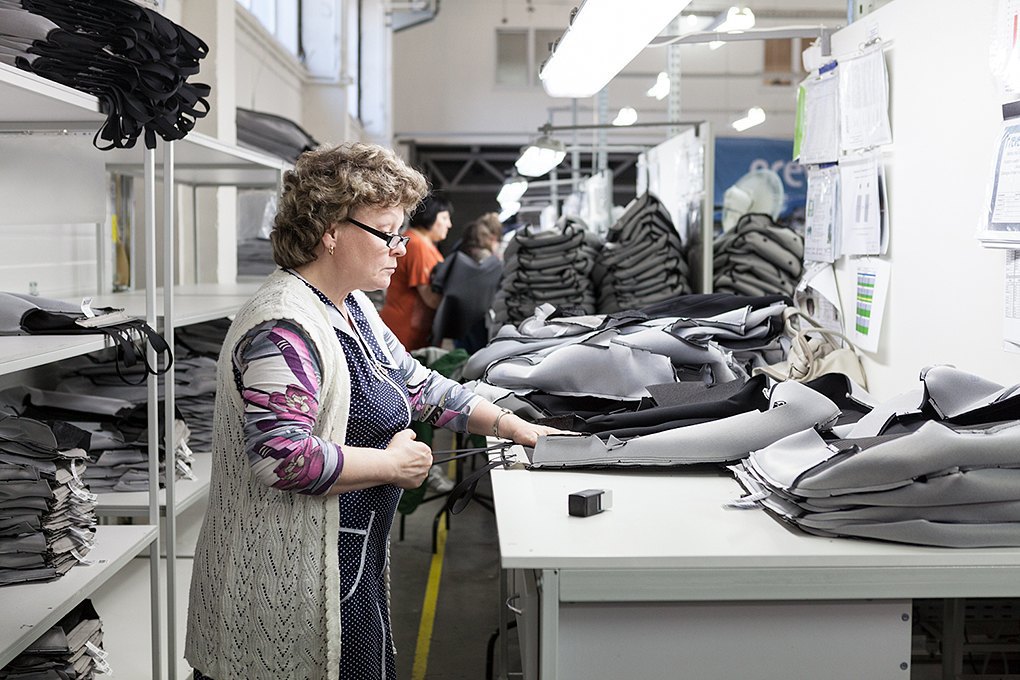
Как делают чехлы для автокресел Volkswagen
---
Компания «Превент Авто Рус» — российское подразделение немецкой компании Prevent, которой принадлежит более 35 заводов в 12 странах мира. Она производит 40% всех чехлов для автокресел в Европе (всего около 11 000 обивок в день), а в Боснии и Герцеговине компания является вторым работодателем после государства. Сейчас основной заказчик компании — концерн Volkswagen.
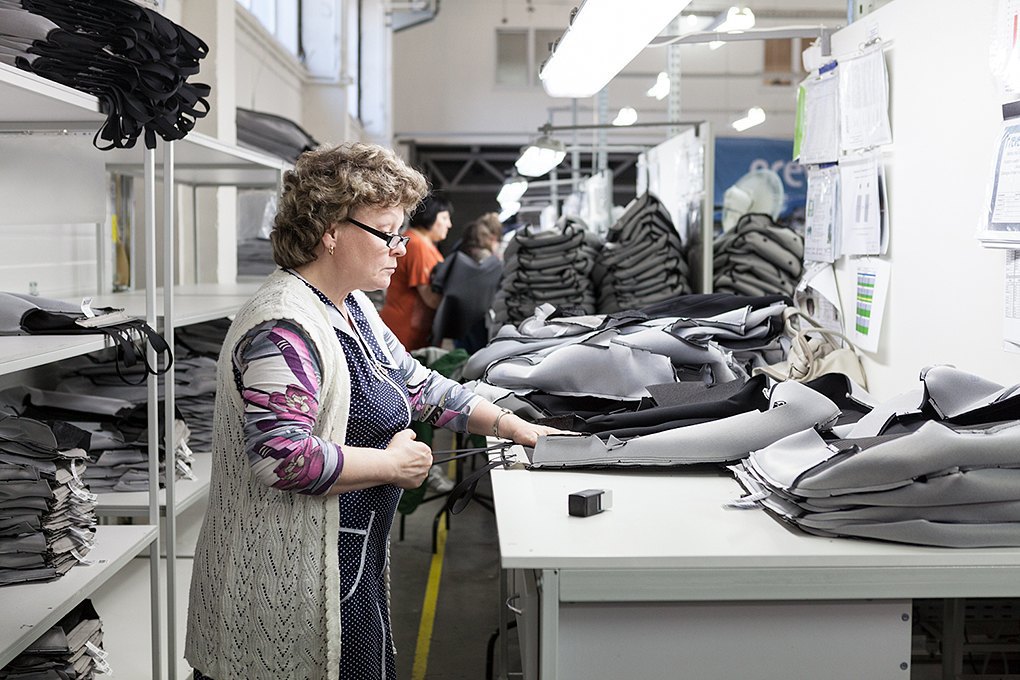
Компания работает с автогигантом не напрямую, а через производителя сидений. Стать поставщиком Volkswagen было непросто, но это стоило того. Крупные автоконцерны не любят «менять лошадей на переправе», поэтому руководство фабрики с вероятностью 80% знает, какие именно комплектующие будет производить через 2-3 года. Своевольно менять и выбирать новых поставщиков ткани и других компонентов фабрика не имеет права, может только выбирать из уже существующего перечня компаний, одобренных основным заказчиком.
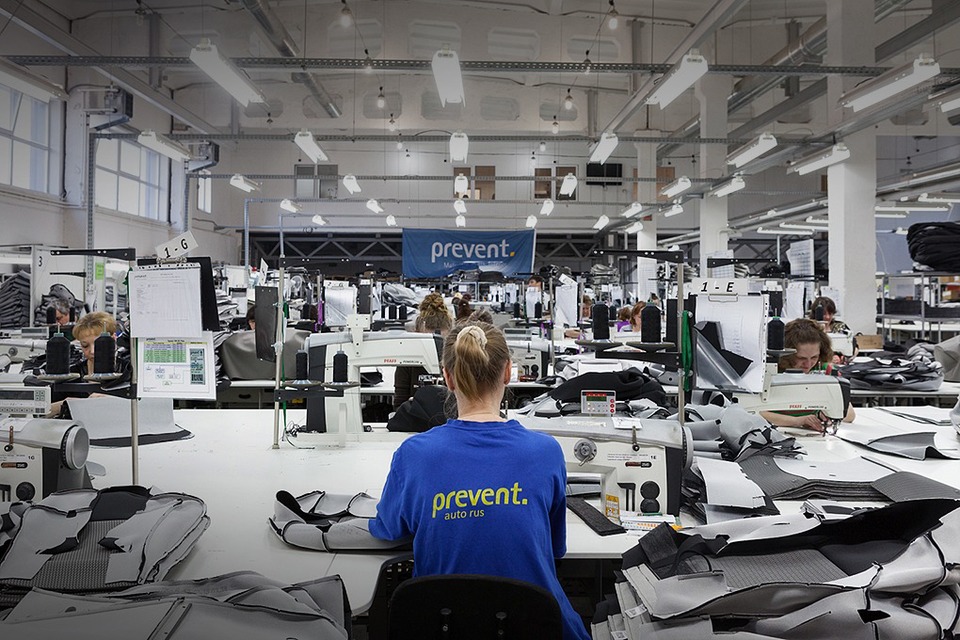
Фабрика расположена в подмосковном городе Озёры, где на месте обанкротившейся текстильной фабрики открылся индустриальный парк. Весь технологический процесс построен как в Европе. Материалы также закупаются у европейских поставщиков. Когда комплектующие доставляют на фабрику, они попадают во временную зону хранения. Если они не соответствуют качеству, их отправляют в изолятор брака. Информация о годных материалах заносится в автоматизированную систему.
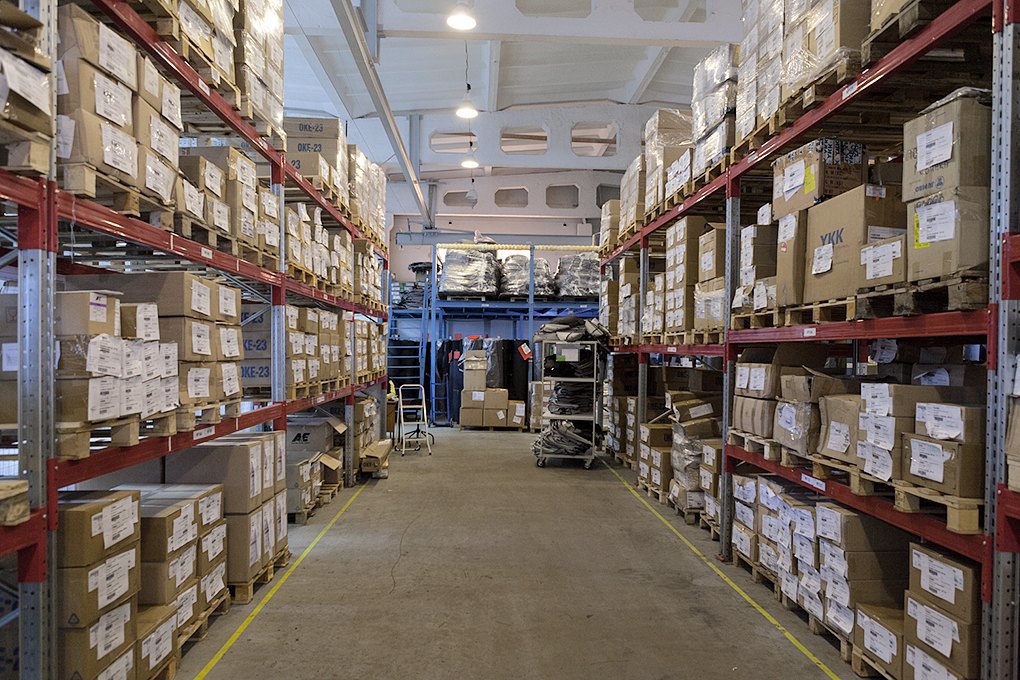
Затем материалы перевозят в зону раскроя. Здесь находится раскройный комплекс Bullmer, который стоит порядка 200 000 евро. В Bullmer загружают программу с картой раскроя ткани. На установку кладётся ткань будущего изделия в 30-40 слоёв в зависимости от её толщины. На ткань — полиэтилен. Под этой плёнкой создаётся вакуум, чтобы зафиксировать ткань на одном месте.
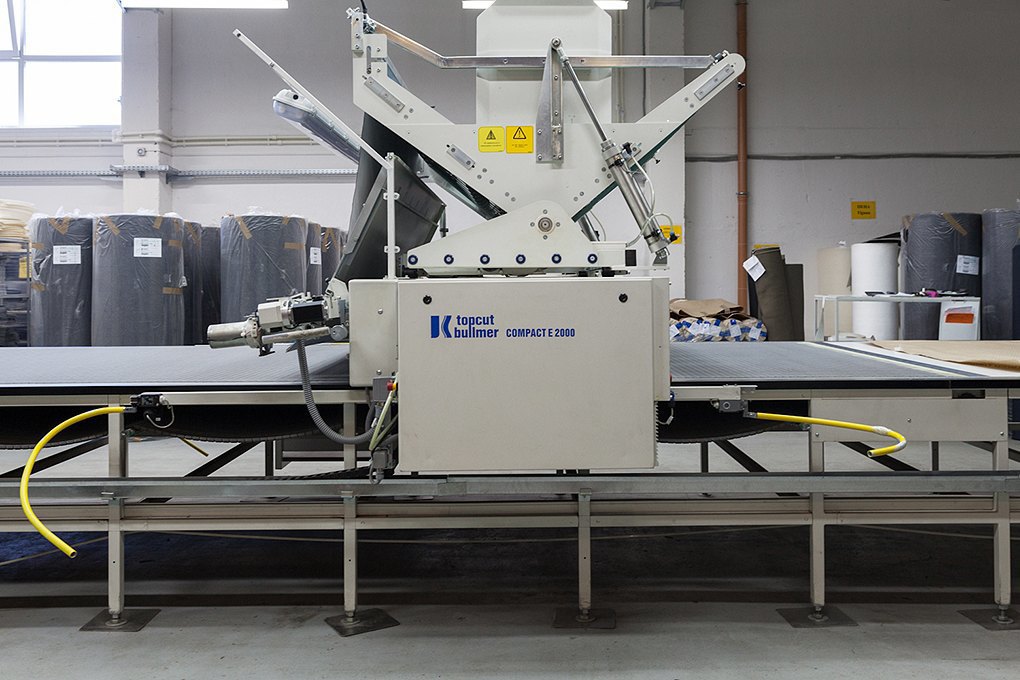
За работой установки следит специальный человек. Задача оператора — правильно разложить ткань, выбрать и запустить программу раскроя и следить за тем, чтобы она выполнялась точно. Обучение операторов установки на заводе проводила команда из Европы. Всего в компании работает около 200 человек.
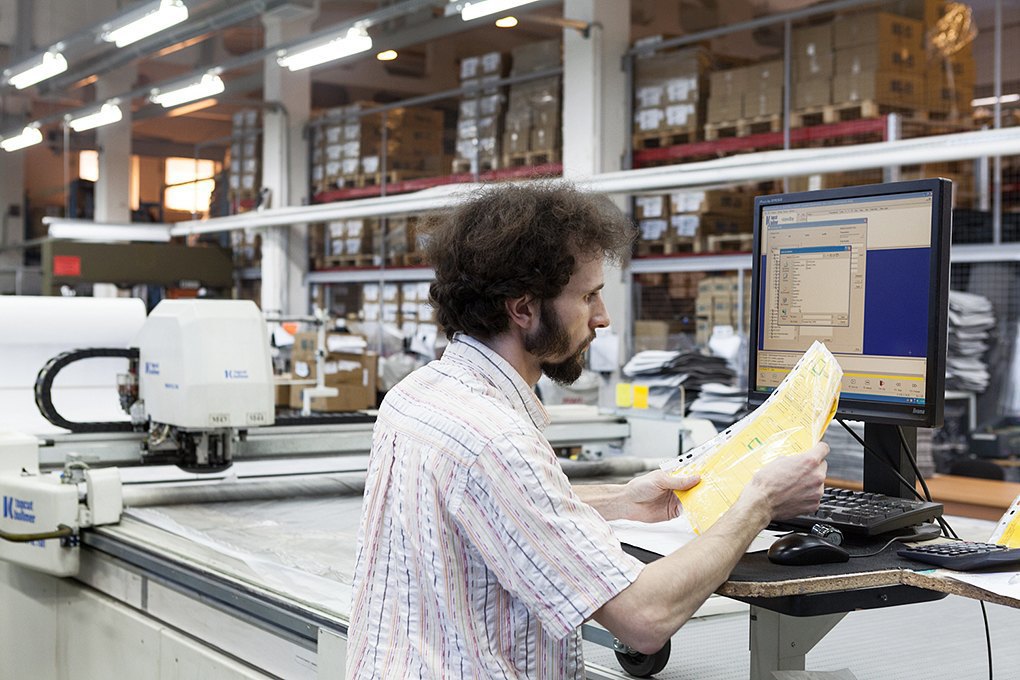
Специальная платформа с острым ножом ездит вдоль разложенной ткани и разрезает её на отдельные части. Как только первая деталь вырезана, оператор останавливает работу установки, чтобы сделать контрольную проверку. Таких остановок на пути будет несколько.
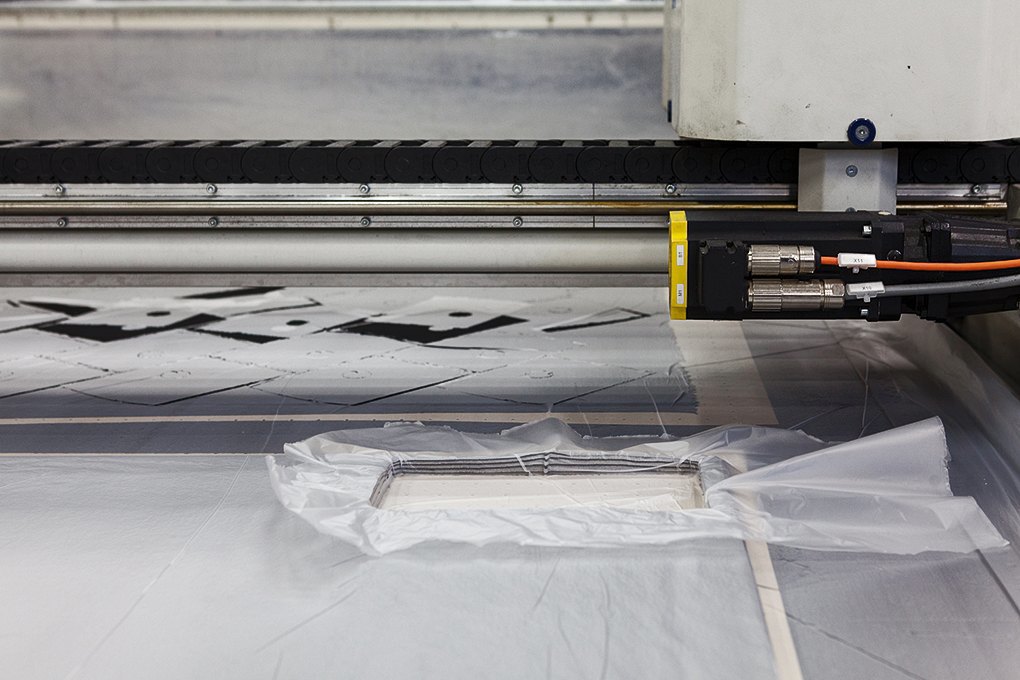
Для проверки оператор идёт к стенду, на котором висят шаблоны. Он выбирает необходимый шаблон и прикладывает его к вырезанной детали. Точность очень важна, так как расстояние между деталями на ткани — всего несколько миллиметров, и любая погрешность может испортить всё изделие. Если всё верно, он снова запускает установку.
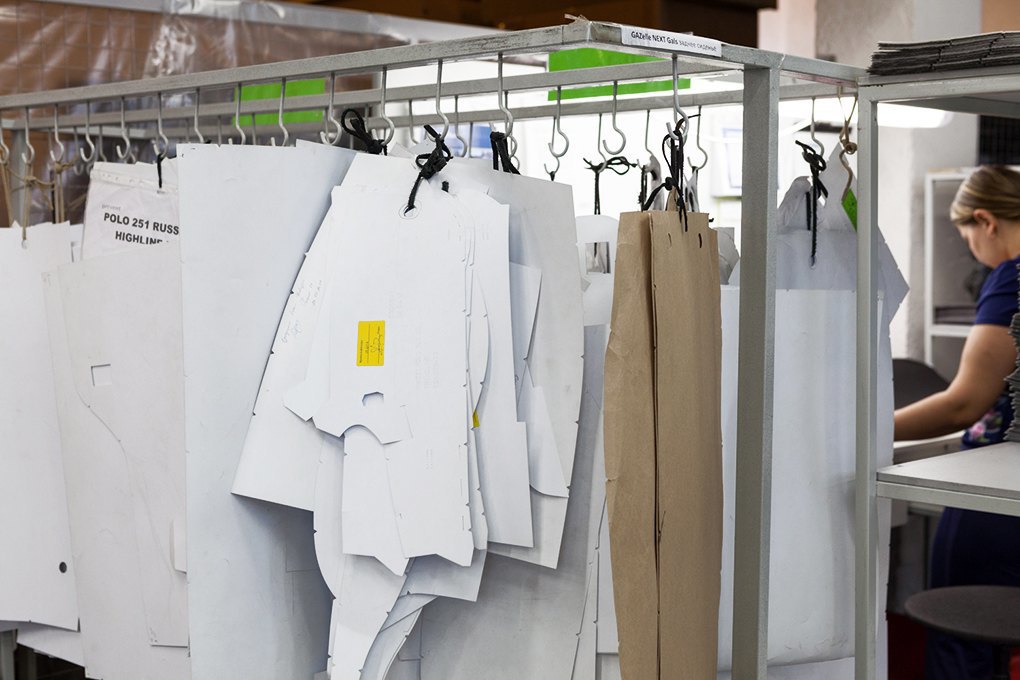
За процессом можно следить на экране компьютера, где фиксируются все произведённые и запланированные действия комплекса. На фото — карта раскроя из 40 деталей. Зелёным выделены те, что уже вырезаны, жёлтым — деталь, на которой установку остановили, красным — будущие.
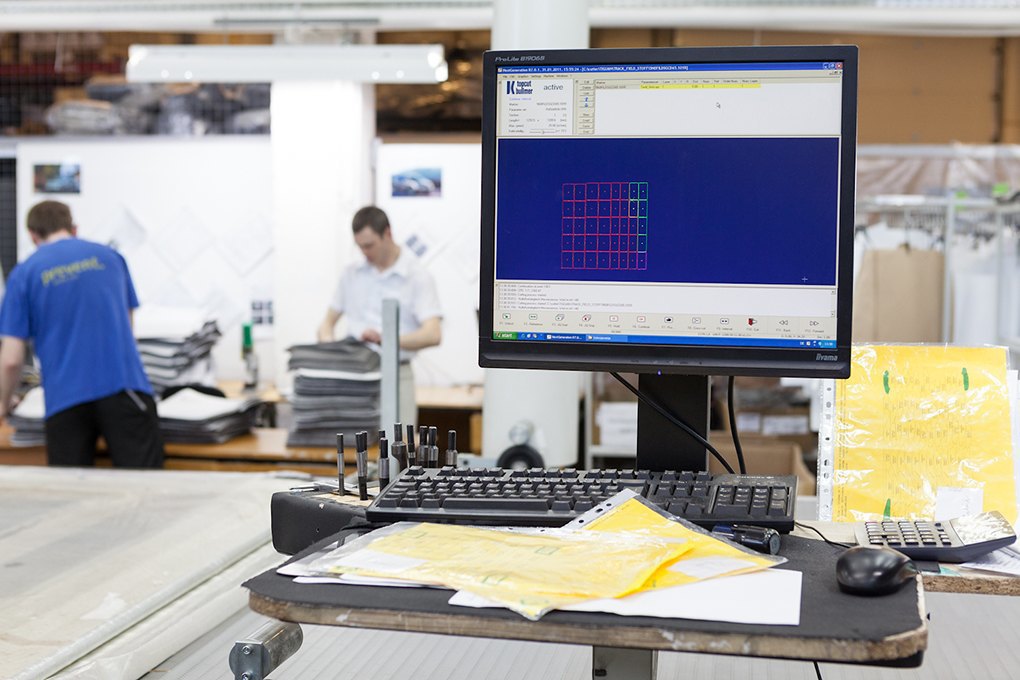
После раскроя части изделия перевозят на тележке в зону производства. Рабочие этого цеха разделены на швейные ячейки по 10-11 человек, ответственные за производство определённого изделия. Каждая швея ячейки выполняет одну операцию и передаёт чехол дальше по цепочке. Все сотрудники фабрики работают в две смены — с 6.30 до 15.00 и с 15.00 до 23.00. В течение смены есть перерыв на обед, и через каждые 2 часа — 10-минутный перерыв. Оплата на заводе сдельная: каждый получает столько, сколько совершил операций.
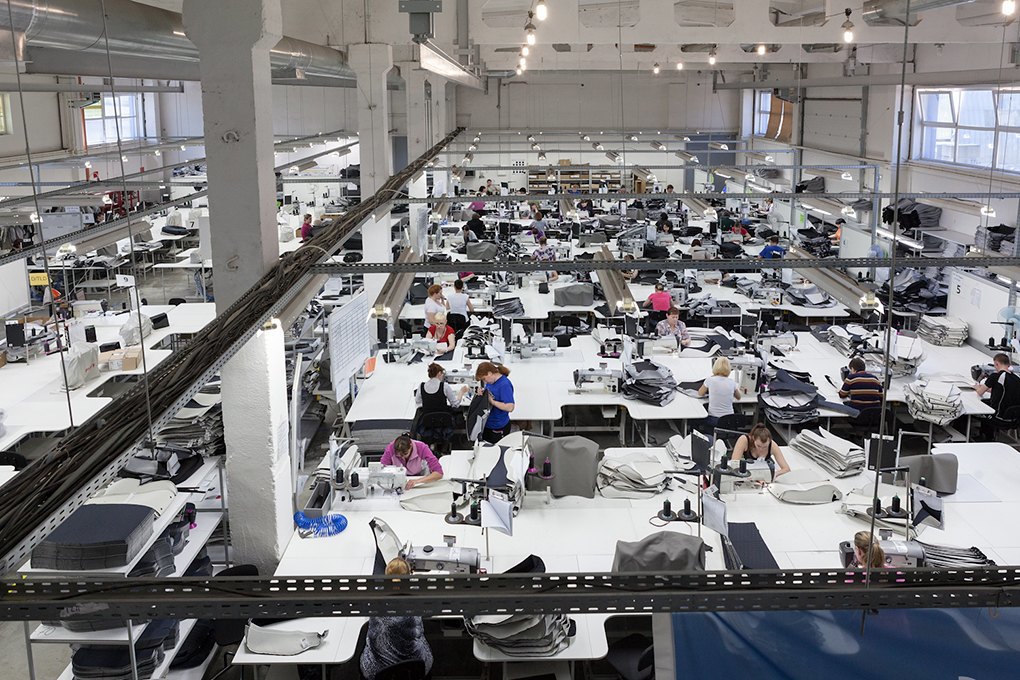
Каждая швея в ячейке контролирует правильность выполнения предыдущей операции. Когда изделие готово, его ещё раз проверяет контролёр. На стене перед ней висит специальный перечень дефектов, на которые нужно обратить внимание.
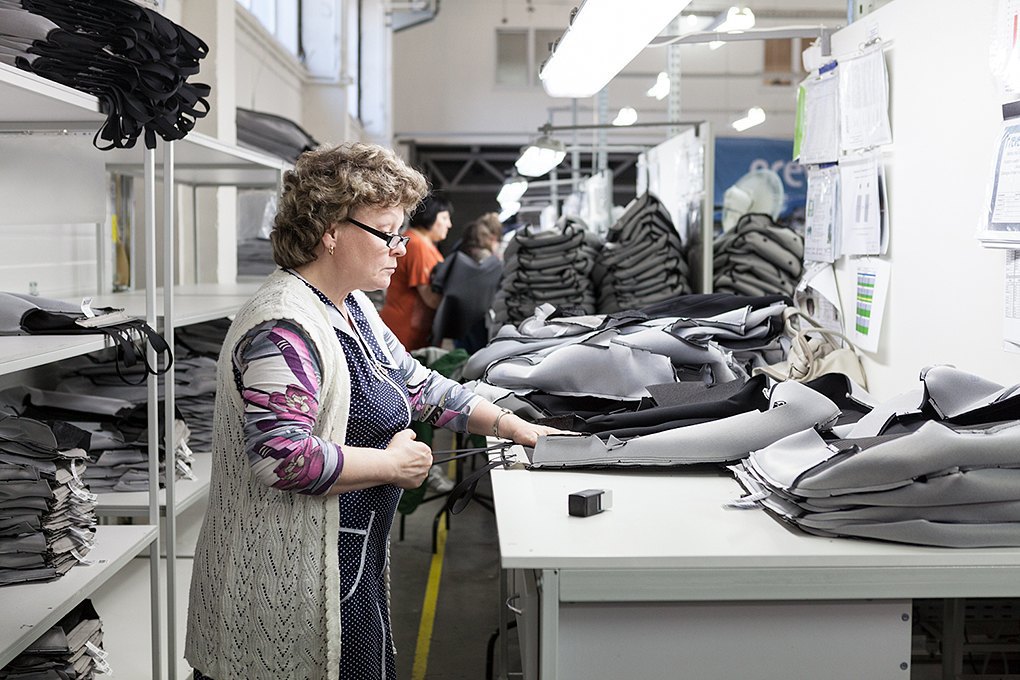
На доске фиксируются результаты работы каждой ячейки. Готовое изделие собирается на тележки и перемещается в зону упаковки, а затем попадает в зону отгрузки. Перед отгрузкой производится финальная проверка качества.
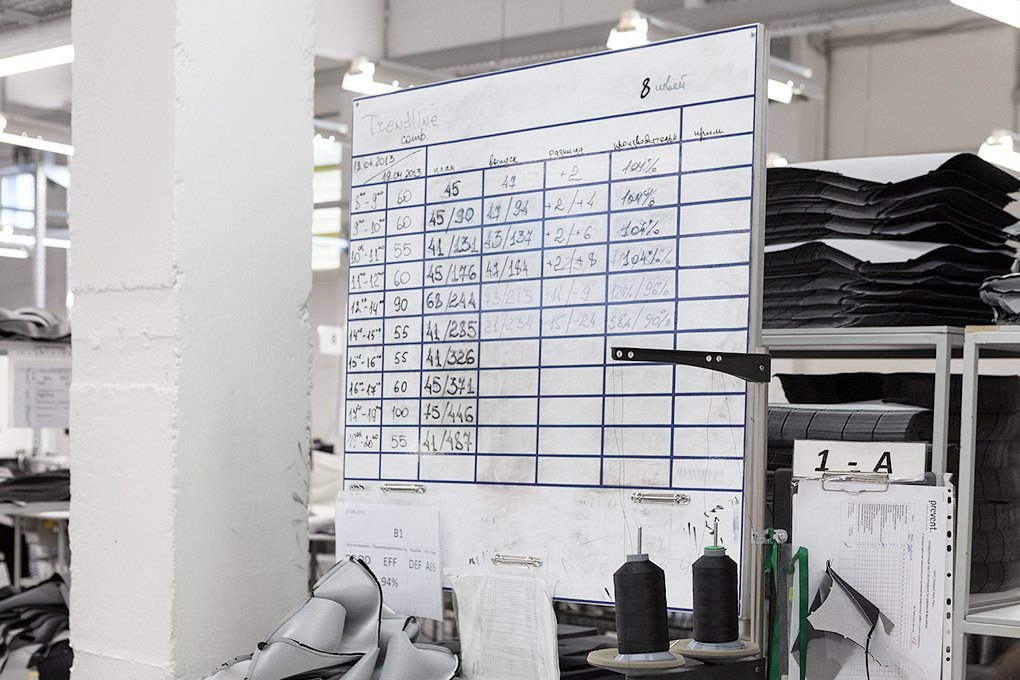
Если дефектов не найдено, контролёр ставит на бирке специальный штамп. У каждого контролёра есть свой уникальный номер, чтобы в случае брака можно было определить, кто допустил ошибку и почему.
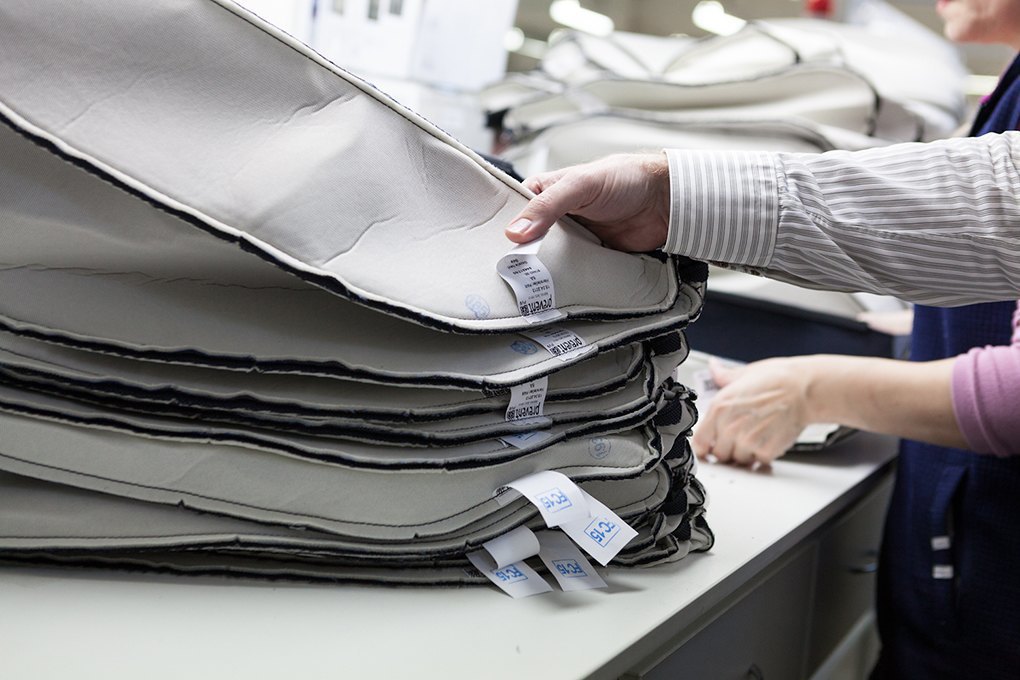
Источник
Если у вас есть производство или сервис, о котором вы хотите рассказать нашим читателям, пишите Александру Куксе (alxmcr@gmail.com) и мы сделаем самый лучший репортаж, который увидят не только читатели сообщества, но и сайта Бигпикча и Как это сделано
Подписывайтесь также на наши группы в фейсбуке, вконтакте, одноклассниках и в гугл+плюс, где будут выкладываться самое интересное из сообщества, плюс материалы, которых нет здесь и видео о том, как устроены вещи в нашем мире.
Жми на иконку и подписывайся!
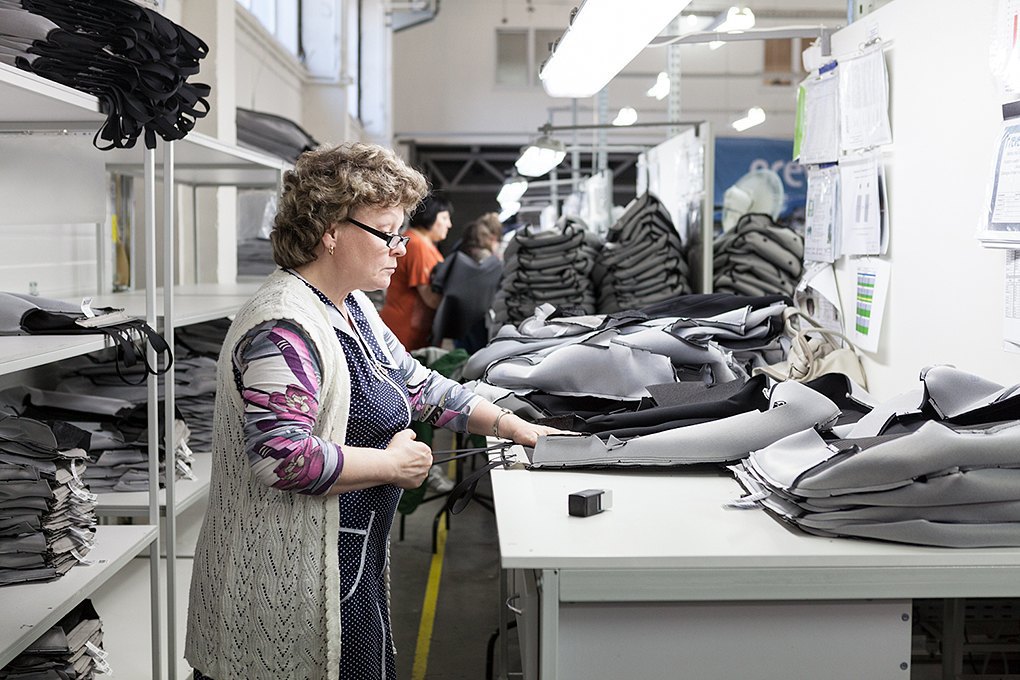
Компания работает с автогигантом не напрямую, а через производителя сидений. Стать поставщиком Volkswagen было непросто, но это стоило того. Крупные автоконцерны не любят «менять лошадей на переправе», поэтому руководство фабрики с вероятностью 80% знает, какие именно комплектующие будет производить через 2-3 года. Своевольно менять и выбирать новых поставщиков ткани и других компонентов фабрика не имеет права, может только выбирать из уже существующего перечня компаний, одобренных основным заказчиком.
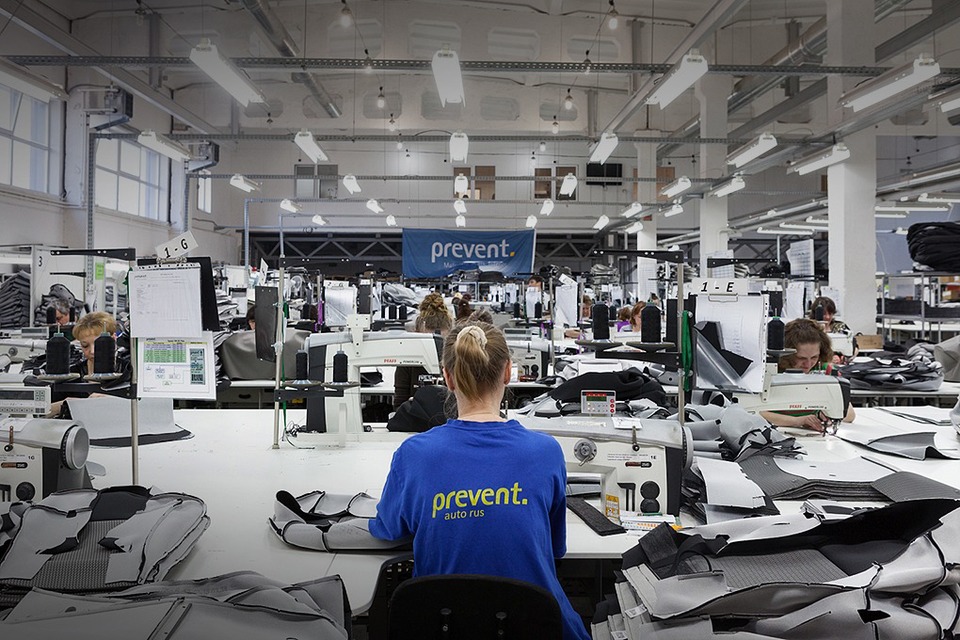
Фабрика расположена в подмосковном городе Озёры, где на месте обанкротившейся текстильной фабрики открылся индустриальный парк. Весь технологический процесс построен как в Европе. Материалы также закупаются у европейских поставщиков. Когда комплектующие доставляют на фабрику, они попадают во временную зону хранения. Если они не соответствуют качеству, их отправляют в изолятор брака. Информация о годных материалах заносится в автоматизированную систему.
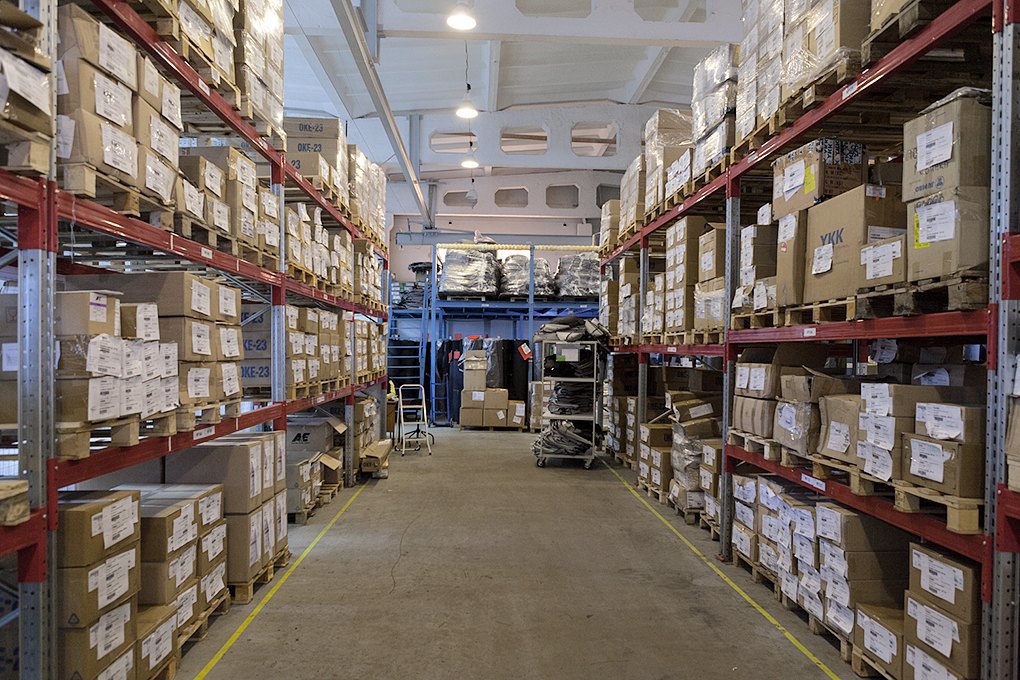
Затем материалы перевозят в зону раскроя. Здесь находится раскройный комплекс Bullmer, который стоит порядка 200 000 евро. В Bullmer загружают программу с картой раскроя ткани. На установку кладётся ткань будущего изделия в 30-40 слоёв в зависимости от её толщины. На ткань — полиэтилен. Под этой плёнкой создаётся вакуум, чтобы зафиксировать ткань на одном месте.
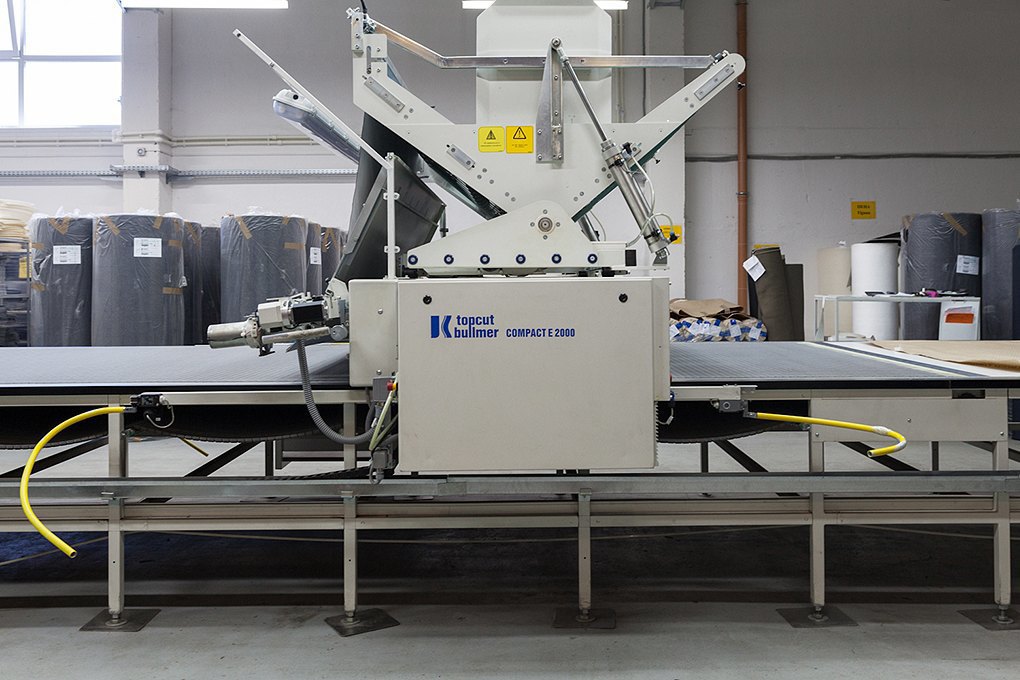
За работой установки следит специальный человек. Задача оператора — правильно разложить ткань, выбрать и запустить программу раскроя и следить за тем, чтобы она выполнялась точно. Обучение операторов установки на заводе проводила команда из Европы. Всего в компании работает около 200 человек.
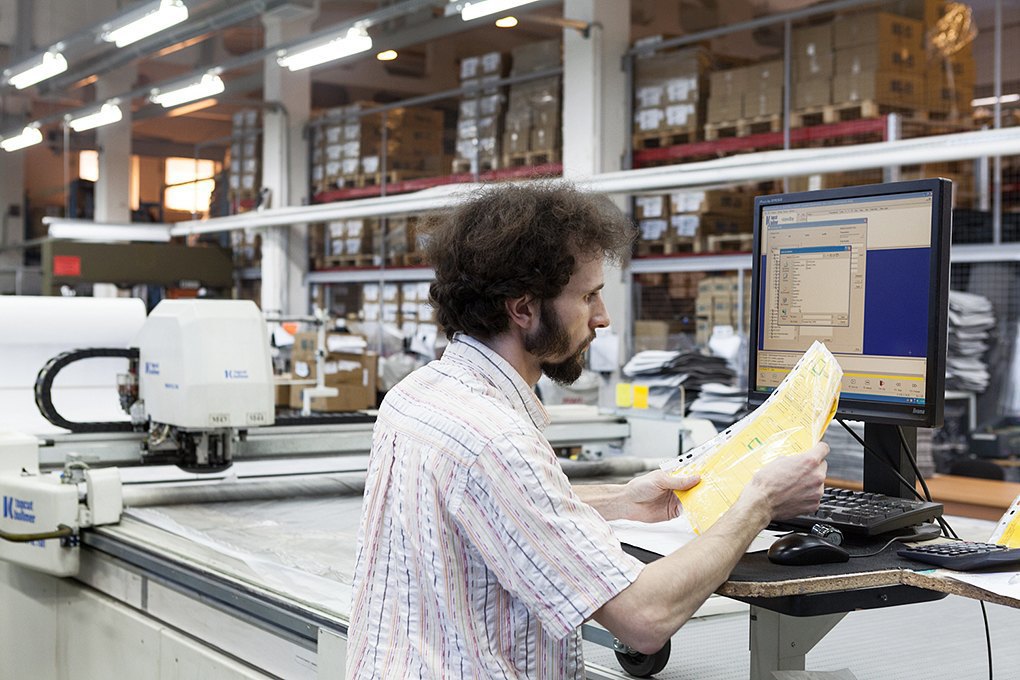
Специальная платформа с острым ножом ездит вдоль разложенной ткани и разрезает её на отдельные части. Как только первая деталь вырезана, оператор останавливает работу установки, чтобы сделать контрольную проверку. Таких остановок на пути будет несколько.
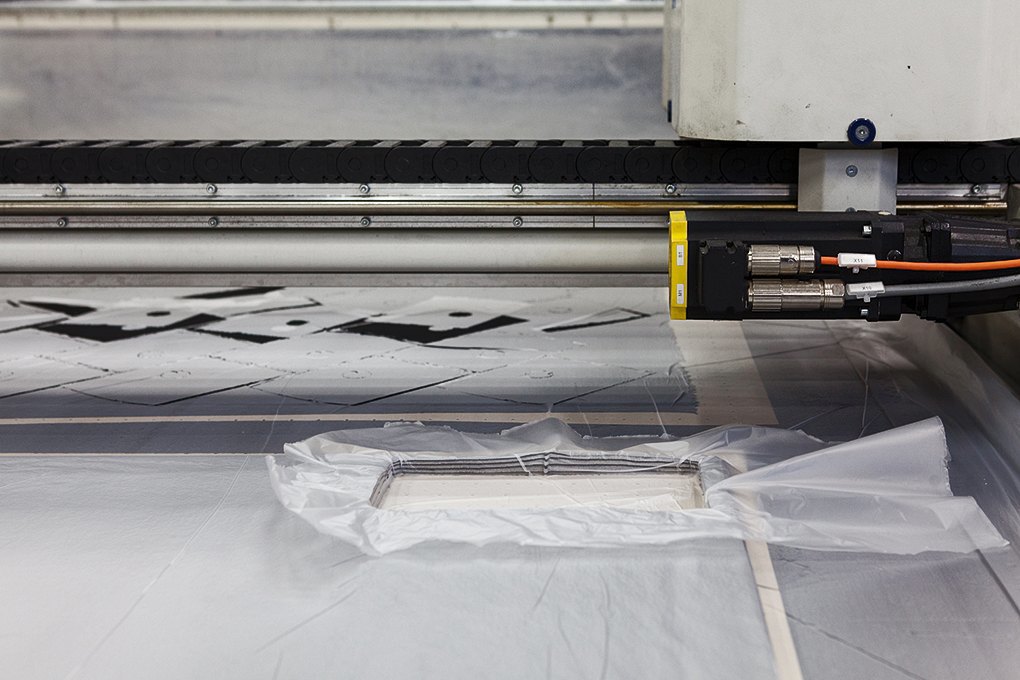
Для проверки оператор идёт к стенду, на котором висят шаблоны. Он выбирает необходимый шаблон и прикладывает его к вырезанной детали. Точность очень важна, так как расстояние между деталями на ткани — всего несколько миллиметров, и любая погрешность может испортить всё изделие. Если всё верно, он снова запускает установку.
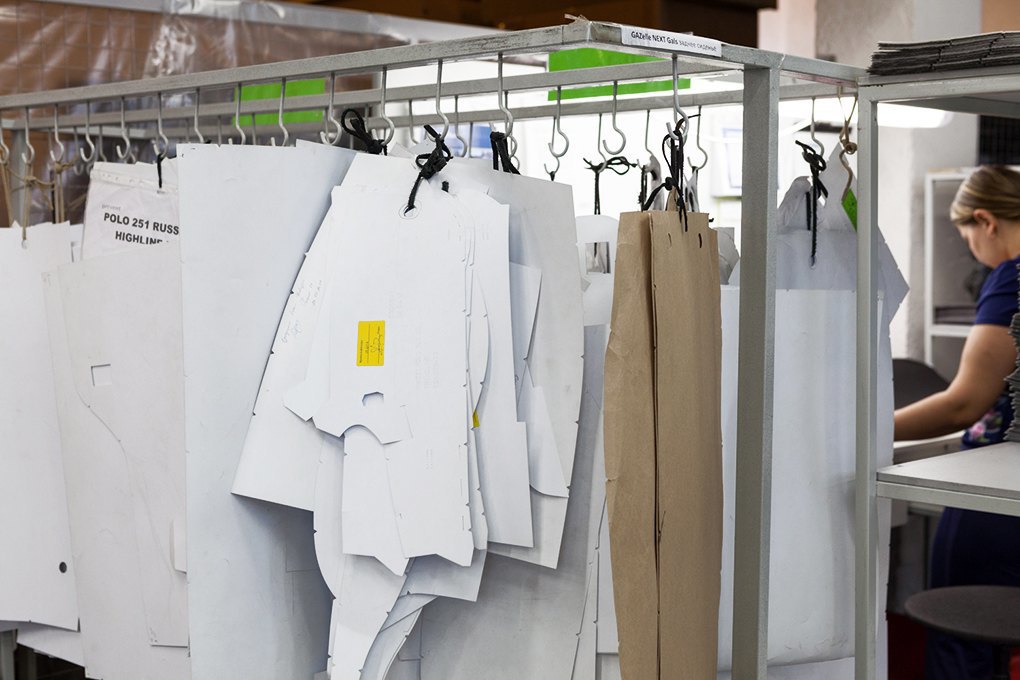
За процессом можно следить на экране компьютера, где фиксируются все произведённые и запланированные действия комплекса. На фото — карта раскроя из 40 деталей. Зелёным выделены те, что уже вырезаны, жёлтым — деталь, на которой установку остановили, красным — будущие.
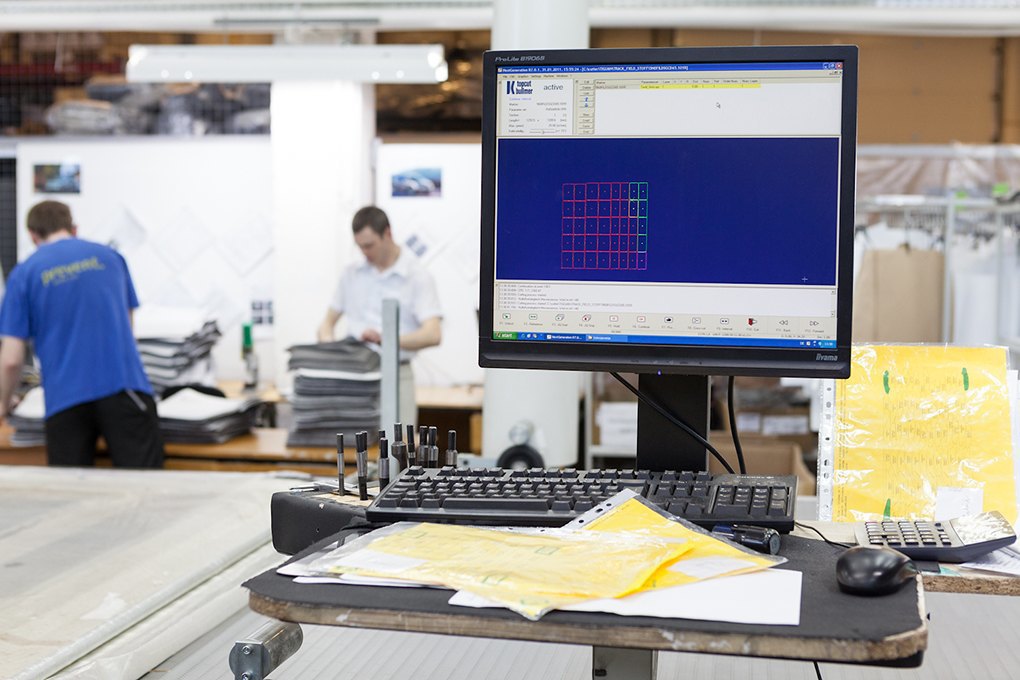
После раскроя части изделия перевозят на тележке в зону производства. Рабочие этого цеха разделены на швейные ячейки по 10-11 человек, ответственные за производство определённого изделия. Каждая швея ячейки выполняет одну операцию и передаёт чехол дальше по цепочке. Все сотрудники фабрики работают в две смены — с 6.30 до 15.00 и с 15.00 до 23.00. В течение смены есть перерыв на обед, и через каждые 2 часа — 10-минутный перерыв. Оплата на заводе сдельная: каждый получает столько, сколько совершил операций.
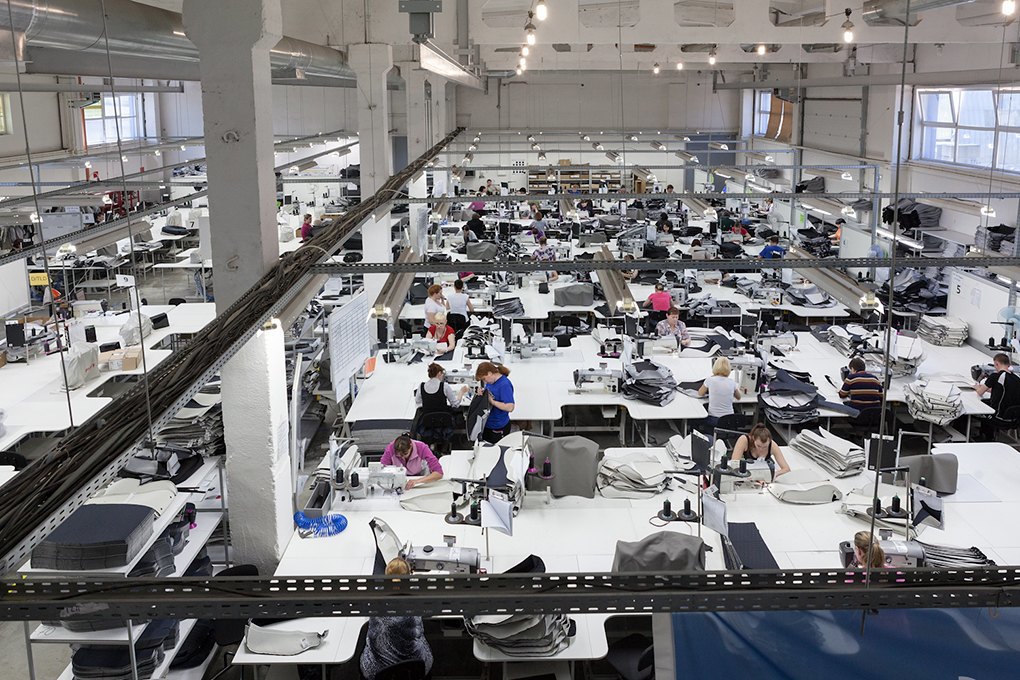
Каждая швея в ячейке контролирует правильность выполнения предыдущей операции. Когда изделие готово, его ещё раз проверяет контролёр. На стене перед ней висит специальный перечень дефектов, на которые нужно обратить внимание.
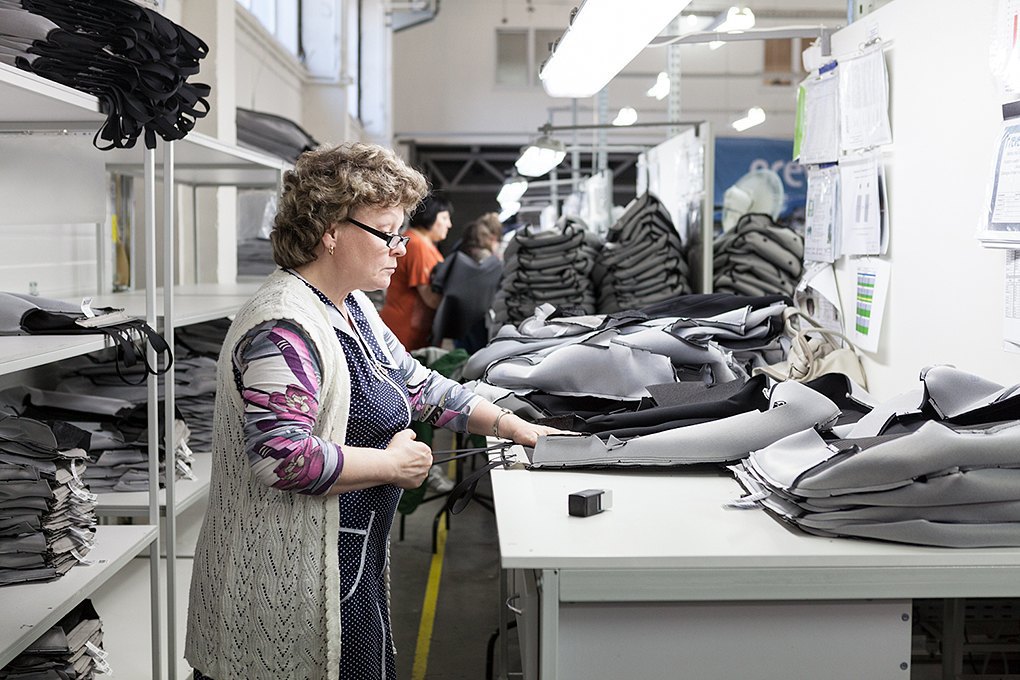
На доске фиксируются результаты работы каждой ячейки. Готовое изделие собирается на тележки и перемещается в зону упаковки, а затем попадает в зону отгрузки. Перед отгрузкой производится финальная проверка качества.
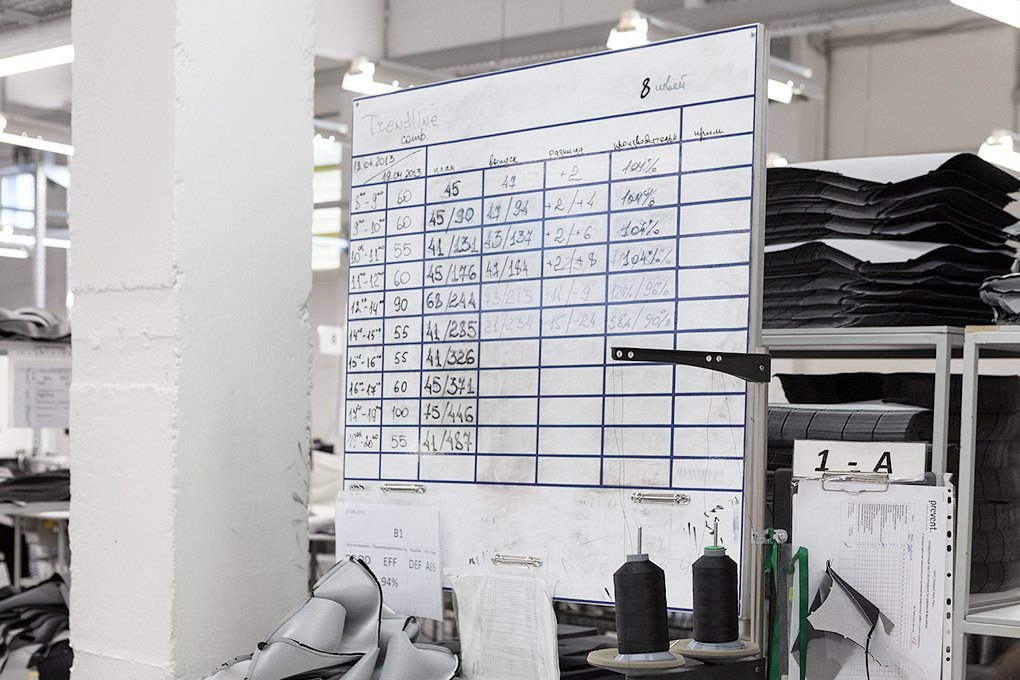
Если дефектов не найдено, контролёр ставит на бирке специальный штамп. У каждого контролёра есть свой уникальный номер, чтобы в случае брака можно было определить, кто допустил ошибку и почему.
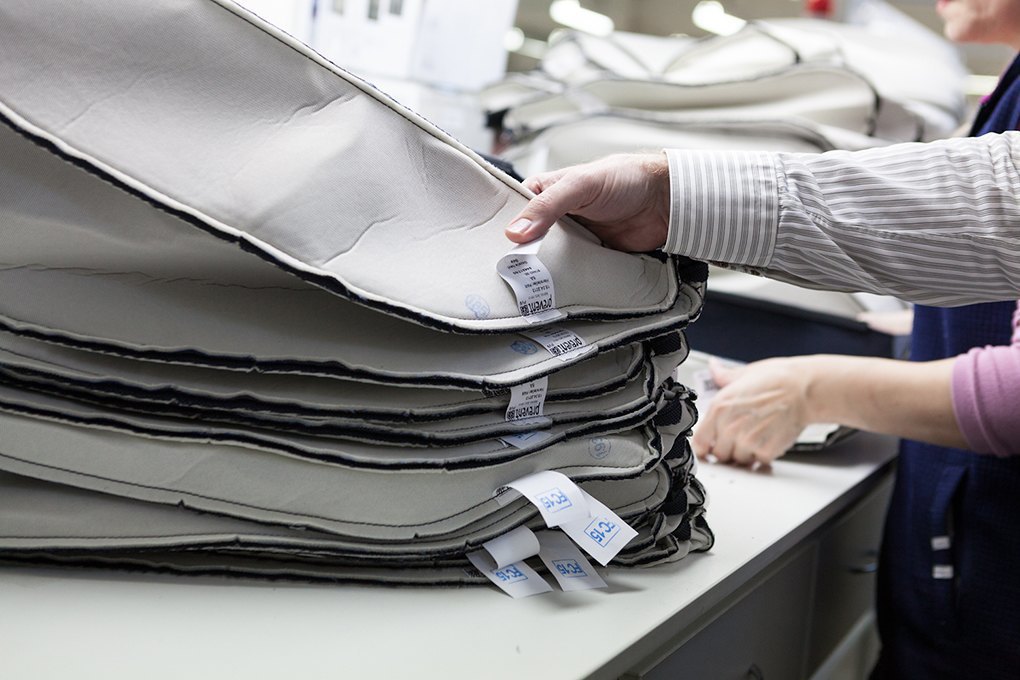
Источник
Если у вас есть производство или сервис, о котором вы хотите рассказать нашим читателям, пишите Александру Куксе (alxmcr@gmail.com) и мы сделаем самый лучший репортаж, который увидят не только читатели сообщества, но и сайта Бигпикча и Как это сделано
Подписывайтесь также на наши группы в фейсбуке, вконтакте, одноклассниках и в гугл+плюс, где будут выкладываться самое интересное из сообщества, плюс материалы, которых нет здесь и видео о том, как устроены вещи в нашем мире.
Жми на иконку и подписывайся!




Комментарии (0)
{related-news}
[/related-news]