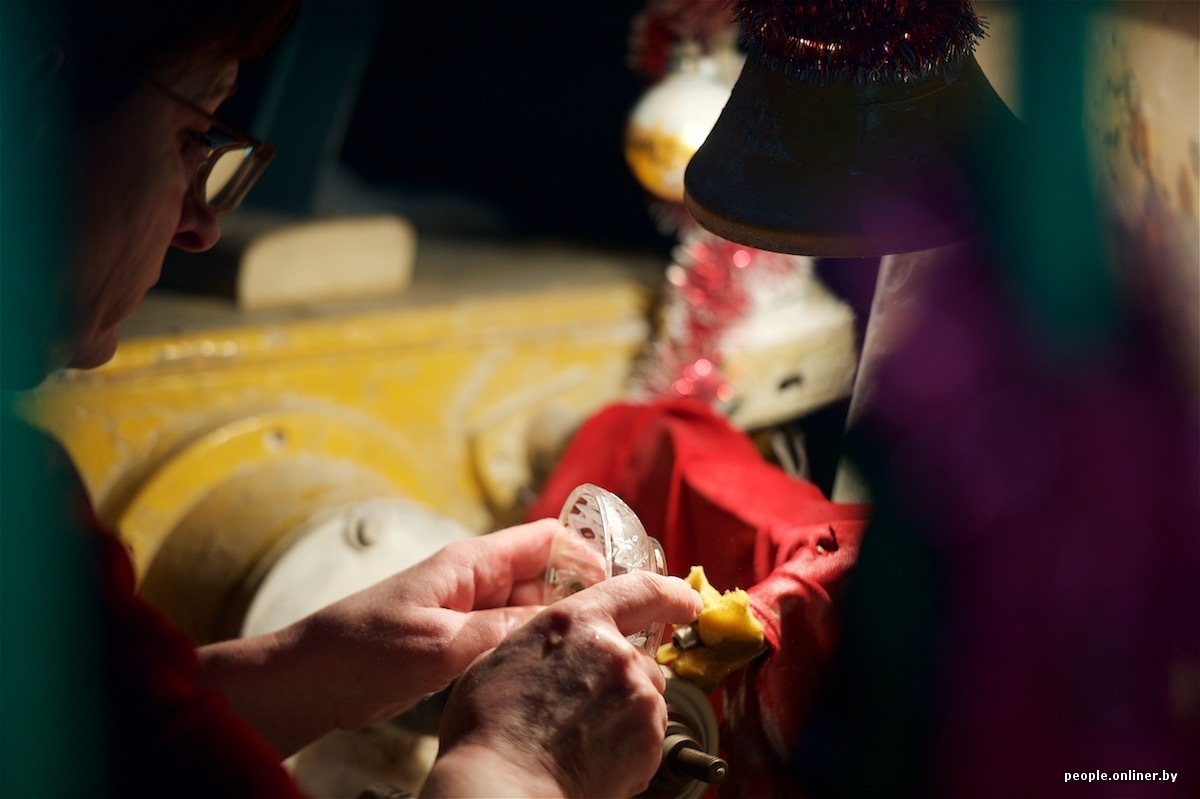
Цех резки — гулкое помещение с высокими потолками. Тут работают с помощью алмазных резаков. Один из резчиков подходит с вазой наперевес. Ваза выступает в качестве то ли экспоната для демонстрации, то ли оружия для угрозы.
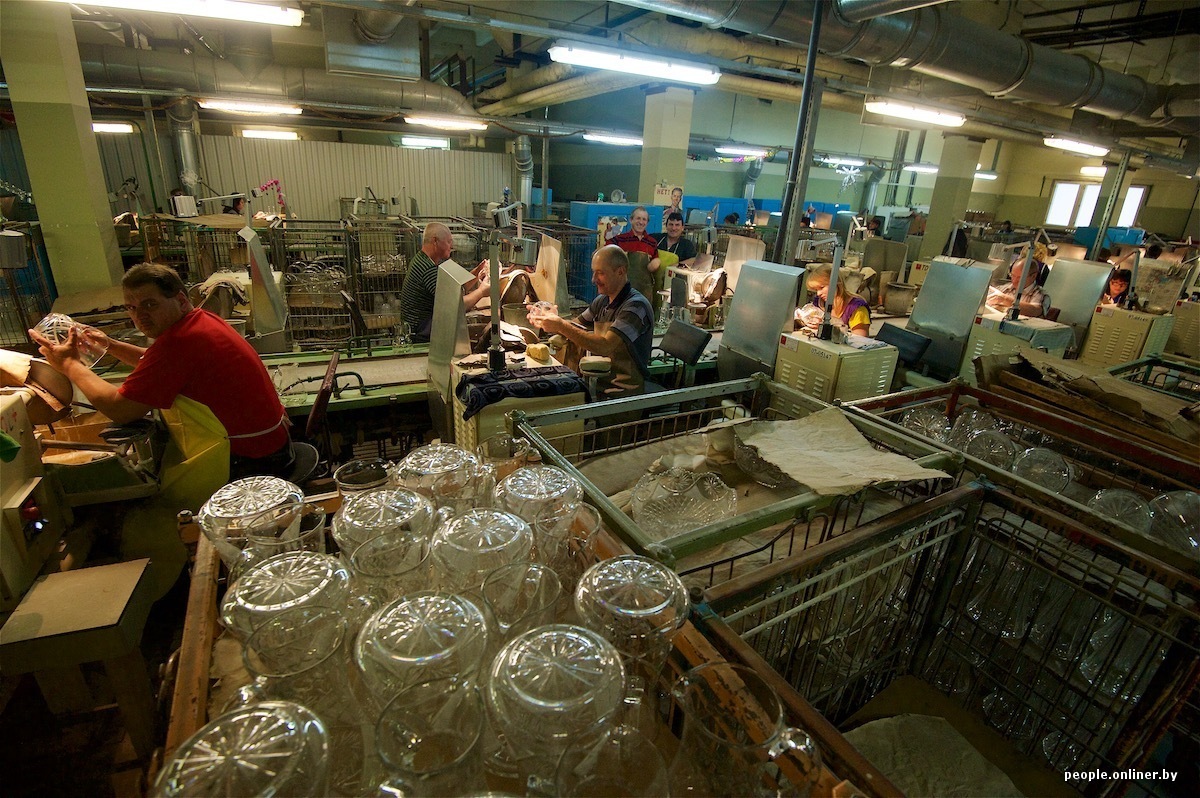
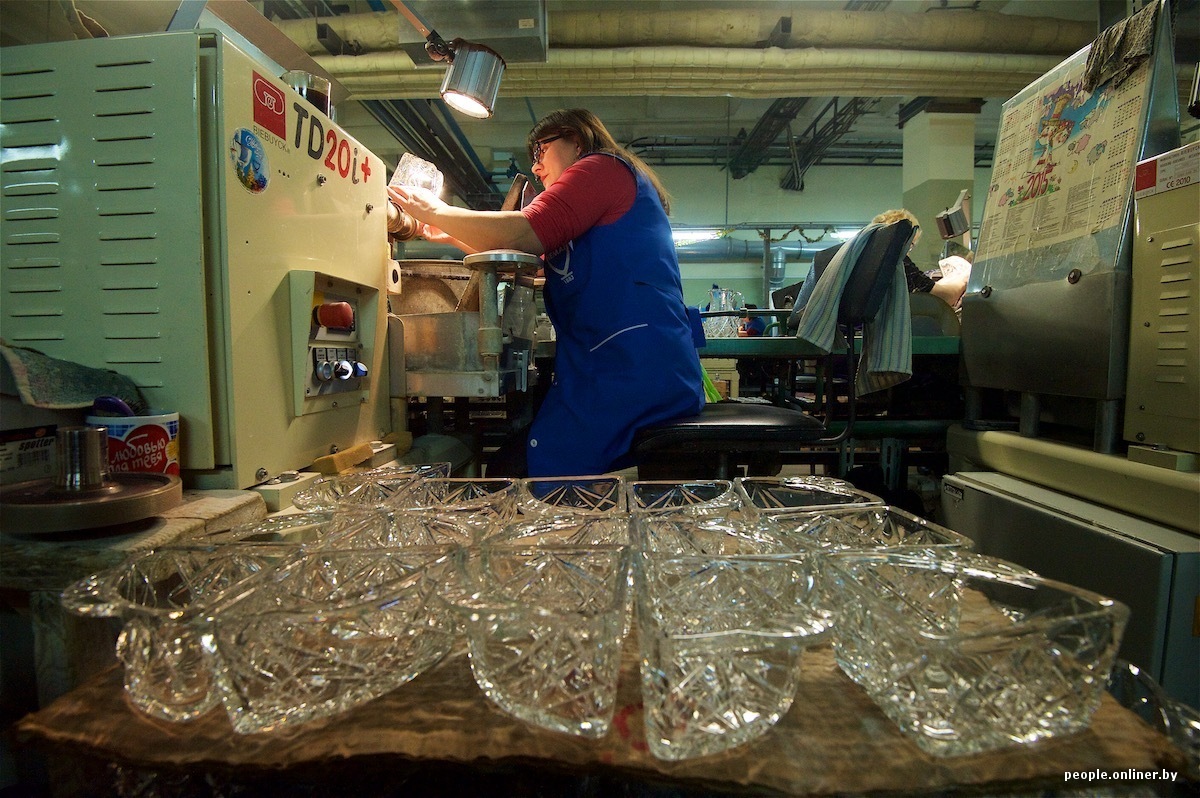
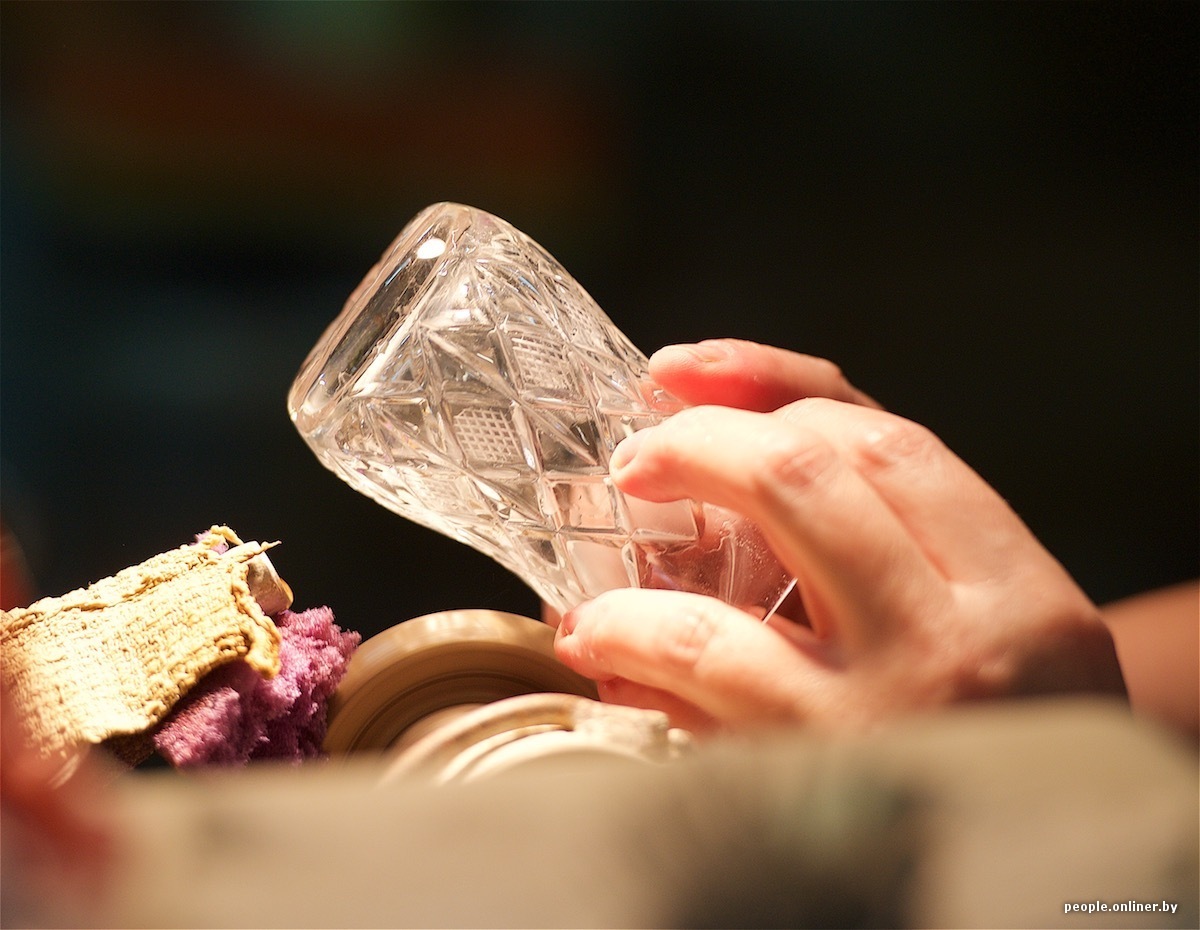
Нарезка сменяется химполировкой. Дело в том, что изначально изделие получается матовым. А обработка кислотами придает ему должный товарный блеск.
Пыль и огонь заводских цехов дополняются водой, которой в изобилии на полу. Работники шлепают по лужам, наполняя большие кассеты. В них можно загрузить почти все, что производится на заводе.
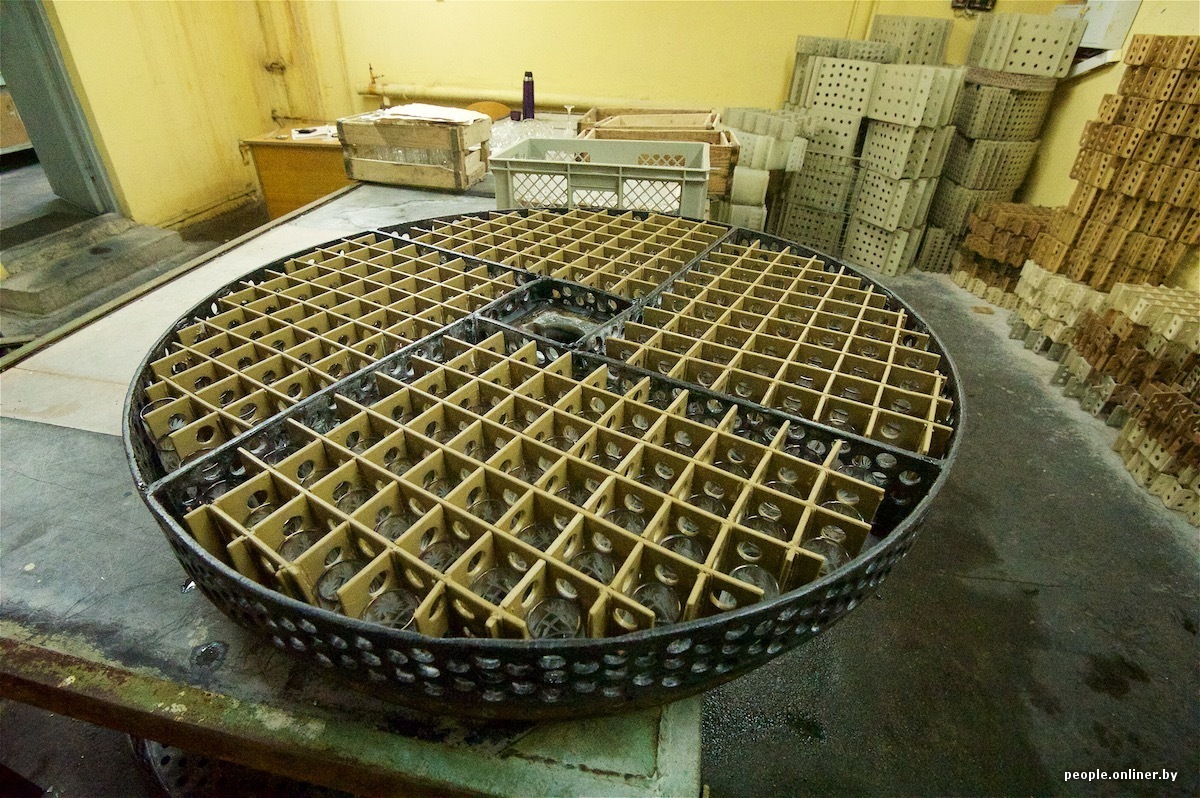
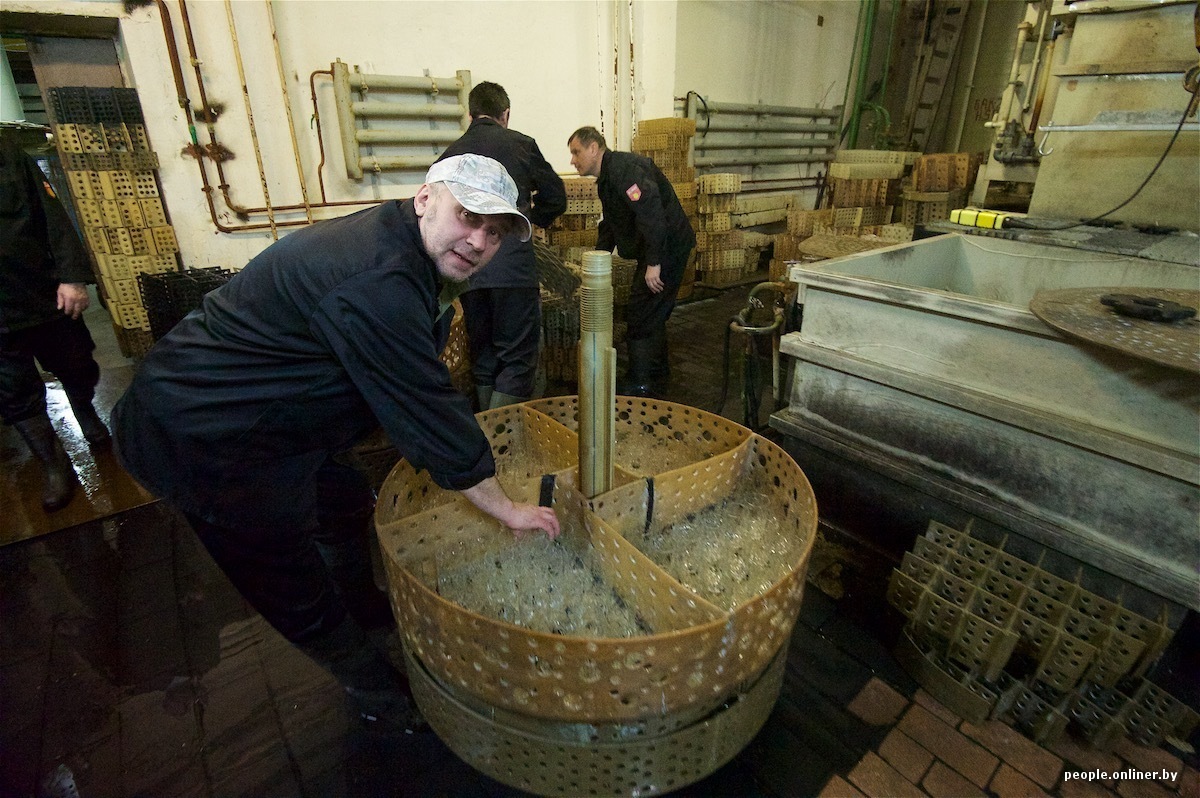
Упакованные кассеты прикладываются друг к дружке, формируя гигантский ролл. Его цепляют тросом и отправляют в ванную с кислотой. Кассеты постоянно вращаются. Мойка длится примерно 40 минут. Стаканы полируются плавиковой и серной кислотами, а на прощание обрабатываются водой.
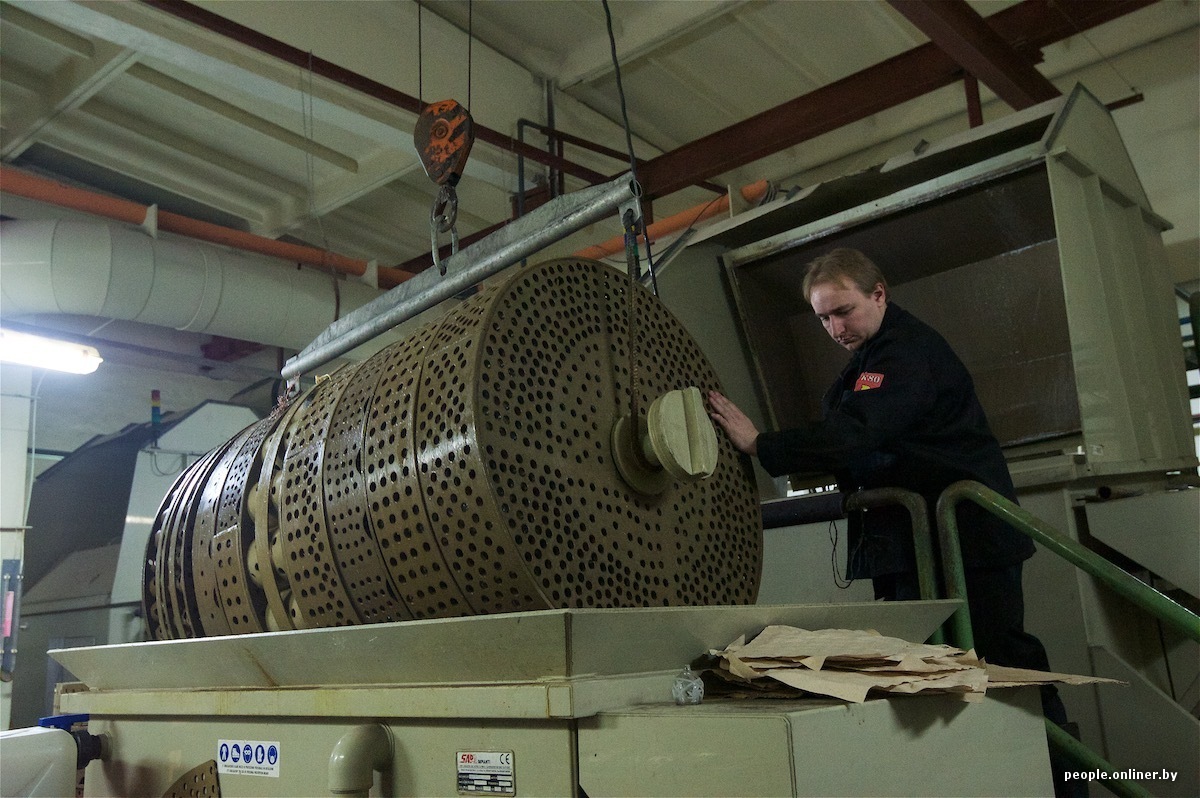
В принципе, все готово. После купания в кислоте стакан могут отправить на дополнительную резку или для наведения финального марафета — например, нанесения золотого кантика. Соответствующая работница занимается этим с 7:00 до 15:00. На каждый бокал наносится настоящее золото.
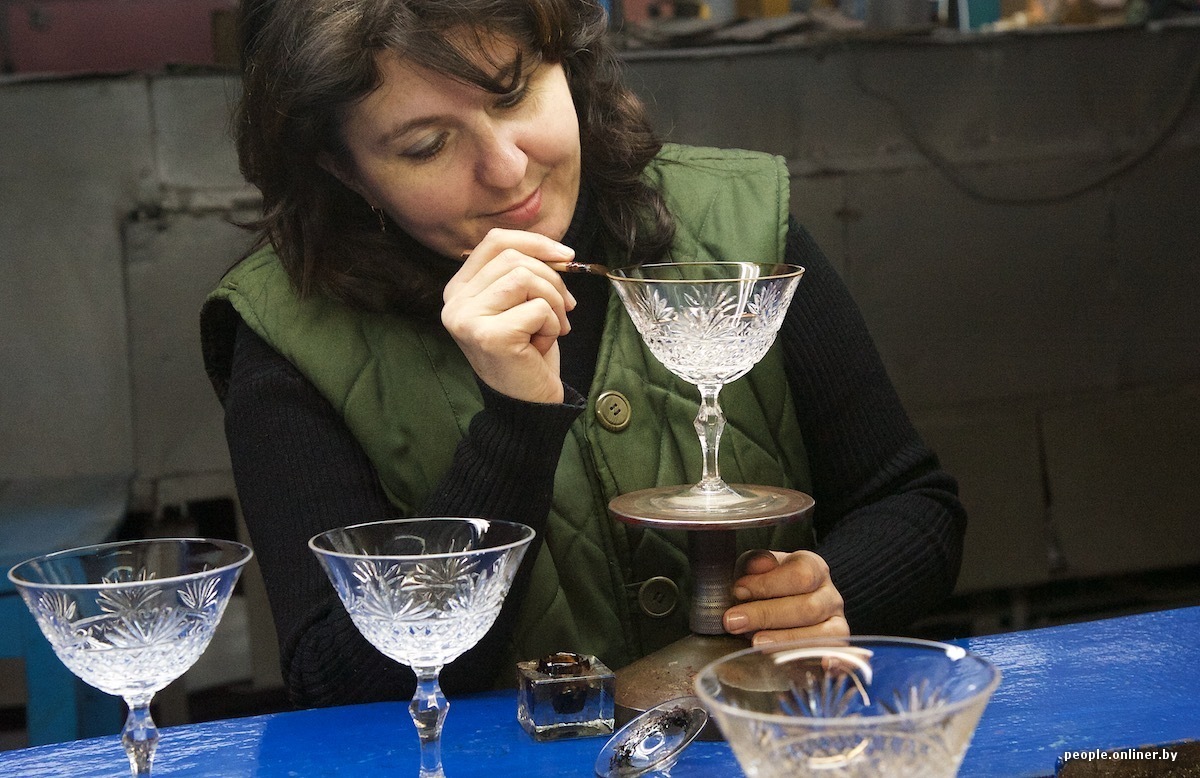
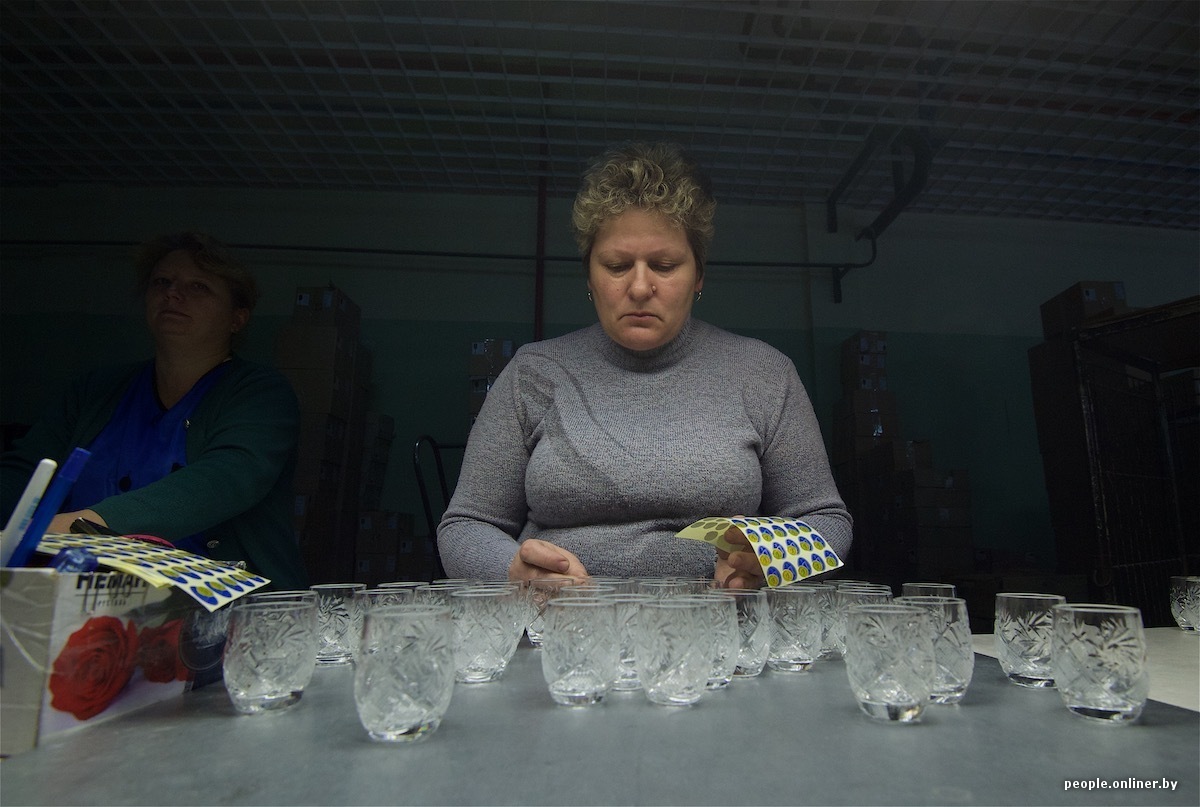
Жизнь любого изделия на заводе завершается в отделе упаковки. Там же располагается последний пункт контроля качества.
Источник
Если у вас есть производство или сервис, о котором вы хотите рассказать нашим читателям, пишите Аслану (shauey@yandex.ru) и мы сделаем самый лучший репортаж, который увидят не только читатели сообщества, но и сайта Как это сделано
Еще раз напомню, что посты теперь можно читать на канале в Телеграме
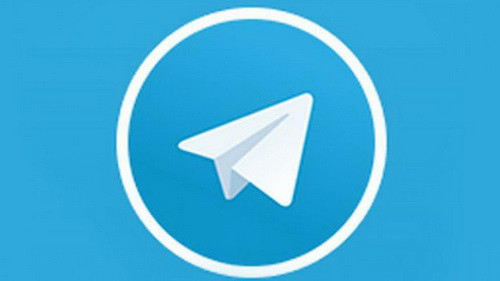
и как обычно в инстаграме. Жмите на ссылки, подписывайтесь и комментируйте, если вопросы по делу, я всегда отвечаю.

Жми на кнопку, чтобы подписаться на "Как это сделано"!

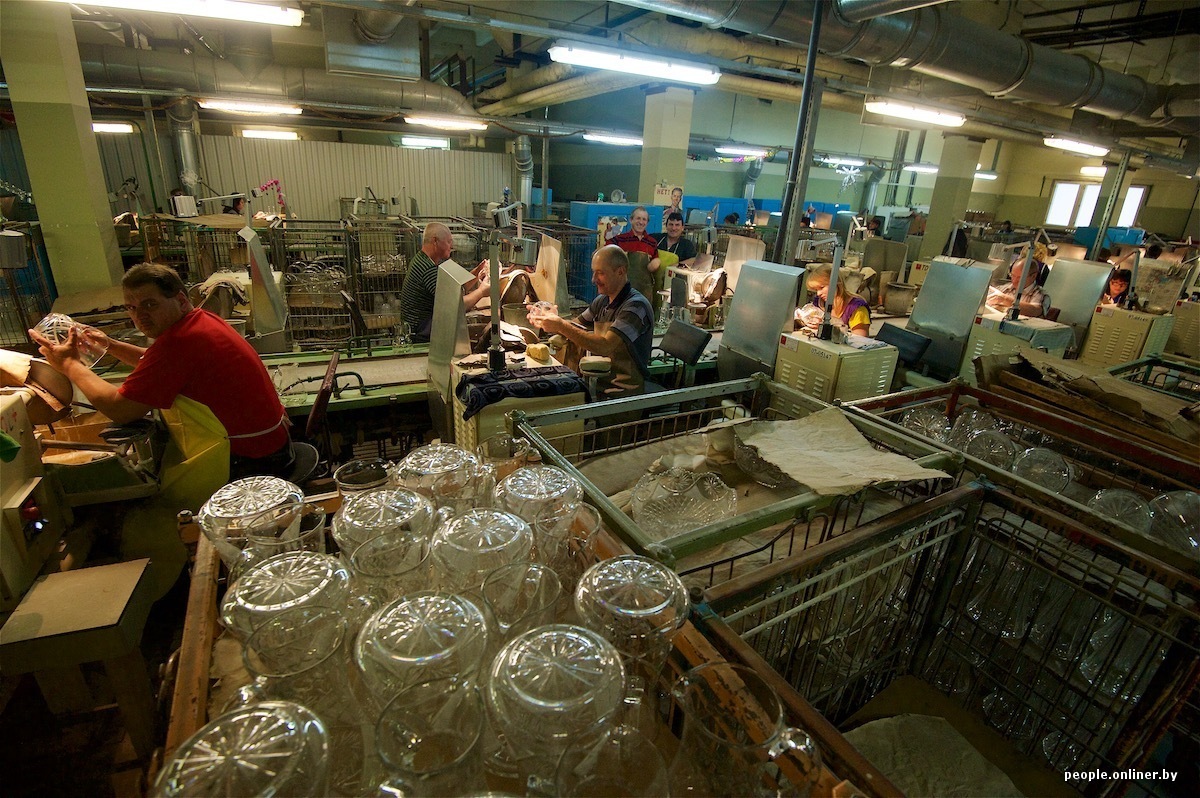
Производство хрусталя начинается в пыльном цеху, где сочиняется шихта. Шихта — сумма песка, поташа и оксида свинца. В хрустале завода «Неман» 58% кварцевого песка и 24% свинца. Остальное — добавки. Песок украинский. В белорусском много железа — стекло получается зеленым. Песок очень-очень мелкий — отсюда и пыль.
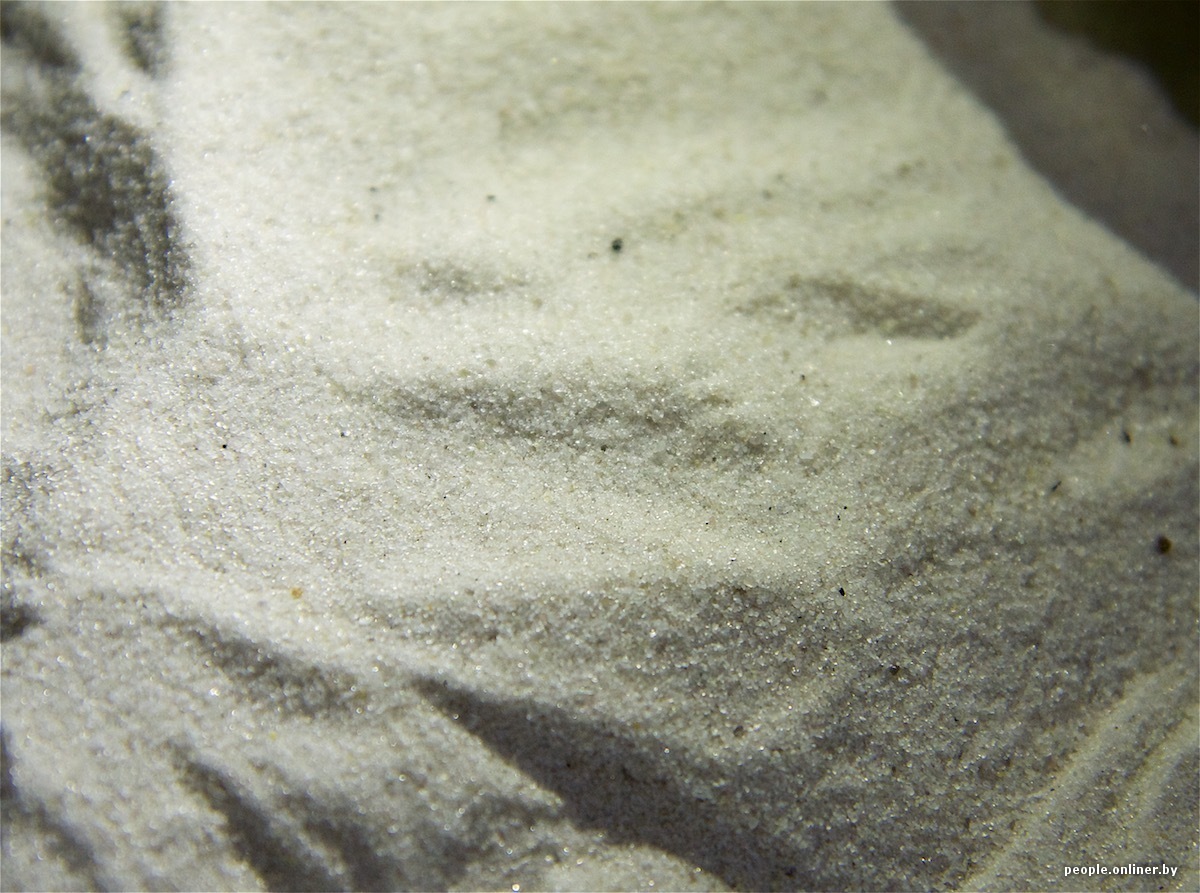
В двухэтажном помещении все зависит от компьютера, который настраивает дозаторы согласно рецептуре. Нужное количество сырья опускается на ленту конвейера и едет к контейнерам, перемешиваясь в однородную массу.
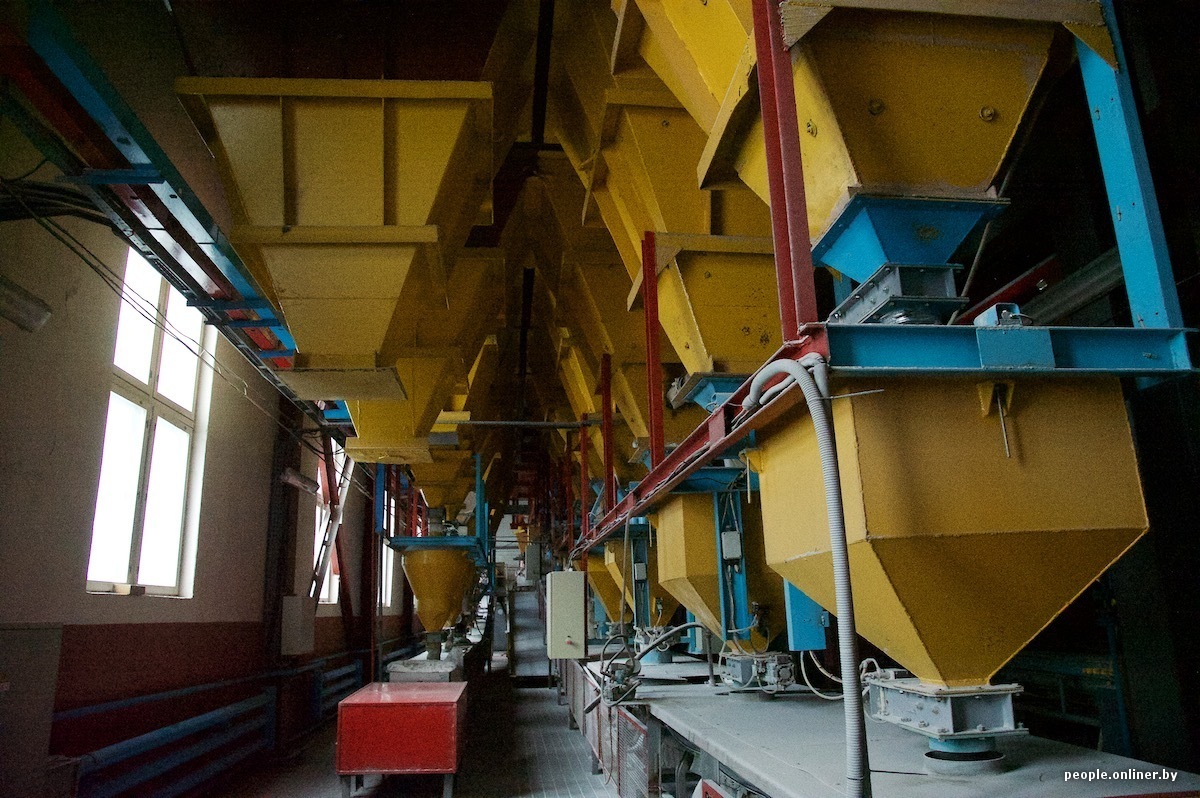
В принципе, стекло и хрусталь — это одно и то же. Правда, в хрустале есть свинец, который окрашивает здешние бочки в оранжевый «вырви глаз» цвет.
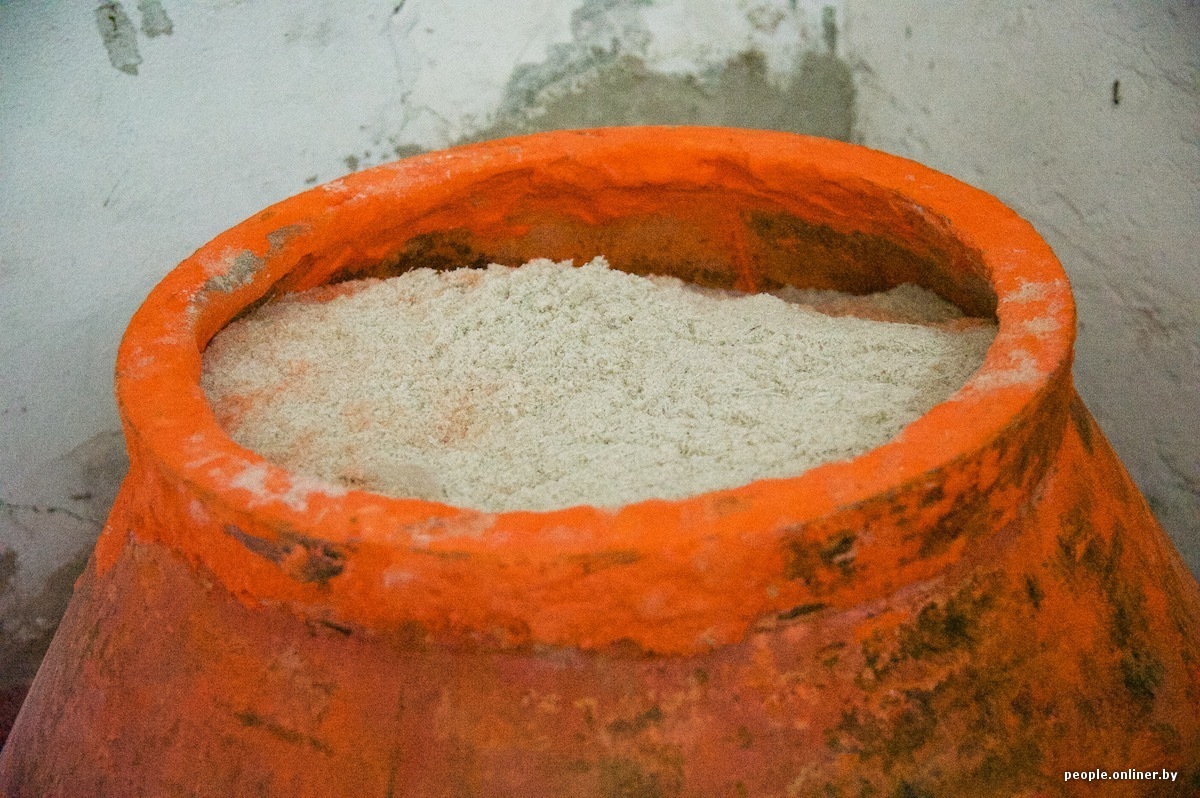
Заготовленная шихта счастливо попадает в самый эффектный цех завода. Прямо декорации из клипов зрелого Rammstein. Тут все пышет жаром. Печей в цеху две. Раньше, говорят, было больше десятка. Печи — почти что вечный двигатель. Паузы делают только вынужденные — c отвлечением на ремонт. Срок непрестанной работы — пять-семь лет.
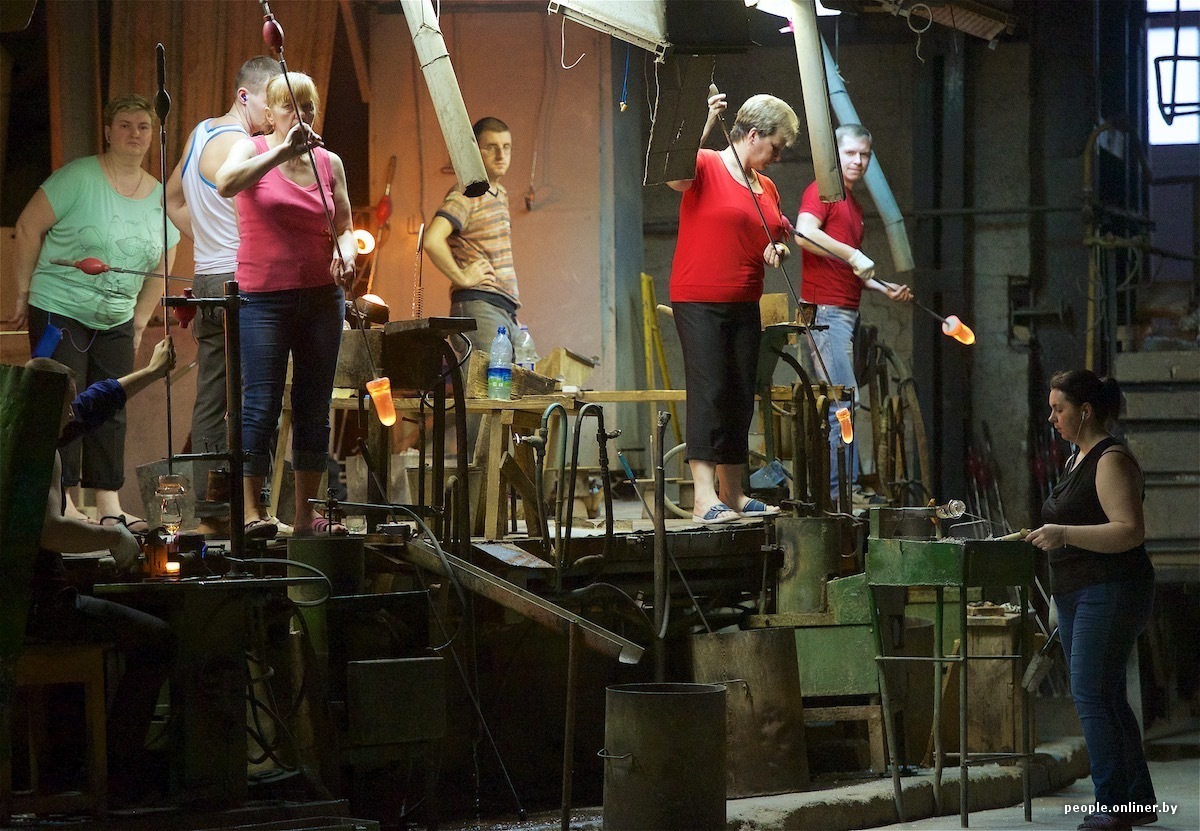
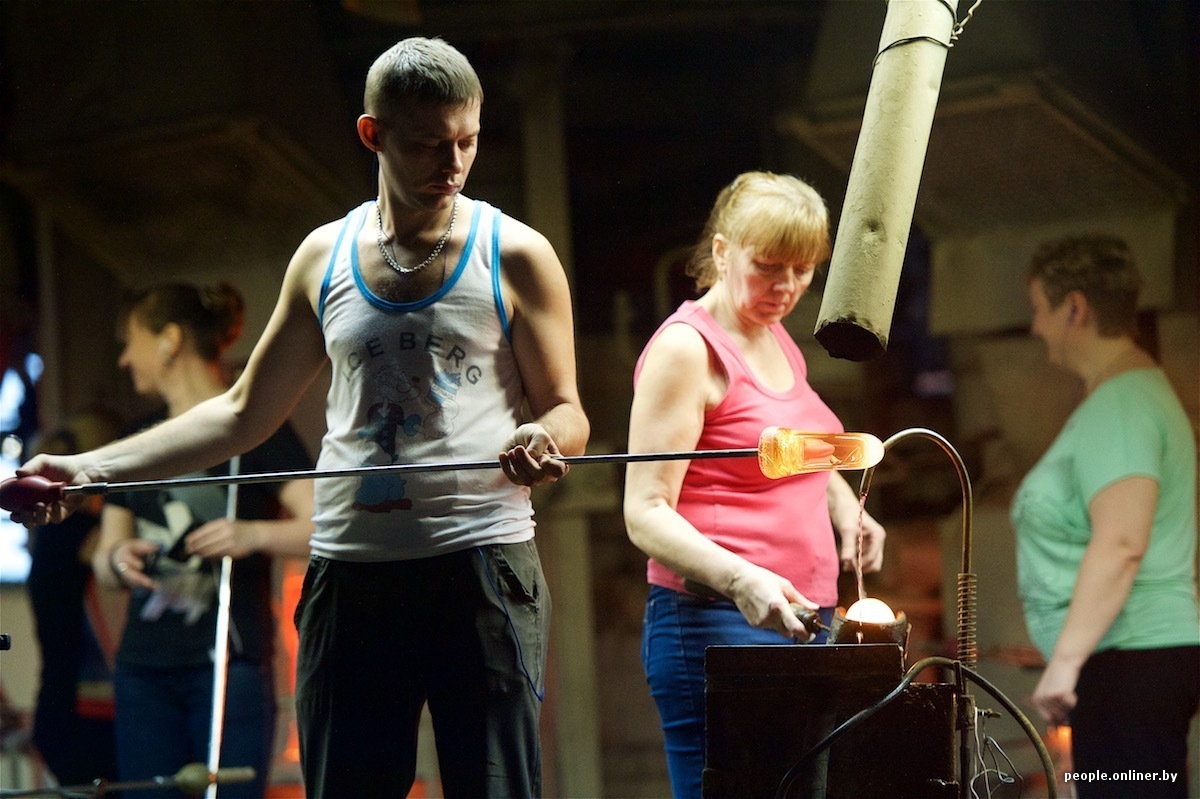
Оттого стекло здесь делается в три смены. Первая — 8:00—16:00, вторая — 16:00—0:00, третья — 0:00—8:00. Рабочий день предполагает получасовой обед и два «перекура» по 15 минут. График у здешних тружеников стекольной отрасли скользящий.
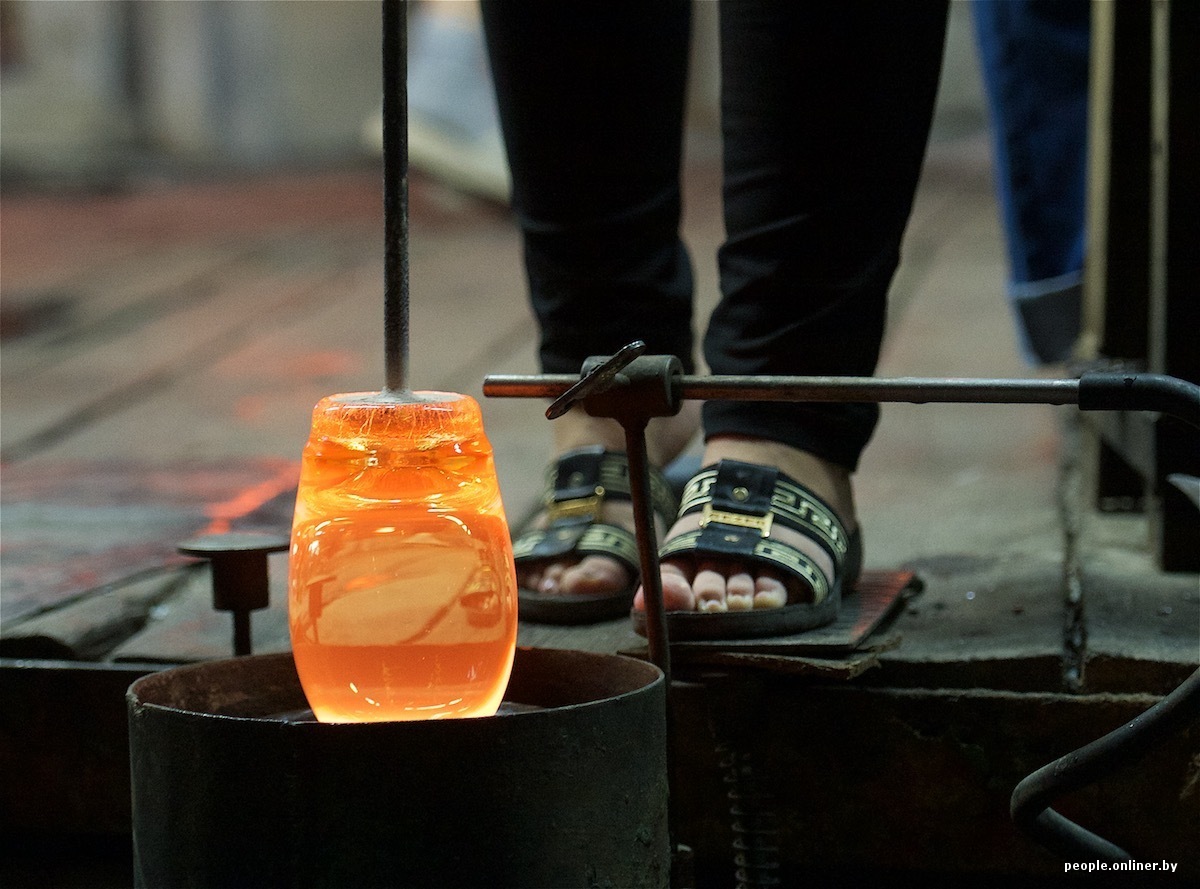
В цеху ощутимо жарко. Участники бригад челночат между печами и чанами с водой в достаточно домашнем виде — майки, сланцы. Говорят, им предлагали униформу, но идея не получила поддержки.
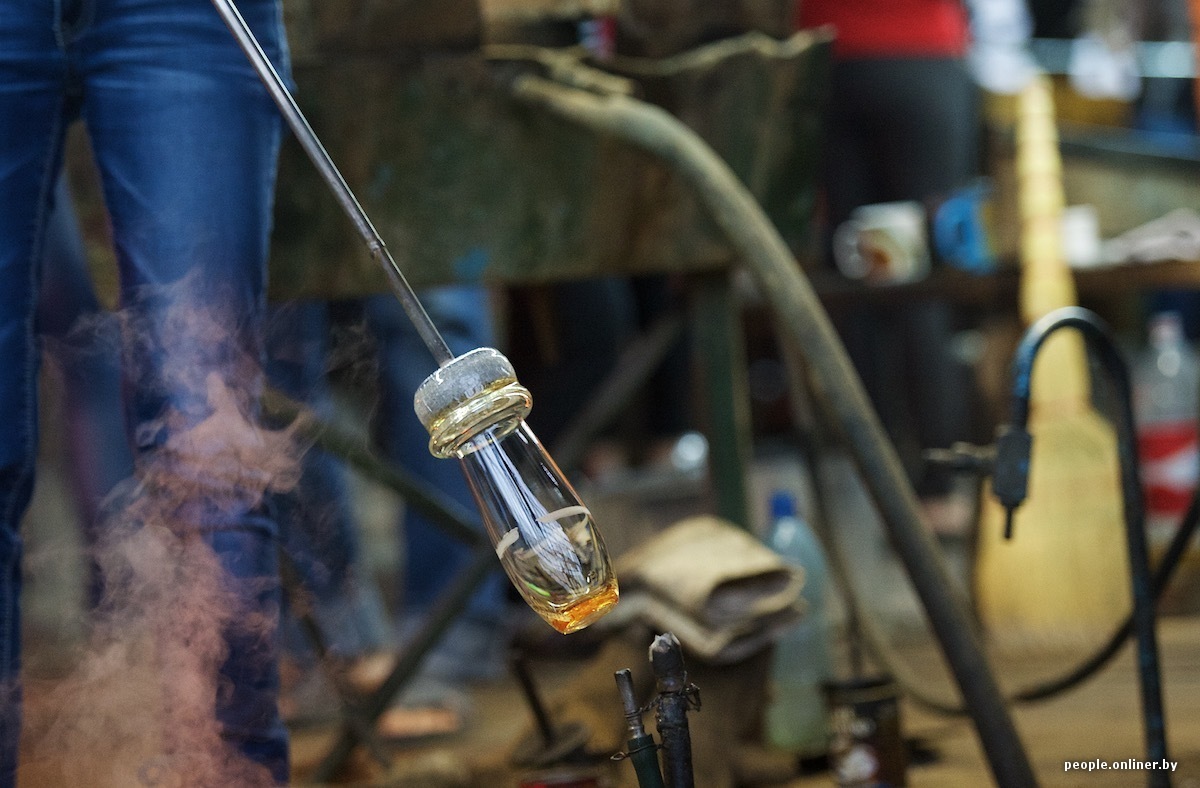
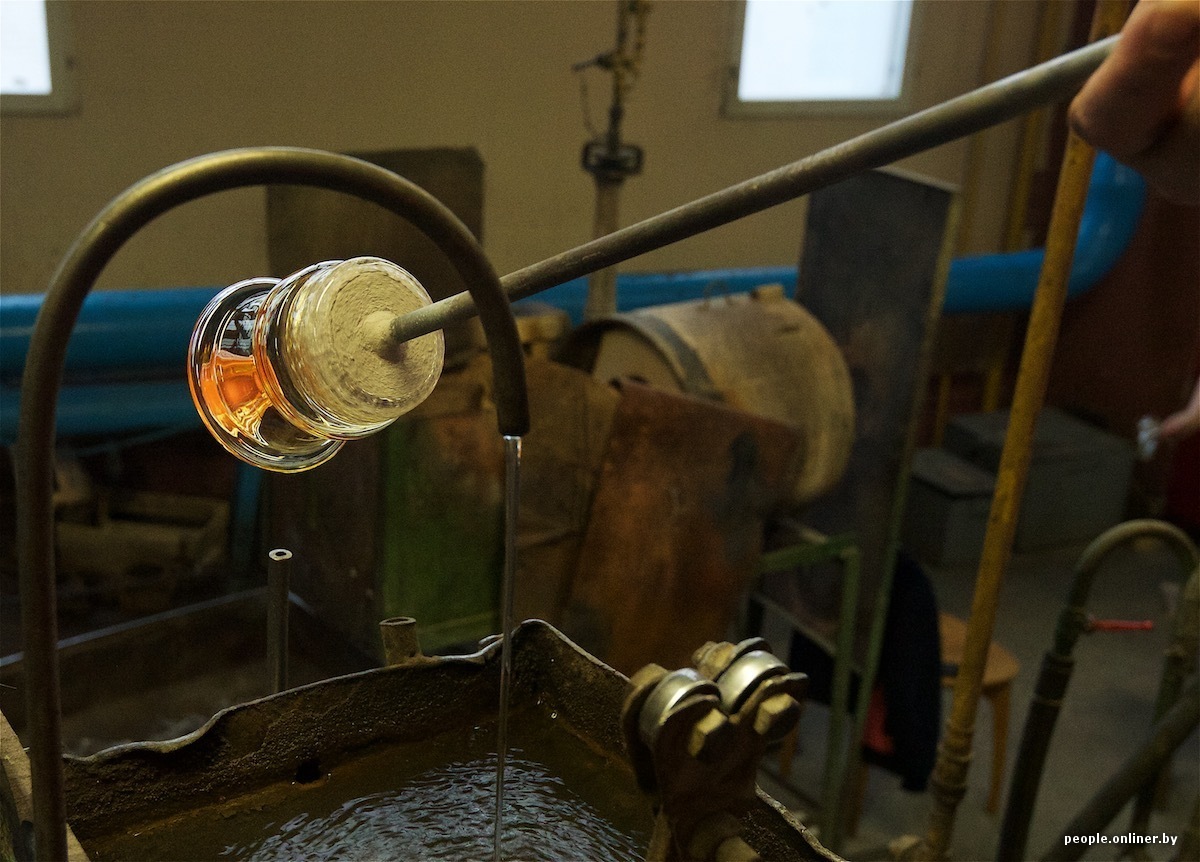
Температурный «Ташкент» дополняется интенсивным шумом. Кто-то просто его не замечает. Кто-то понижает наушниками.



Работники поделены на бригады. В каждой по шесть человек. Два выдувальщика. Это люди с «волшебными палочками», которые придают раскаленному стеклу необходимую форму силой своих развитых легких. Они делают пойло — верхнюю часть бокала. К выдувальщикам добавляется пара наборщиков. Первый подает сырье для ножки, второй — для донышка. Дополняют бригаду прессовщик и бригадир, заодно занятый еще и шлифовкой.
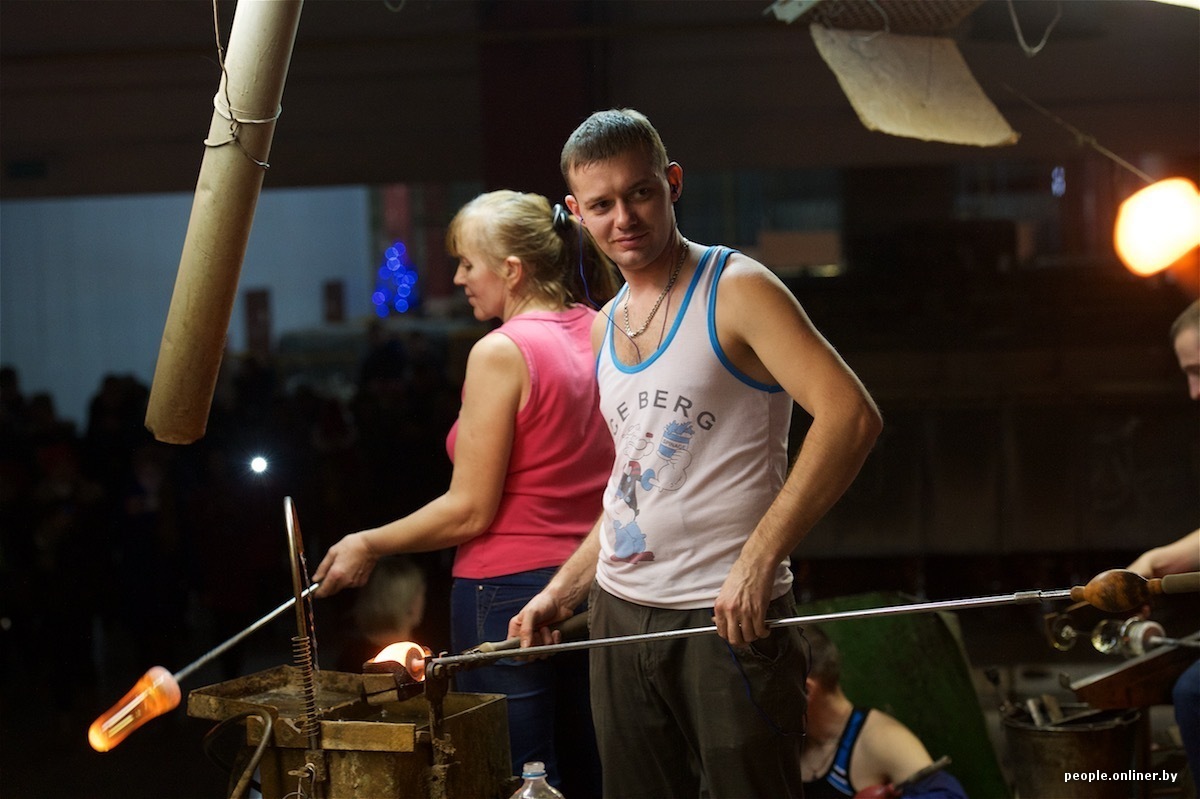

Выдувальщик — топовая профессия на заводе, которая предполагает самую высокую вредность. Человек, получивший семь лет «горячего» стажа, имеет право уйти на пенсию раньше. Женщины — в 45 лет, мужчины — в 50.
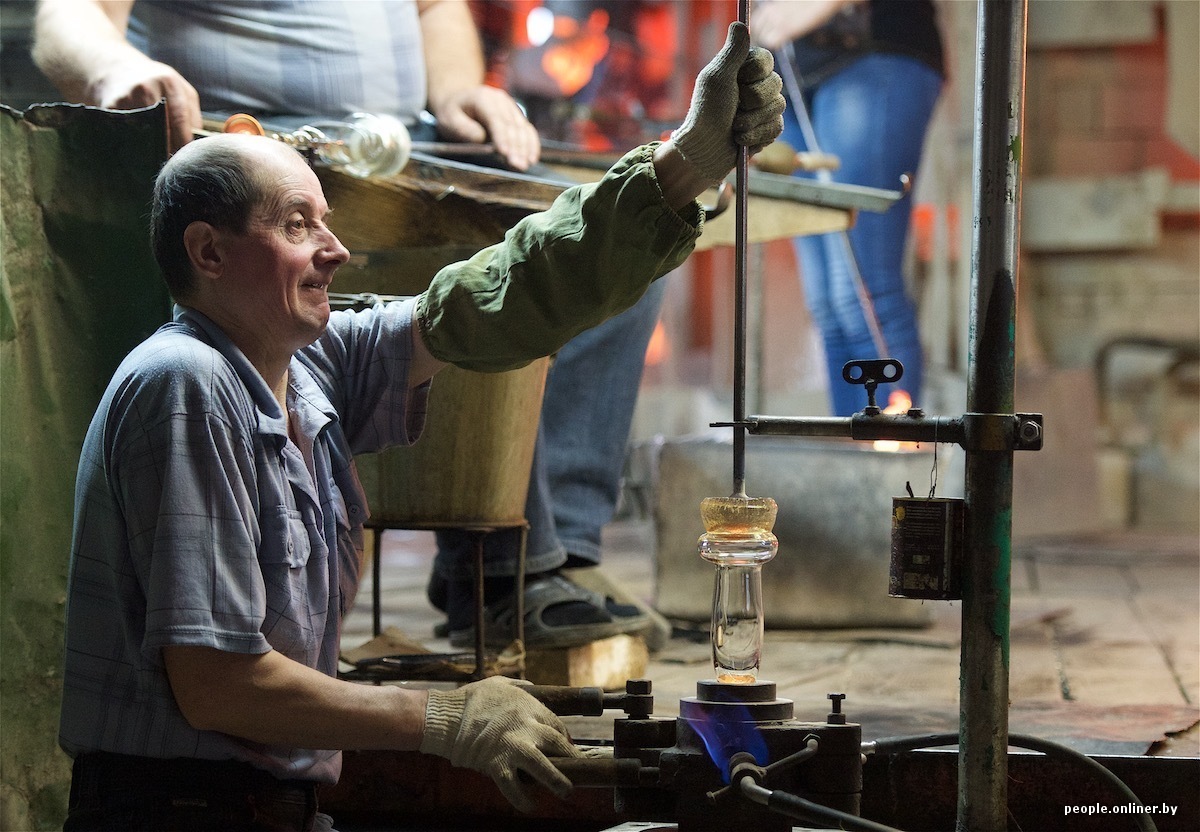
Заготовки будущих изделий попадают с горячего производства на широкую ленту конвейера, который направляет их в намного более тихое и прохладное помещение.
Там с будущих бокалов, ваз и прочей заводской продукции снимается напряжение, чтобы стекло не растрескалось. Плюс заготовки остывают.
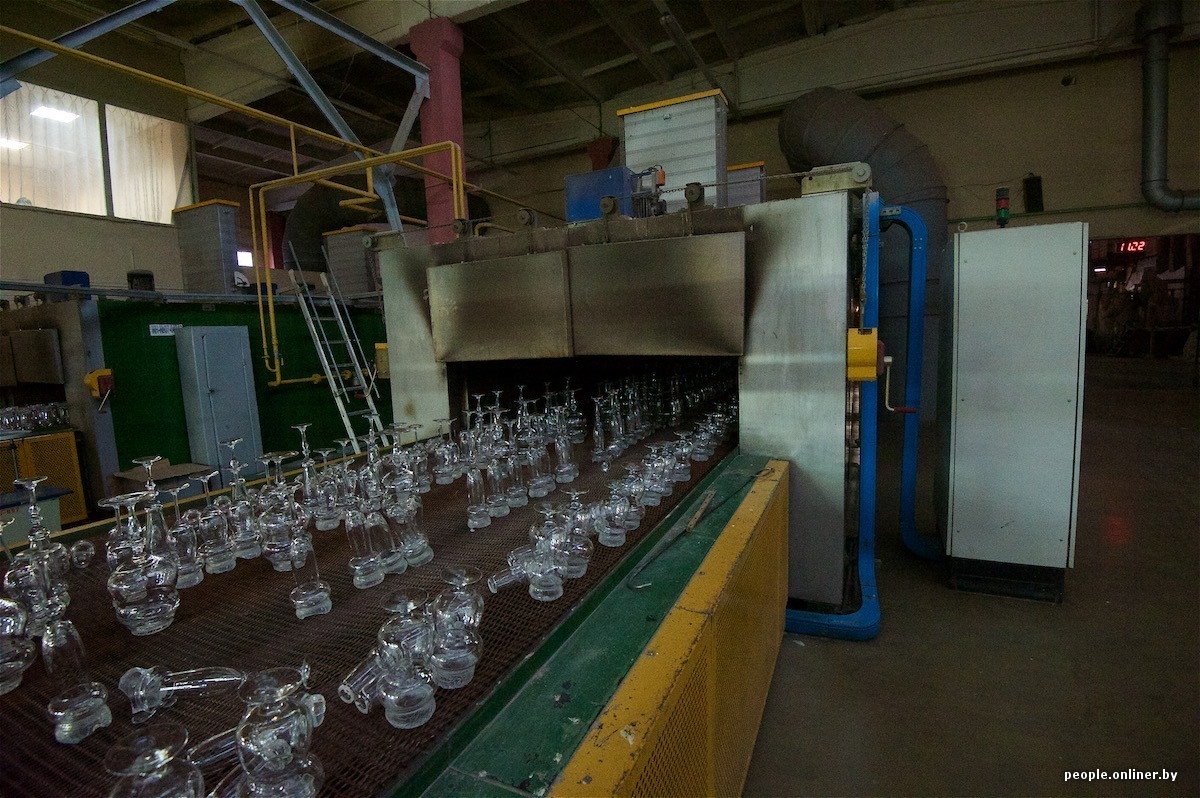
У каждого изделия своя высота резки. Сперва наносятся необходимые метки. По ним с помощью газовой горелки осуществляется резка. Все остатки попадают в контейнер, затем измельчаются на специальной мельнице и снова становятся сырьем.
Здесь же находится первый отдел товарного контроля (ОТК). Наличный брак отправляется на переплавку. К слову, когда-то работникам приходилось расплавлять и хорошо выполненные изделия. Просто в СССР начали бороться с алкоголем, и оттого поступило указание отправлять в огонь все рюмочные и другие формы, связанные с выпивкой. В итоге из графинов делали вазы для фруктов.
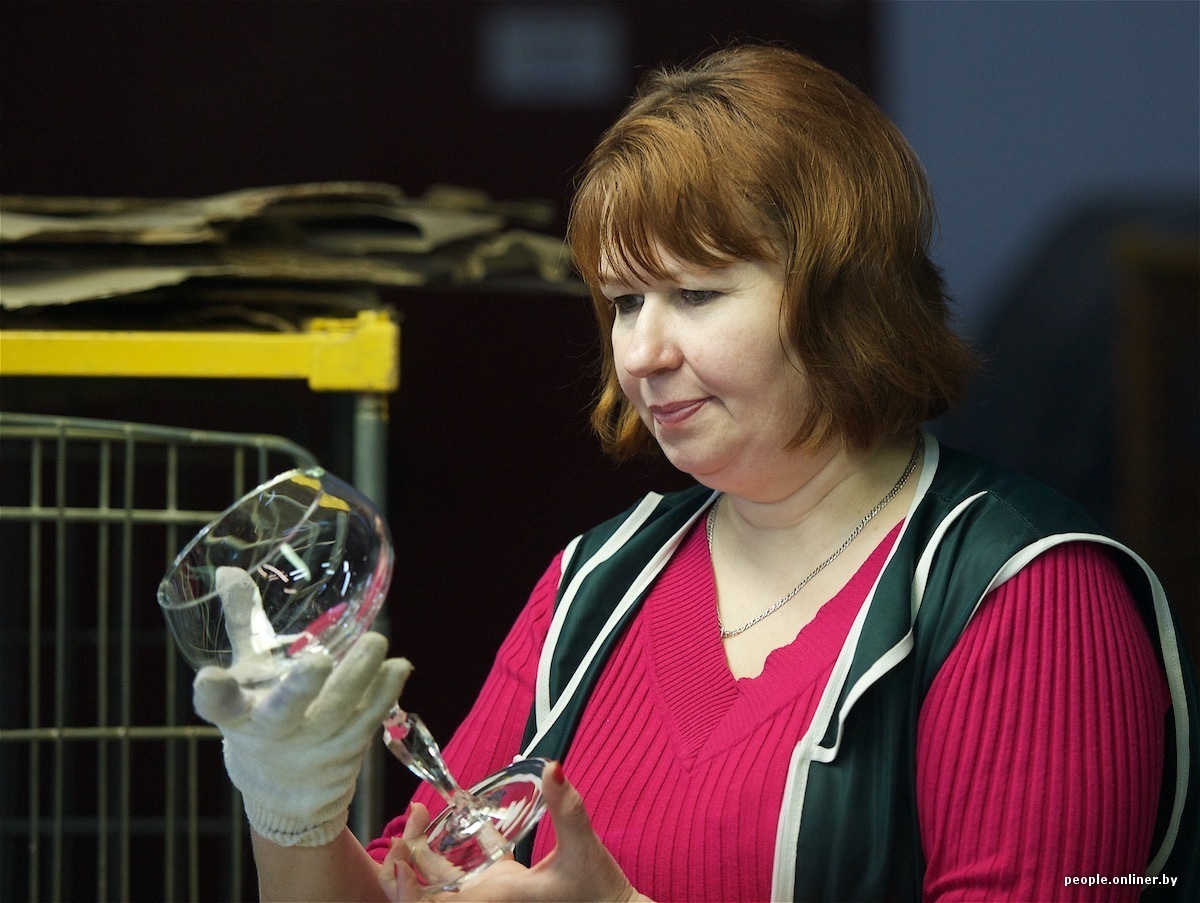
На ленте виднеются почти что вазы — бокалы каких-то нереальных размеров. Оказывается, это заказ из Азербайджана. Вообще, 65% продукции отправляется на экспорт.
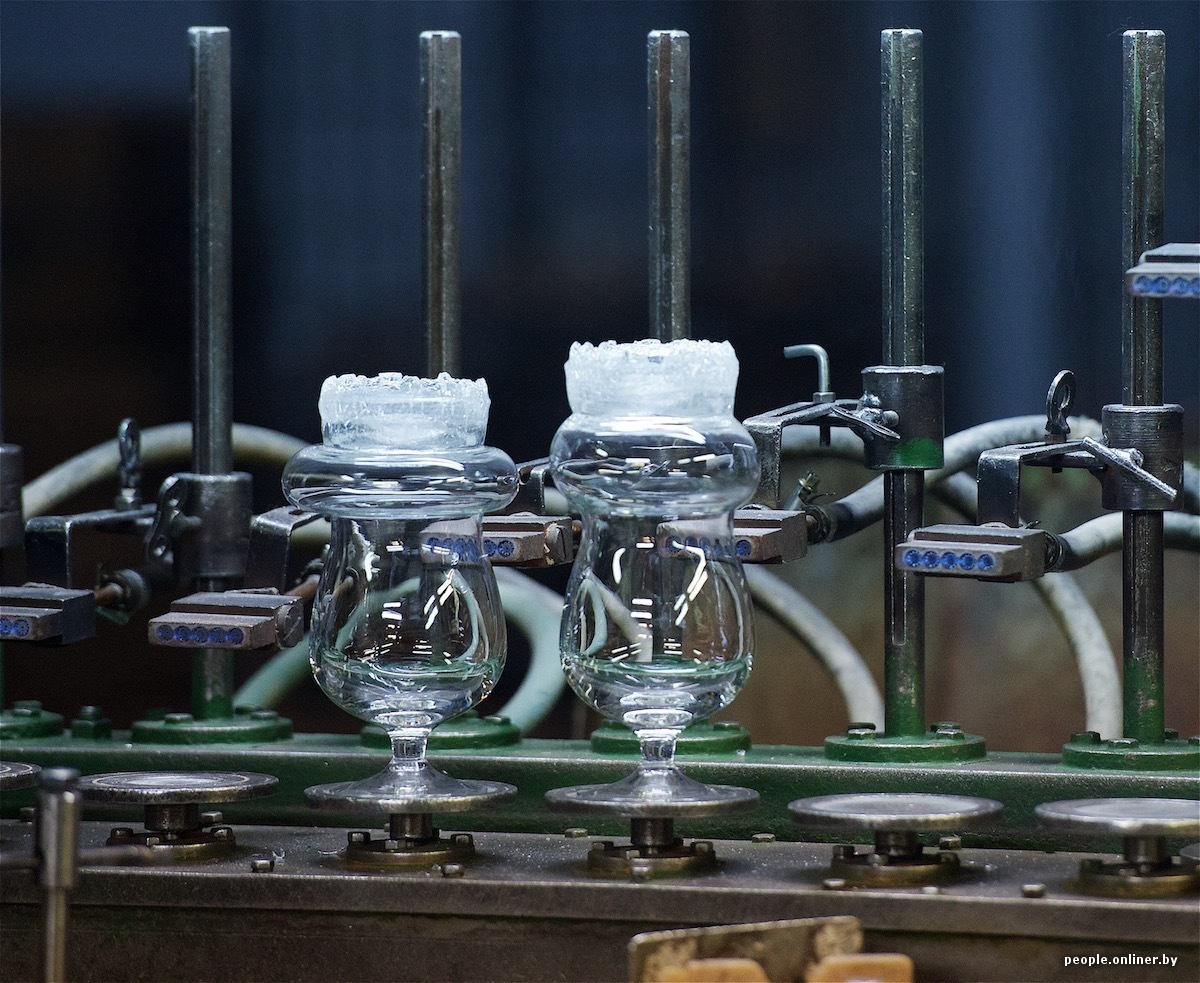
— У нас этот хрусталь покупают даже американцы, — хвалятся работники.
Продукция доставляется из Беларуси в США в контейнерах. Более всего в ней заинтересована компания North American Crystal, с которой стеклозавод сотрудничает примерно десять лет.
После первого контроля качества некоторые бокалы/стаканы/рюмки аккуратно упаковываются, некоторые поступают в специальный станок для шлифовки острых краев. Чтобы никто не порезался. Процесс называется «отопка».
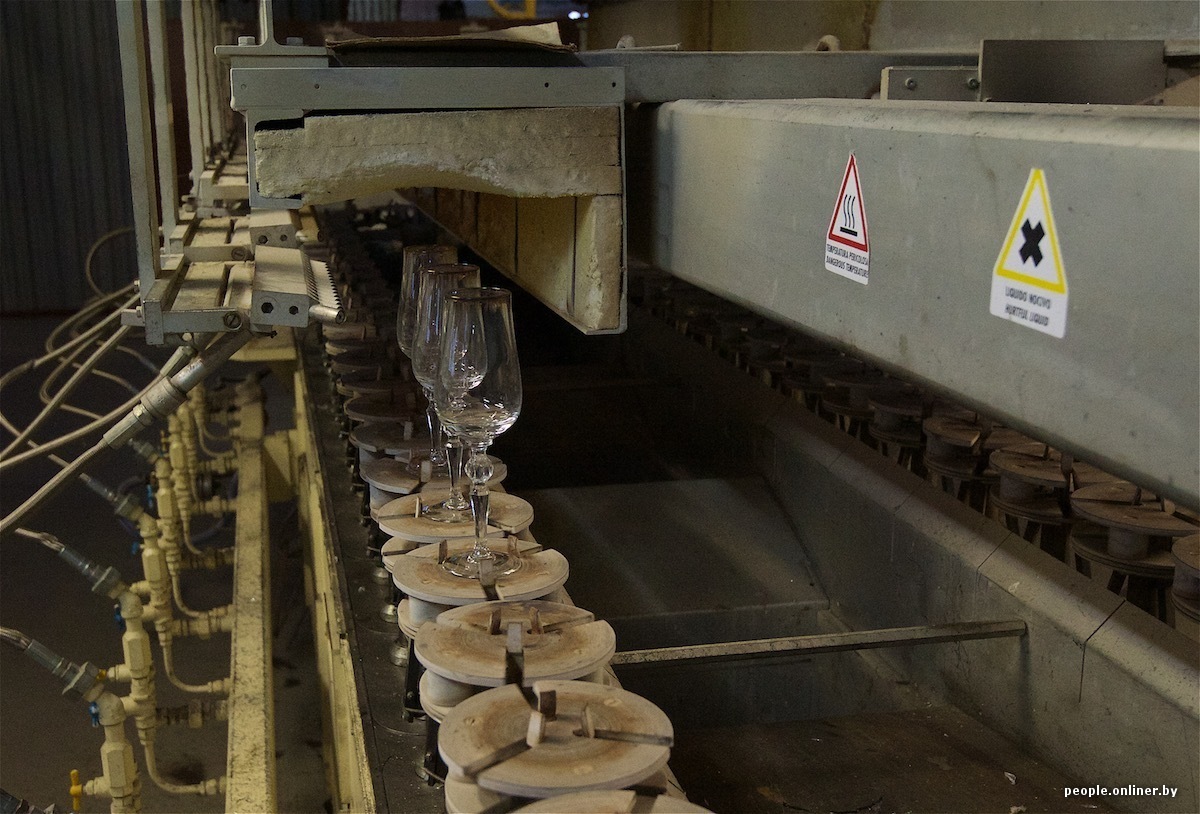
По завершении отбивки и отопки стакан попадает в цех обработки. Тут на него глиной наносятся необходимые метки. Все делается руками при помощи кисти. Затем размеченное изделие уходит к резчикам по ленте конвейера. Каждый из них знает, что нужно взять в работу. Здесь же находится второй пункт контроля качества.
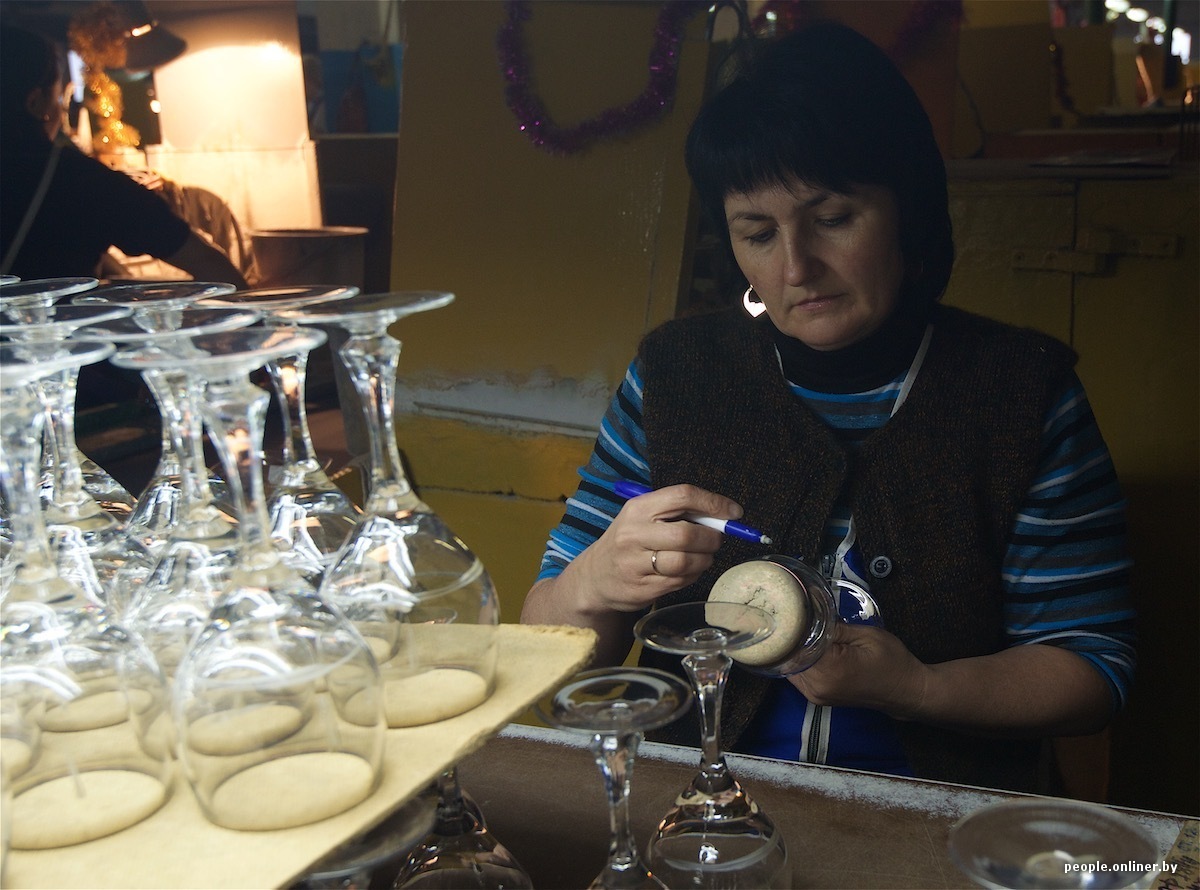
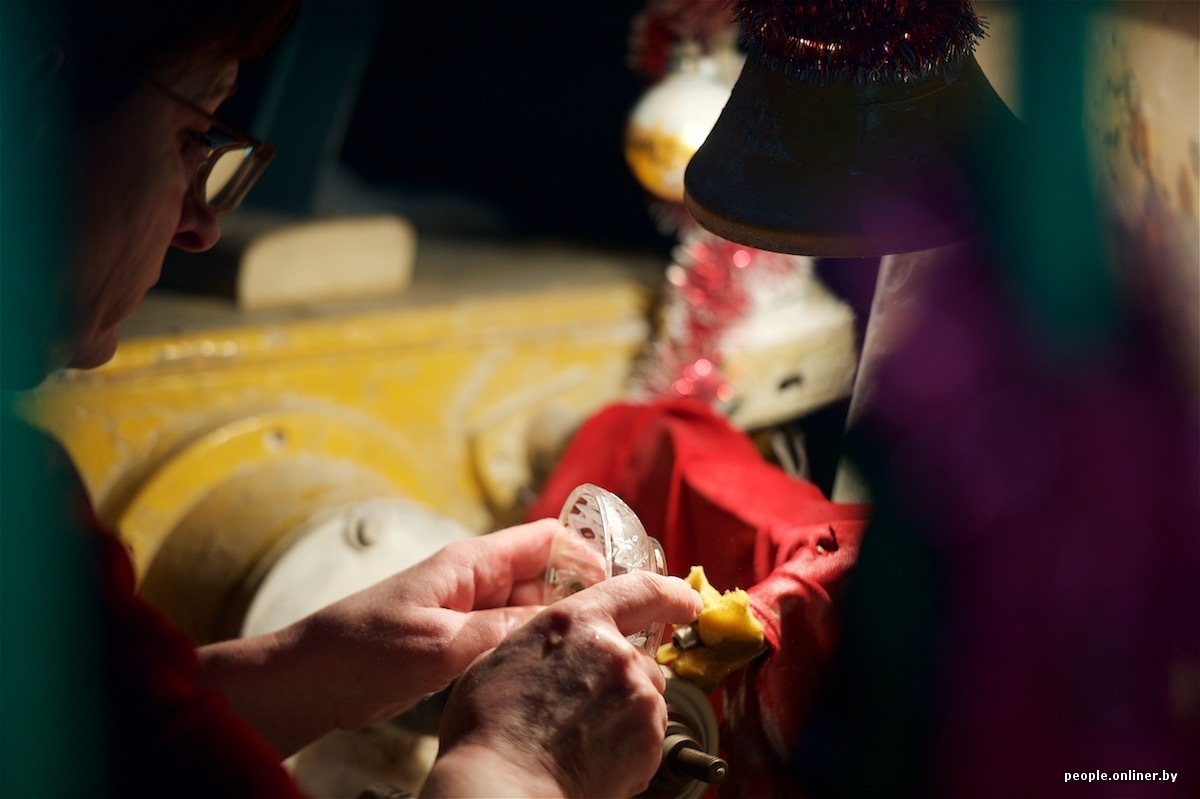
Цех резки — гулкое помещение с высокими потолками. Тут работают с помощью алмазных резаков. Один из резчиков подходит с вазой наперевес. Ваза выступает в качестве то ли экспоната для демонстрации, то ли оружия для угрозы.
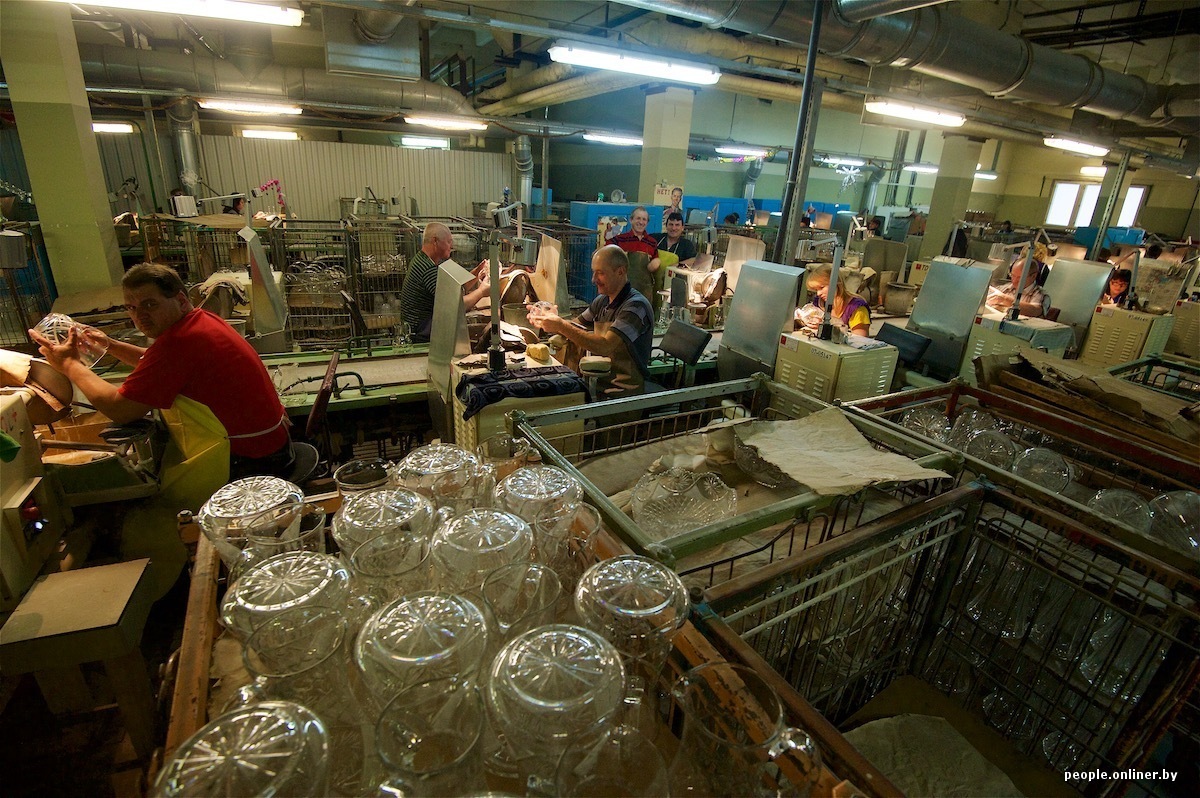
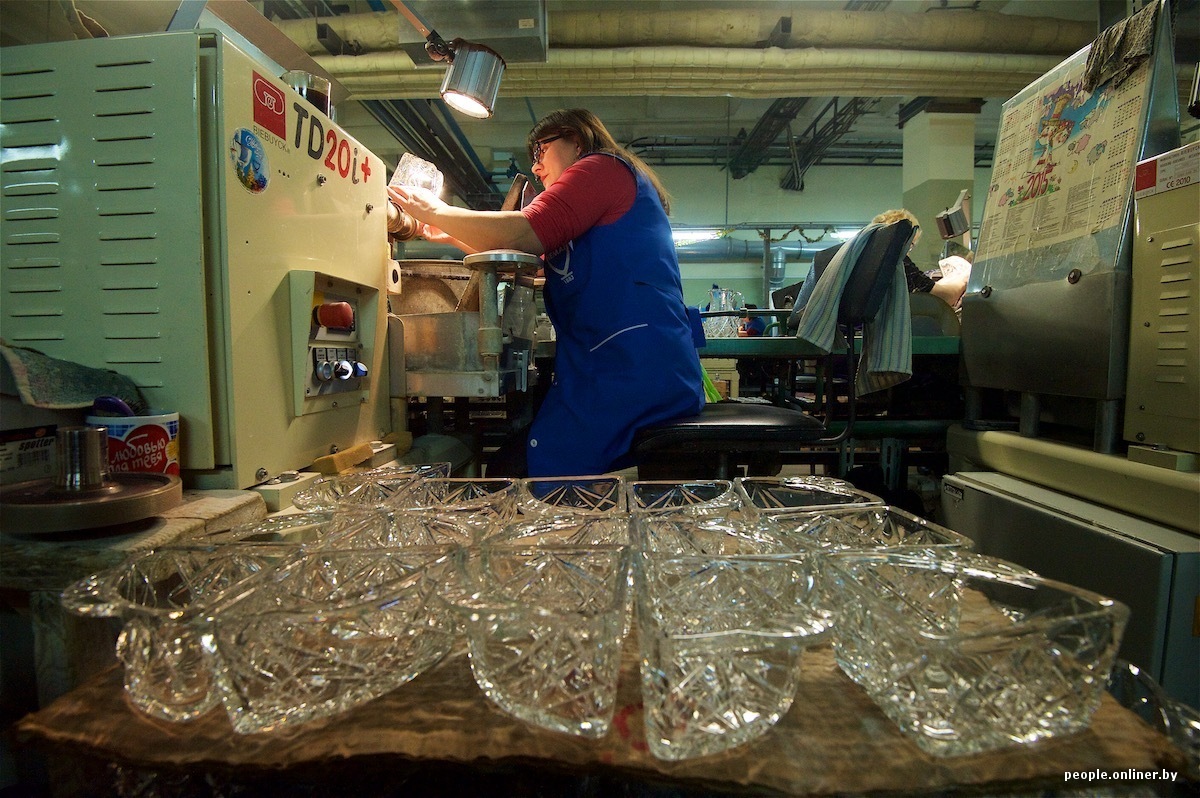
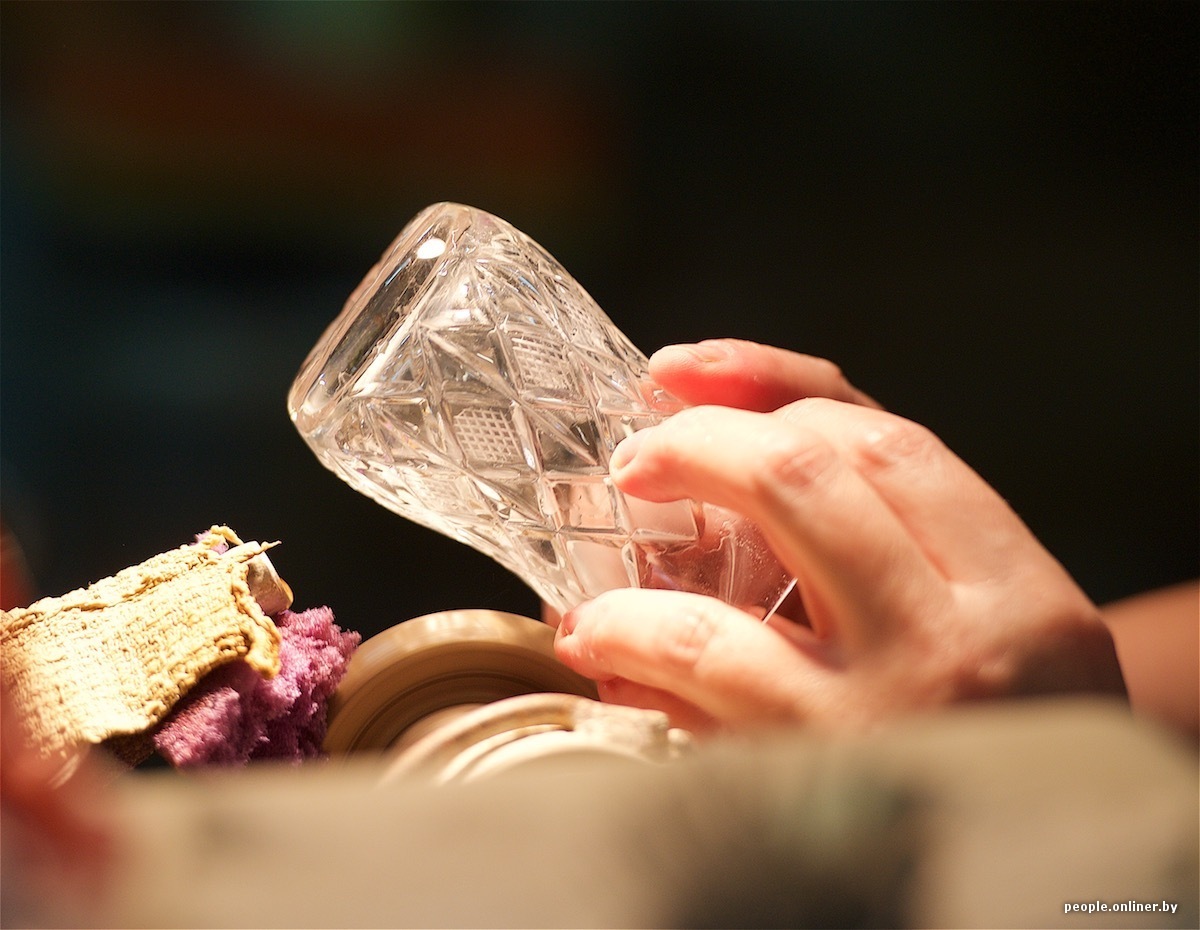
Нарезка сменяется химполировкой. Дело в том, что изначально изделие получается матовым. А обработка кислотами придает ему должный товарный блеск.
Пыль и огонь заводских цехов дополняются водой, которой в изобилии на полу. Работники шлепают по лужам, наполняя большие кассеты. В них можно загрузить почти все, что производится на заводе.
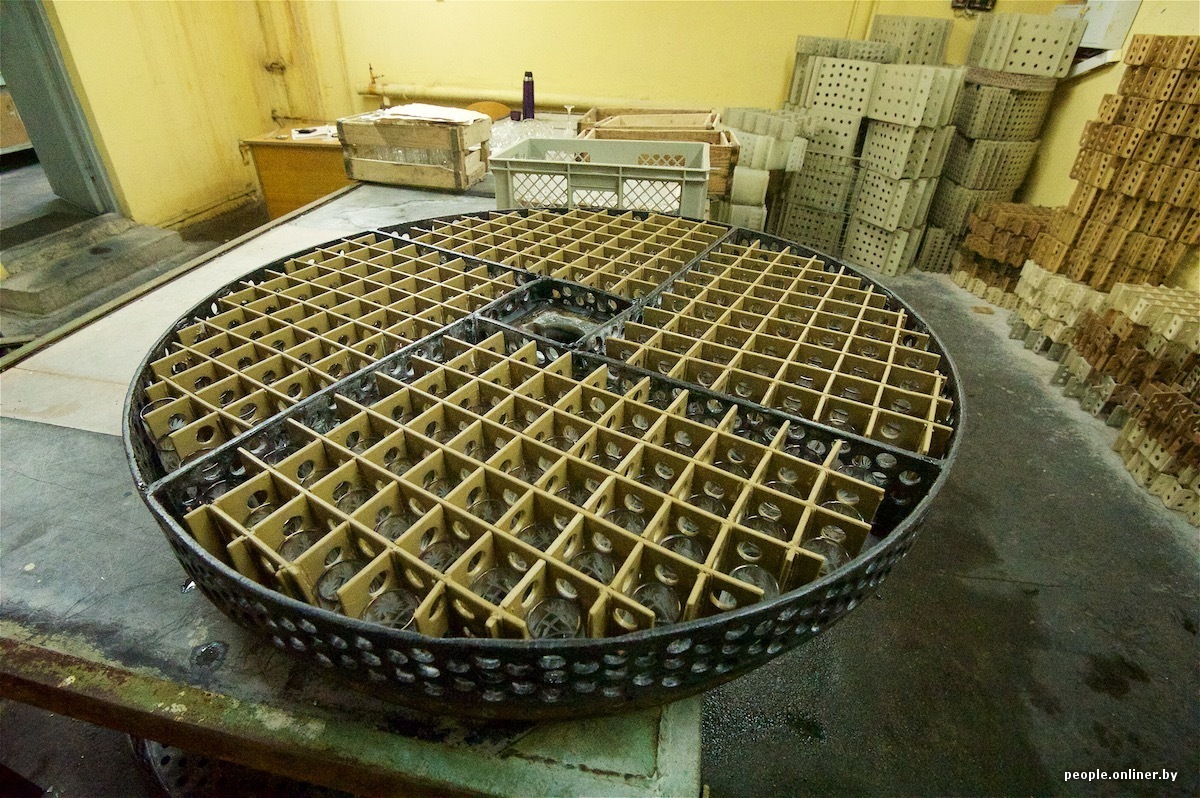
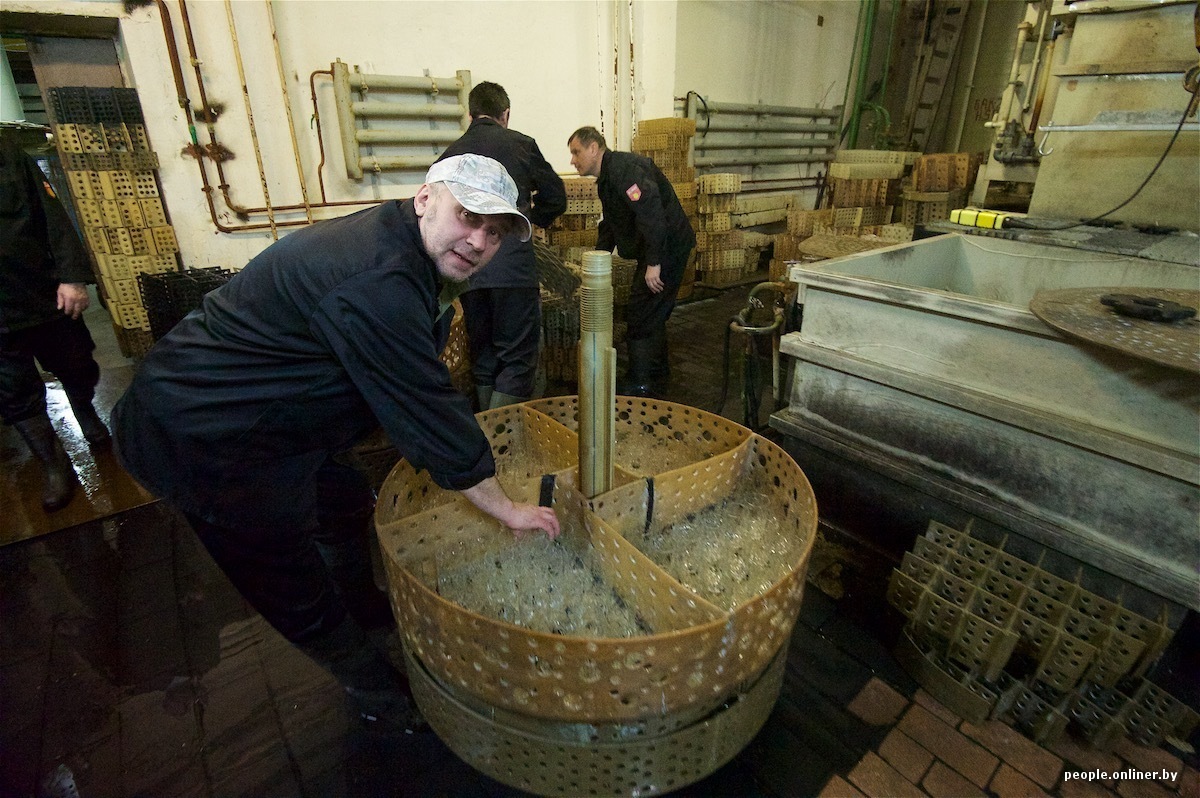
Упакованные кассеты прикладываются друг к дружке, формируя гигантский ролл. Его цепляют тросом и отправляют в ванную с кислотой. Кассеты постоянно вращаются. Мойка длится примерно 40 минут. Стаканы полируются плавиковой и серной кислотами, а на прощание обрабатываются водой.
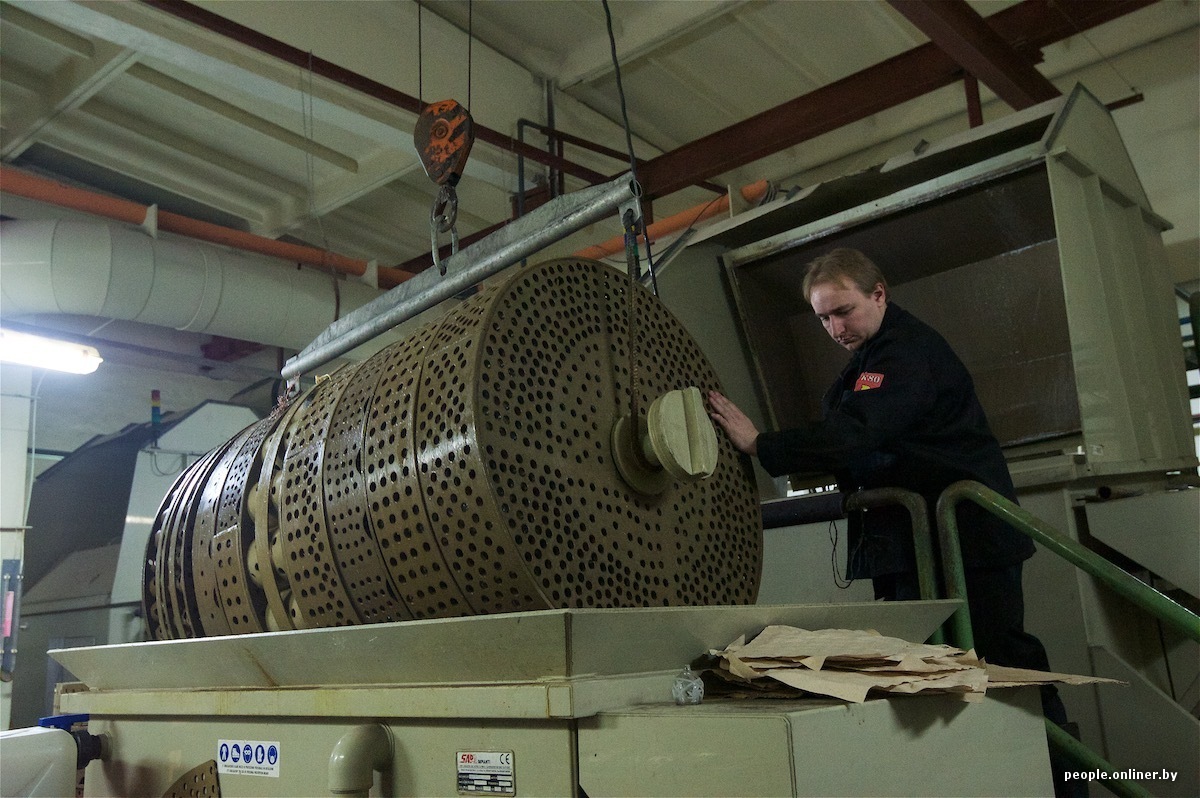
В принципе, все готово. После купания в кислоте стакан могут отправить на дополнительную резку или для наведения финального марафета — например, нанесения золотого кантика. Соответствующая работница занимается этим с 7:00 до 15:00. На каждый бокал наносится настоящее золото.
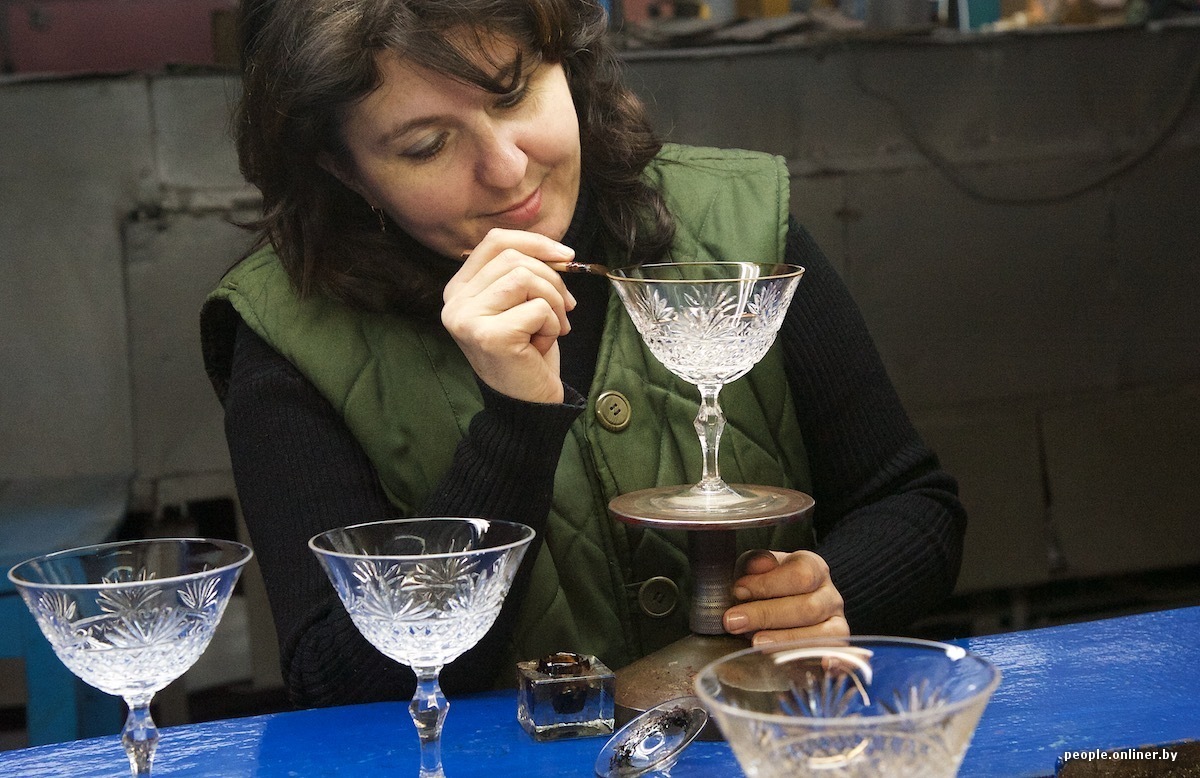
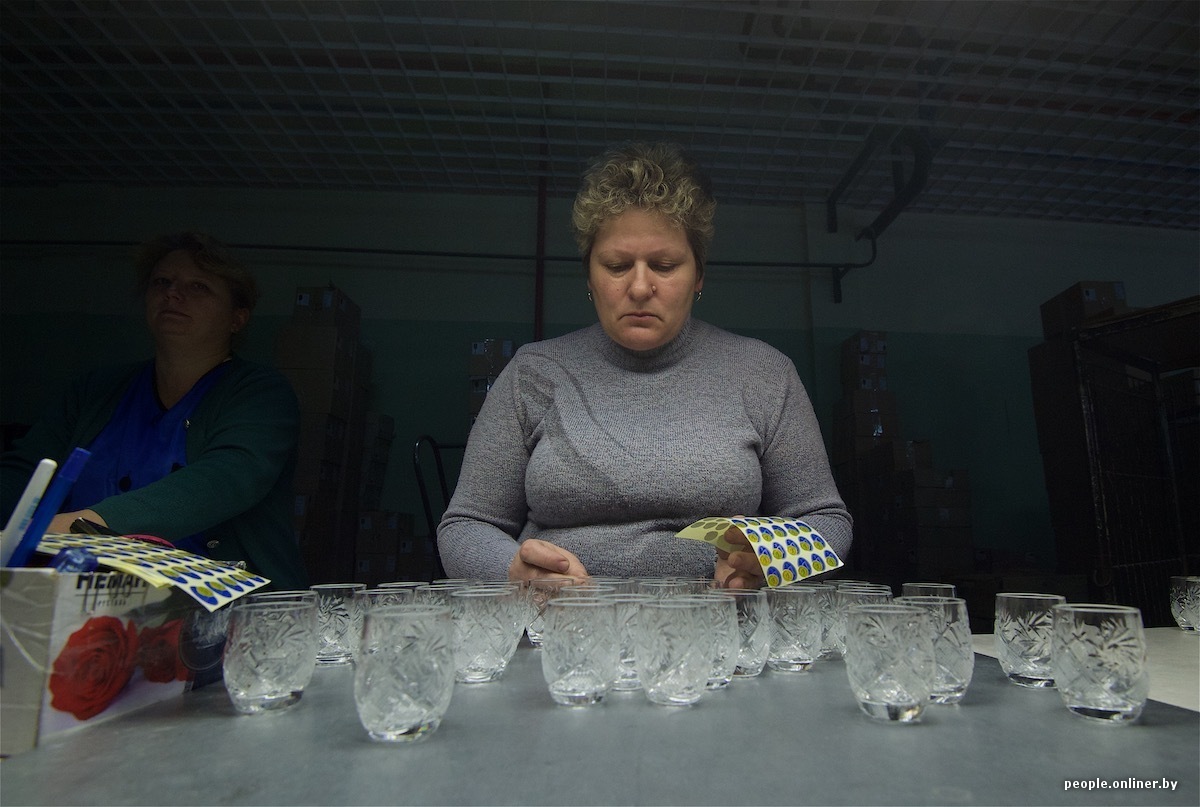
Жизнь любого изделия на заводе завершается в отделе упаковки. Там же располагается последний пункт контроля качества.
Источник
Если у вас есть производство или сервис, о котором вы хотите рассказать нашим читателям, пишите Аслану (shauey@yandex.ru) и мы сделаем самый лучший репортаж, который увидят не только читатели сообщества, но и сайта Как это сделано
Еще раз напомню, что посты теперь можно читать на канале в Телеграме
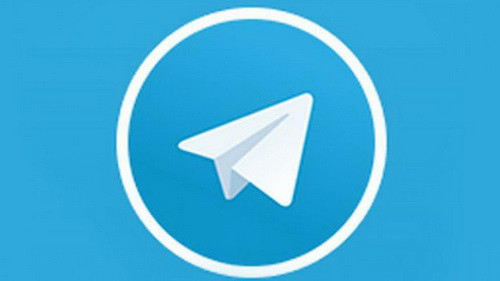
и как обычно в инстаграме. Жмите на ссылки, подписывайтесь и комментируйте, если вопросы по делу, я всегда отвечаю.

Жми на кнопку, чтобы подписаться на "Как это сделано"!

Комментарии (0)
{related-news}
[/related-news]