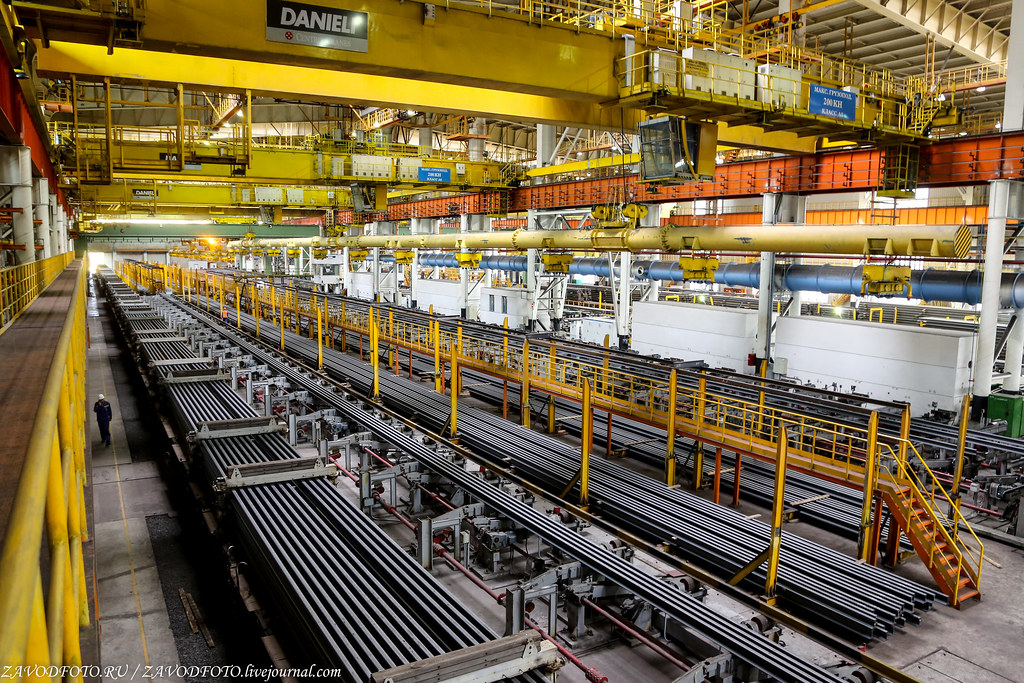
Где делают лучшие в России рельсы
---
Наверняка многие из нас хотели бы хоть завтра рвануть в длительное путешествие. Конечно, есть любители летать, но есть и те, кто предпочтут именно железнодорожную романтику. Стук колёс, вагон-ресторан, подстаканники, курочка и хорошая компания, что для счастья ещё надо... Между прочим, если верить статистике, каждый житель России 9 раз в году пользуется поездом. И это далеко не предел, так в СССР эта цифра составляла в среднем 15 поездок на каждого человека в год. А еще, оказывается, по длине сети железных дорог, наша страна уступает только США. Так это я к чему? А умеем ли мы делать хорошие рельсы? Готовы ли мы переходить на высокоскоростные магистрали? В последнее время об этом много стали говорить, и, знаете, я напросился в гости к одному такому отечественному производителю и был приятно удивлён. Итак, мы с вами на Челябинском металлургическом комбинате.
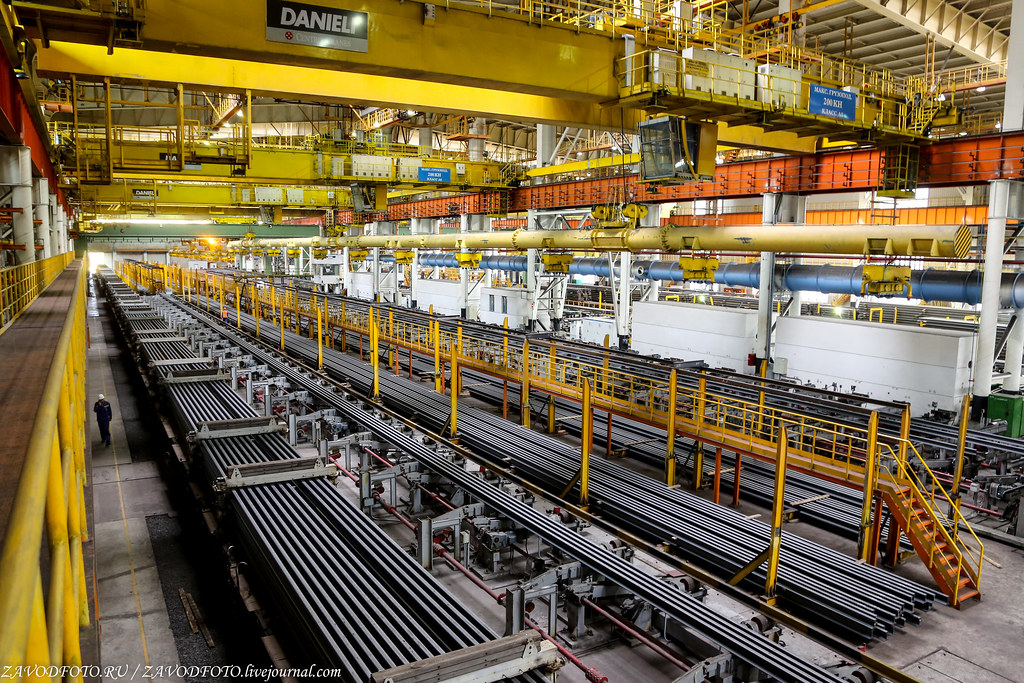
Еще до революции рассматривалось несколько проектов строительства крупного металлургического производства на Урале, качественно отличающегося от устаревших Демидовских заводов. Строительство Бакальского металлургического завода (именно так сначала назывался Челябинский металлургический комбинат) началось в 1934 году. Сырьевой базой для промышленного гиганта должно было стать Бакальское месторождение железных руд. Но вскоре стройку заморозили. Дело в том, что советское металлургическое машиностроение потянуть такой проект было не в состоянии, а средств на закупку оборудования за границей то ли не было, то ли сами иностранцы не соглашались его продать. Так в замороженном виде Бакальский завод и просуществовал до 1941 года.
2.
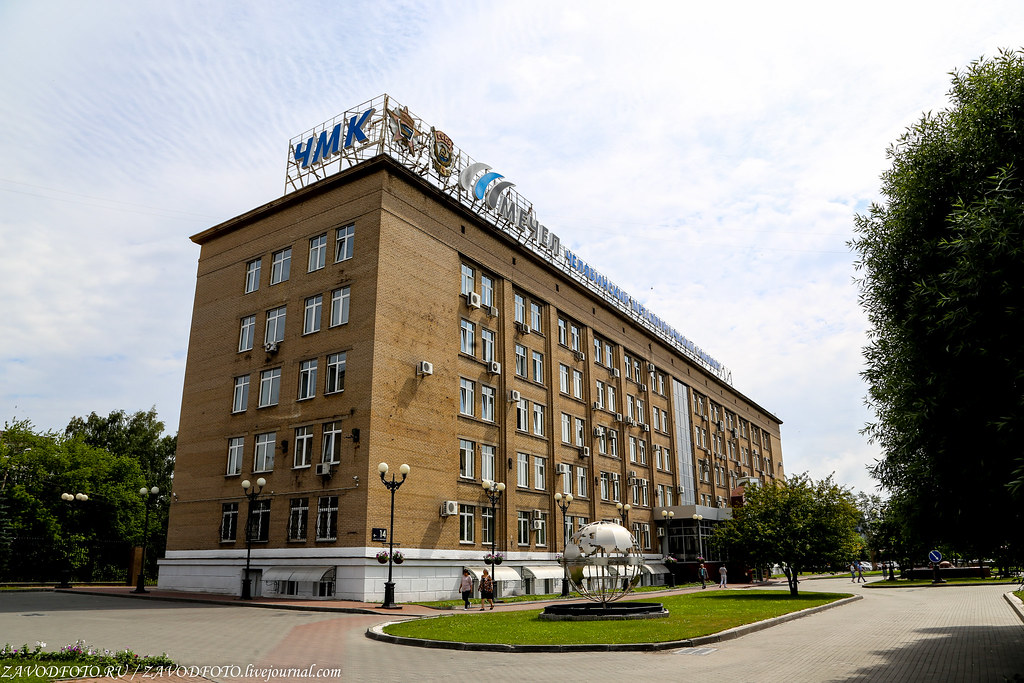
Когда я ехал сюда, у меня не было никаких сомнений, что это очень мощный и большой завод. Вот посмотрите, какой огромный цех, где расположены лишь некоторые, так сказать, запчасти к одному из станов.
3.
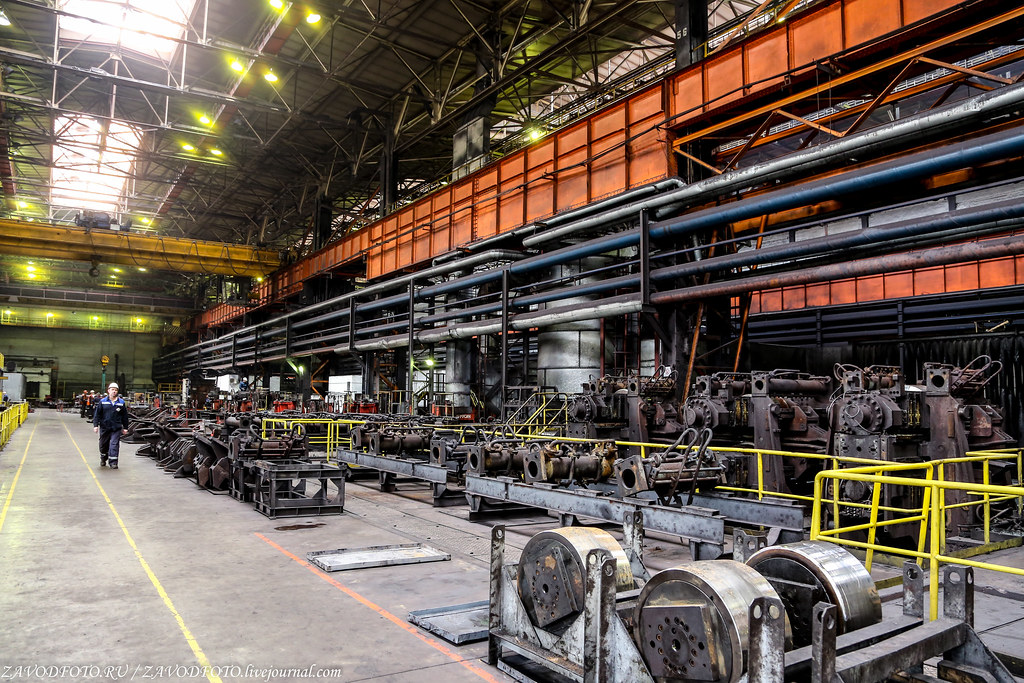
За десять дней до начала Великой Отечественной войны Советом Народных Комиссаров СССР принято Постановление о строительстве завода. Незакрытый вопрос с оборудованием для будущего предприятия решился сам собой: с осени 1941 года на строительную площадку стали прибывать эшелоны с эвакуированными мощностями Алчевского металлургического завода, подмосковной Электростали, завода "Красный октябрь" (Сталинград), Новолипецкого металлургического завода и Запорожстали. 1 мая 1942 года был уложен первый кубометр бетона в фундамент будущего электросталеплавильного цеха. 19 апреля 1943 года первый металл хлынул в разливочный ковш. Эта дата и является официальным Днём рождения Челябинского металлургического комбината. 30 апреля первая доменная печь выдала первый чугун, а 2 августа на коксовой батарее № 1 получен первый кокс. В каждом третьем танке и боевом самолёте Великой Отечественной войны, выпускаемых с 1943 года, была челябинская сталь. Тогда же здесь научились выплавлять металл для шарикоподшипников (прежде его массово закупали в Великобритании). В советское время завод успешно участвовал в выполнении космических программ, производил металл для военно-промышленного комплекса и наукоёмкого сектора экономики. В 2003 году ЧМК вошёл в состав Группы «Мечел». И практически сразу же на предприятии начинается реализация масштабной программы технического перевооружения, по сути, и сейчас эта история продолжается.
4. стенд с прокатными валками
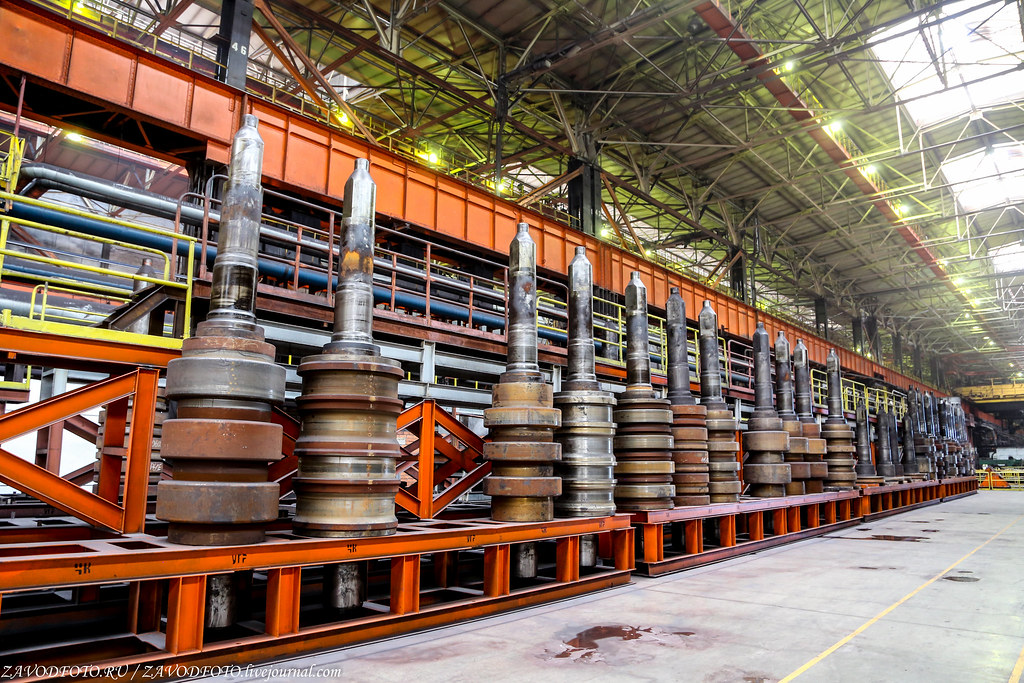
В качестве примера предлагаю остановиться на нашей сегодняшней повестке, производстве рельсов нового поколения. В марте 2012 года на ЧМК запустили комплекс по производству рельсовой стали, который включил в себя машину непрерывного литья заготовок № 5 (МНЛЗ-5) и агрегаты внепечной обработки стали, годовой производительностью 1,2 млн тонн. А в июле 2013 года открыли новый универсальный рельсобалочный стан (УРБС), который стал первым в России производством фасонного проката и рельсов длиной от 12,5 до 100 метров. Важно отметить, что на новом производстве создали более 1500 новых рабочих мест, а благодаря выводу из эксплуатации старого оборудования и строительству современных очистных сооружений, существенно снизилась и доля воздействия ЧМК на окружающую среду, что для Челябинска весьма актуально.
5. валки обжимной клети
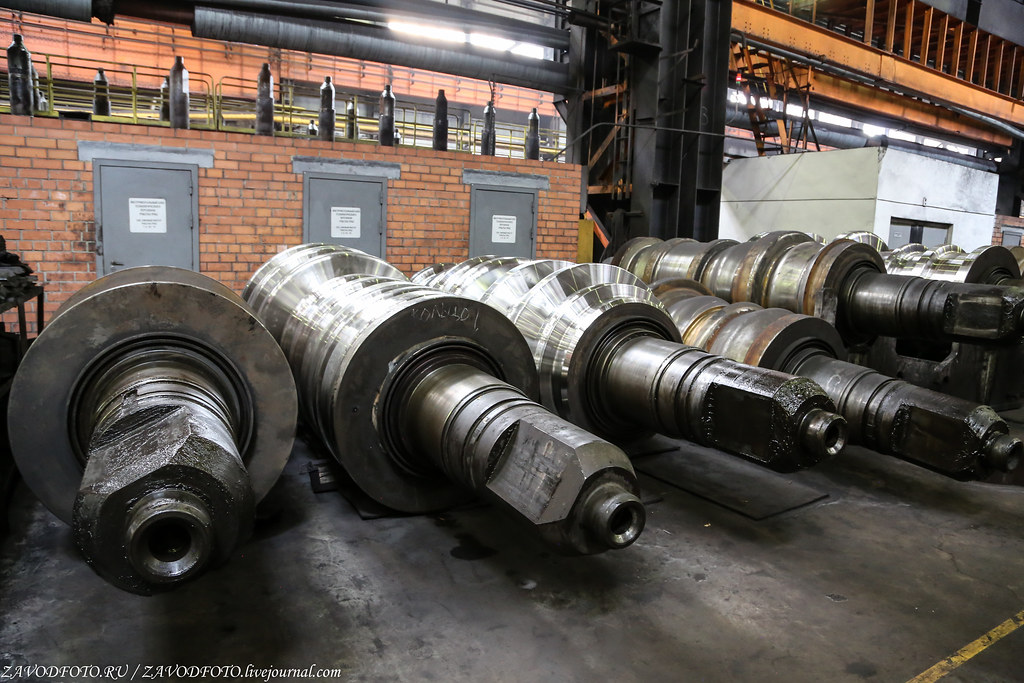
6. Нагревательная печь. Примерно каждые 2 минуты отсюда выходят заготовки, из которых и получаются наши 100-метровые рельсы.
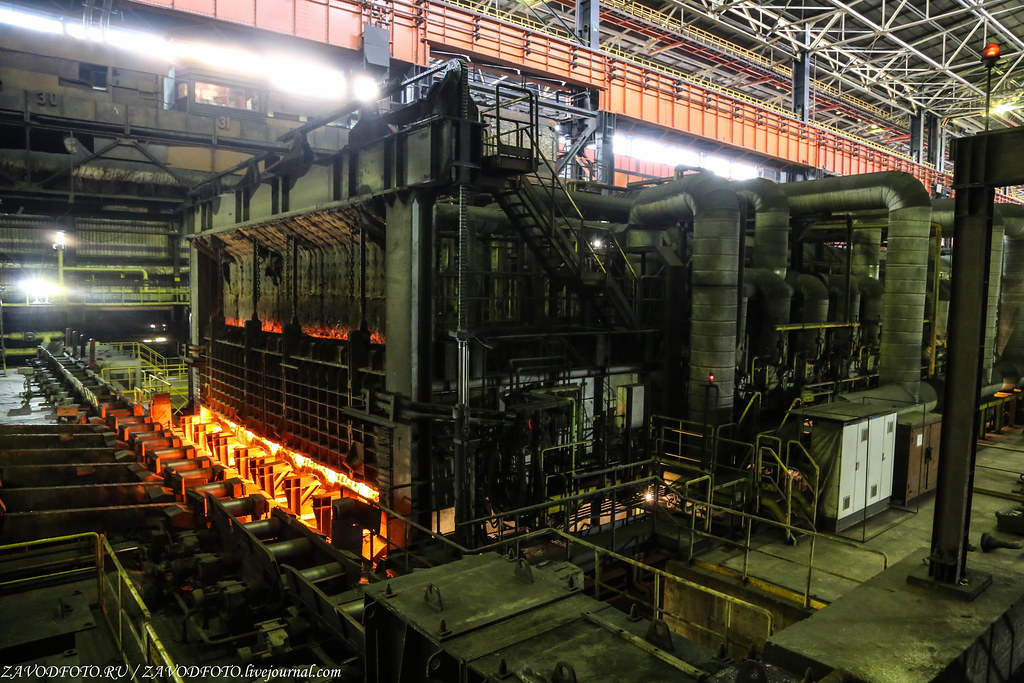
Вкратце весь процесс производства представлен на этой картинке. Если идти с самого начала, то сталь для рельсов выплавляется в кислородно-конвертерном цехе, где попадает в ковш-печь, доводится до определенной температуры и химического состава. Следующий этап – вакууматор. Здесь путем снижения давления из стали удаляются газообразные элементы. Потом идет процесс разливки и кристаллизации на машине непрерывной разливки заготовок (МНЛЗ), где получается блюм с необходимым качеством стали. Далее заготовки режутся, остывают и после тщательного контроля, вновь отправляются в нагревательную печь. Вот где по-настоящему жарко - 1300°С, это температура действующего вулкана.
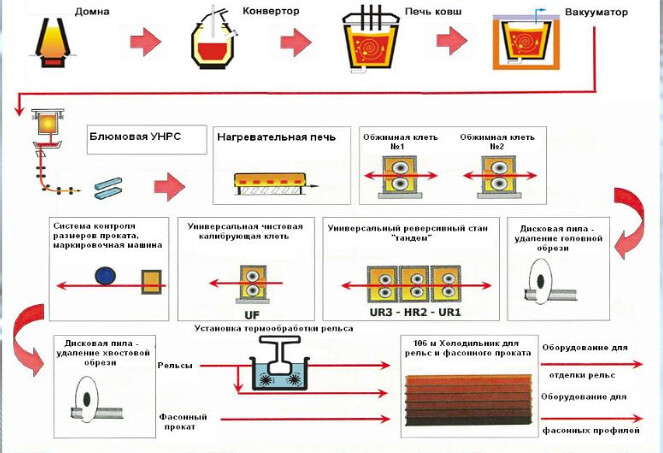
7. Длина рельсовой заготовки составляет порядка 8 метров, вес - около 7 тонны. После того, как она вышла из печи, заготовка попадает в установку, где сбивается окалина с помощью хорошего контрастного душа. Струи воды под давлением в 250 атмосфер, как будто ножом по маслу, отделяют корку от металла со всех сторон.
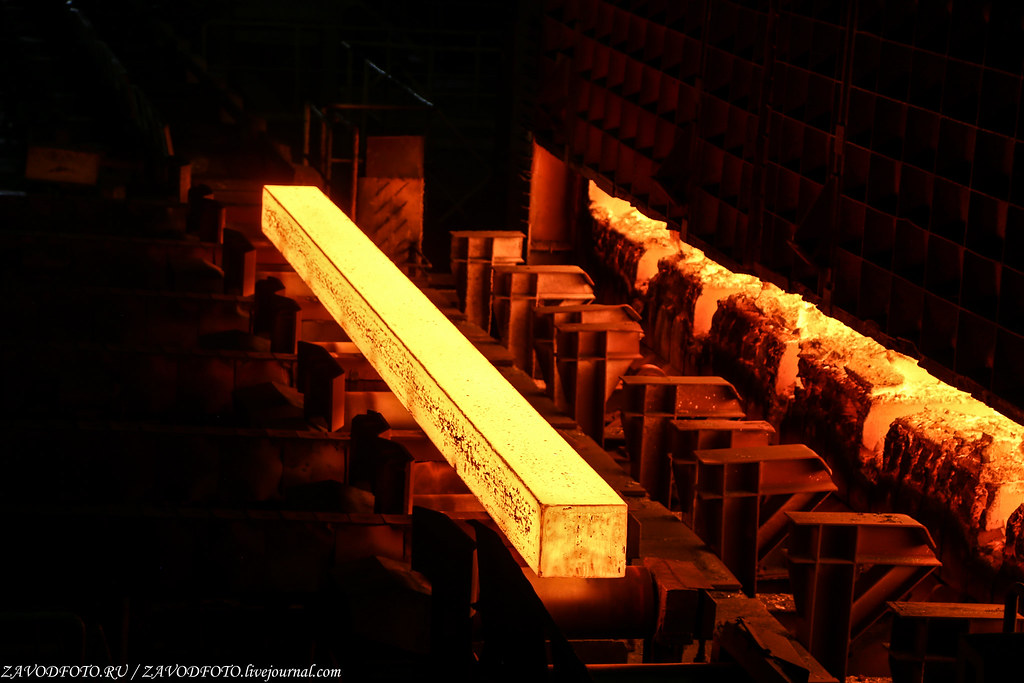
Сегодня Челябинский металлургический комбинат - это одно из крупнейших в России предприятий полного металлургического цикла по выпуску качественных и высококачественных сталей. Предприятие выпускает широкий ассортимент продукции: арматуру для стройки, нержавейку для машиностроения, рельсы, балку. За всё время работы на ЧМК было освоено производство около 2 000 различных марок стали и сплавов, а также более 4 000 профилеразмеров проката. Между прочим, ЧМК - это одно из немногих предприятий страны, которому дано право присваивать продукции собственный индекс - ЧС (Челябинская Сталь). Среди клиентов ЧМК замечены: атомная энергетика, тяжелая промышленность, химическое и энергетическое производство, автомобильное и сельскохозяйственное машиностроение, подшипниковые и трубопрокатные заводы, строительные компании и, конечно же, РЖД. Например, в 2017-м году ЧМК отгрузил РЖД 330 тысяч тонн рельсов, если перевести тонны в километры, длина пути покроет расстояние от Челябинска до Санкт-Петербурга.
8. На следующей стадии заготовку в свои крепкие объятия принимает обжимная клеть. Благодаря ей придаётся геометрическая форма предварительно, как его называют прокатчики, «лидерному» профилю уже похожему на готовый рельс или балку.
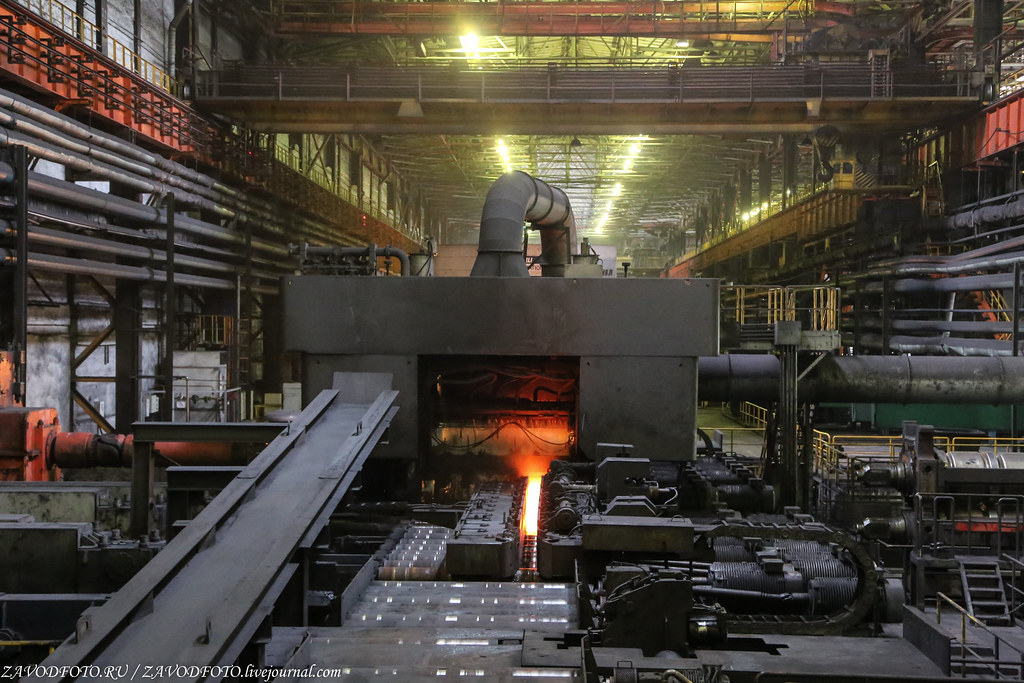
Универсальность стана как раз заключается в выпуске как рельсовой продукции, так и фасонного проката для строительной отрасли. Вот, например, мимо нас проехала «собачья кость», так, любя, местные металлурги называют заготовки для двутавровой балки, используемой в строительстве.
9.
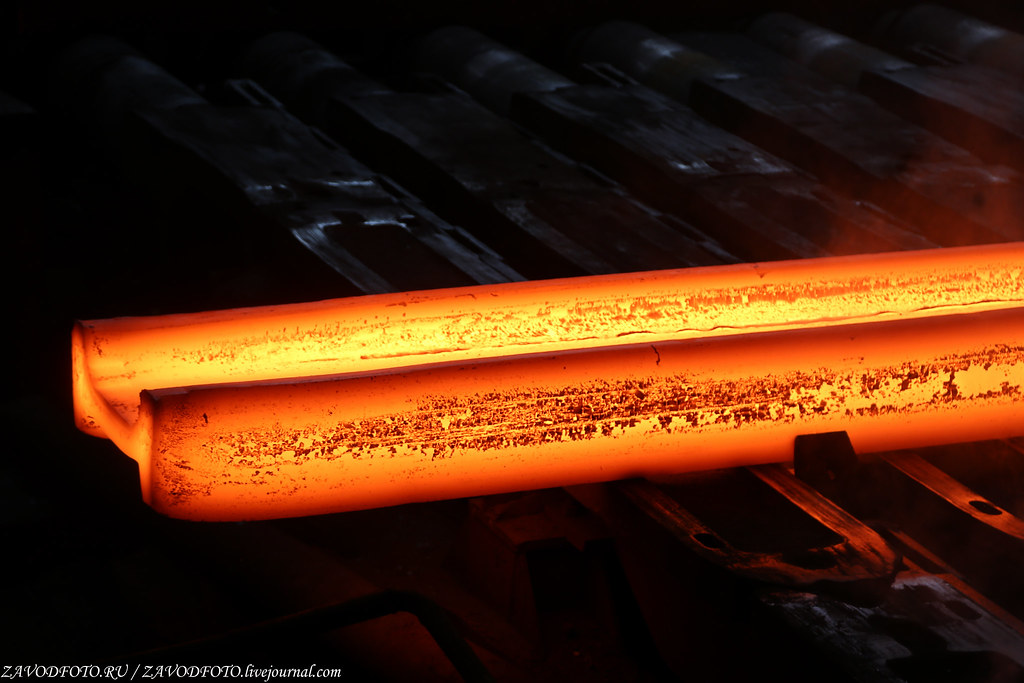
Аспирационная система очистки газов - вот еще объект, на который хотел бы обратить ваше внимание. Создавалась она специально под рельсобалочный стан. Проект индивидуальный. Такая система больше нигде не используется. Имеет 3 уровня очистки. По принципу работы аспирационная система схожа с бытовым пылесосом, только огромных размеров. Она улавливает мельчайшие частицы пыли и различные химические элементы, образующиеся при горячей прокатке.
10. Аспирационная система очистки газов.
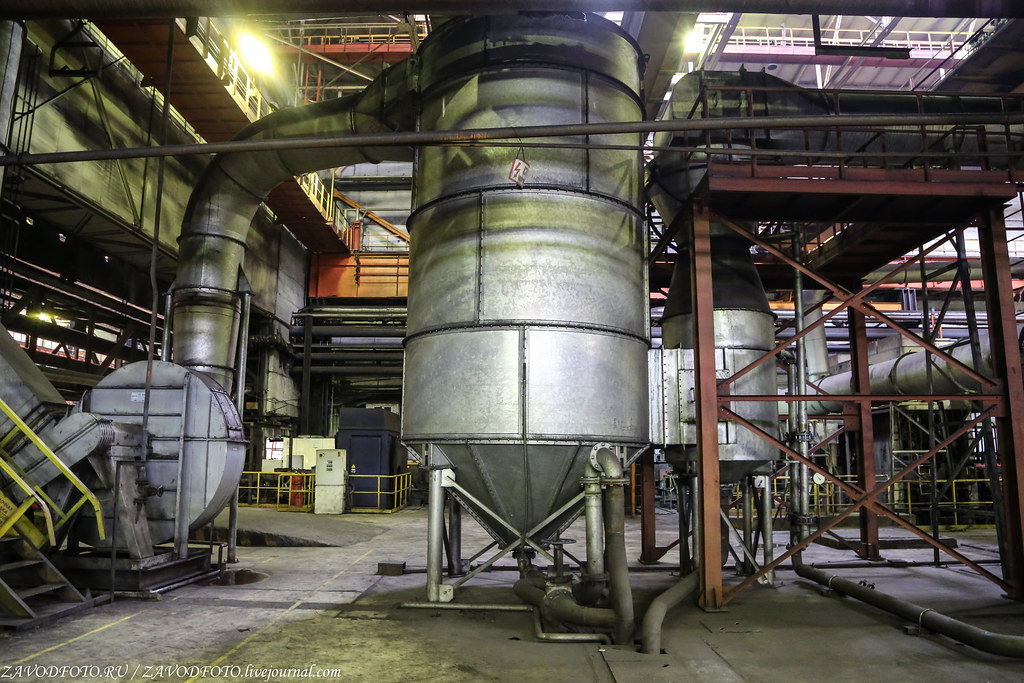
Наконец, наши заготовки попадают на клети рельсобалочного стана. Именно здесь и производятся рельсы длиной до 100 метров с применением самых новейших технологий. И первым делом на них ставят клеймо качества, свидетельствующего, что рельсы сделаны на Урале. На ЧМК гордятся своей продукцией. Буква «Ч» - фирменный знак предприятия – всегда стоит на каждом произведённом рельсе, как и дата его выпуска на стане.
11. маркировка рельса при прокатке
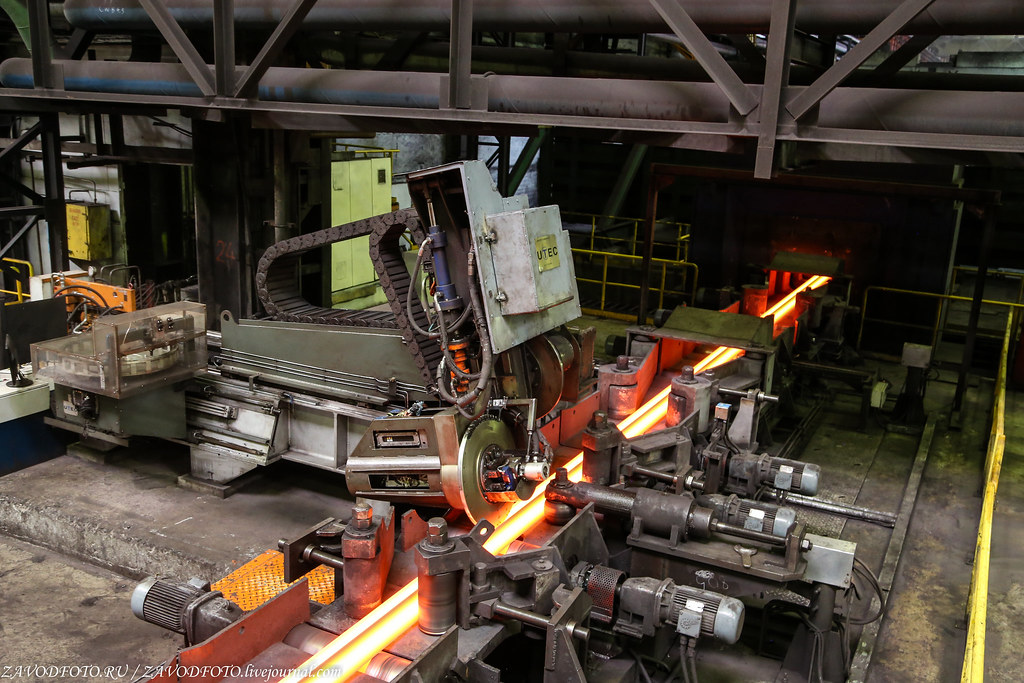
Общая площадь рельсобалочного производства составляет более 186 000 квадратных метров. Между прочим, на этой площади легко бы могли поместиться 26 футбольных полей. Да-да, таких, где проходил недавно наш чемпионат мира. Для строительства только здания рельсоотделки (он занимает 1/3 цеха) было изготовлено 15 500 тонн металлоконструкций. Это примерно две Эйфелевы башни. На устройство фундамента затрачено 144 500 кубических метров бетона. По объему это 35 больших плавательных бассейнов. Длина нового стана составляет около 1,5 километров, а если мерить всю технологическую линию, то она более 3 километров. Общий объём цеха сопоставим с объёмом пусковых установок космических кораблей.
12. рельс на ванне закалки
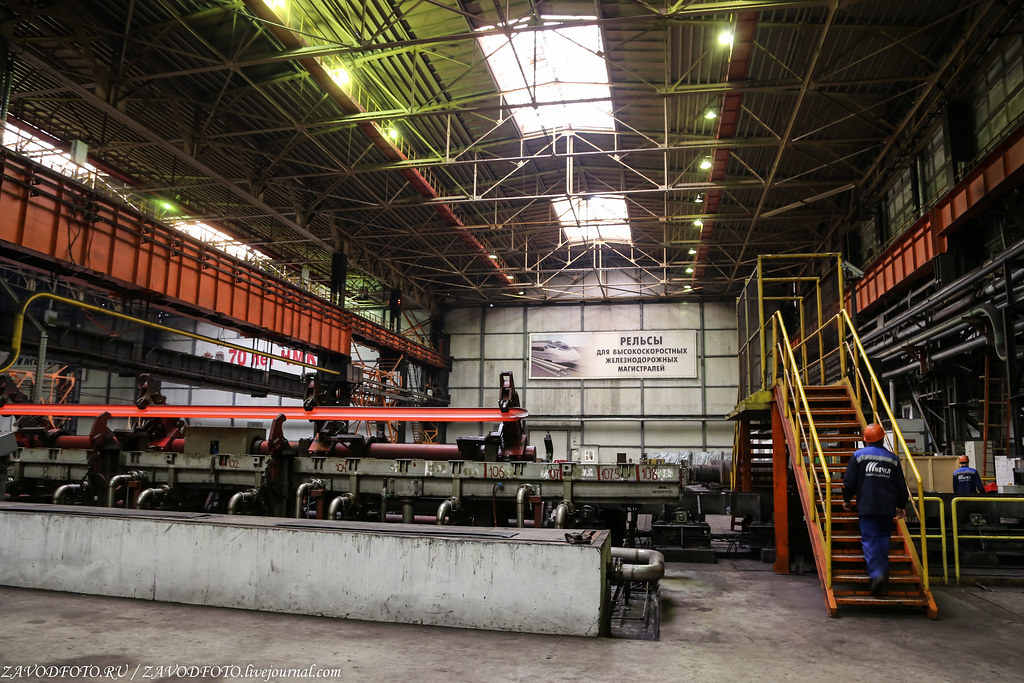
Поставщиком оборудования для стана выступила итальянская компания Danieli, генеральным подрядчиком стала китайская корпорация China Minmetals. Строили его два года. Между прочим, в марте 2017 года рельсобалочный стан ЧМК признан лучшим проектом по импортозамещению по версии Российского союза промышленников и предпринимателей. Общая производственная мощность этого стана превышает 1 млн. тонн в год фасонного проката и рельсовой продукции.
13.
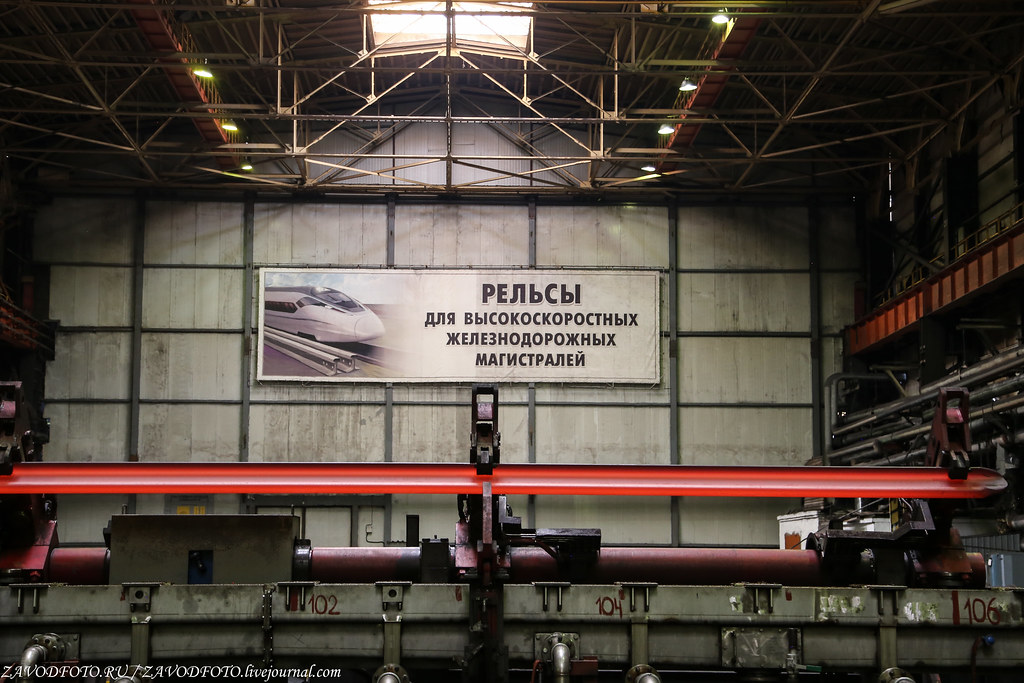
Рельсы здесь закаливаются в уникальном растворе полимера, который и придаёт им особую твёрдость и прочность. Между прочим, данная технология не имеет аналогов в России и защищена международными патентами.
14. закалка головки рельса в полимере
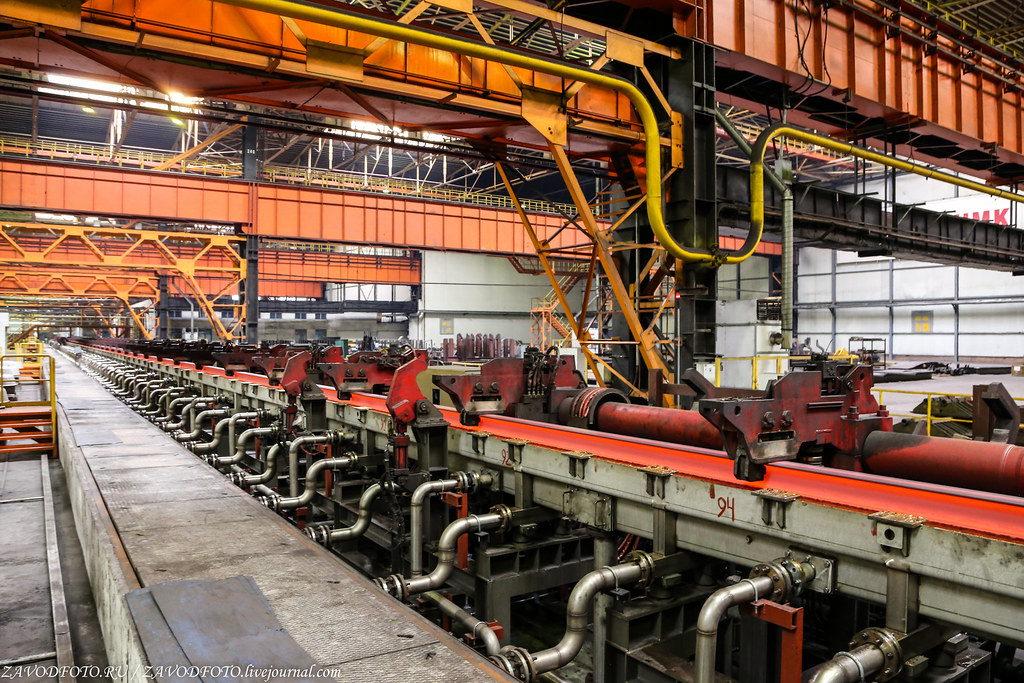
15. захваты линии закалки
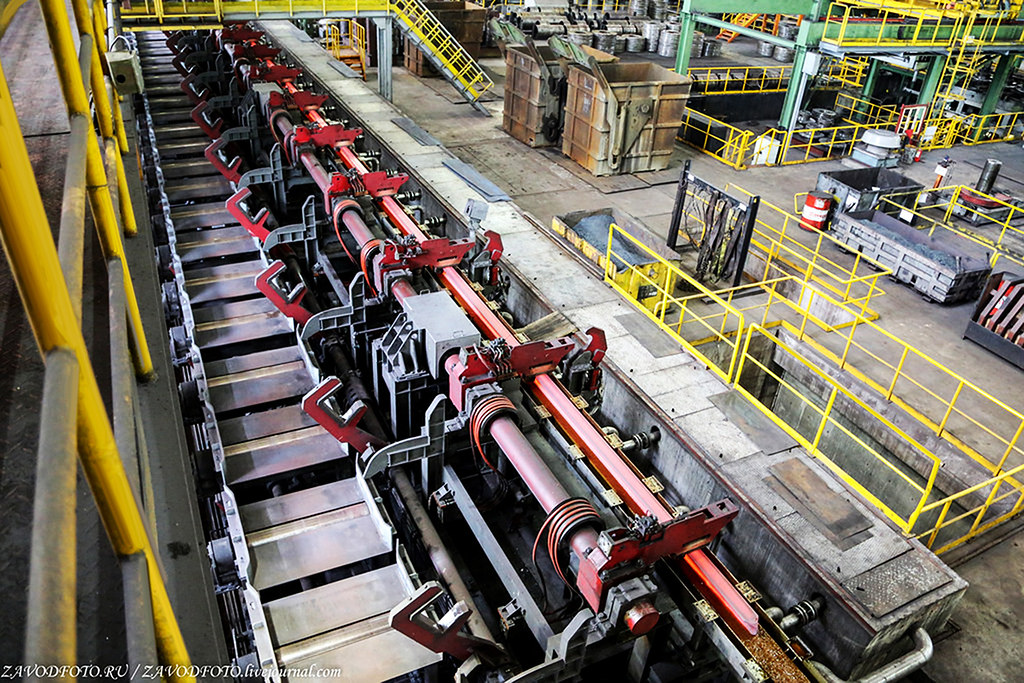
За счёт различных пластических манипуляций, выросли наши рельсы длинными-предлинными. Поэтому их надо немного укоротить. За "цирюльника" тут работает специально обученная машина - пила горячей резки.
16.
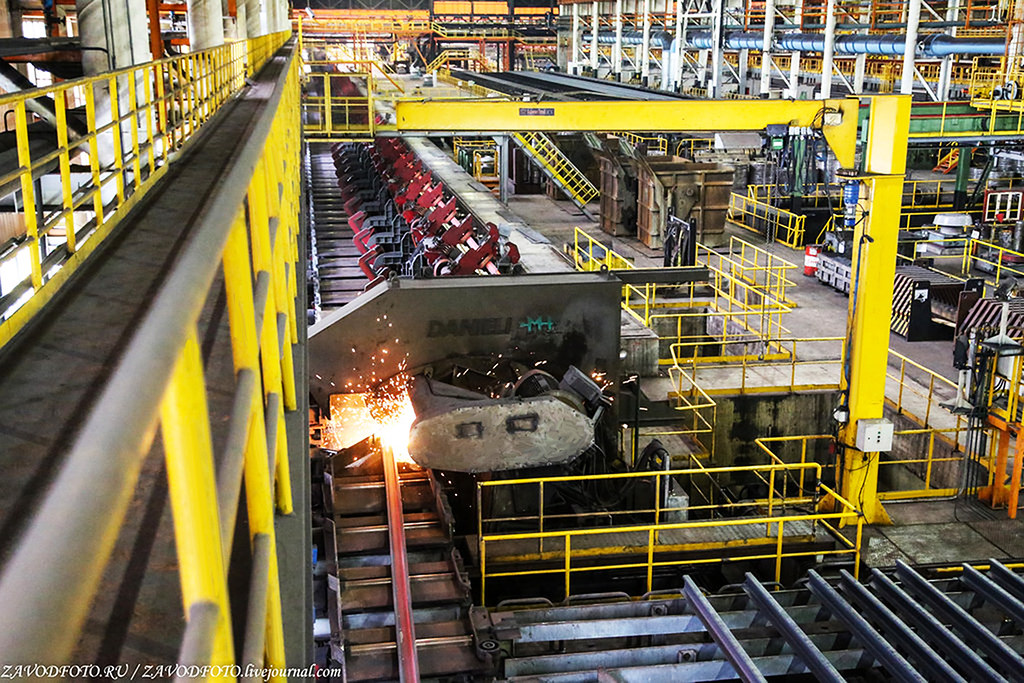
17. пила горячей резки
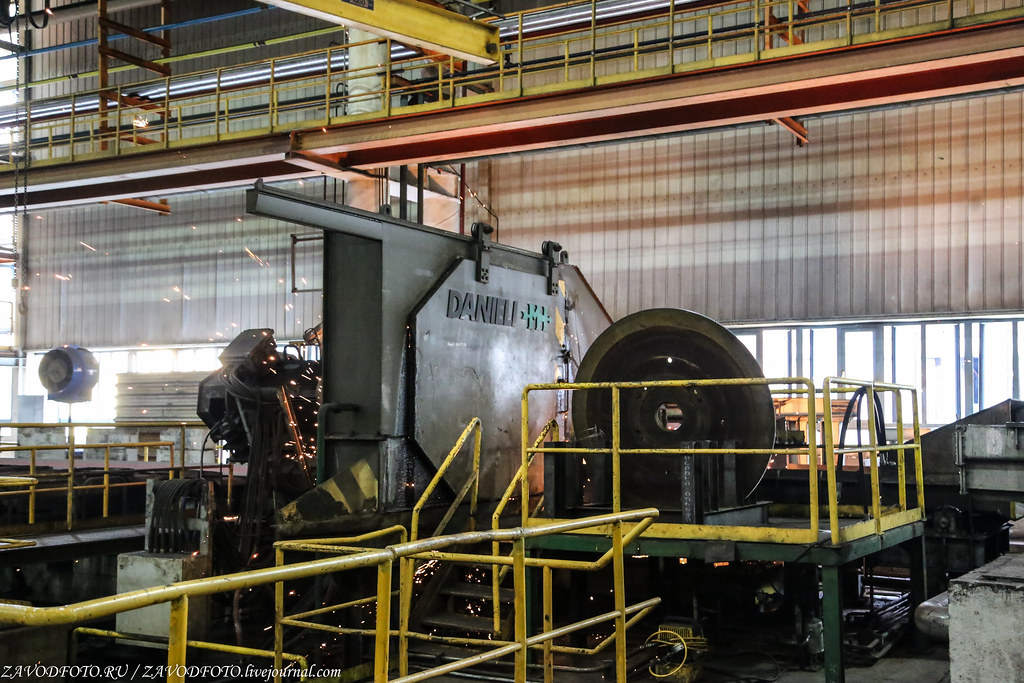
Прямолинейность рельсов достигается в том числе благодаря специальному холодильнику. На этом технологическом участке стана рельсы остывают 2,5 часа. Рейки, выставленные здесь с высокой точностью, помогают избежать деформации железнодорожной продукции, которая попадает на холодильник еще горячей.
18. Рельсы перед правкой на холодильнике
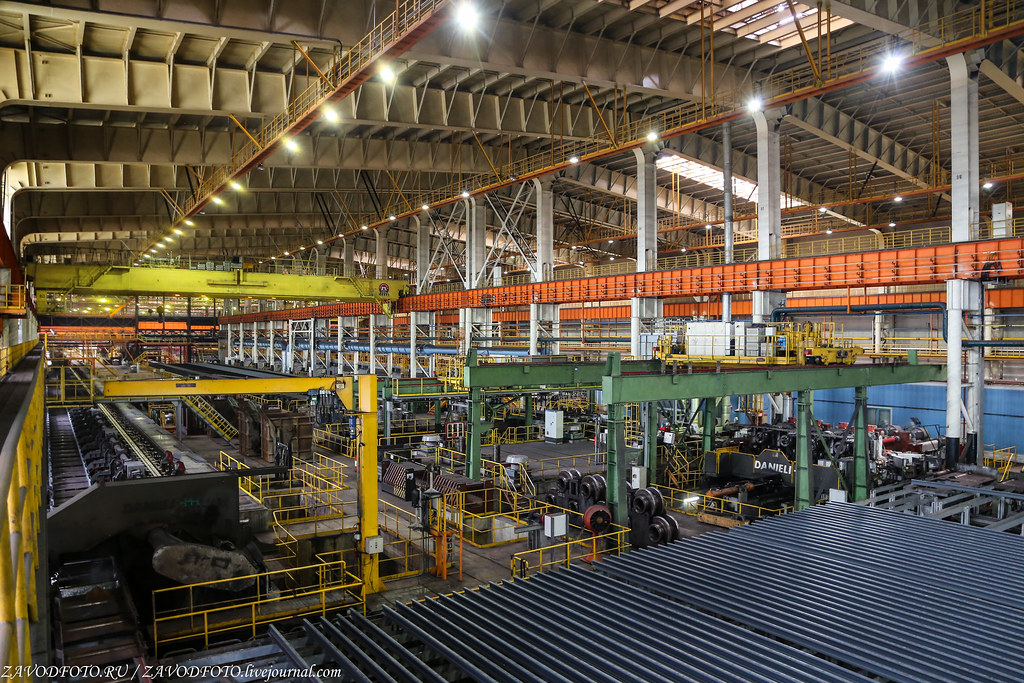
19. Пару часов они тут остывают-отдыхают.

На финишной прямой наши рейсы проходят две правильные машины, которые выпрямляют рельсы по горизонтали и вертикали.
20. горизонтальная роликоправильная машина
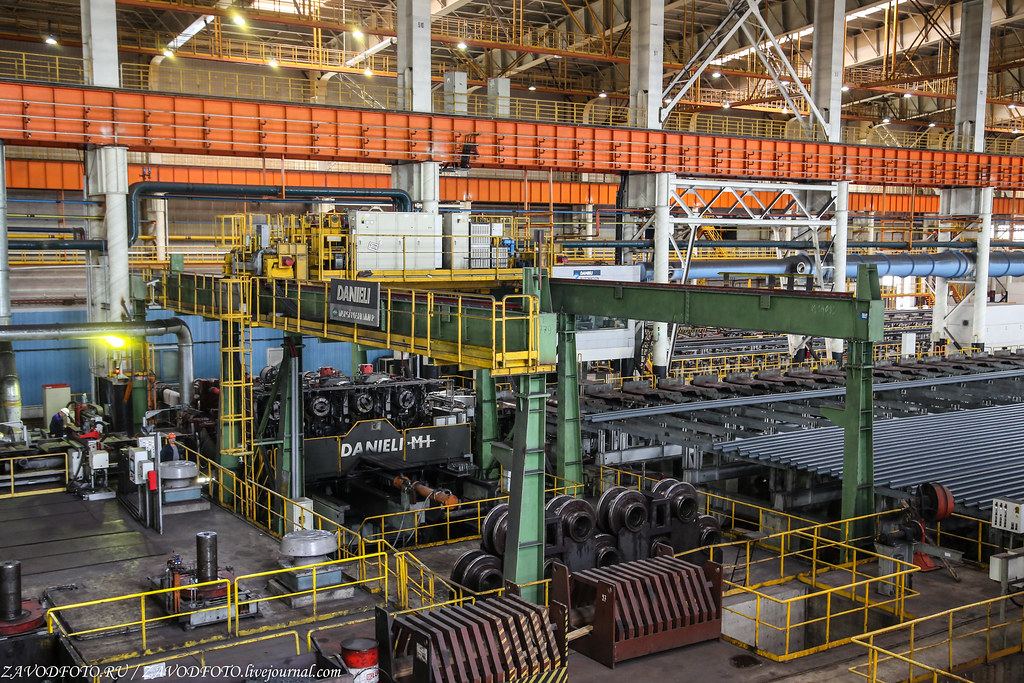
21. вертикальная роликоправильная машина
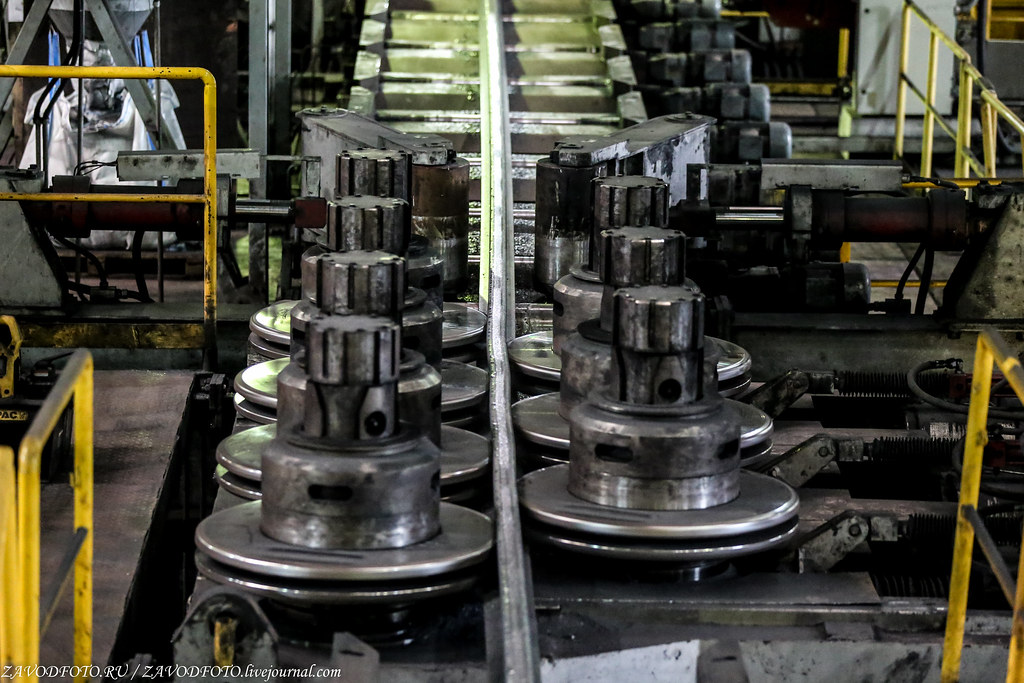
На каждой стадии производства вроде и так осуществляется полный контроль за изделием, но на финише наши рельсы ждут настоящие испытания, вернее, их пять. За это отвечает специальная автоматизированная линия неразрушающего контроля (НРК).
22. линия приборов НРК
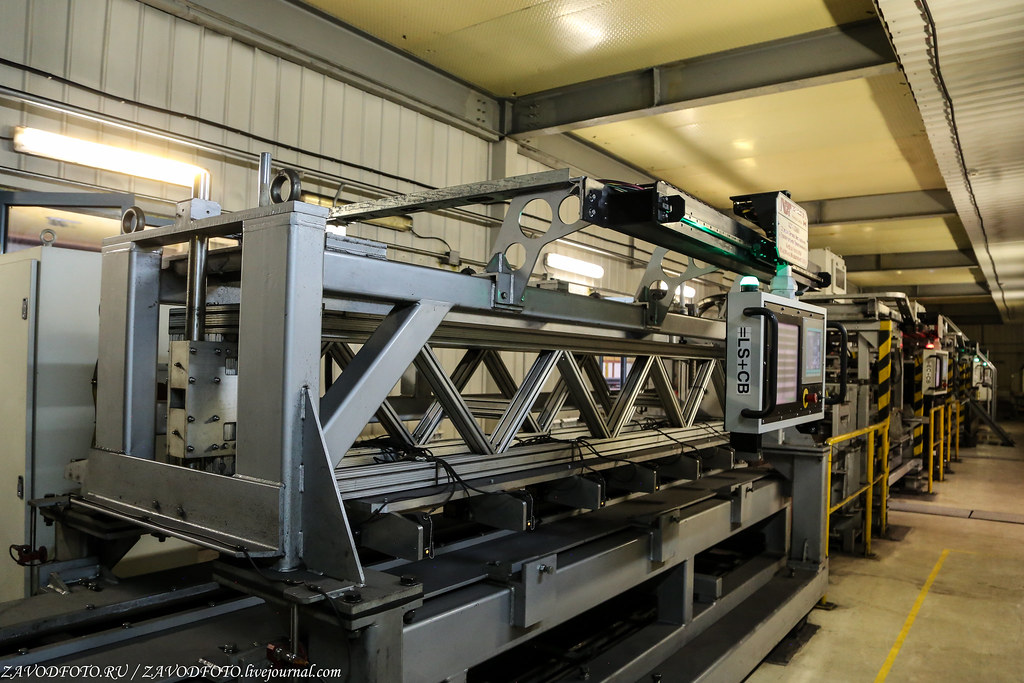
Все рельсы сканируется на прямолинейность, на наличие различных дефектов, а также сам размер профиля и качество самого металла.
23. прибор замера прямолинейности НРК
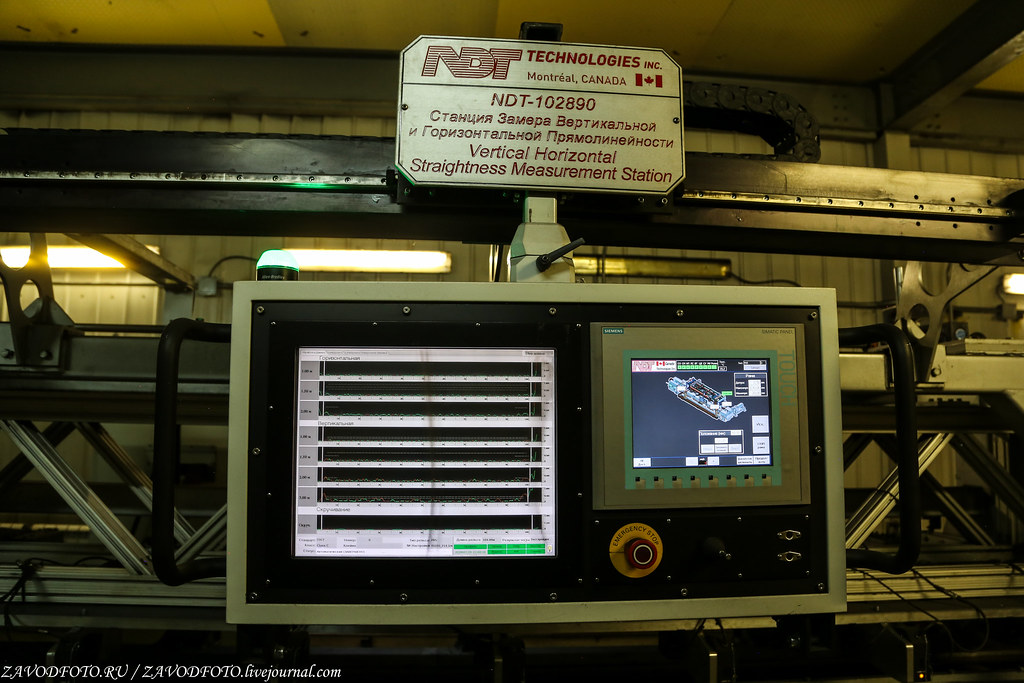
24.
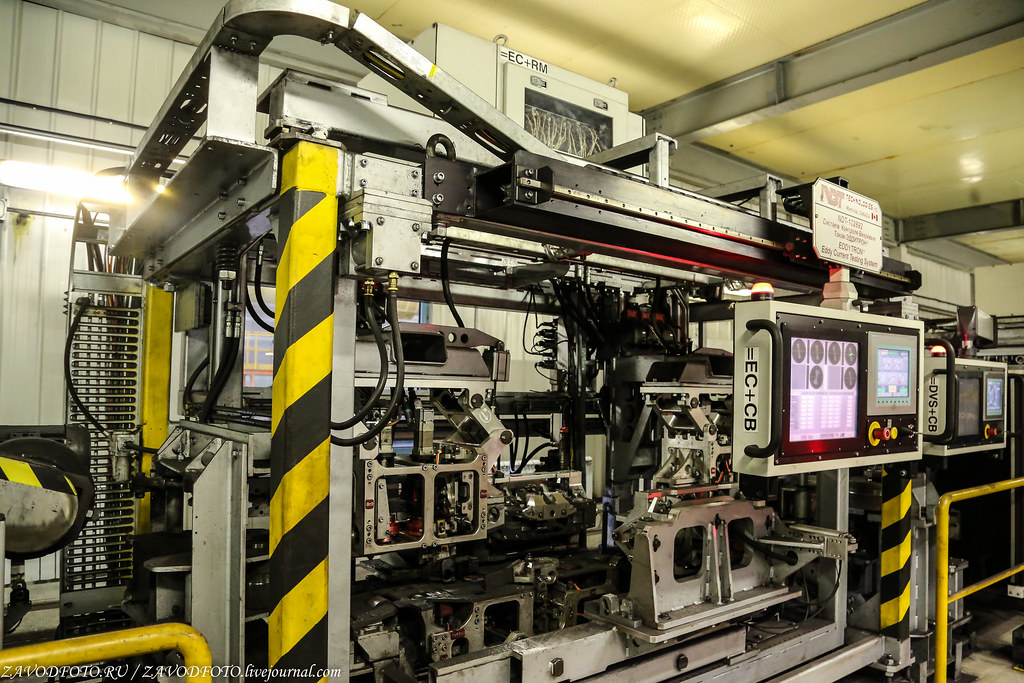
25. Кстати, рельсы ЧМК превосходят иностранные аналоги по ряду важных показателей, например, низкотемпературной надежности, повышенной износостойкости и контактной выносливости.
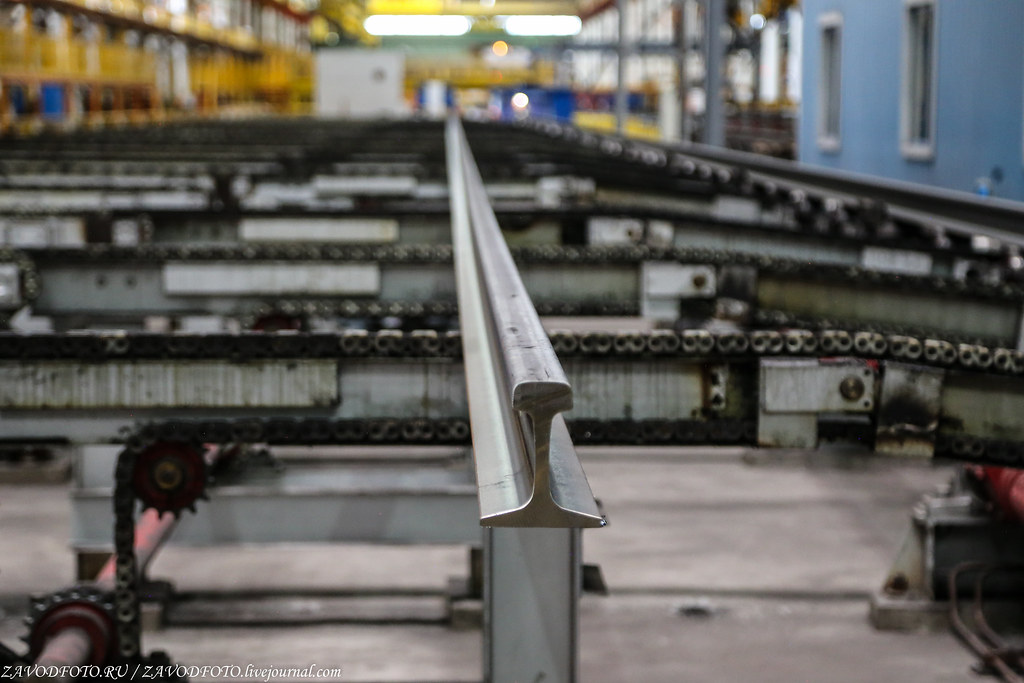
26. А ещё меня удивили вот такие краны, я ещё нигде таких не видел. Поразительно, как одним машинистом с помощью джойстиков, бесшумно приводится в движение громадная машина длиной 100 метров и весом в 400 легковых автомобилей.

27. Отгрузка рельсов клиентам осуществляется, как ж/д транспортом, так и автомобильным.

Дальнейшая сварка 100-метровых рельсов в длинные 800-метровые плети происходит на другом предприятии - Челябинском рельсосварочном РСП-13, которое также расположено на промплощадке ЧМК, но в состав Группы «Мечел» не входит. Ладно, про них вкратце тоже расскажу, хоть пока туда я и не попал. Челябинское РСП-13 - это одно из крупнейших рельсосварочных предприятий в мире. Его производственная мощность составляет около 450 тыс. тонн бесстыкового пути в год. После сварки готовые 800-метровые плети отправляются уже непосредственно к месту укладки скоростных и высокоскоростных железнодорожных магистралей. Их везут к месту укладки в таком же длинном 800-метровом железнодорожном составе – при транспортировке плети, несмотря на стальной характер, достаточно гибкие и не ломаются. Данная длина позволяет при укладке избежать большого количества сварных стыков, благодаря чему путь становится «бархатным» и бесшумным.
28.
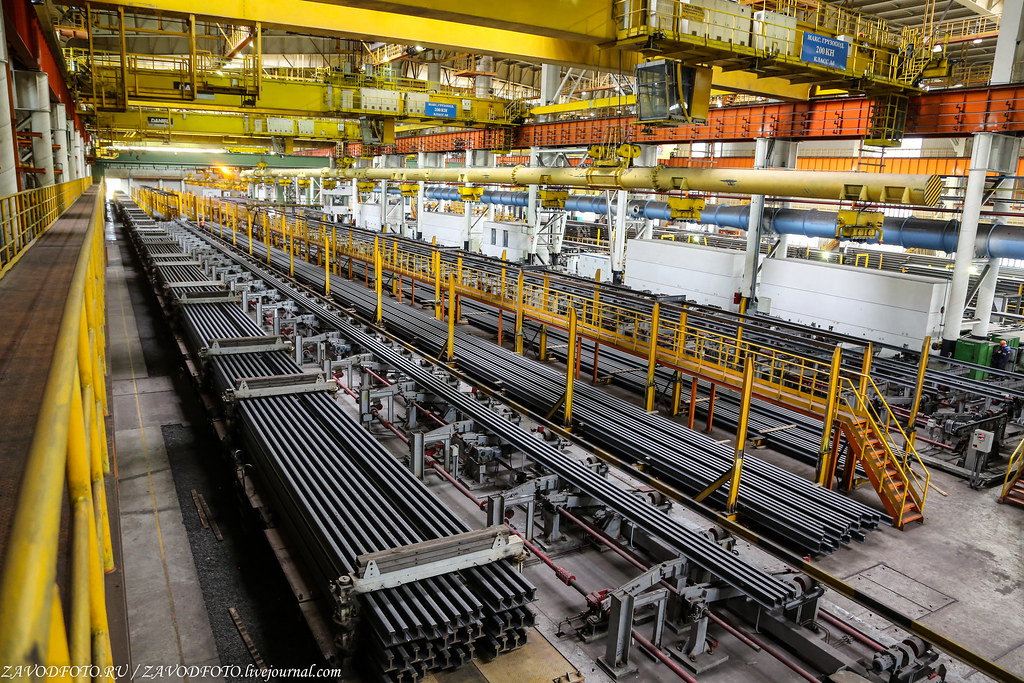
На российском рынке рельсы ЧМК с успехом заменили и превзошли импортные аналоги. Когда я своими глазами вижу такое мощное, действующее производство, упакованное лучшим в мире оборудованием, да помноженное на отечественные знания и экспертность, плюс к этому молодых амбициозных ребят, которые здесь трудятся, я с уверенностью могу сказать, что у нашей металлургии, да и у страны в целом, точно есть большое будущее.
29.
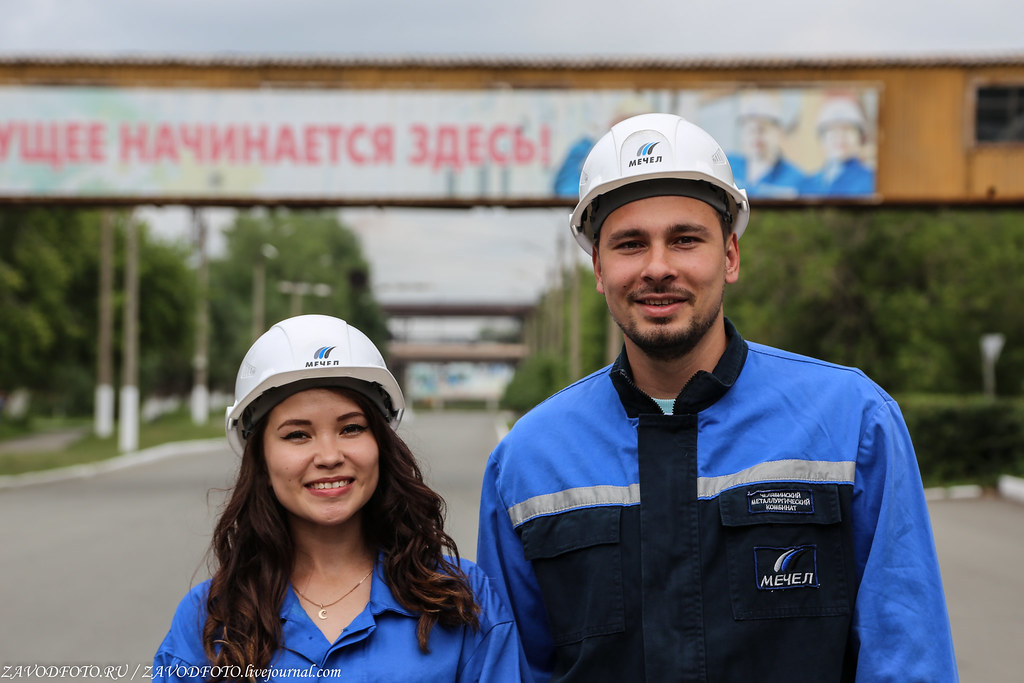
30. Большое спасибо всей пресс-службе ПАО «Мечел» за организацию такой интересной и познавательной поездки!
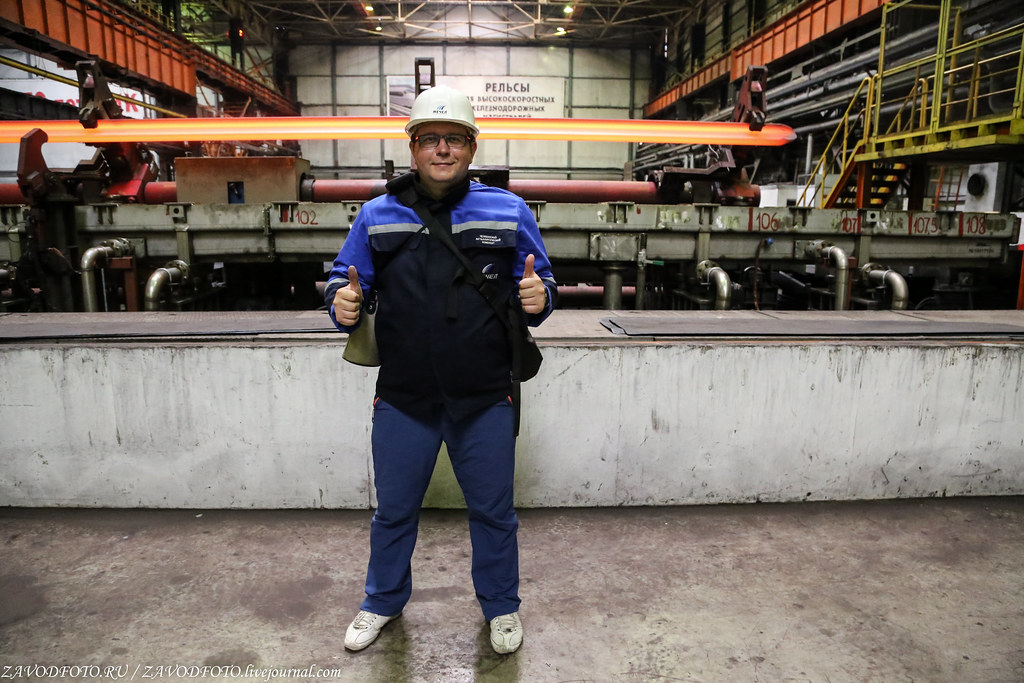
Р. S. Уважаемые собственники и акционеры, представители пресс-служб компаний, отделы маркетинга и другие заинтересованные лица, если на Вашем предприятие есть, что показать - "Как это делается и почему именно так!", мы всегда рады принять участие. Не стесняйтесь, пишите нам сами akciirosta@yandex.ru и расскажите о себе, пригласив нас к ВАМ в гости. Берите пример с лидеров!
Уже около 400 предприятий открыли перед нами свои двери, а вот и мои репортажи оттуда:
Почему наша промышленность самая лучшая в мире: http://zavodfoto.livejournal.com/4701859.html
Мы всегда рады новым друзьям, добавляйтесь и читайте нас в:

А ещё прошу всех в гости: http://ok.ru/zavodfoto и https://www.facebook.com/groups/ZAVODFOTO/
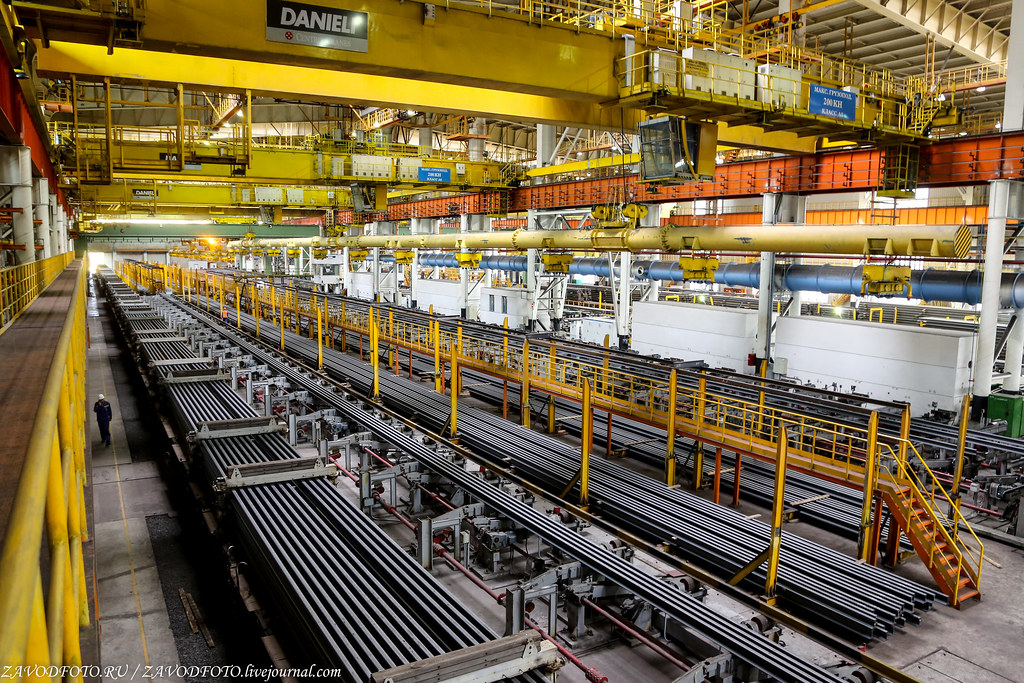
Еще до революции рассматривалось несколько проектов строительства крупного металлургического производства на Урале, качественно отличающегося от устаревших Демидовских заводов. Строительство Бакальского металлургического завода (именно так сначала назывался Челябинский металлургический комбинат) началось в 1934 году. Сырьевой базой для промышленного гиганта должно было стать Бакальское месторождение железных руд. Но вскоре стройку заморозили. Дело в том, что советское металлургическое машиностроение потянуть такой проект было не в состоянии, а средств на закупку оборудования за границей то ли не было, то ли сами иностранцы не соглашались его продать. Так в замороженном виде Бакальский завод и просуществовал до 1941 года.
2.
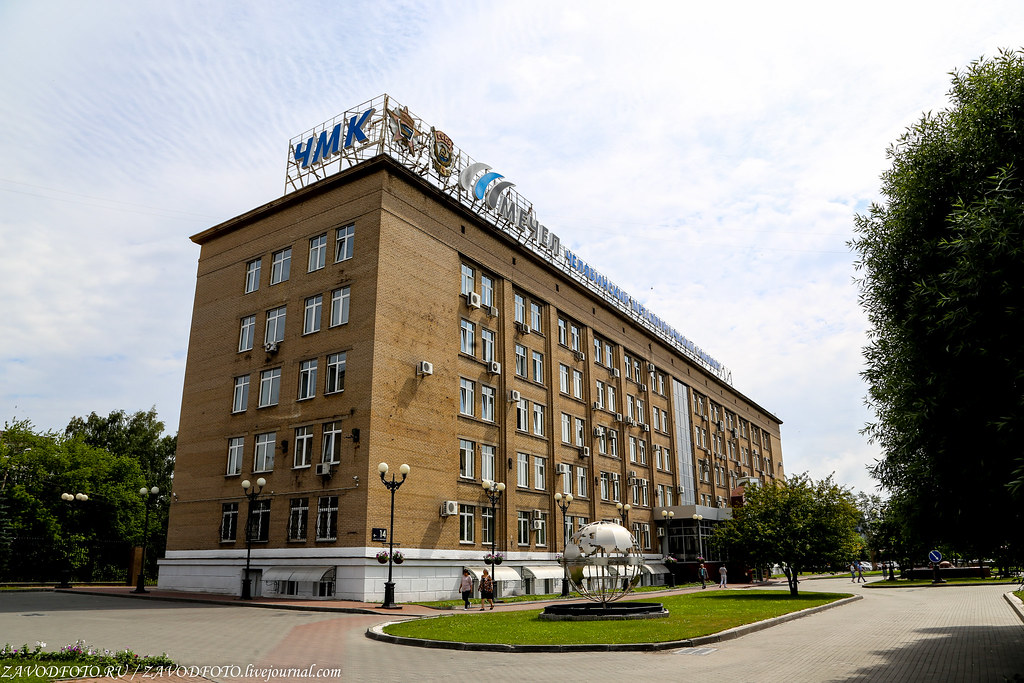
Когда я ехал сюда, у меня не было никаких сомнений, что это очень мощный и большой завод. Вот посмотрите, какой огромный цех, где расположены лишь некоторые, так сказать, запчасти к одному из станов.
3.
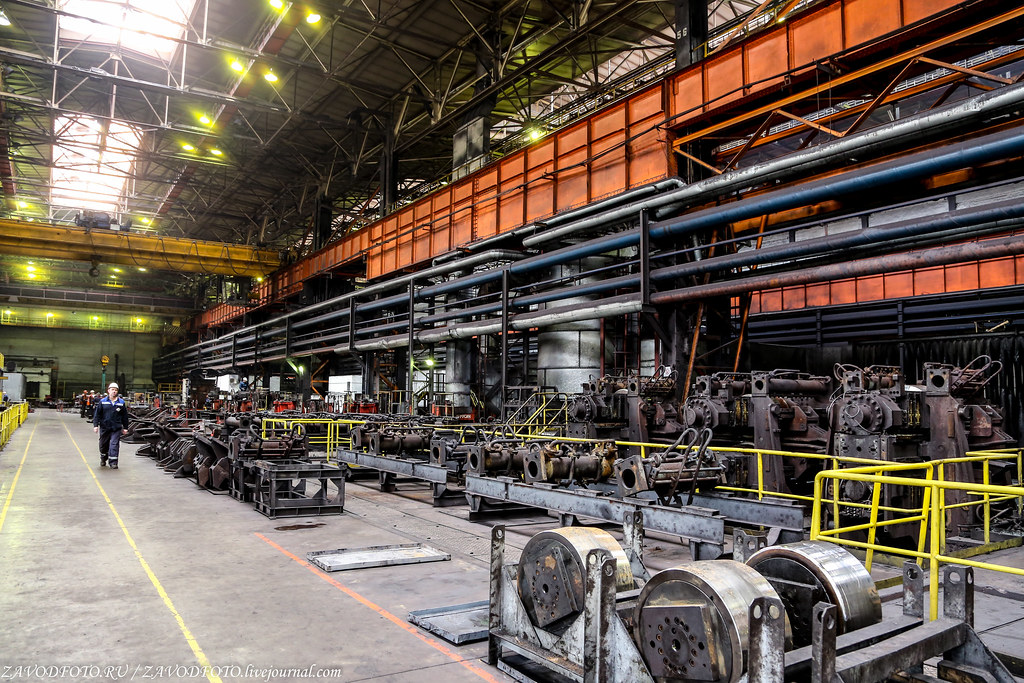
За десять дней до начала Великой Отечественной войны Советом Народных Комиссаров СССР принято Постановление о строительстве завода. Незакрытый вопрос с оборудованием для будущего предприятия решился сам собой: с осени 1941 года на строительную площадку стали прибывать эшелоны с эвакуированными мощностями Алчевского металлургического завода, подмосковной Электростали, завода "Красный октябрь" (Сталинград), Новолипецкого металлургического завода и Запорожстали. 1 мая 1942 года был уложен первый кубометр бетона в фундамент будущего электросталеплавильного цеха. 19 апреля 1943 года первый металл хлынул в разливочный ковш. Эта дата и является официальным Днём рождения Челябинского металлургического комбината. 30 апреля первая доменная печь выдала первый чугун, а 2 августа на коксовой батарее № 1 получен первый кокс. В каждом третьем танке и боевом самолёте Великой Отечественной войны, выпускаемых с 1943 года, была челябинская сталь. Тогда же здесь научились выплавлять металл для шарикоподшипников (прежде его массово закупали в Великобритании). В советское время завод успешно участвовал в выполнении космических программ, производил металл для военно-промышленного комплекса и наукоёмкого сектора экономики. В 2003 году ЧМК вошёл в состав Группы «Мечел». И практически сразу же на предприятии начинается реализация масштабной программы технического перевооружения, по сути, и сейчас эта история продолжается.
4. стенд с прокатными валками
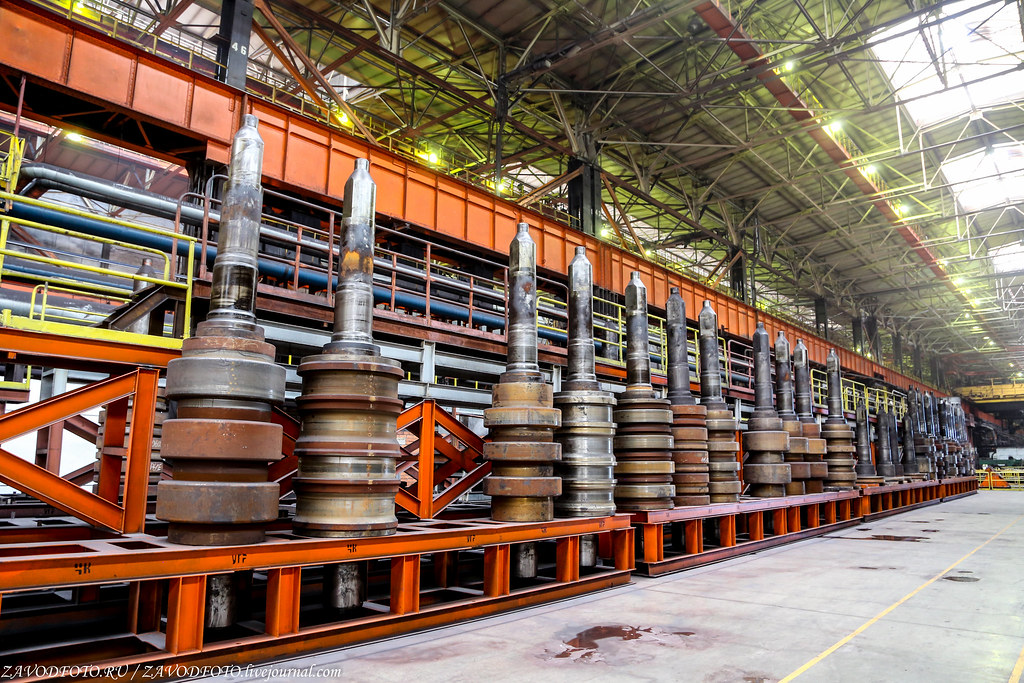
В качестве примера предлагаю остановиться на нашей сегодняшней повестке, производстве рельсов нового поколения. В марте 2012 года на ЧМК запустили комплекс по производству рельсовой стали, который включил в себя машину непрерывного литья заготовок № 5 (МНЛЗ-5) и агрегаты внепечной обработки стали, годовой производительностью 1,2 млн тонн. А в июле 2013 года открыли новый универсальный рельсобалочный стан (УРБС), который стал первым в России производством фасонного проката и рельсов длиной от 12,5 до 100 метров. Важно отметить, что на новом производстве создали более 1500 новых рабочих мест, а благодаря выводу из эксплуатации старого оборудования и строительству современных очистных сооружений, существенно снизилась и доля воздействия ЧМК на окружающую среду, что для Челябинска весьма актуально.
5. валки обжимной клети
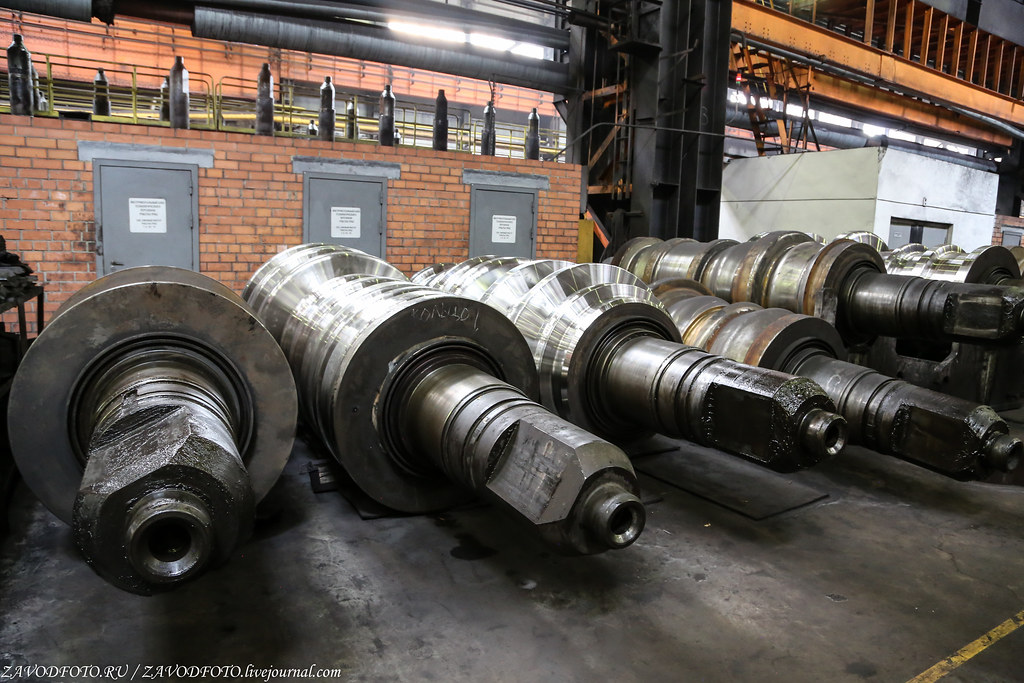
6. Нагревательная печь. Примерно каждые 2 минуты отсюда выходят заготовки, из которых и получаются наши 100-метровые рельсы.
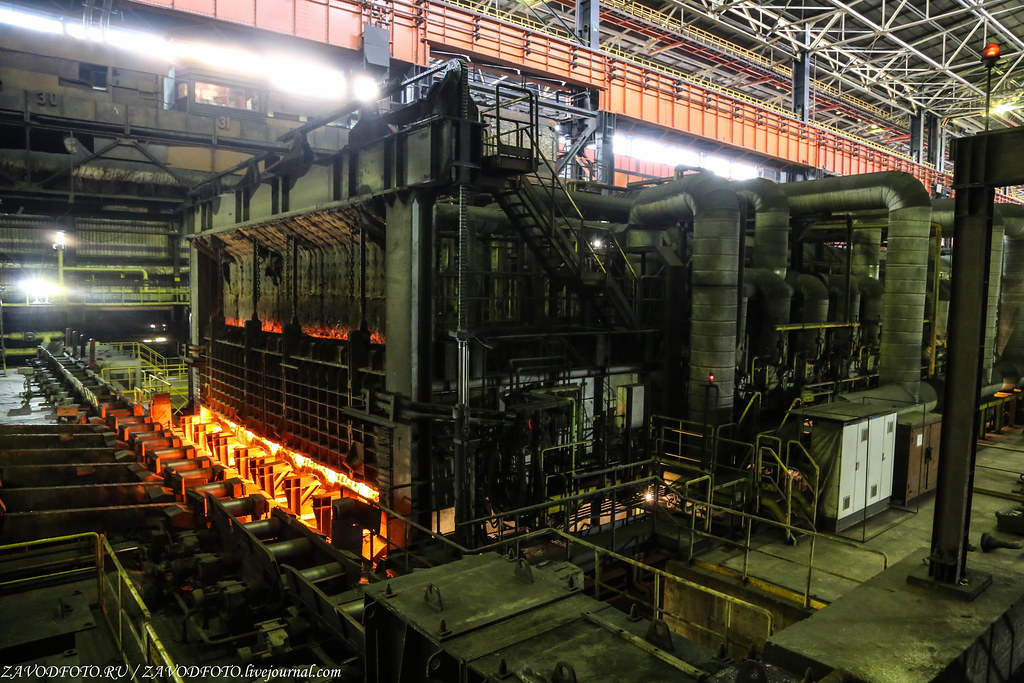
Вкратце весь процесс производства представлен на этой картинке. Если идти с самого начала, то сталь для рельсов выплавляется в кислородно-конвертерном цехе, где попадает в ковш-печь, доводится до определенной температуры и химического состава. Следующий этап – вакууматор. Здесь путем снижения давления из стали удаляются газообразные элементы. Потом идет процесс разливки и кристаллизации на машине непрерывной разливки заготовок (МНЛЗ), где получается блюм с необходимым качеством стали. Далее заготовки режутся, остывают и после тщательного контроля, вновь отправляются в нагревательную печь. Вот где по-настоящему жарко - 1300°С, это температура действующего вулкана.
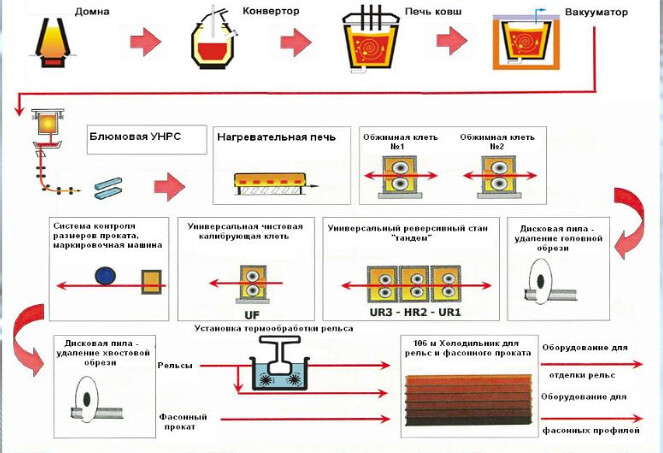
7. Длина рельсовой заготовки составляет порядка 8 метров, вес - около 7 тонны. После того, как она вышла из печи, заготовка попадает в установку, где сбивается окалина с помощью хорошего контрастного душа. Струи воды под давлением в 250 атмосфер, как будто ножом по маслу, отделяют корку от металла со всех сторон.
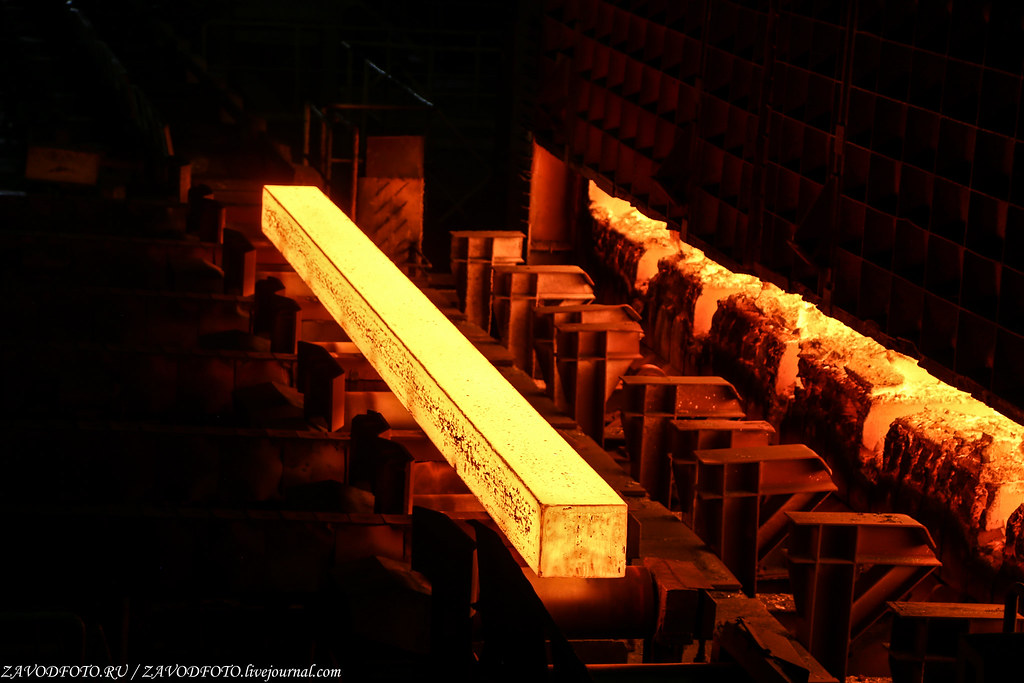
Сегодня Челябинский металлургический комбинат - это одно из крупнейших в России предприятий полного металлургического цикла по выпуску качественных и высококачественных сталей. Предприятие выпускает широкий ассортимент продукции: арматуру для стройки, нержавейку для машиностроения, рельсы, балку. За всё время работы на ЧМК было освоено производство около 2 000 различных марок стали и сплавов, а также более 4 000 профилеразмеров проката. Между прочим, ЧМК - это одно из немногих предприятий страны, которому дано право присваивать продукции собственный индекс - ЧС (Челябинская Сталь). Среди клиентов ЧМК замечены: атомная энергетика, тяжелая промышленность, химическое и энергетическое производство, автомобильное и сельскохозяйственное машиностроение, подшипниковые и трубопрокатные заводы, строительные компании и, конечно же, РЖД. Например, в 2017-м году ЧМК отгрузил РЖД 330 тысяч тонн рельсов, если перевести тонны в километры, длина пути покроет расстояние от Челябинска до Санкт-Петербурга.
8. На следующей стадии заготовку в свои крепкие объятия принимает обжимная клеть. Благодаря ей придаётся геометрическая форма предварительно, как его называют прокатчики, «лидерному» профилю уже похожему на готовый рельс или балку.
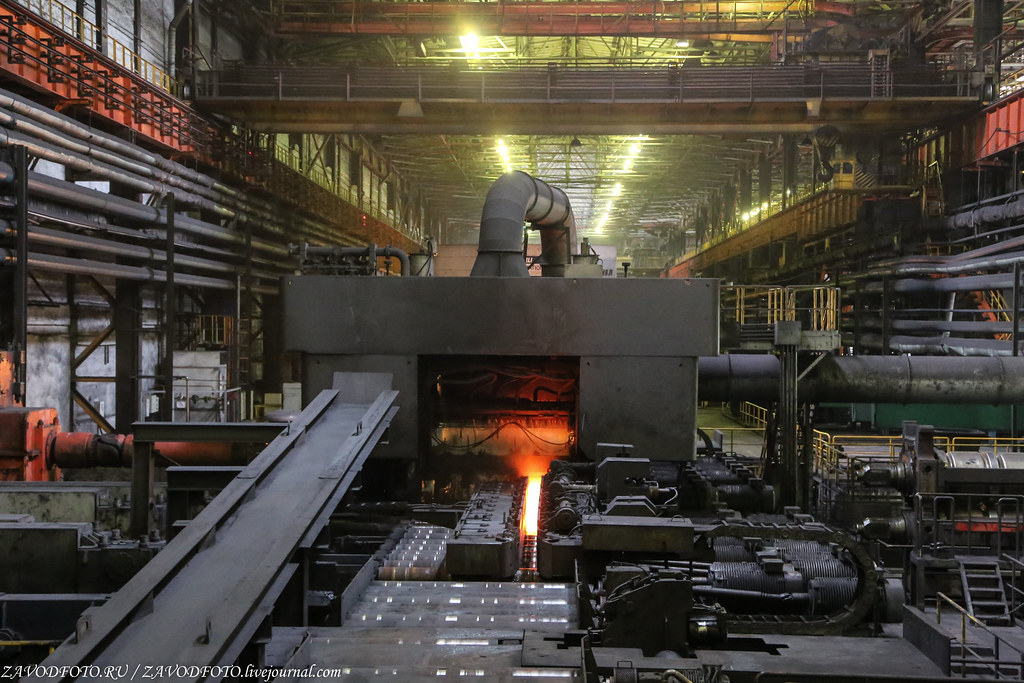
Универсальность стана как раз заключается в выпуске как рельсовой продукции, так и фасонного проката для строительной отрасли. Вот, например, мимо нас проехала «собачья кость», так, любя, местные металлурги называют заготовки для двутавровой балки, используемой в строительстве.
9.
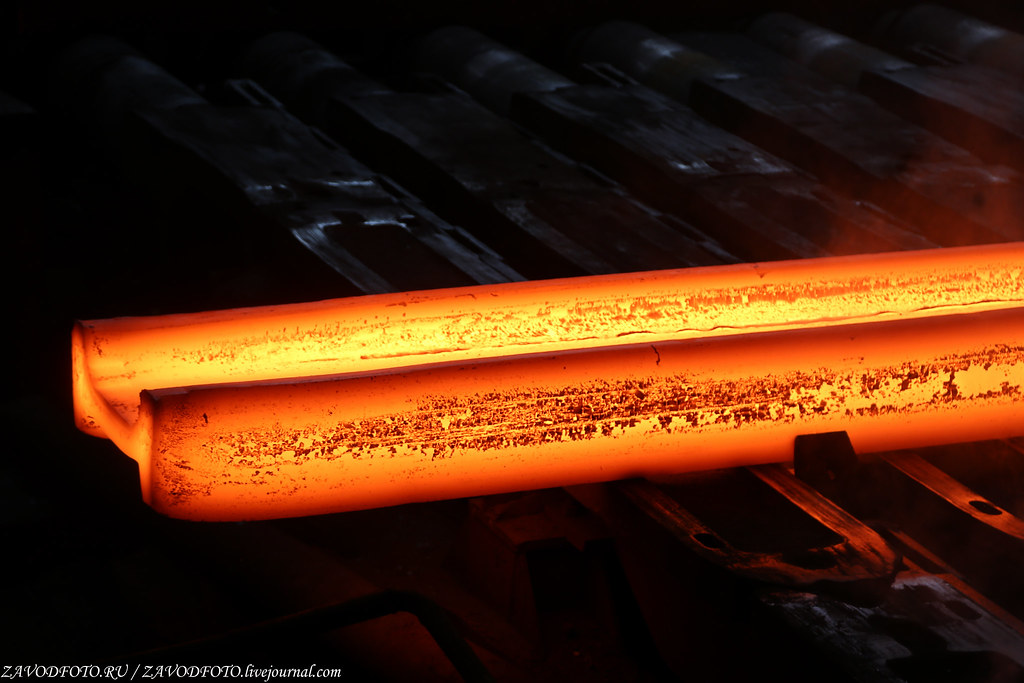
Аспирационная система очистки газов - вот еще объект, на который хотел бы обратить ваше внимание. Создавалась она специально под рельсобалочный стан. Проект индивидуальный. Такая система больше нигде не используется. Имеет 3 уровня очистки. По принципу работы аспирационная система схожа с бытовым пылесосом, только огромных размеров. Она улавливает мельчайшие частицы пыли и различные химические элементы, образующиеся при горячей прокатке.
10. Аспирационная система очистки газов.
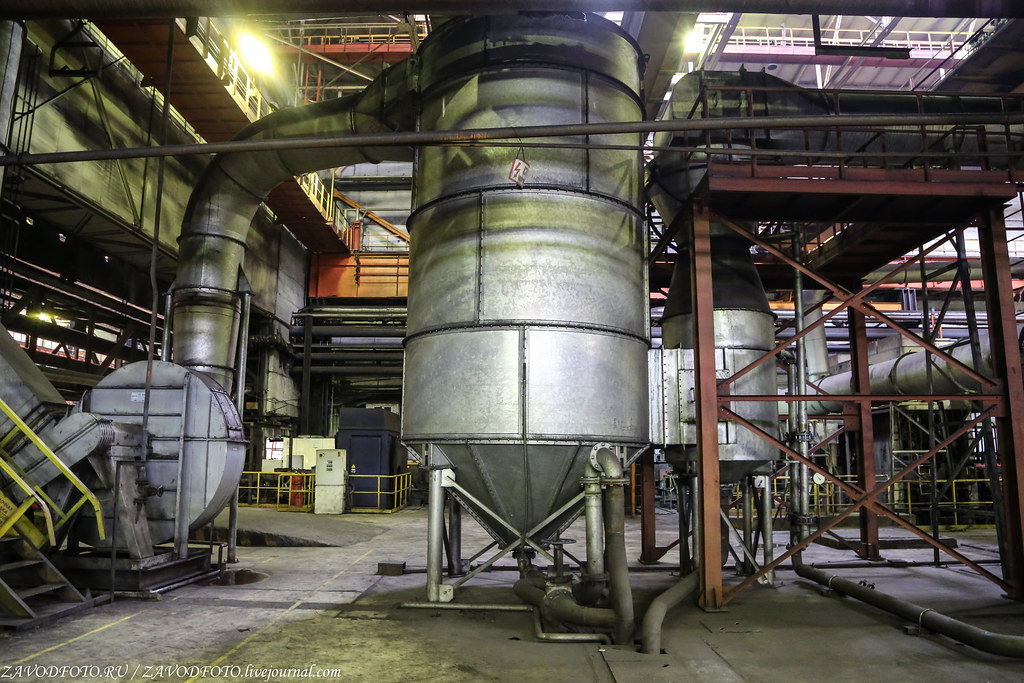
Наконец, наши заготовки попадают на клети рельсобалочного стана. Именно здесь и производятся рельсы длиной до 100 метров с применением самых новейших технологий. И первым делом на них ставят клеймо качества, свидетельствующего, что рельсы сделаны на Урале. На ЧМК гордятся своей продукцией. Буква «Ч» - фирменный знак предприятия – всегда стоит на каждом произведённом рельсе, как и дата его выпуска на стане.
11. маркировка рельса при прокатке
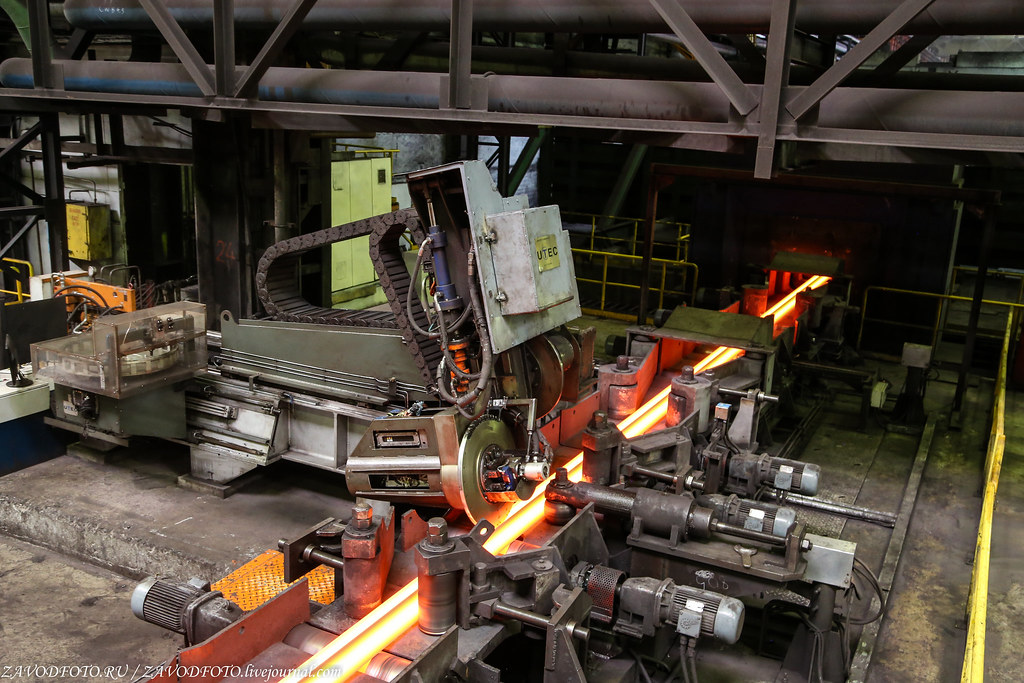
Общая площадь рельсобалочного производства составляет более 186 000 квадратных метров. Между прочим, на этой площади легко бы могли поместиться 26 футбольных полей. Да-да, таких, где проходил недавно наш чемпионат мира. Для строительства только здания рельсоотделки (он занимает 1/3 цеха) было изготовлено 15 500 тонн металлоконструкций. Это примерно две Эйфелевы башни. На устройство фундамента затрачено 144 500 кубических метров бетона. По объему это 35 больших плавательных бассейнов. Длина нового стана составляет около 1,5 километров, а если мерить всю технологическую линию, то она более 3 километров. Общий объём цеха сопоставим с объёмом пусковых установок космических кораблей.
12. рельс на ванне закалки
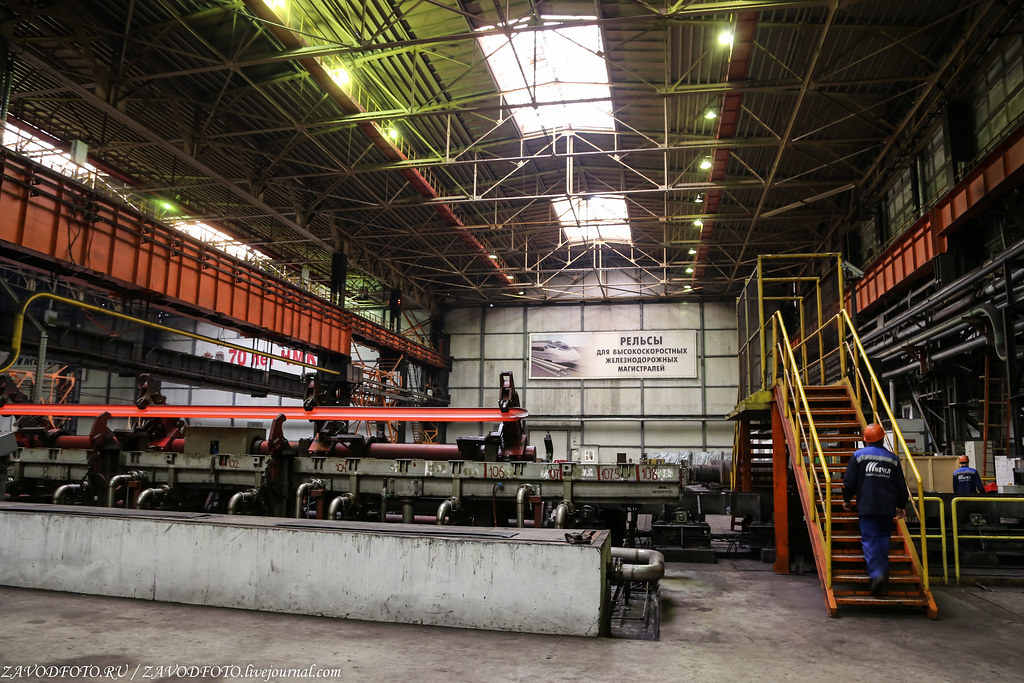
Поставщиком оборудования для стана выступила итальянская компания Danieli, генеральным подрядчиком стала китайская корпорация China Minmetals. Строили его два года. Между прочим, в марте 2017 года рельсобалочный стан ЧМК признан лучшим проектом по импортозамещению по версии Российского союза промышленников и предпринимателей. Общая производственная мощность этого стана превышает 1 млн. тонн в год фасонного проката и рельсовой продукции.
13.
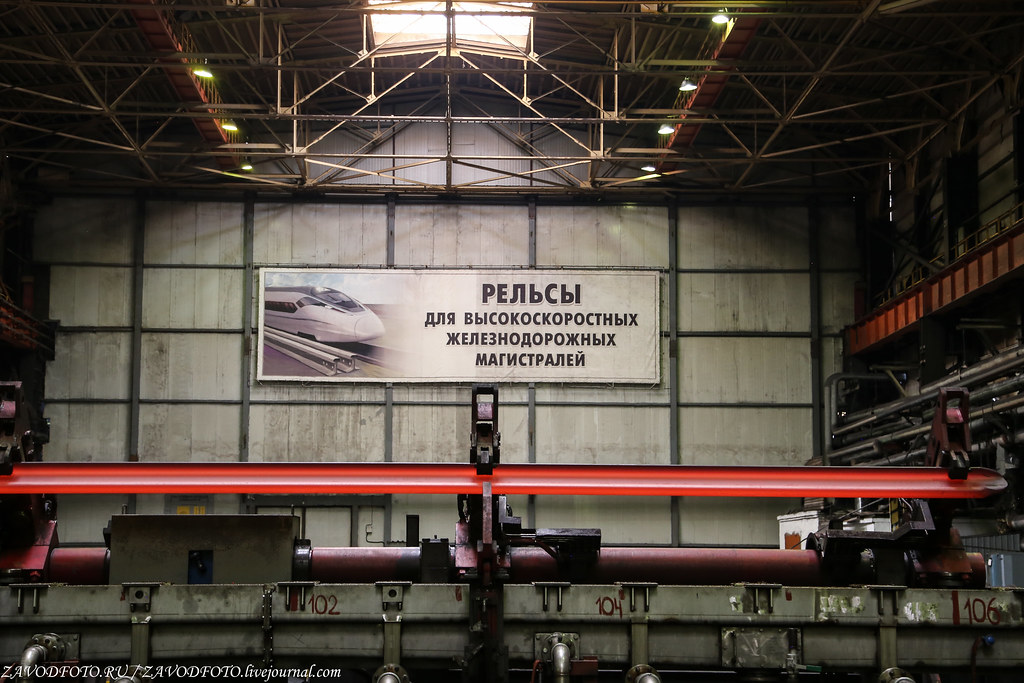
Рельсы здесь закаливаются в уникальном растворе полимера, который и придаёт им особую твёрдость и прочность. Между прочим, данная технология не имеет аналогов в России и защищена международными патентами.
14. закалка головки рельса в полимере
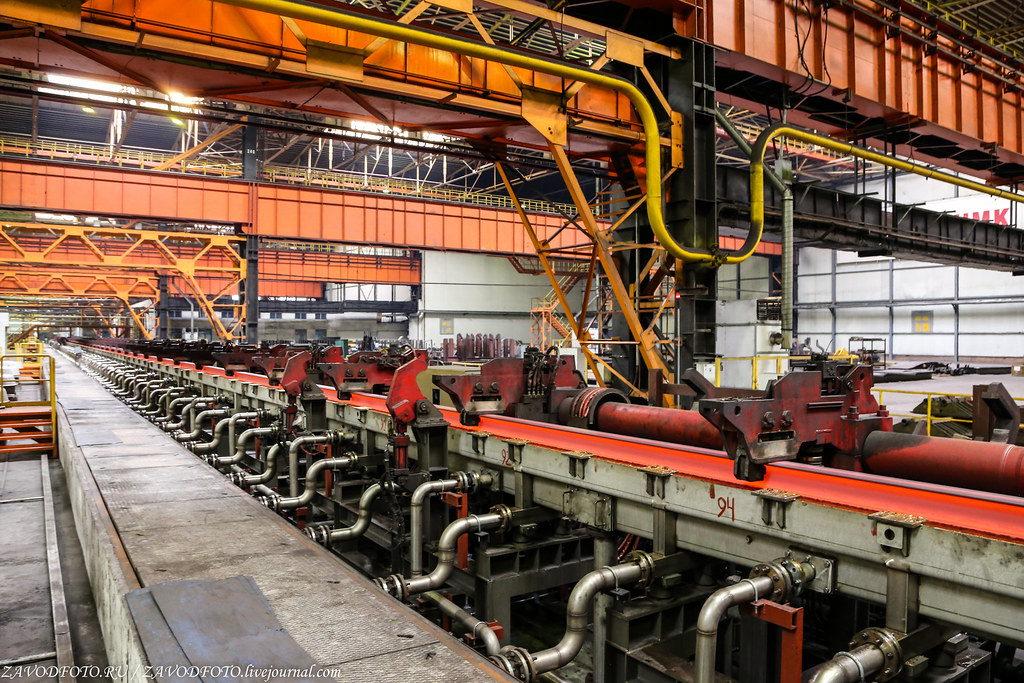
15. захваты линии закалки
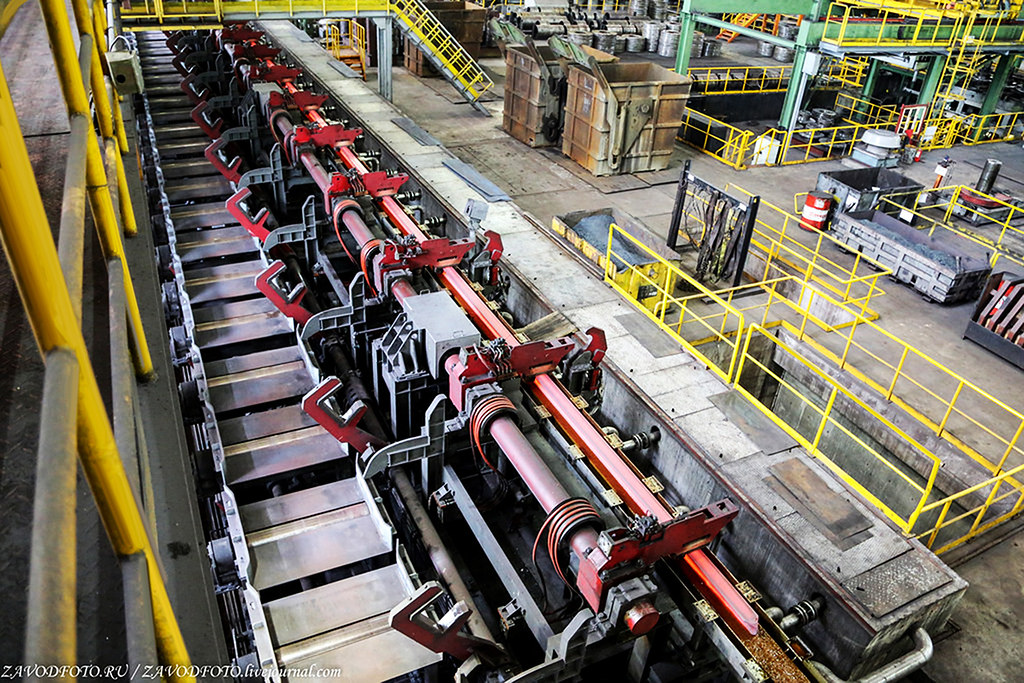
За счёт различных пластических манипуляций, выросли наши рельсы длинными-предлинными. Поэтому их надо немного укоротить. За "цирюльника" тут работает специально обученная машина - пила горячей резки.
16.
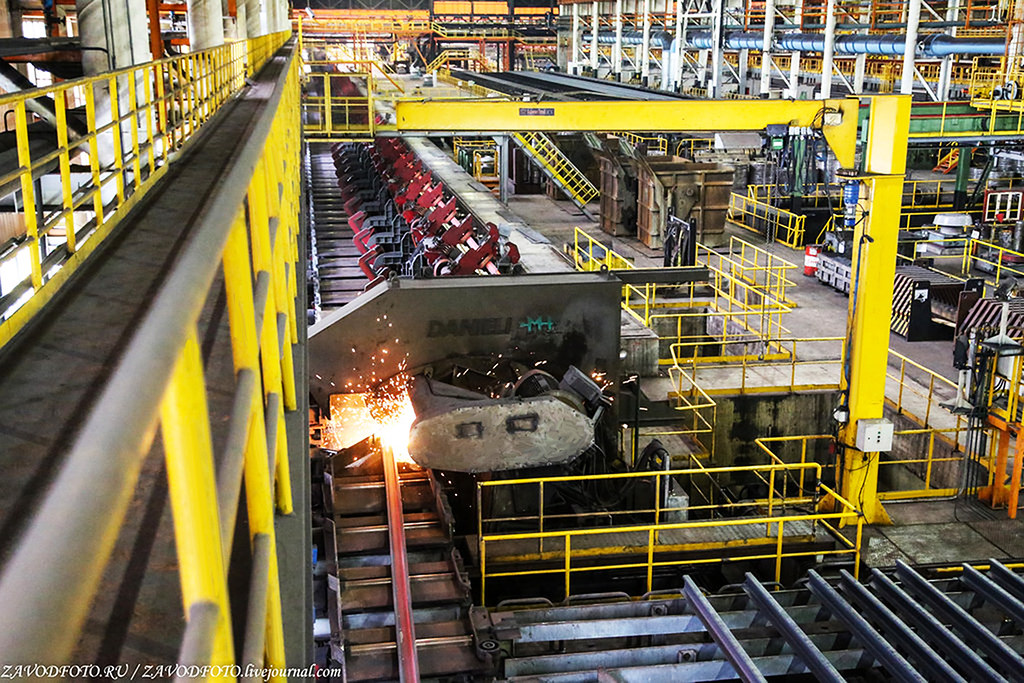
17. пила горячей резки
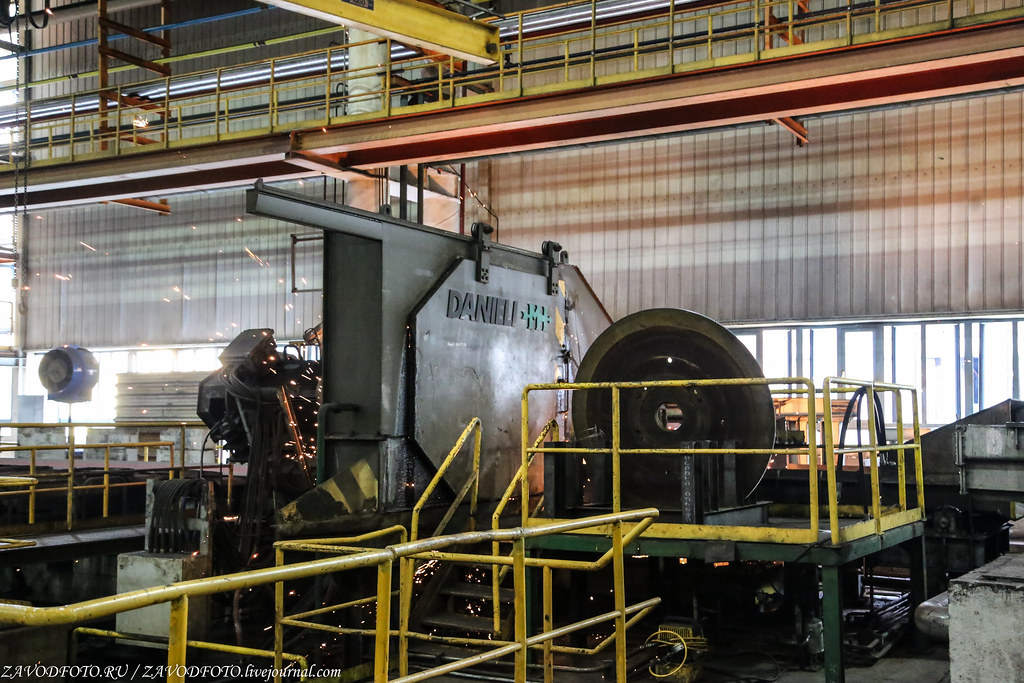
Прямолинейность рельсов достигается в том числе благодаря специальному холодильнику. На этом технологическом участке стана рельсы остывают 2,5 часа. Рейки, выставленные здесь с высокой точностью, помогают избежать деформации железнодорожной продукции, которая попадает на холодильник еще горячей.
18. Рельсы перед правкой на холодильнике
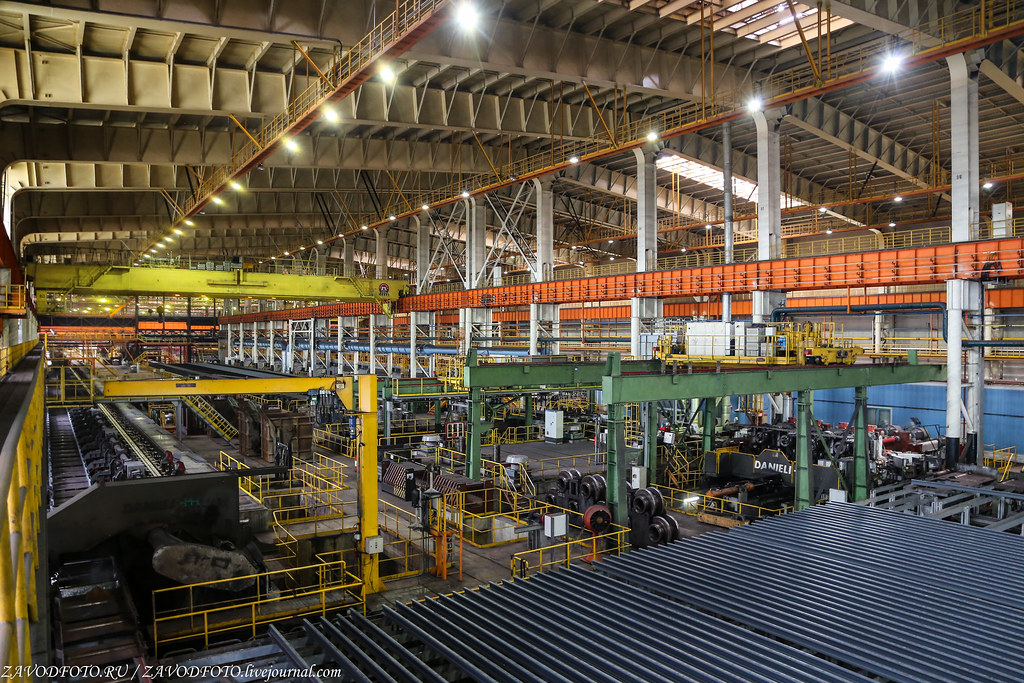
19. Пару часов они тут остывают-отдыхают.

На финишной прямой наши рейсы проходят две правильные машины, которые выпрямляют рельсы по горизонтали и вертикали.
20. горизонтальная роликоправильная машина
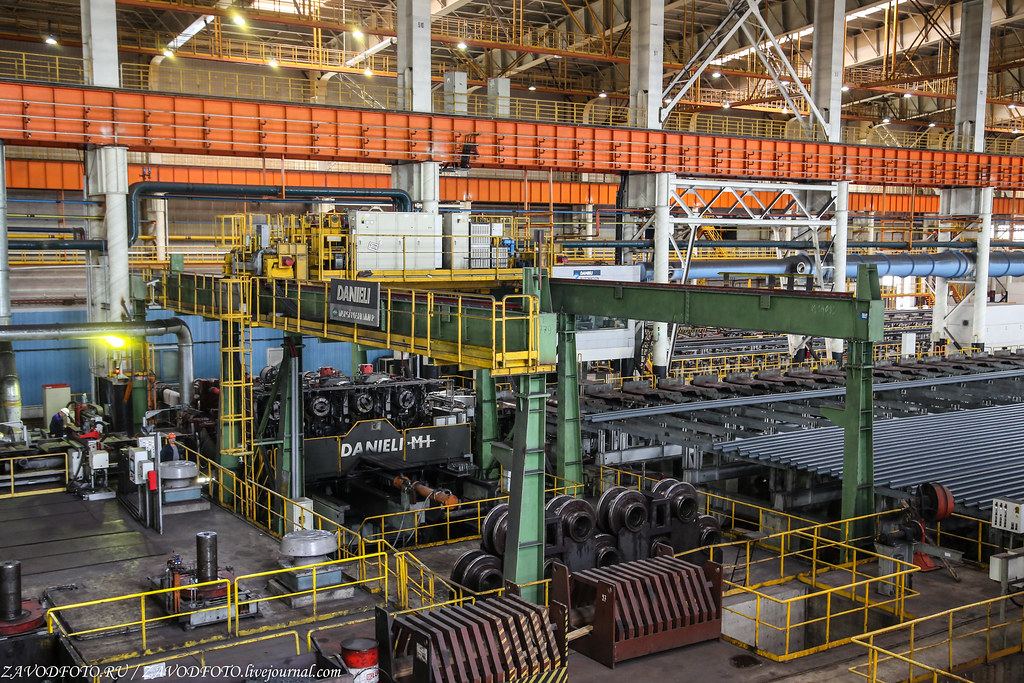
21. вертикальная роликоправильная машина
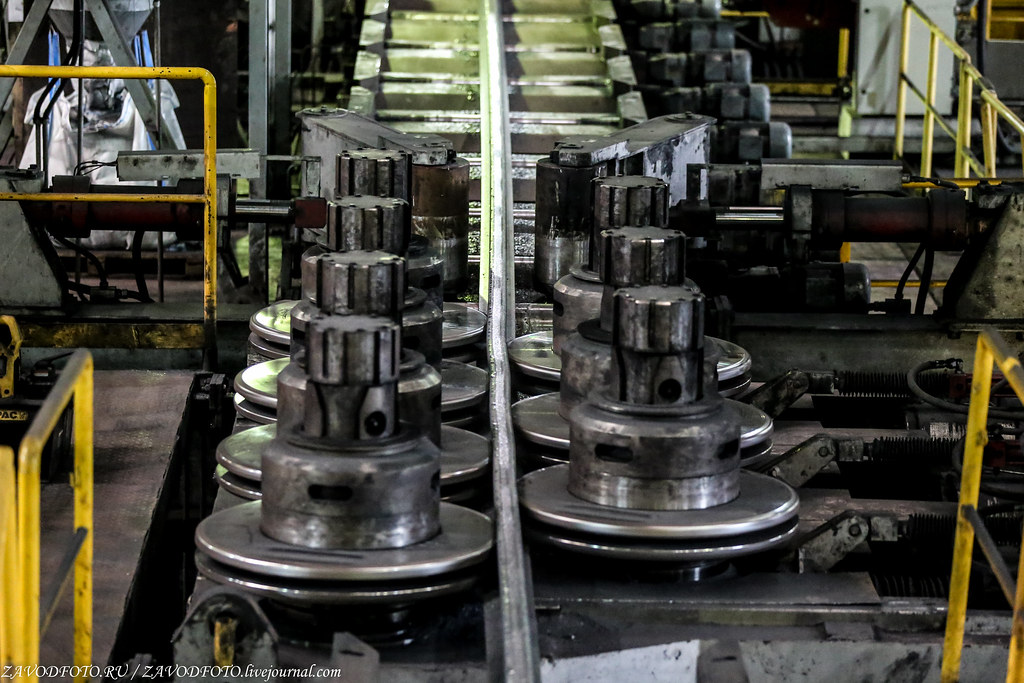
На каждой стадии производства вроде и так осуществляется полный контроль за изделием, но на финише наши рельсы ждут настоящие испытания, вернее, их пять. За это отвечает специальная автоматизированная линия неразрушающего контроля (НРК).
22. линия приборов НРК
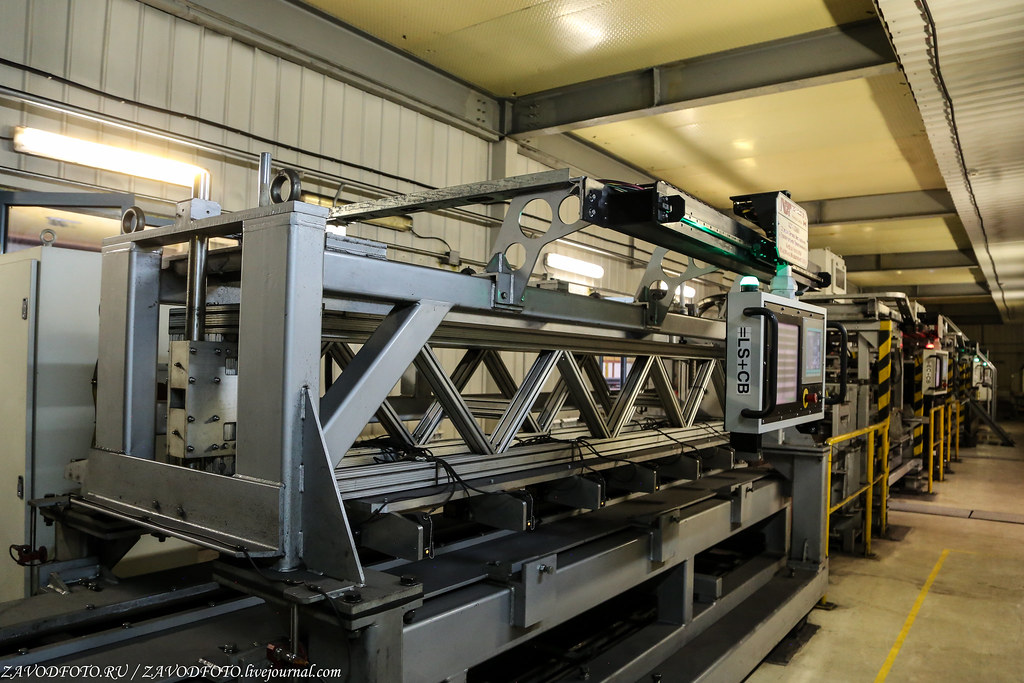
Все рельсы сканируется на прямолинейность, на наличие различных дефектов, а также сам размер профиля и качество самого металла.
23. прибор замера прямолинейности НРК
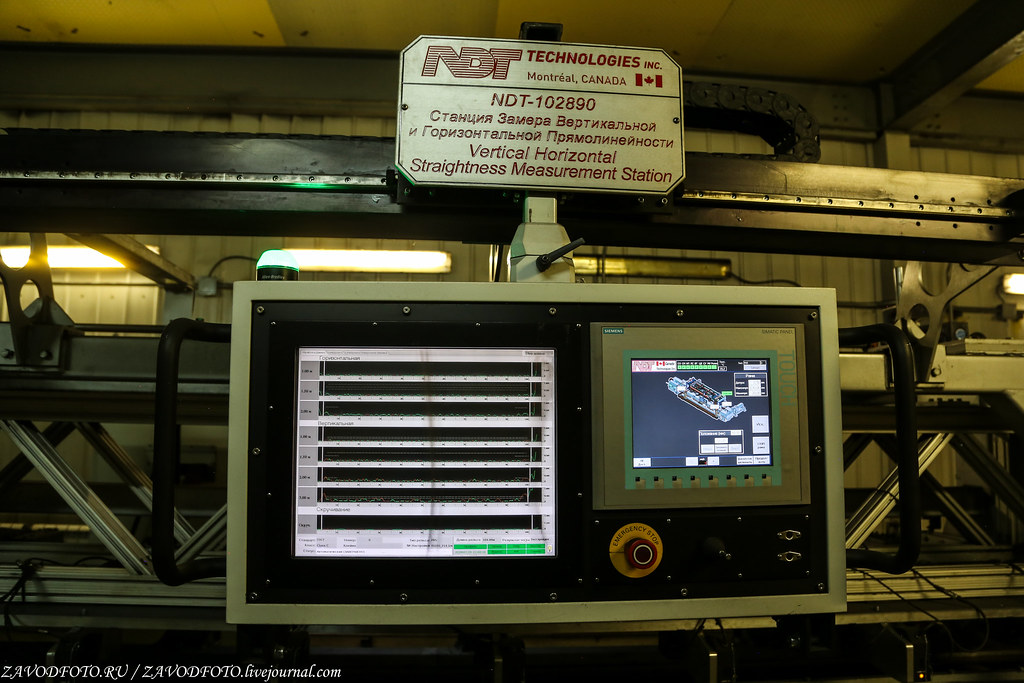
24.
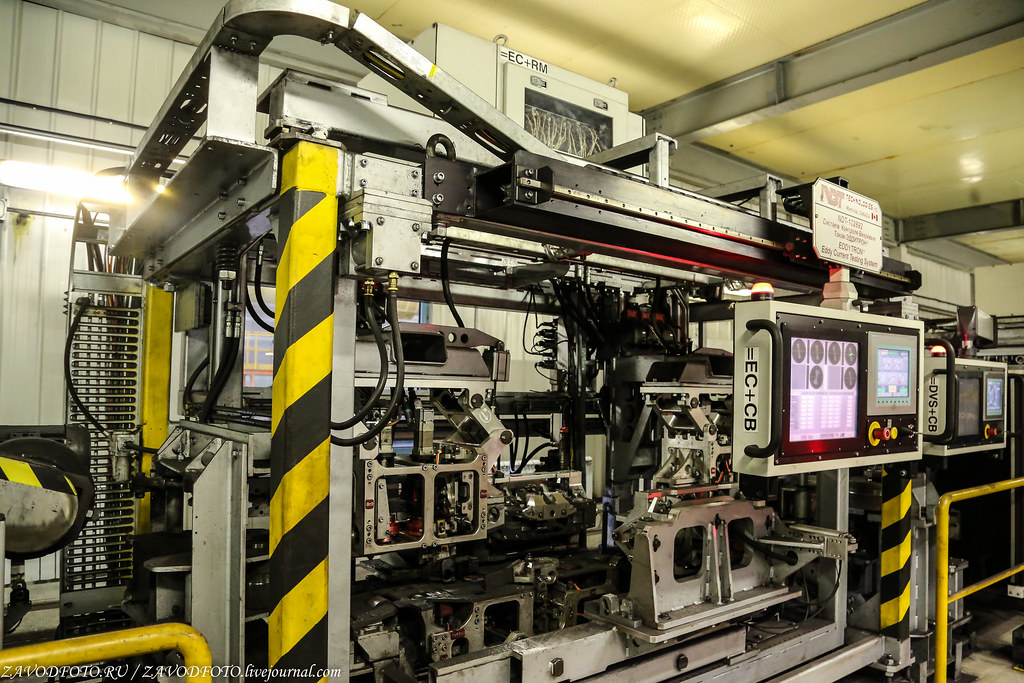
25. Кстати, рельсы ЧМК превосходят иностранные аналоги по ряду важных показателей, например, низкотемпературной надежности, повышенной износостойкости и контактной выносливости.
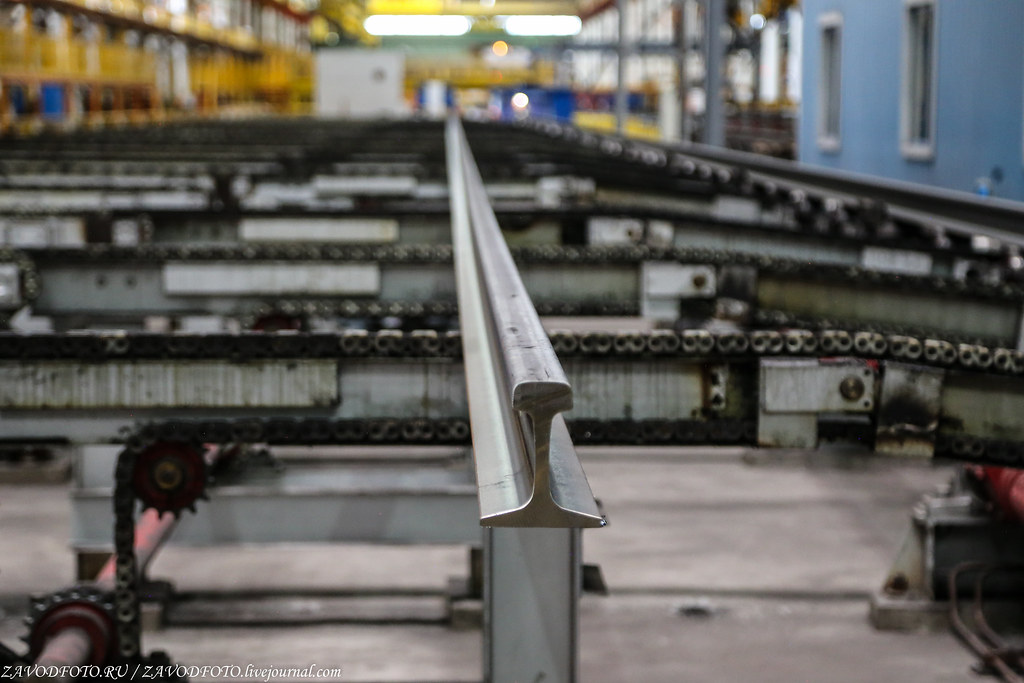
26. А ещё меня удивили вот такие краны, я ещё нигде таких не видел. Поразительно, как одним машинистом с помощью джойстиков, бесшумно приводится в движение громадная машина длиной 100 метров и весом в 400 легковых автомобилей.

27. Отгрузка рельсов клиентам осуществляется, как ж/д транспортом, так и автомобильным.

Дальнейшая сварка 100-метровых рельсов в длинные 800-метровые плети происходит на другом предприятии - Челябинском рельсосварочном РСП-13, которое также расположено на промплощадке ЧМК, но в состав Группы «Мечел» не входит. Ладно, про них вкратце тоже расскажу, хоть пока туда я и не попал. Челябинское РСП-13 - это одно из крупнейших рельсосварочных предприятий в мире. Его производственная мощность составляет около 450 тыс. тонн бесстыкового пути в год. После сварки готовые 800-метровые плети отправляются уже непосредственно к месту укладки скоростных и высокоскоростных железнодорожных магистралей. Их везут к месту укладки в таком же длинном 800-метровом железнодорожном составе – при транспортировке плети, несмотря на стальной характер, достаточно гибкие и не ломаются. Данная длина позволяет при укладке избежать большого количества сварных стыков, благодаря чему путь становится «бархатным» и бесшумным.
28.
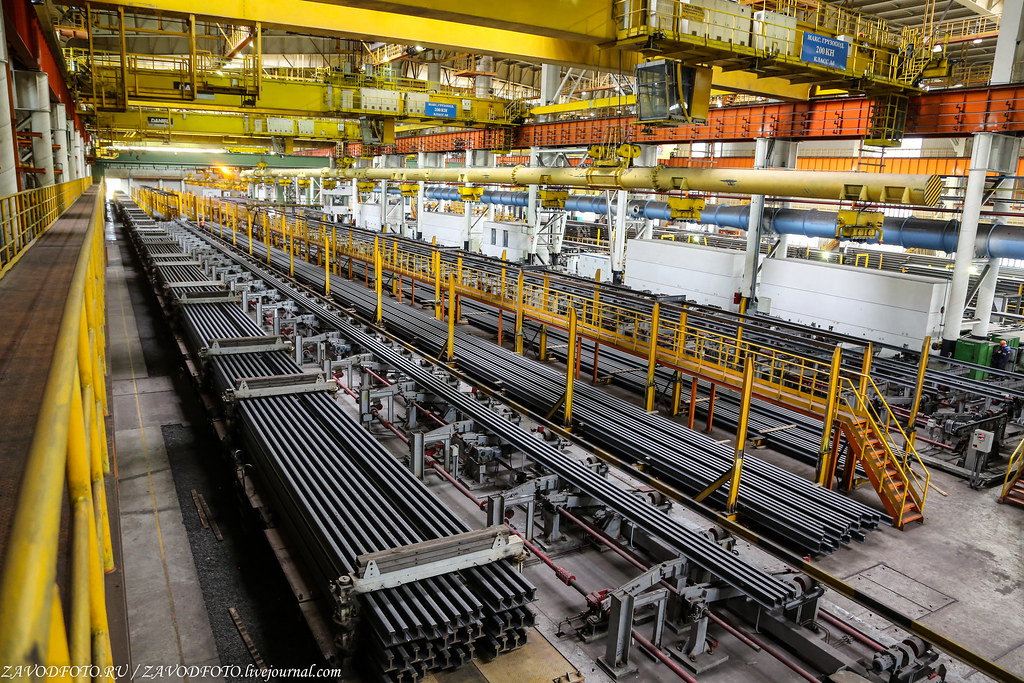
На российском рынке рельсы ЧМК с успехом заменили и превзошли импортные аналоги. Когда я своими глазами вижу такое мощное, действующее производство, упакованное лучшим в мире оборудованием, да помноженное на отечественные знания и экспертность, плюс к этому молодых амбициозных ребят, которые здесь трудятся, я с уверенностью могу сказать, что у нашей металлургии, да и у страны в целом, точно есть большое будущее.
29.
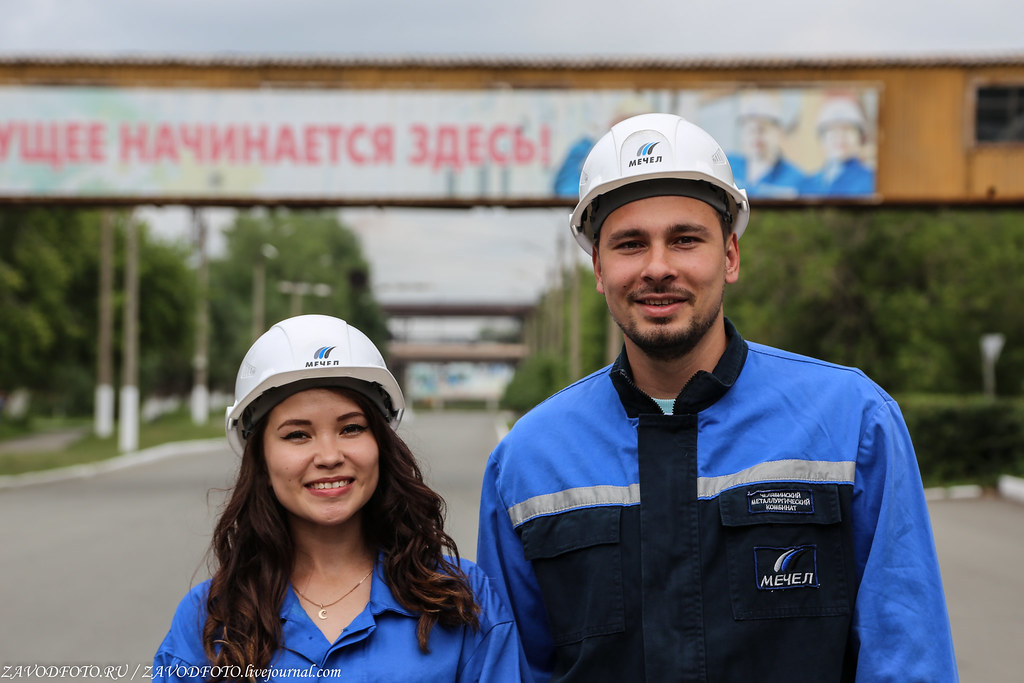
30. Большое спасибо всей пресс-службе ПАО «Мечел» за организацию такой интересной и познавательной поездки!
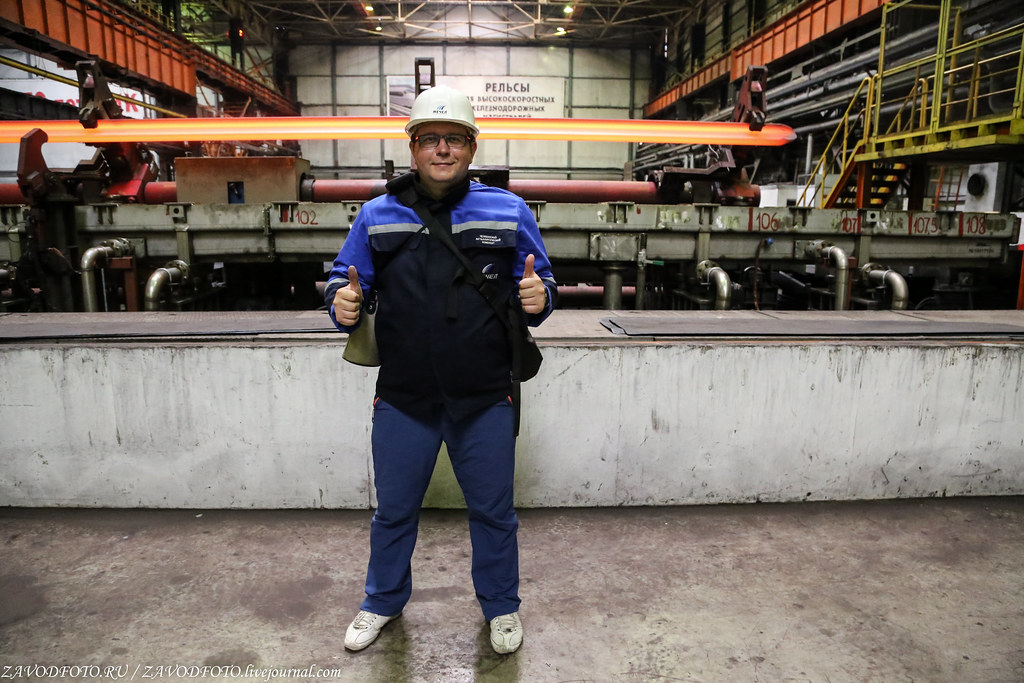
Р. S. Уважаемые собственники и акционеры, представители пресс-служб компаний, отделы маркетинга и другие заинтересованные лица, если на Вашем предприятие есть, что показать - "Как это делается и почему именно так!", мы всегда рады принять участие. Не стесняйтесь, пишите нам сами akciirosta@yandex.ru и расскажите о себе, пригласив нас к ВАМ в гости. Берите пример с лидеров!
Уже около 400 предприятий открыли перед нами свои двери, а вот и мои репортажи оттуда:
Почему наша промышленность самая лучшая в мире: http://zavodfoto.livejournal.com/4701859.html
Мы всегда рады новым друзьям, добавляйтесь и читайте нас в:

А ещё прошу всех в гости: http://ok.ru/zavodfoto и https://www.facebook.com/groups/ZAVODFOTO/
Взято: zavodfoto.livejournal.com
Комментарии (0)
{related-news}
[/related-news]