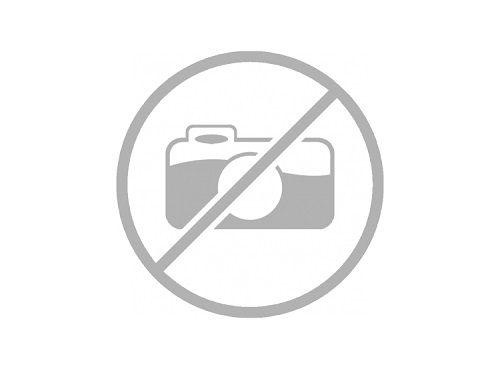
Предприятие "АэроКомпозит" в Ульяновске
---
Оригинал взят у коллеги
russos в АэроКомпозит в Ульяновске
При разработке перспективного отечественного среднемагистрального лайнера МС-21 Объединенная авиастроительная корпорация (ПАО «ОАК») сделала выбор в пользу создания совершенного аэродинамического крыла из полимерных композиционных материалов (ПКМ). К его разработке и созданию в 2008 году приступила компания «АэроКомпозит», ставшая первым Центром компетенций ПАО «ОАК» в сфере инновационных разработок и производства элементов конструкций воздушных судов из ПКМ. Ульяновская производственная площадка стала первым заводом в мире, где используется инфузионная технология при изготовлении силовых длинномерных элементов консоли крыла самолета.
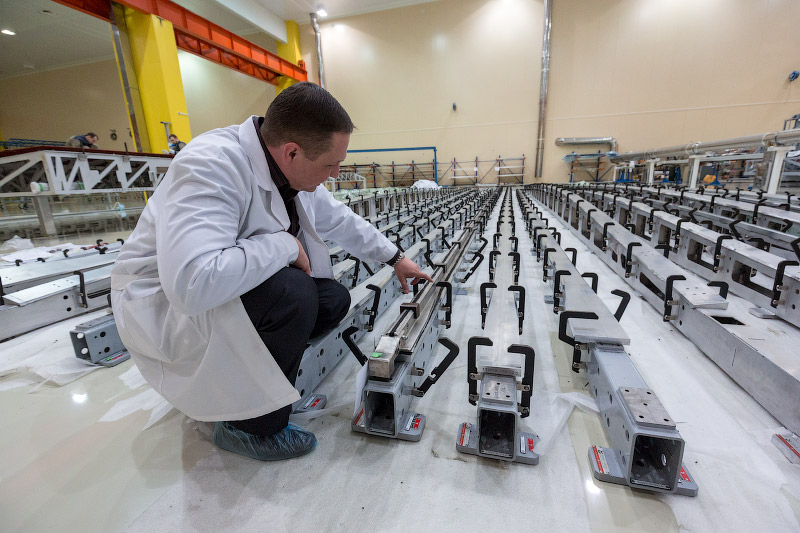
Для описания процесса в двух словах воспользуюсь выдержкой из статьи «Самолет МС-21 поставят на черное крыло» журнала «Умное производство».
Принципиальное отличие метода вакуумной инфузии от традиционной автоклавной технологии — он предполагает работу с сухим материалом. Сухой материал — шестимиллиметровая лента из углеволокна с тонким клеевым покрытием для фиксации. В помещении «чистая комната» на участке автоматической выкладки робот наносит на оснастку по всей длине конструкции слои лент под разными углами. Внедрение роботизированных установок на заводе «АэроКомпозит-Ульяновск» позволяет значительно увеличить производительность. Сначала выполняется так называемая позитивная (выкладочная) оснастка, а на следующем участке деталь ждет негативная оснастка — для инфузии.
Далее деталь перемещается на другой участок, где происходит позиционирование стрингеров, их установка на панель кессона крыла — завершающий этап формирования преформы. Затем на преформу устанавливается вакуумный мешок, подключаются каналы для дальнейшего вакуумирования и подачи связующего. В специальном термоинфузионном центре связующее под давлением подается в заготовку. Именно здесь происходит процесс формования будущей композитной конструкции. На выходе композитный элемент представляет из себя монолит 18 метров в длину. При этом на всех участках обеспечен пооперационный контроль. На первых операциях — визуальный с применением ручных приборов, а когда деталь «испеклась», проводится предварительный неразрушающий контроль, после чего конструкция подается на участок механообработки. После механической обработки проводится финальный контроль при помощи роботизированной установки неразрушающего контроля, которая осуществляет сканирование элемента конструкции.
Если вы хотите немного прочитать про теорию и практику композитных материалов, то вам сюда — О материальном в авиации.
Фотографировать производство на этом заводе было очень сложно — очень много снимать было нельзя. Производство очень высокотехнологично и содержит много тонкостей процесса. По сути — это острие авиационной науки в современной истории. Но, вот что получилось. Часть фотографий предоставлена пресс-службой предприятия.
1. Предприятие развернуло свои мощности в неиспользуемых цехах Авиастара, которые были полностью перестроены для решения задач современного производства.
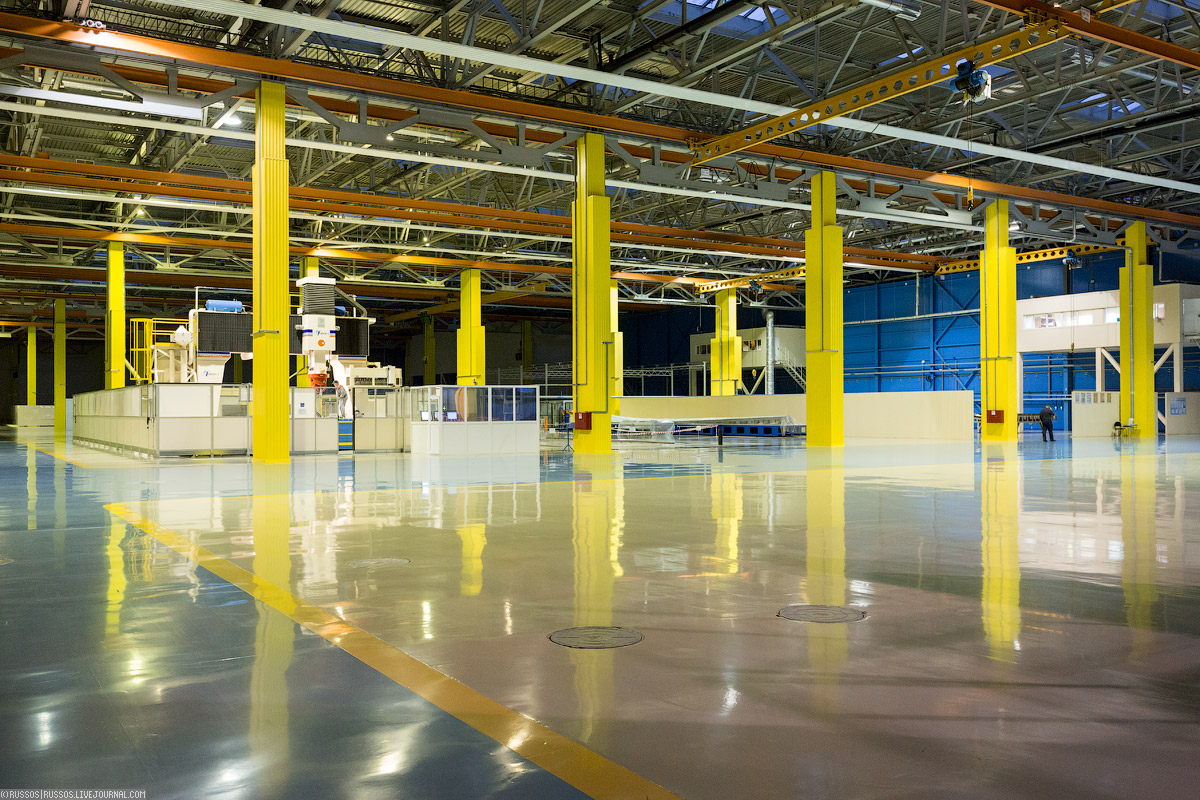
2. Участок автоматической выкладки. На переднем плане панель консоли крыла, на заднем — лонжерон.
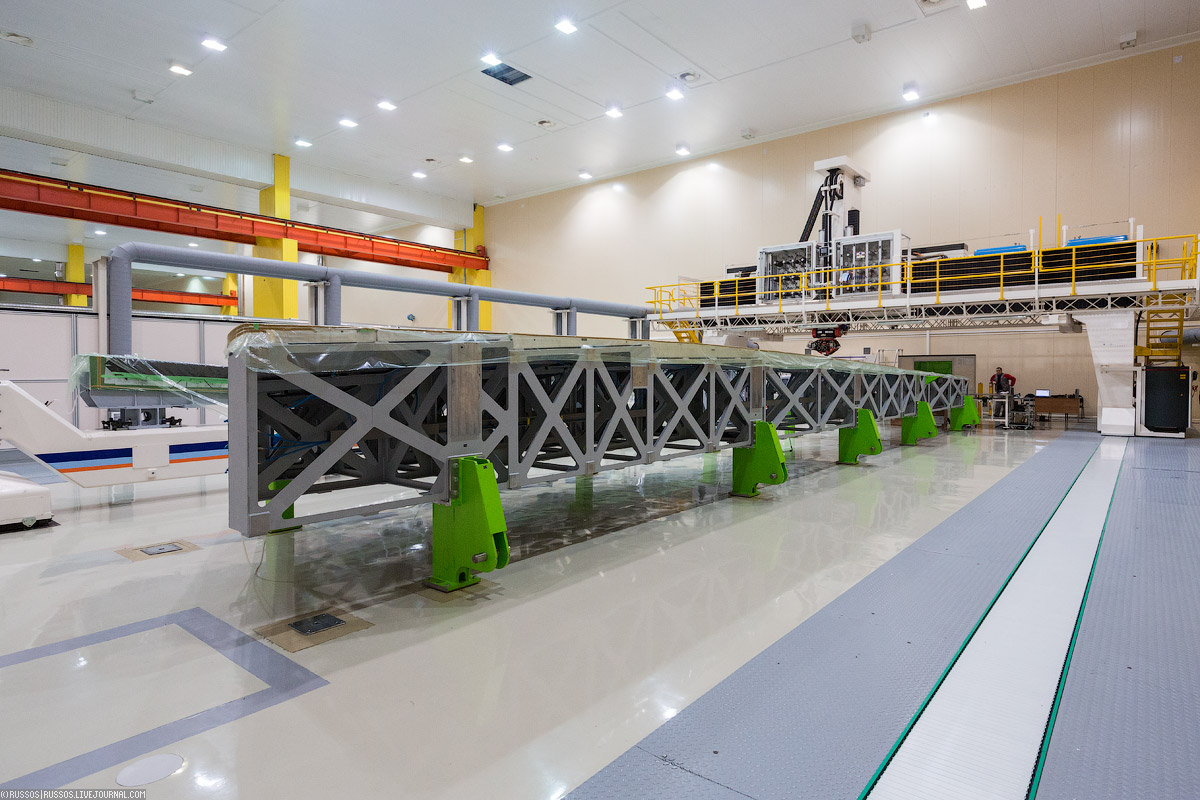
3. Выкладка лонжерона крыла шестимиллиметровой углеродной лентой.
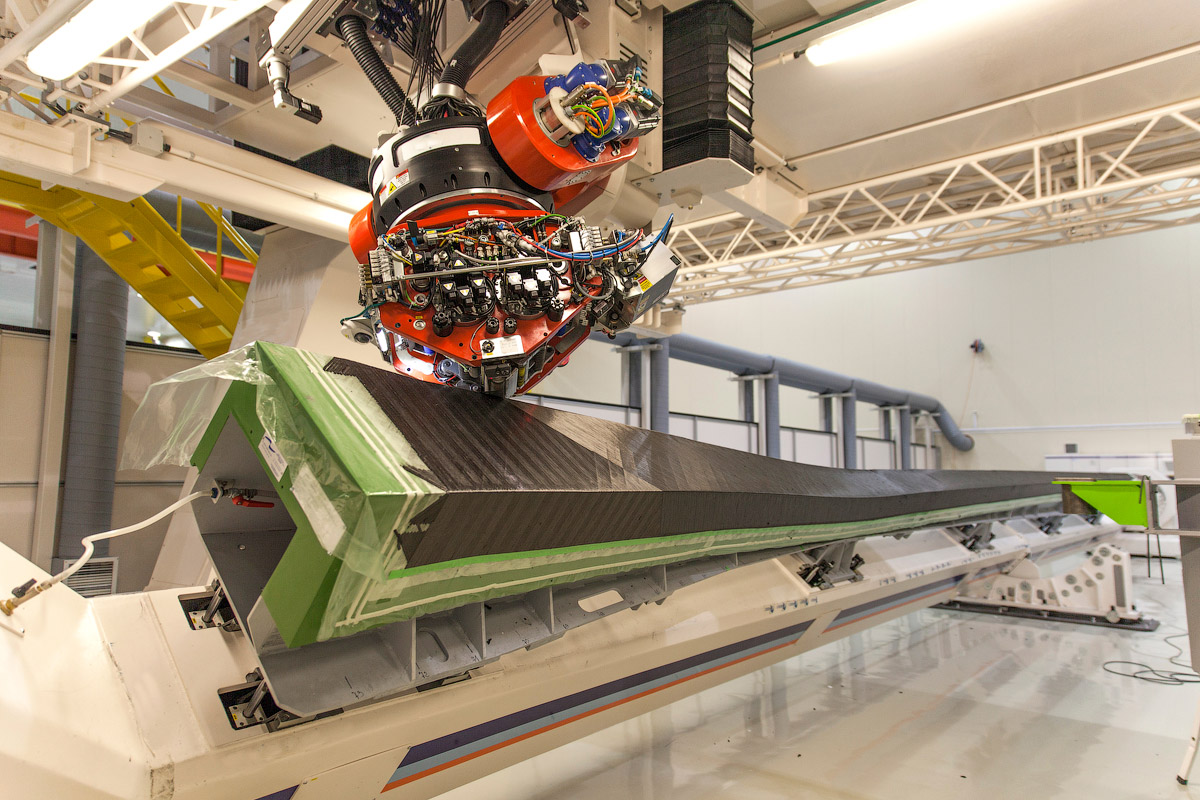
(с) фото пресс-службы АэроКомпозита.
4. Выложенные первые два слоя панели-спутника. Вся работа по подготовке основных и технологических материалов, выкладка углеродной ленты, а также сборка вакуумного мешка, проводится в помещении с контролируемыми параметрами — в так называемой «чистой комнате». Специальная система кондиционирования обеспечивает здесь поддержание заданных нашей технологией параметров температуры и влажности воздуха, атмосферного давления. Здесь недопустимо, чтобы в воздухе витали даже мельчайшие дисперсные частицы. Чистота этого помещения площадью 11 тысяч квадратных метров вполне сопоставима с чистотой больничных операционных.
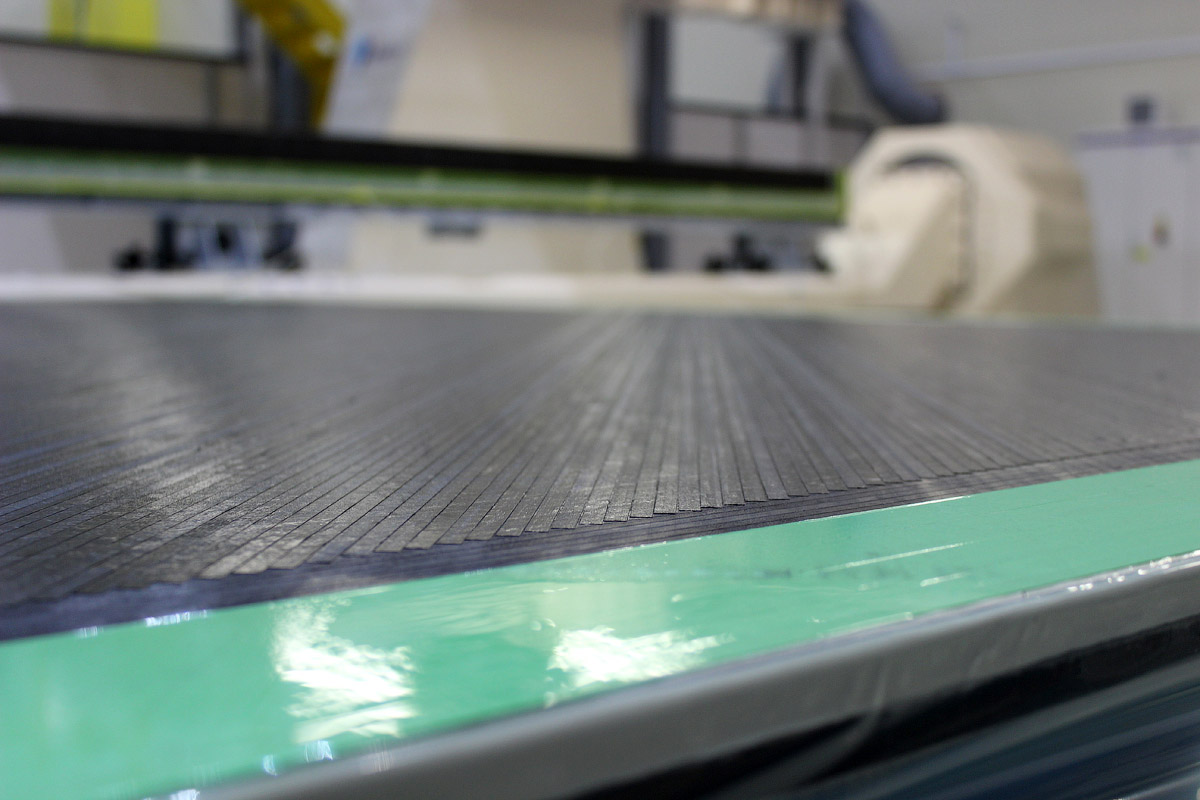
(с) фото пресс-службы АэроКомпозита.
5. Визуальный контроль выложенных слоев.

(с) фото пресс-службы АэроКомпозита.
6. Система перемещения преформ панелей консоли крыла (слева) и система переворота преформ лонжеронов (справа).
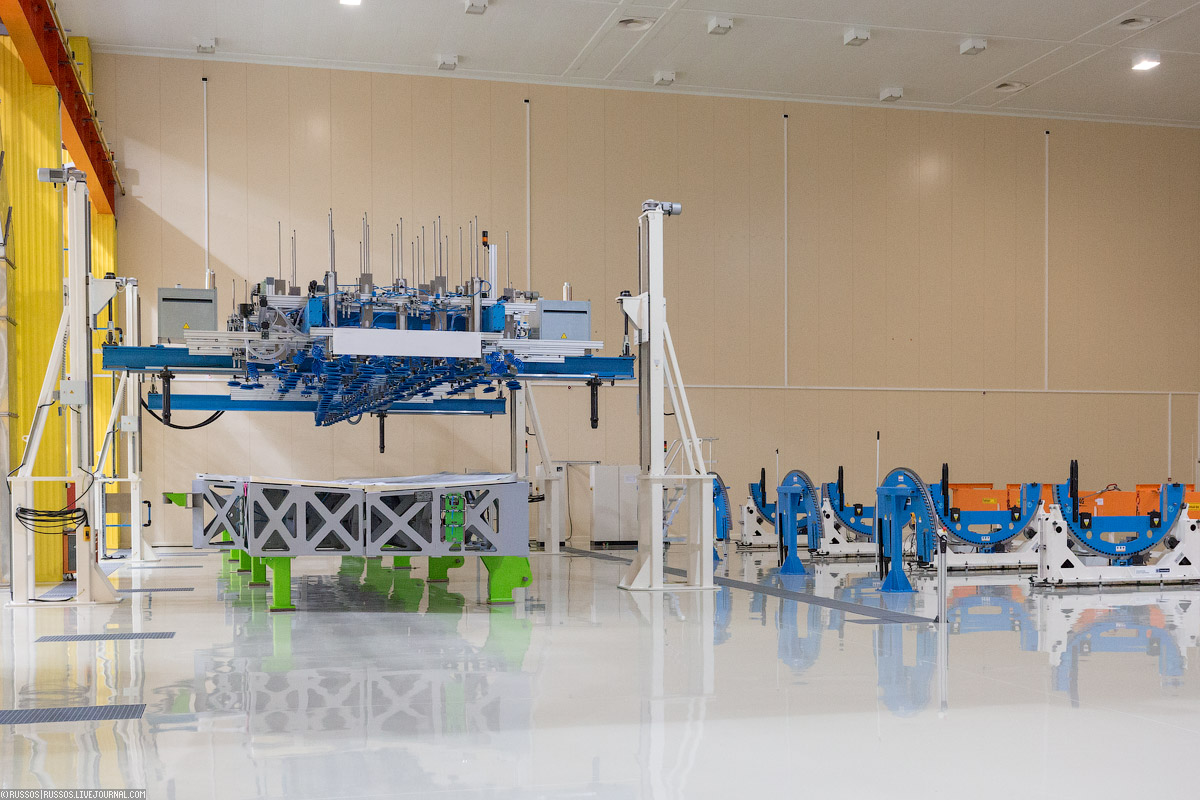
7. Присоски.
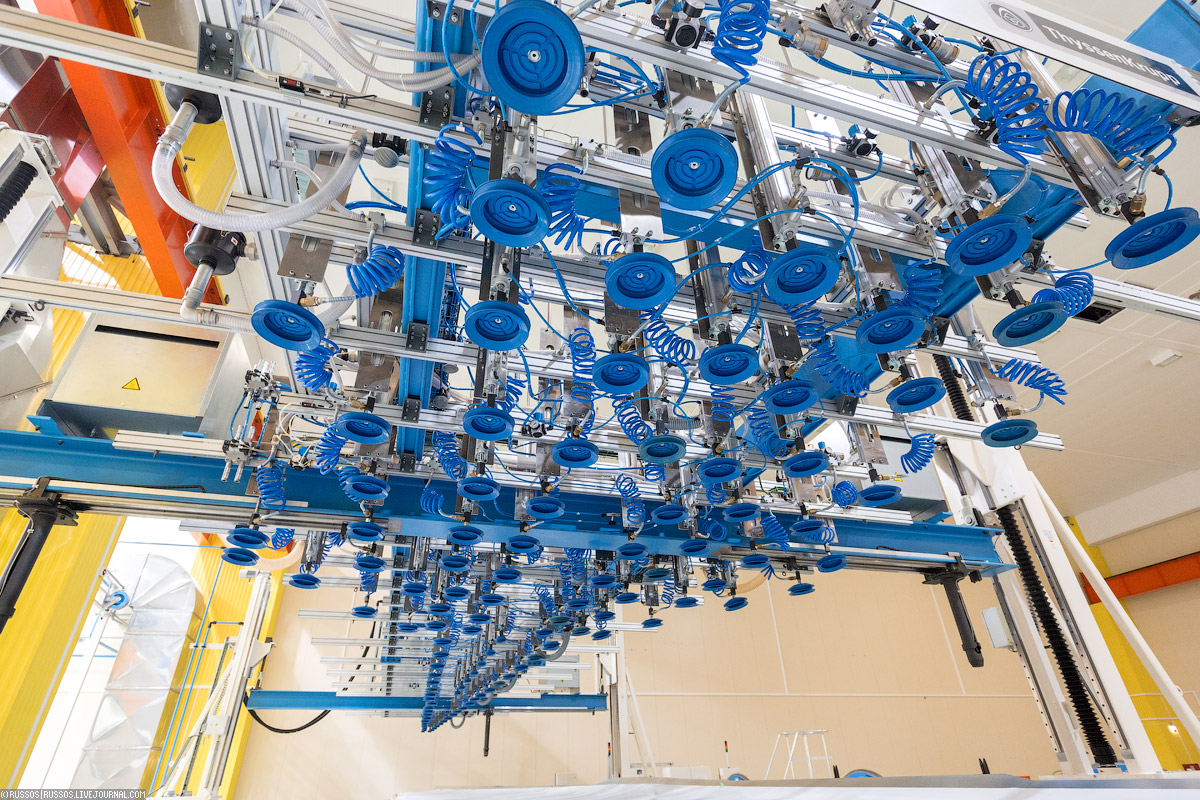
8. Полученная «П»-образная преформа разрезается. Получается два «Г»-образных профиля, которые складываются в «Т»-образный. На фотографии стрингер установлен в проектное положение, зафиксирован в стапеле и в таком виде монтируется на обшивку панели консоли крыла.
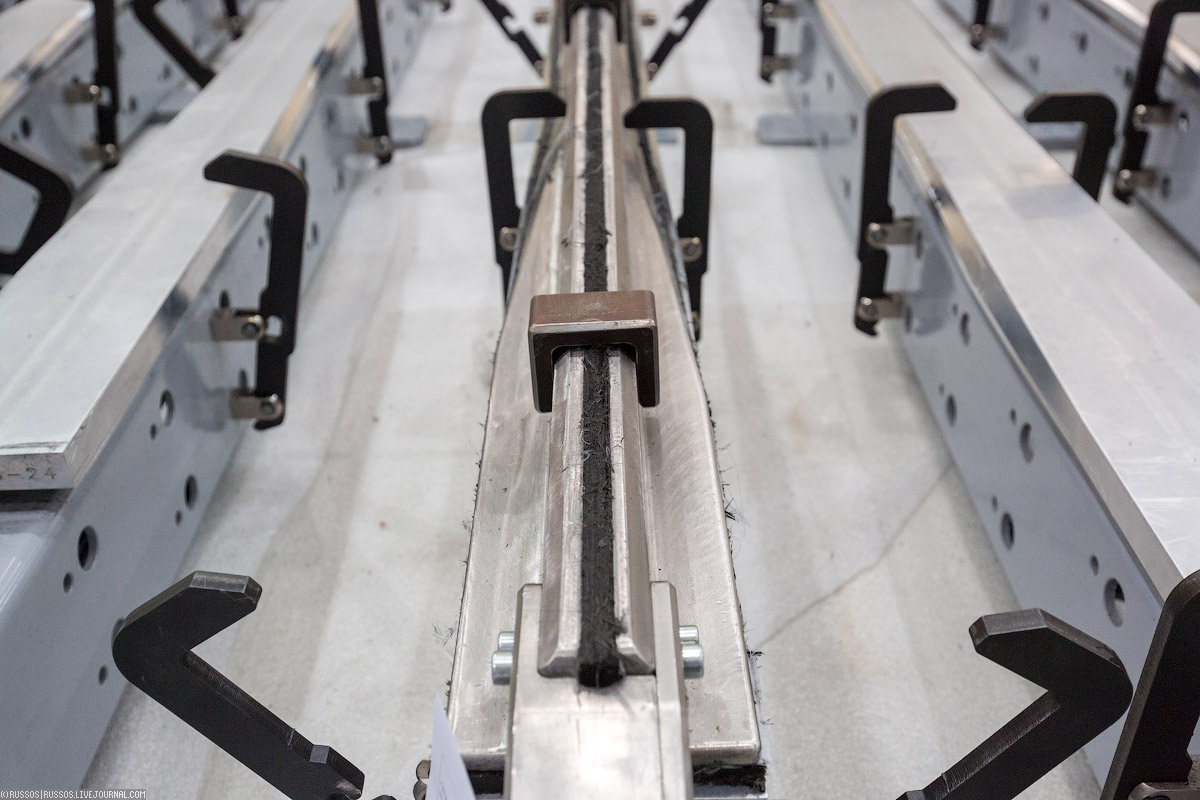
9. Участок выкладки на панель консоли крыла подготовленных стрингеров.
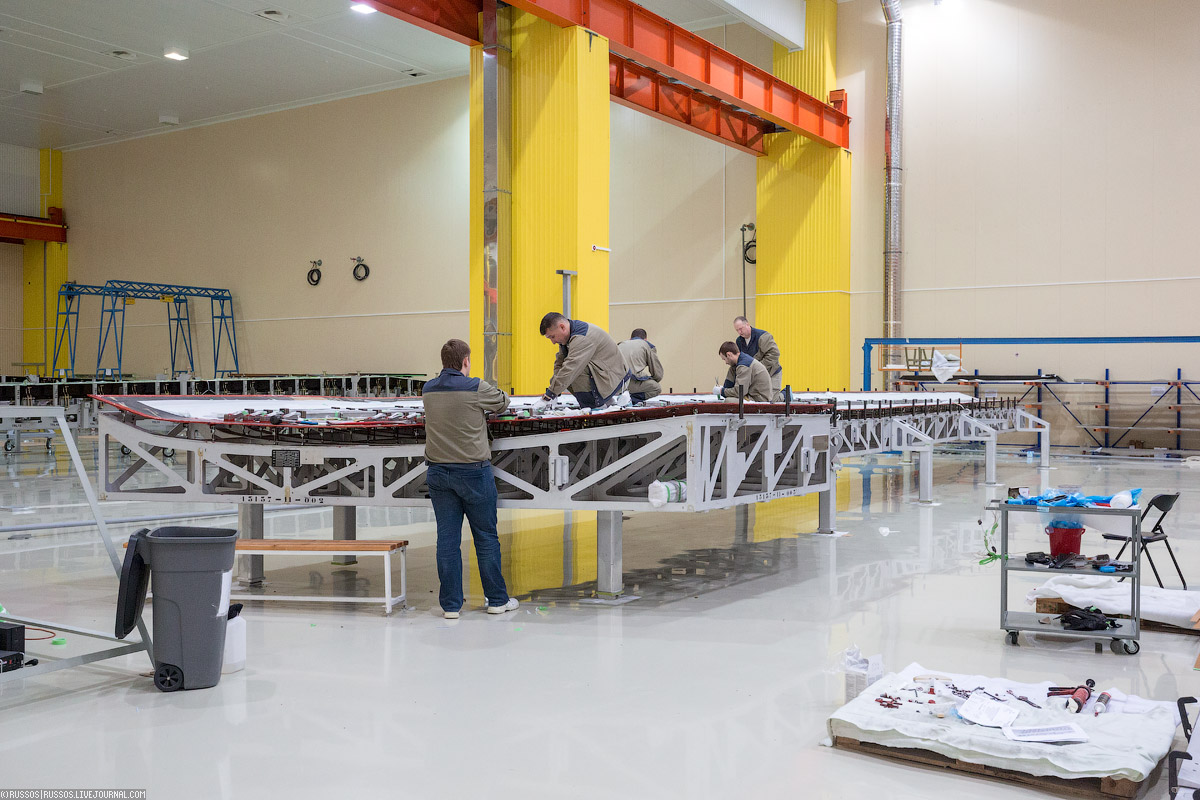
10. Термоинфузионный центр. Формуется все при небольших температурах. Одновременно можно изготавливать несколько изделий. Совместно с длинномерными элементами «поджариваются» и панели-спутники, так называемая, «уменьшенная копия», которая проходит все этапы изготовления параллельно с основным изделием. Спутник предназначен для того, чтобы провести на нем все испытания по контролю качества основного изделия. Так как спутник изготавливается вкупе с самой деталью, в аналогичных условиях и по абсолютно точным параметрам, он является аналогом этой детали. Затем панель-спутник отправляется в испытательную лабораторию, где из нее нарезают около 600 образцов-свидетелей, каждый из которых проверят «на прочность». Специалисты проведут испытания на разрыв, на сжатие и на сдвиг.
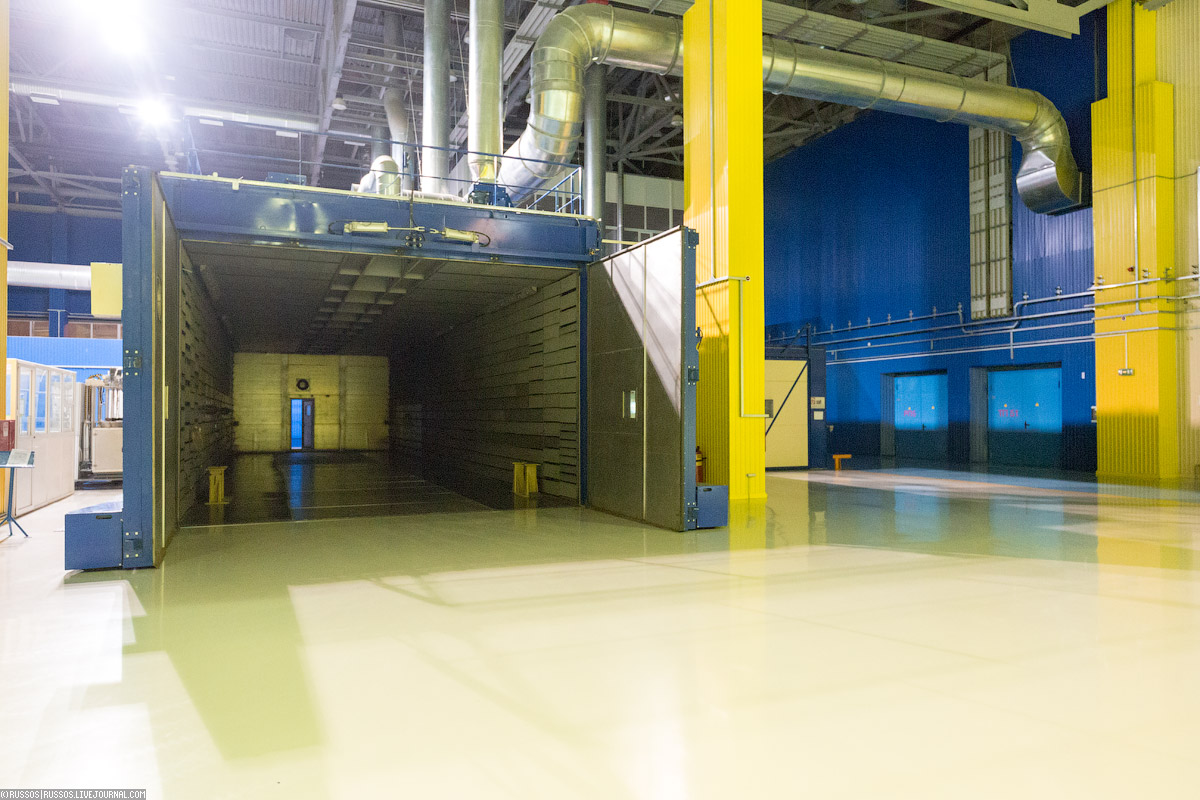
11. На снимке монолитные элементы после выхода из термоинфузионного центра. Слева — панель консоли крыла. Справа — панель центроплана.
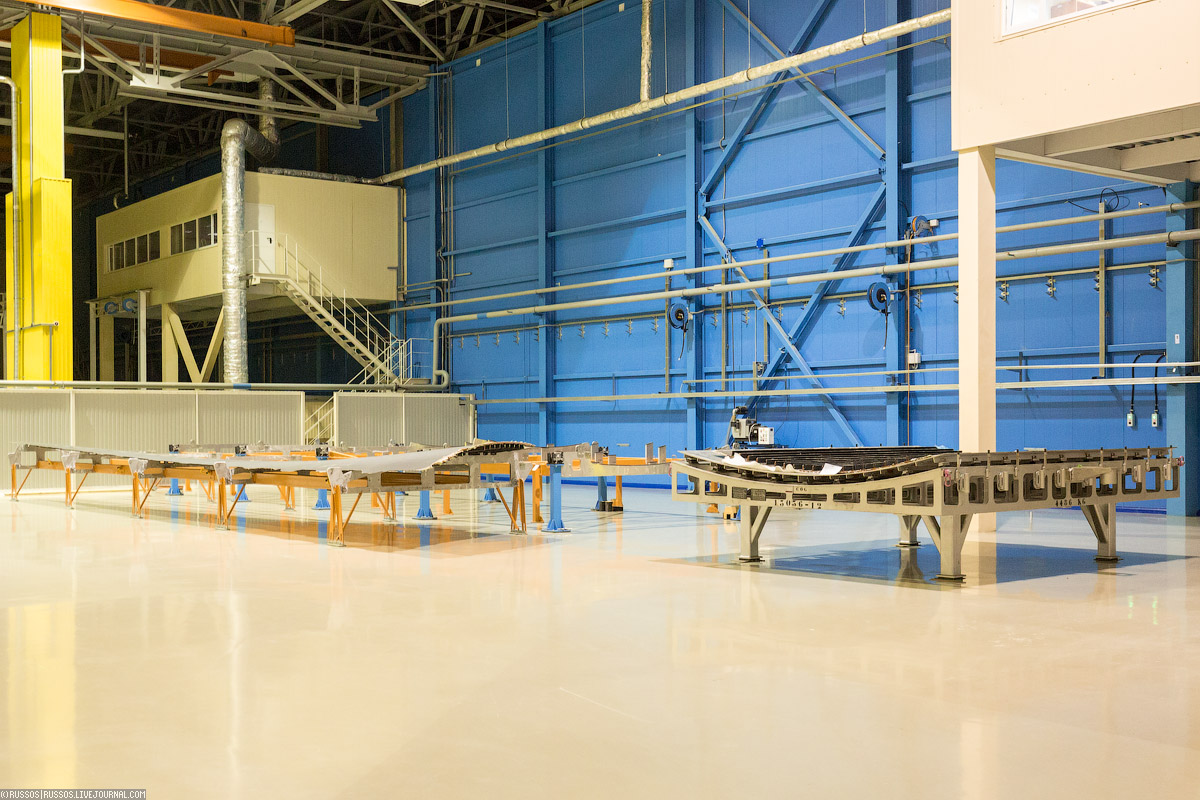
12. Заместитель начальника композитного производства Павел Дягилев рассказывает об особенностях технологического процесса. Рядом с ним — композитная панель консоли крыла самолета перед механической обработкой. Это длинномерный монолит.
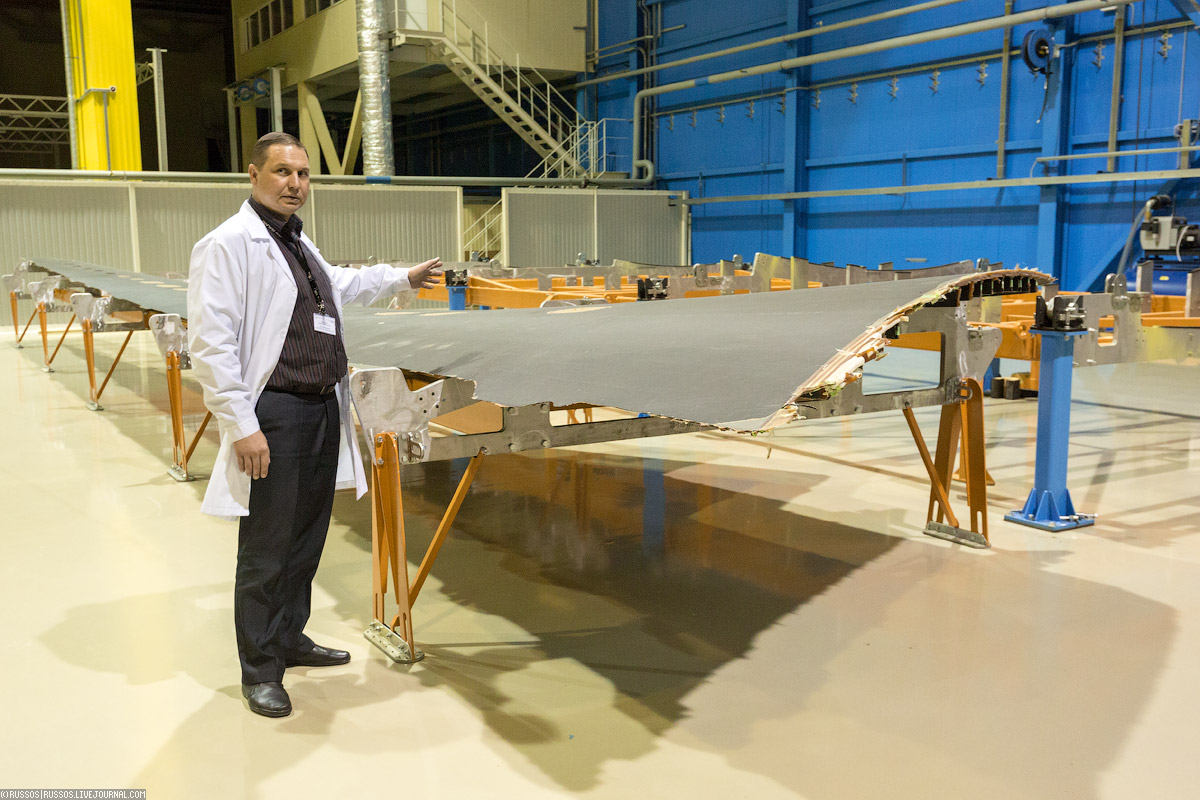
13. Пятикоординатный фрезерный центр позволяет выполнять механическую обработку как мелких, так и крупногабаритных изделий (18 метров в длину) сложной геометрии.
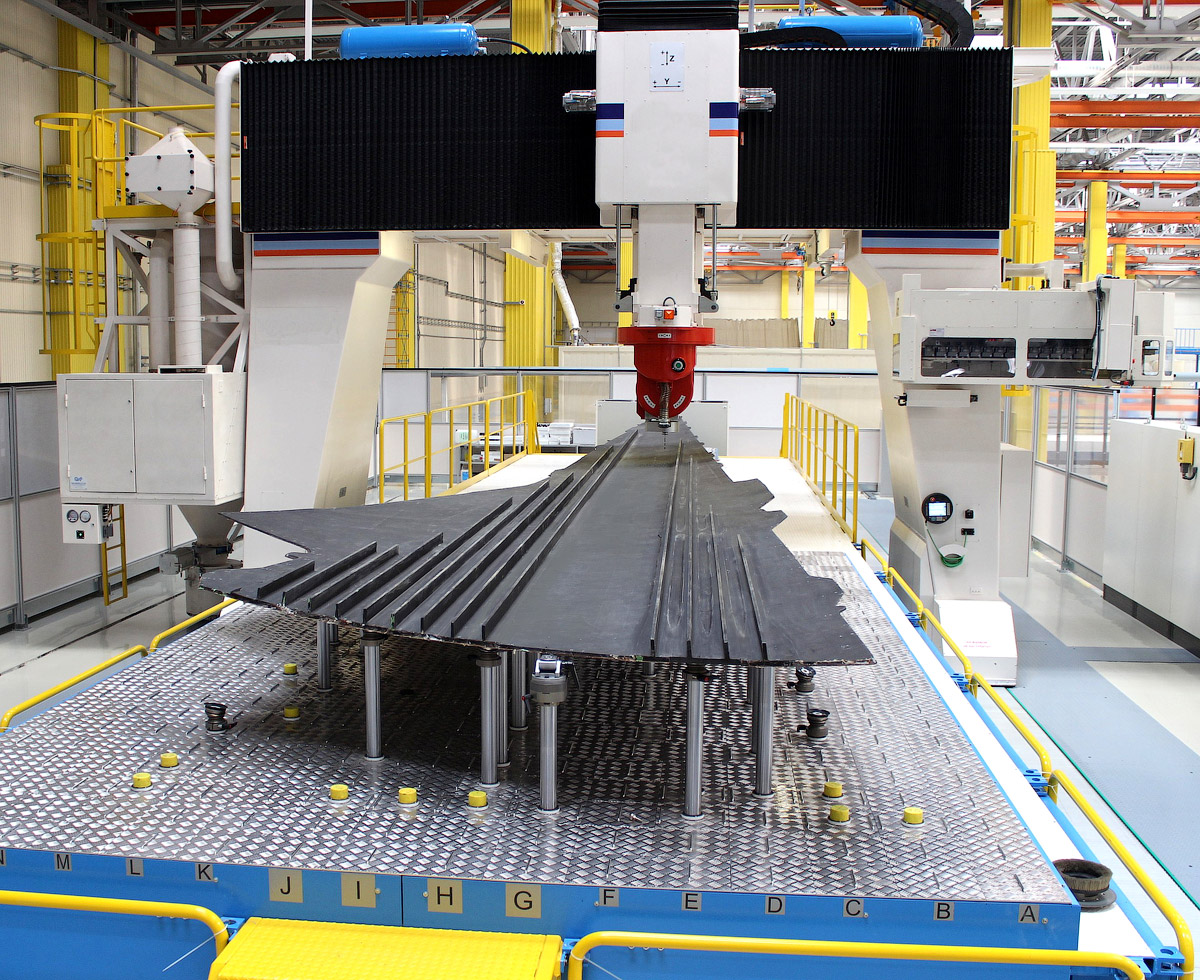
(с) фото пресс-службы АэроКомпозита.
14. Верхняя панель консоли крыла и лонжерон на участке проведения неразрушающего контроля.
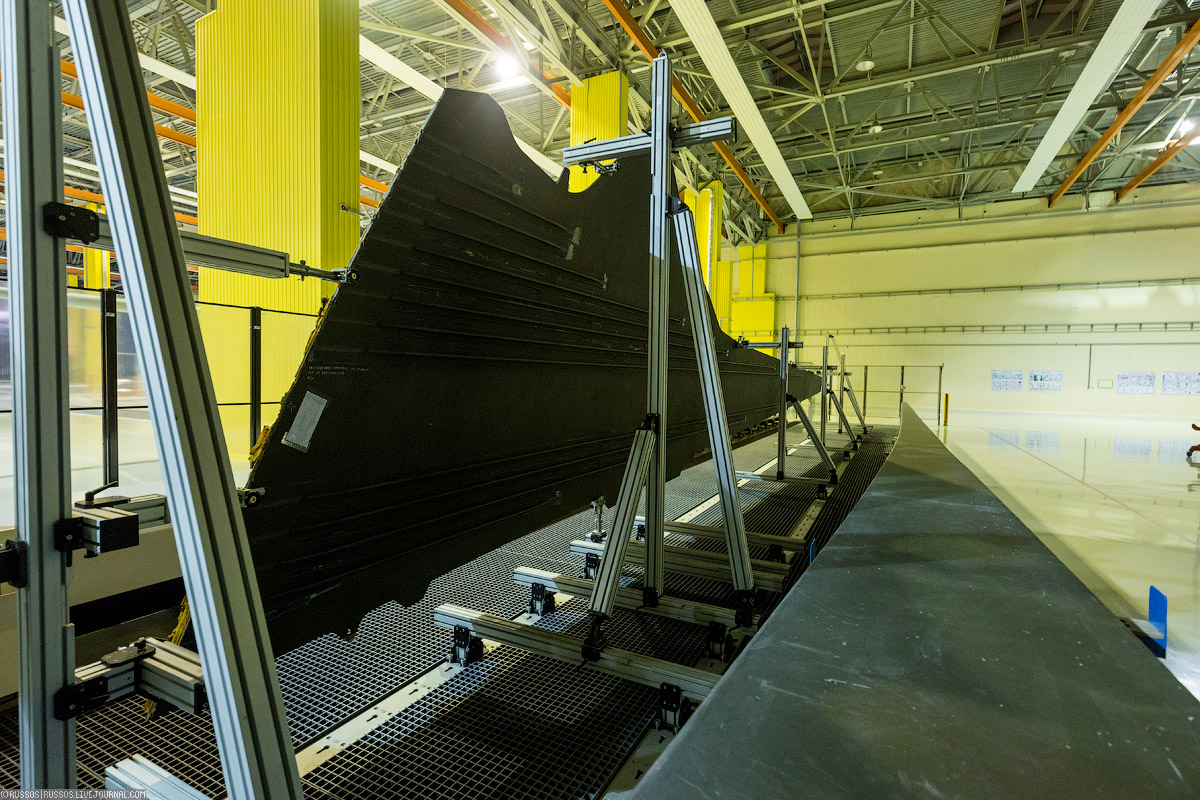
15. Ультразвуковое исследование лонжерона крыла.
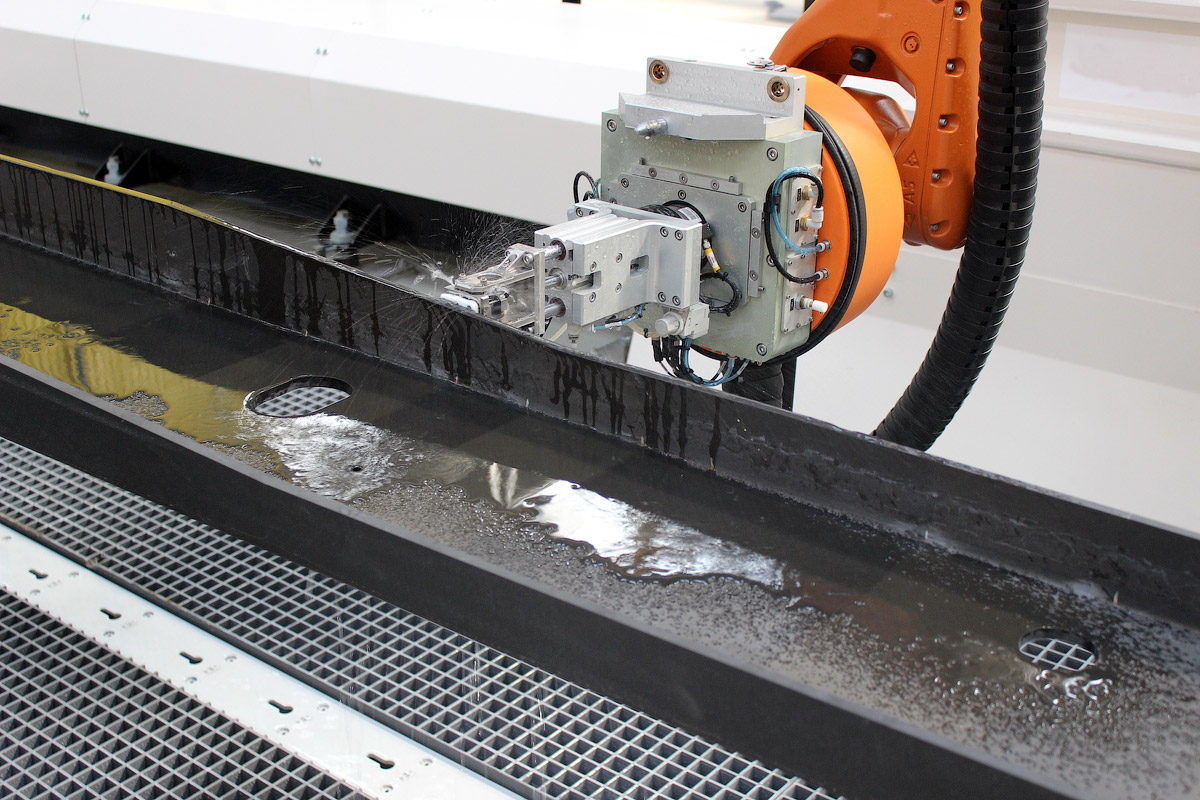
(с) фото пресс-службы АэроКомпозита.
16. К сожалению, когда я там был, готовые консоли крыла были уже доставлены на Иркутский авиационный завод, где полным ходом идет сборка первого самолета МС-21. Но сборочный участок и станции впечатляют.
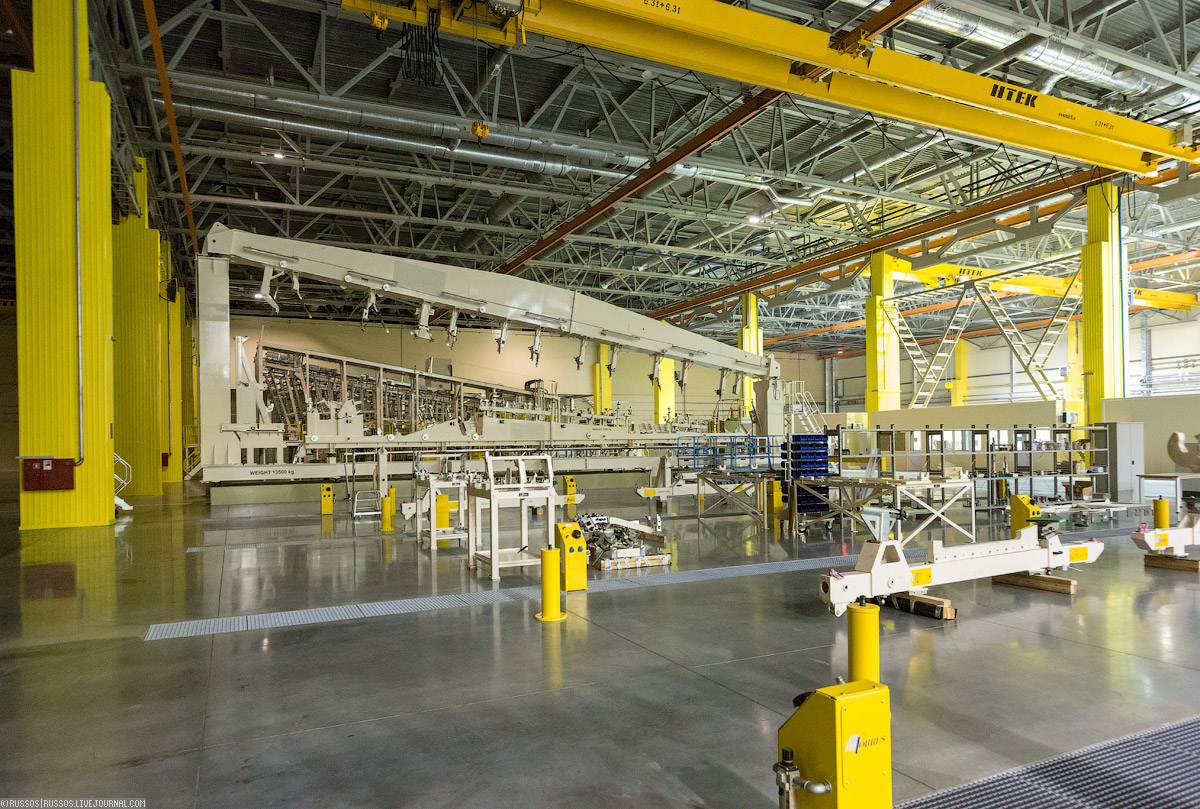
17. Две панели центроплана на сборочной станции.
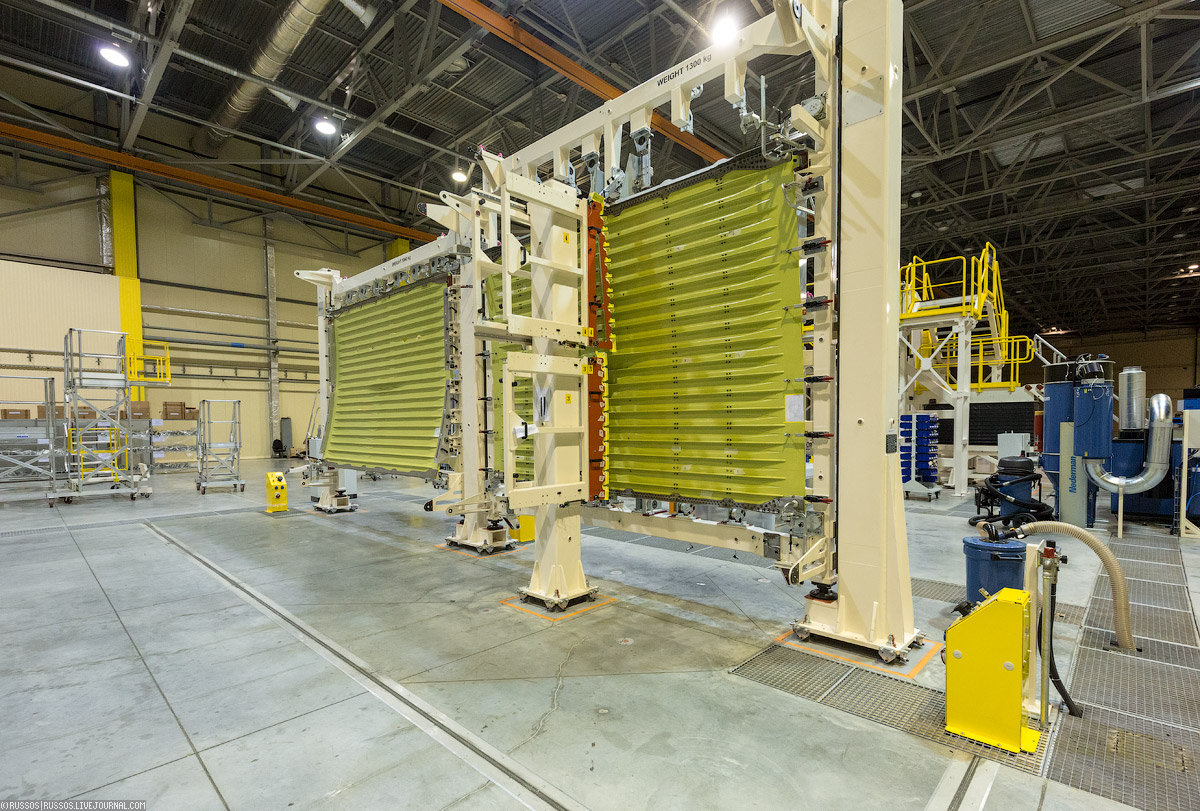
18. Установка компенсаторов нервюр. Они соединяют обшивку с нервюрами и позволяют обеспечить заданную форму профиля поверхности.
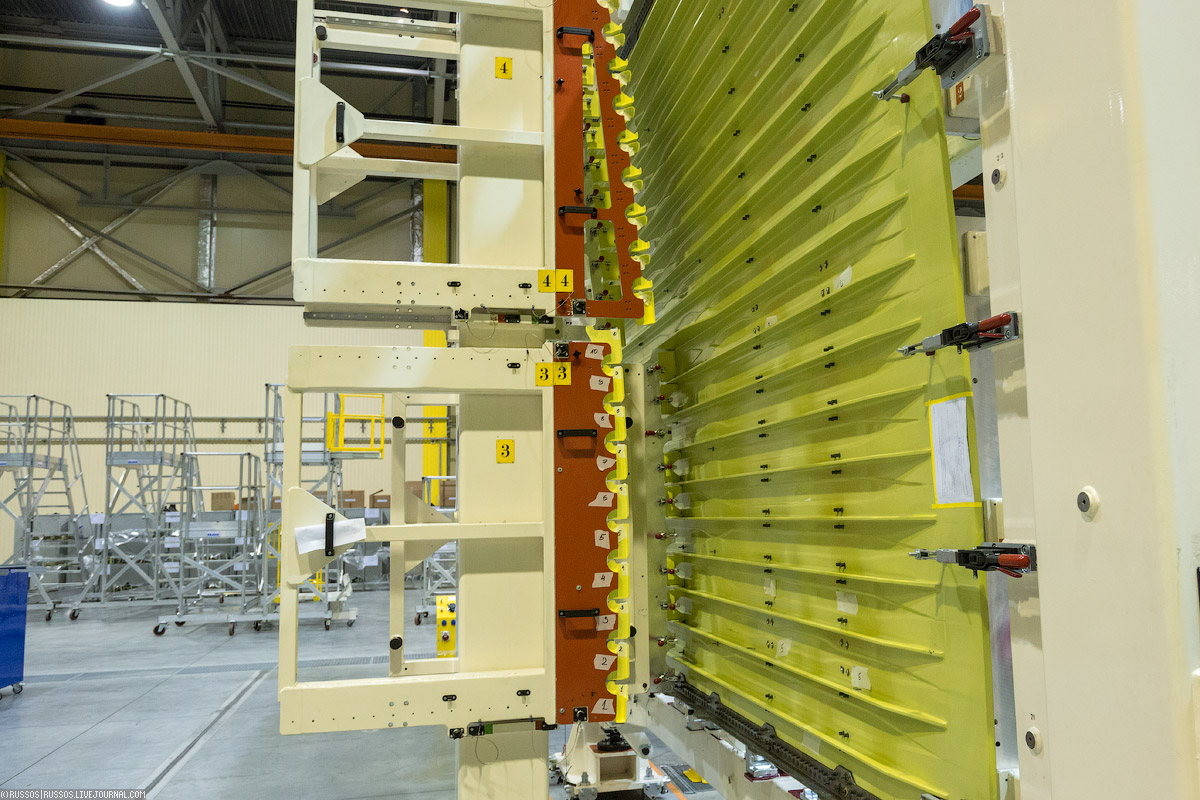
19. На предприятии готовятся к установке стенда для предварительной стыковки консолей крыла лайнера с центропланом.
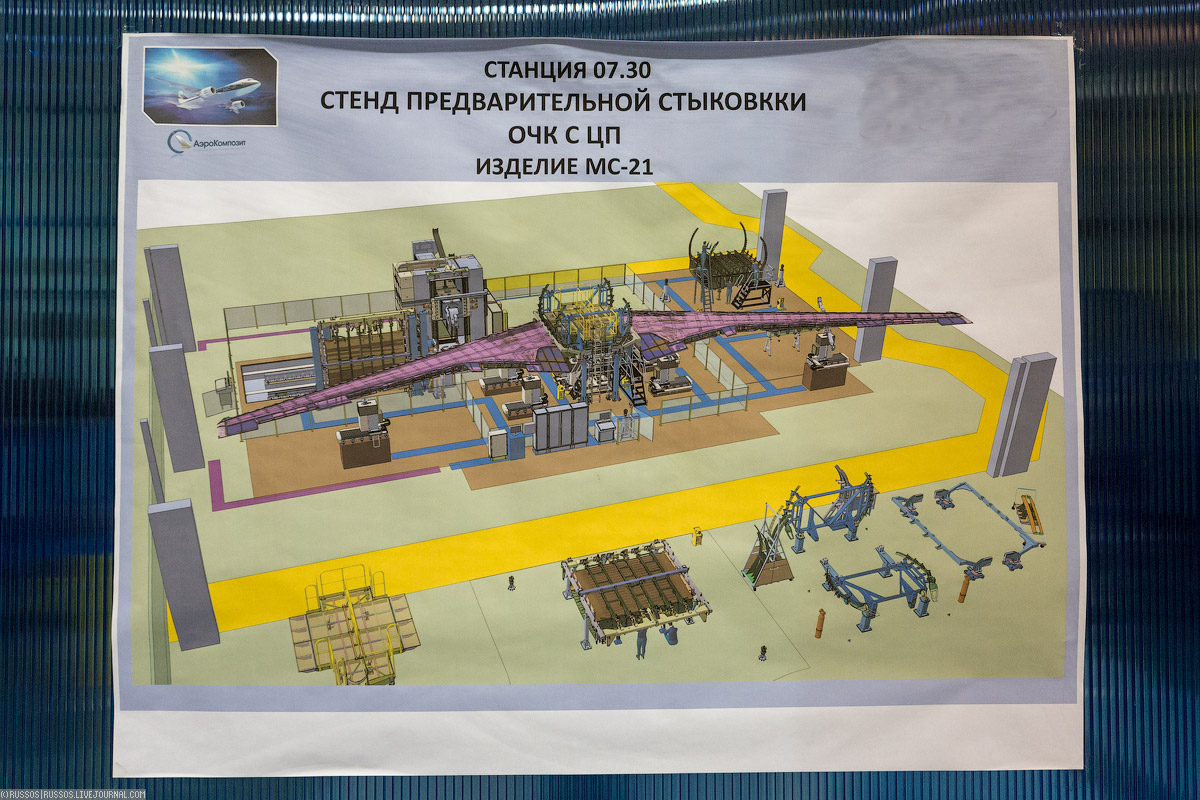
20. Рядом собирают предкрылки консоли крыла.
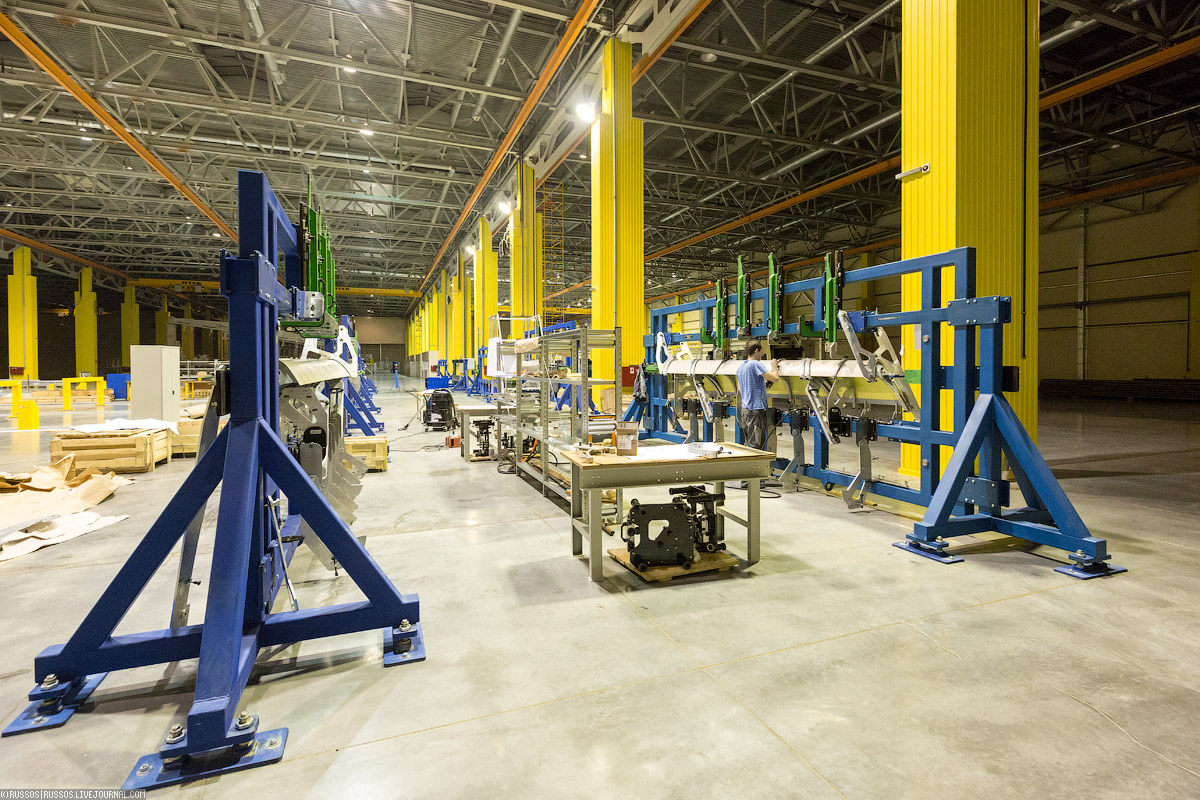
Друзья, первый полет МС-21 уже почти реальность. Он должен состоятся уже в этом году. Да даже, если в следующем — это будет грандиозное событие в отечественном авиастроении.
Огромное спасибо сотрудникам компании «АэроКомпозит» за помощь в подготовке материала.

При разработке перспективного отечественного среднемагистрального лайнера МС-21 Объединенная авиастроительная корпорация (ПАО «ОАК») сделала выбор в пользу создания совершенного аэродинамического крыла из полимерных композиционных материалов (ПКМ). К его разработке и созданию в 2008 году приступила компания «АэроКомпозит», ставшая первым Центром компетенций ПАО «ОАК» в сфере инновационных разработок и производства элементов конструкций воздушных судов из ПКМ. Ульяновская производственная площадка стала первым заводом в мире, где используется инфузионная технология при изготовлении силовых длинномерных элементов консоли крыла самолета.
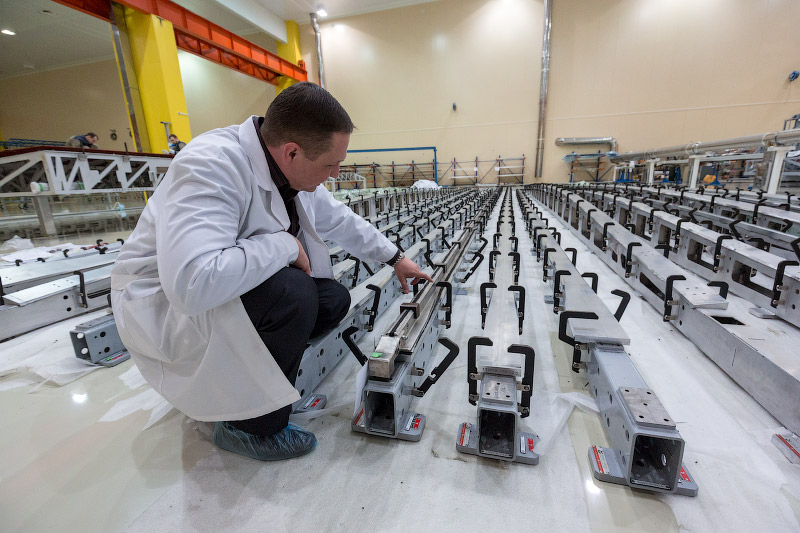
Для описания процесса в двух словах воспользуюсь выдержкой из статьи «Самолет МС-21 поставят на черное крыло» журнала «Умное производство».
Принципиальное отличие метода вакуумной инфузии от традиционной автоклавной технологии — он предполагает работу с сухим материалом. Сухой материал — шестимиллиметровая лента из углеволокна с тонким клеевым покрытием для фиксации. В помещении «чистая комната» на участке автоматической выкладки робот наносит на оснастку по всей длине конструкции слои лент под разными углами. Внедрение роботизированных установок на заводе «АэроКомпозит-Ульяновск» позволяет значительно увеличить производительность. Сначала выполняется так называемая позитивная (выкладочная) оснастка, а на следующем участке деталь ждет негативная оснастка — для инфузии.
Далее деталь перемещается на другой участок, где происходит позиционирование стрингеров, их установка на панель кессона крыла — завершающий этап формирования преформы. Затем на преформу устанавливается вакуумный мешок, подключаются каналы для дальнейшего вакуумирования и подачи связующего. В специальном термоинфузионном центре связующее под давлением подается в заготовку. Именно здесь происходит процесс формования будущей композитной конструкции. На выходе композитный элемент представляет из себя монолит 18 метров в длину. При этом на всех участках обеспечен пооперационный контроль. На первых операциях — визуальный с применением ручных приборов, а когда деталь «испеклась», проводится предварительный неразрушающий контроль, после чего конструкция подается на участок механообработки. После механической обработки проводится финальный контроль при помощи роботизированной установки неразрушающего контроля, которая осуществляет сканирование элемента конструкции.
Если вы хотите немного прочитать про теорию и практику композитных материалов, то вам сюда — О материальном в авиации.
Фотографировать производство на этом заводе было очень сложно — очень много снимать было нельзя. Производство очень высокотехнологично и содержит много тонкостей процесса. По сути — это острие авиационной науки в современной истории. Но, вот что получилось. Часть фотографий предоставлена пресс-службой предприятия.
1. Предприятие развернуло свои мощности в неиспользуемых цехах Авиастара, которые были полностью перестроены для решения задач современного производства.
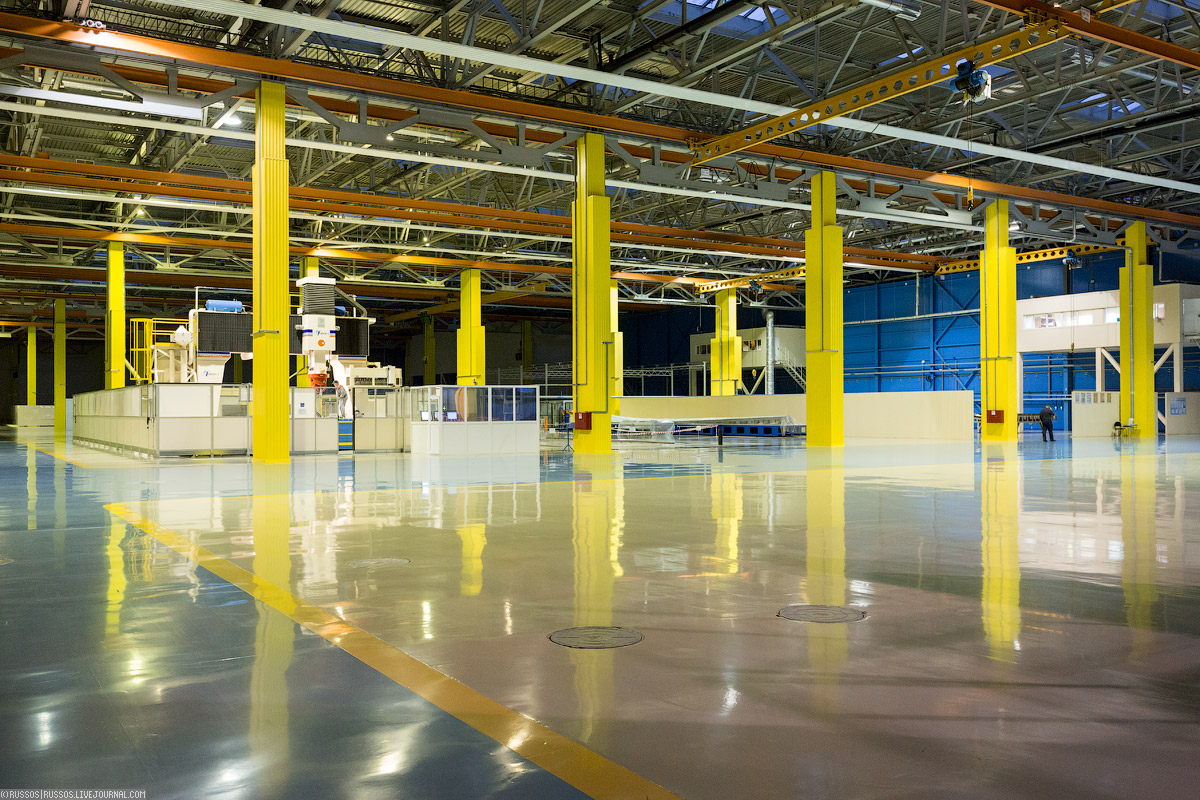
2. Участок автоматической выкладки. На переднем плане панель консоли крыла, на заднем — лонжерон.
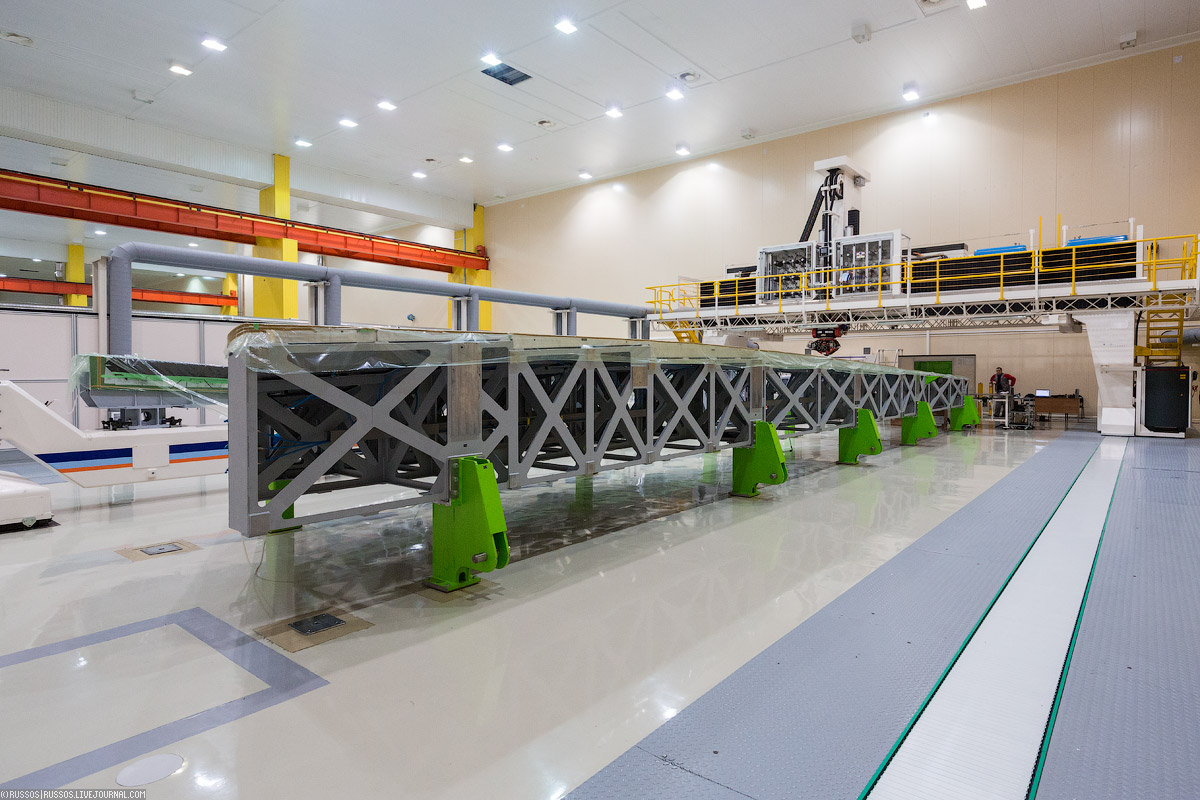
3. Выкладка лонжерона крыла шестимиллиметровой углеродной лентой.
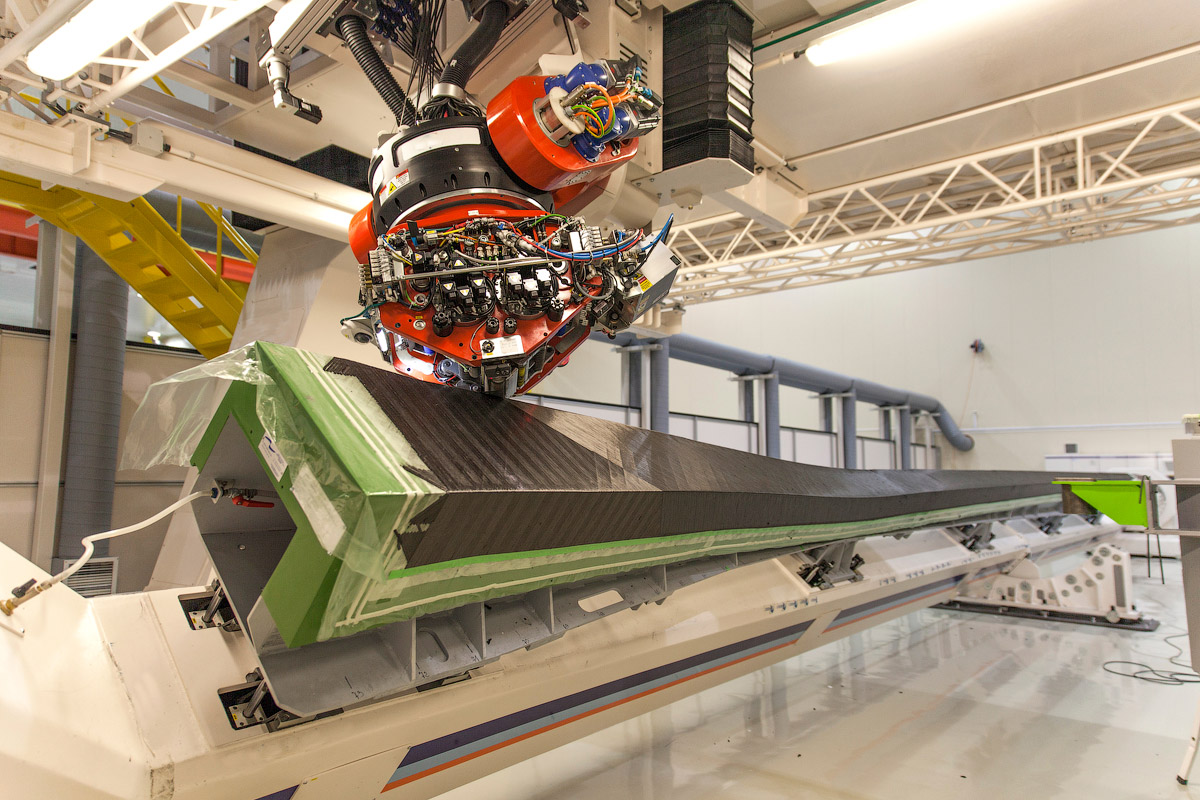
(с) фото пресс-службы АэроКомпозита.
4. Выложенные первые два слоя панели-спутника. Вся работа по подготовке основных и технологических материалов, выкладка углеродной ленты, а также сборка вакуумного мешка, проводится в помещении с контролируемыми параметрами — в так называемой «чистой комнате». Специальная система кондиционирования обеспечивает здесь поддержание заданных нашей технологией параметров температуры и влажности воздуха, атмосферного давления. Здесь недопустимо, чтобы в воздухе витали даже мельчайшие дисперсные частицы. Чистота этого помещения площадью 11 тысяч квадратных метров вполне сопоставима с чистотой больничных операционных.
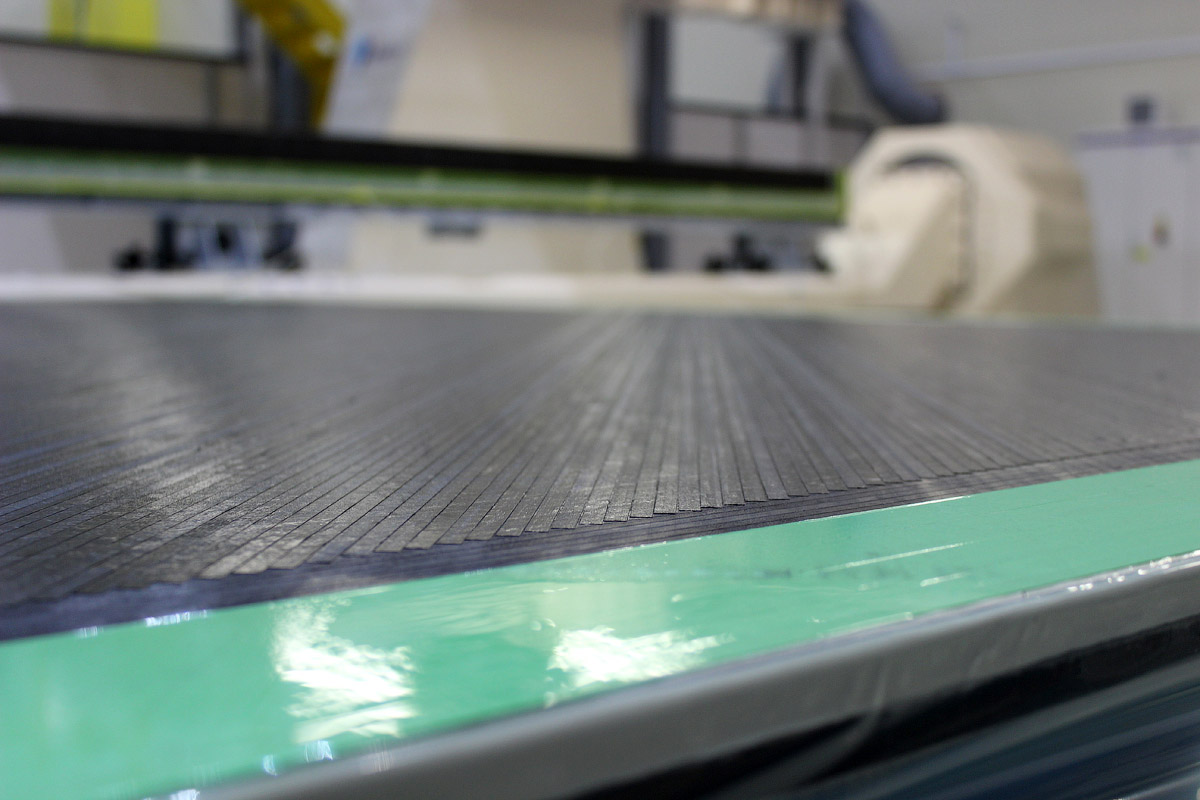
(с) фото пресс-службы АэроКомпозита.
5. Визуальный контроль выложенных слоев.

(с) фото пресс-службы АэроКомпозита.
6. Система перемещения преформ панелей консоли крыла (слева) и система переворота преформ лонжеронов (справа).
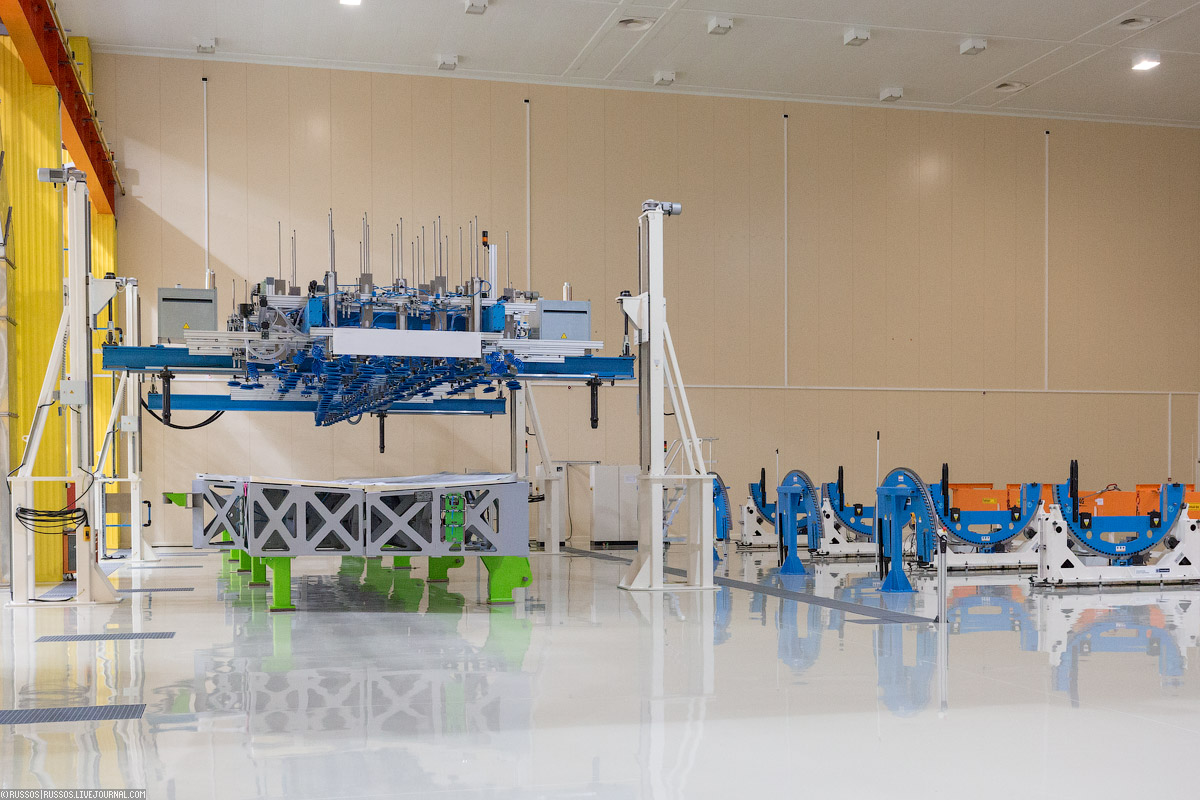
7. Присоски.
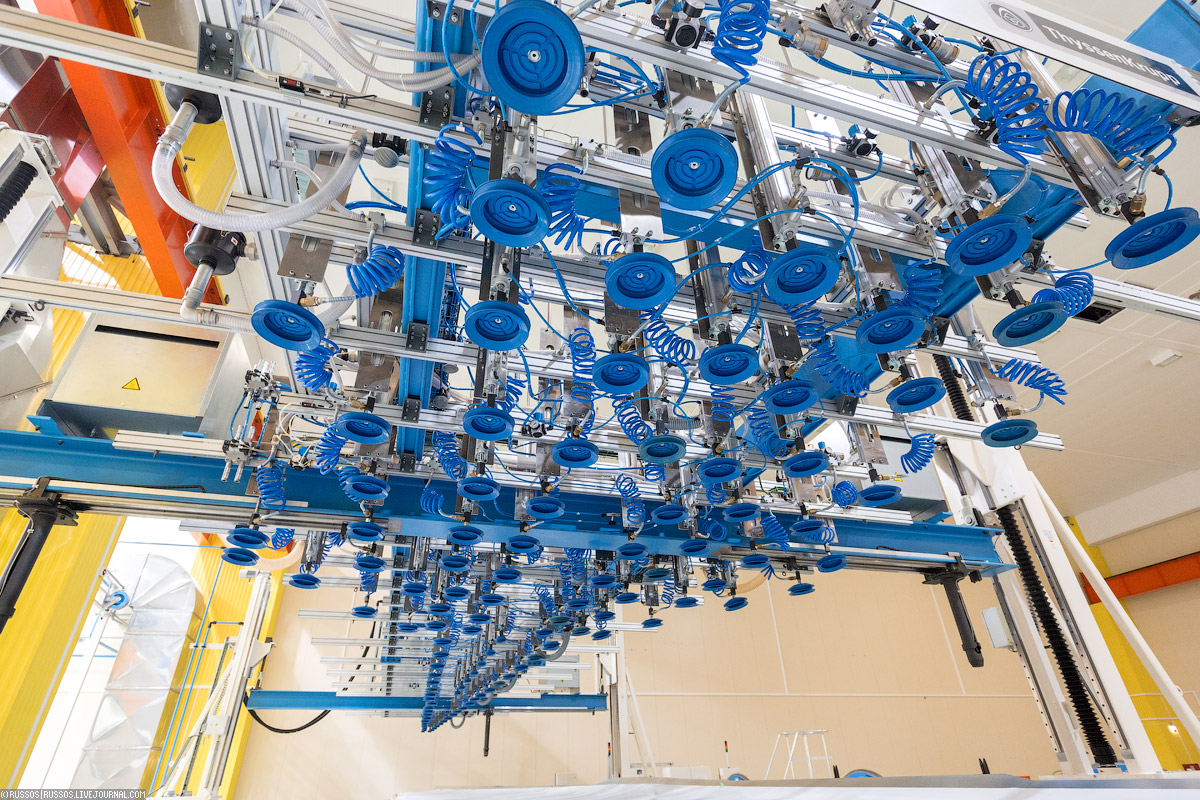
8. Полученная «П»-образная преформа разрезается. Получается два «Г»-образных профиля, которые складываются в «Т»-образный. На фотографии стрингер установлен в проектное положение, зафиксирован в стапеле и в таком виде монтируется на обшивку панели консоли крыла.
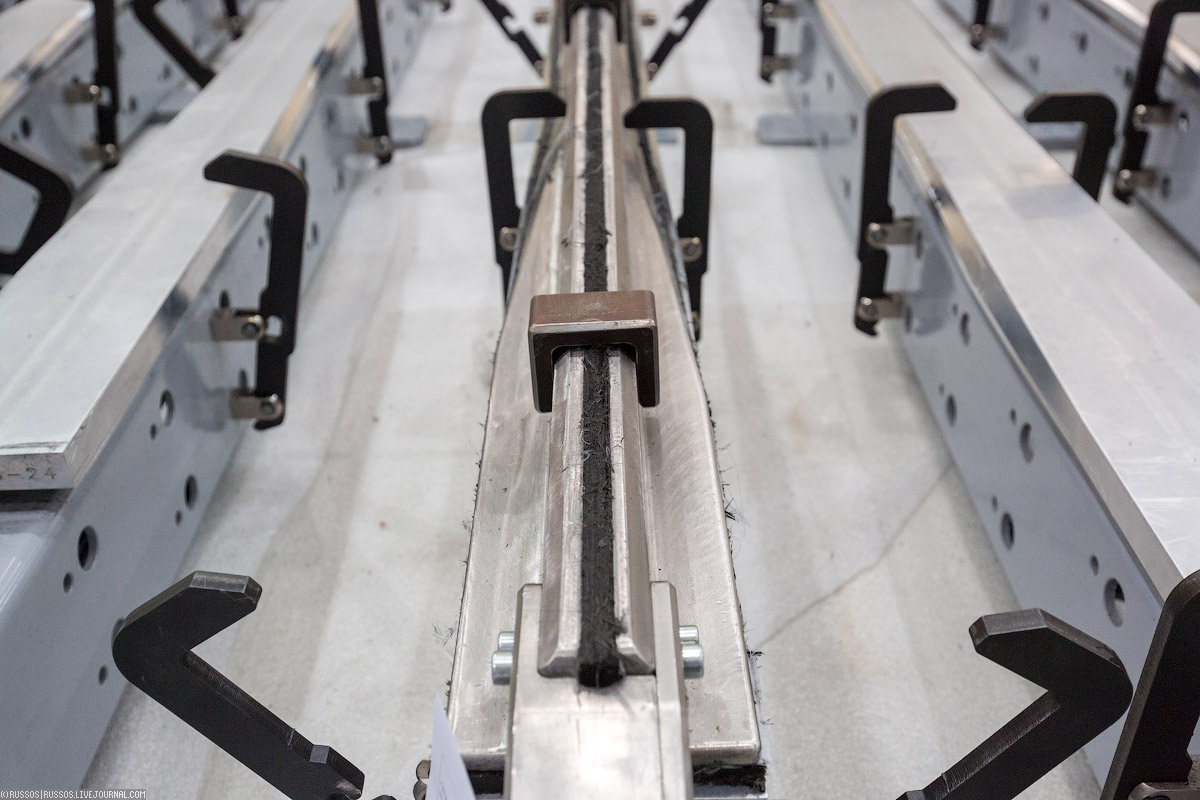
9. Участок выкладки на панель консоли крыла подготовленных стрингеров.
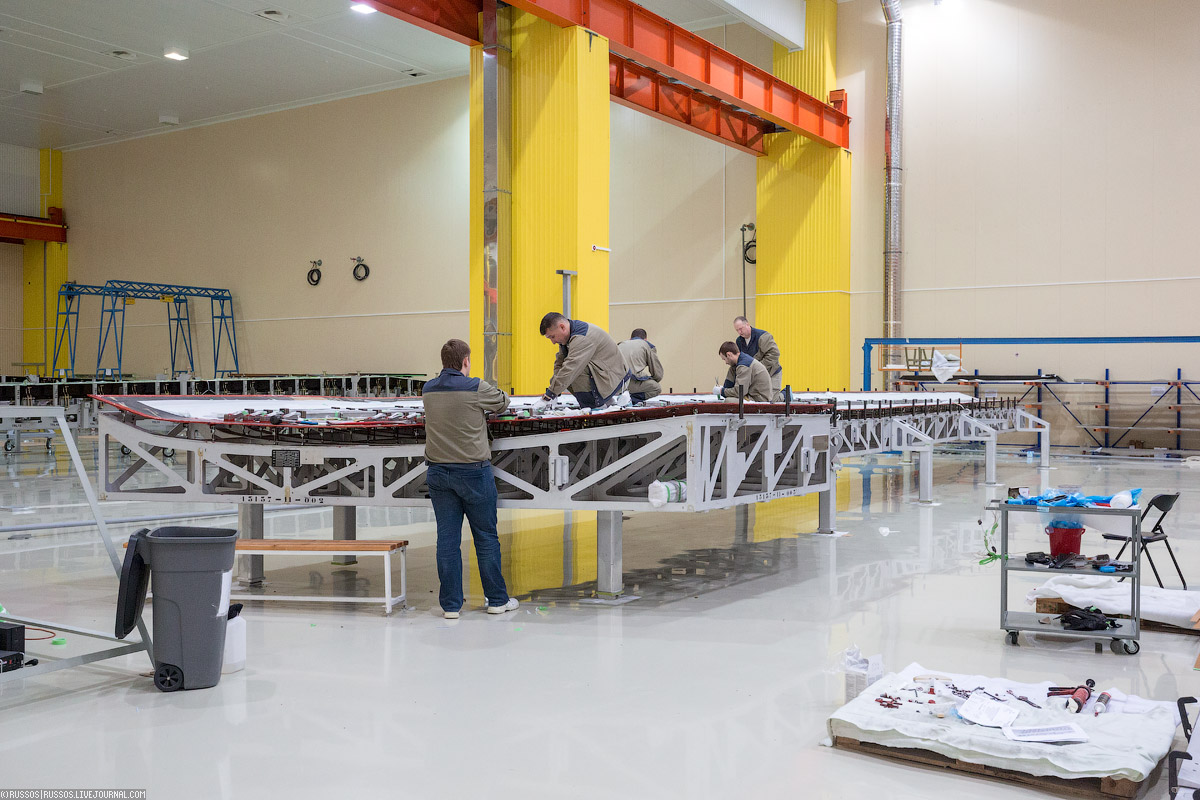
10. Термоинфузионный центр. Формуется все при небольших температурах. Одновременно можно изготавливать несколько изделий. Совместно с длинномерными элементами «поджариваются» и панели-спутники, так называемая, «уменьшенная копия», которая проходит все этапы изготовления параллельно с основным изделием. Спутник предназначен для того, чтобы провести на нем все испытания по контролю качества основного изделия. Так как спутник изготавливается вкупе с самой деталью, в аналогичных условиях и по абсолютно точным параметрам, он является аналогом этой детали. Затем панель-спутник отправляется в испытательную лабораторию, где из нее нарезают около 600 образцов-свидетелей, каждый из которых проверят «на прочность». Специалисты проведут испытания на разрыв, на сжатие и на сдвиг.
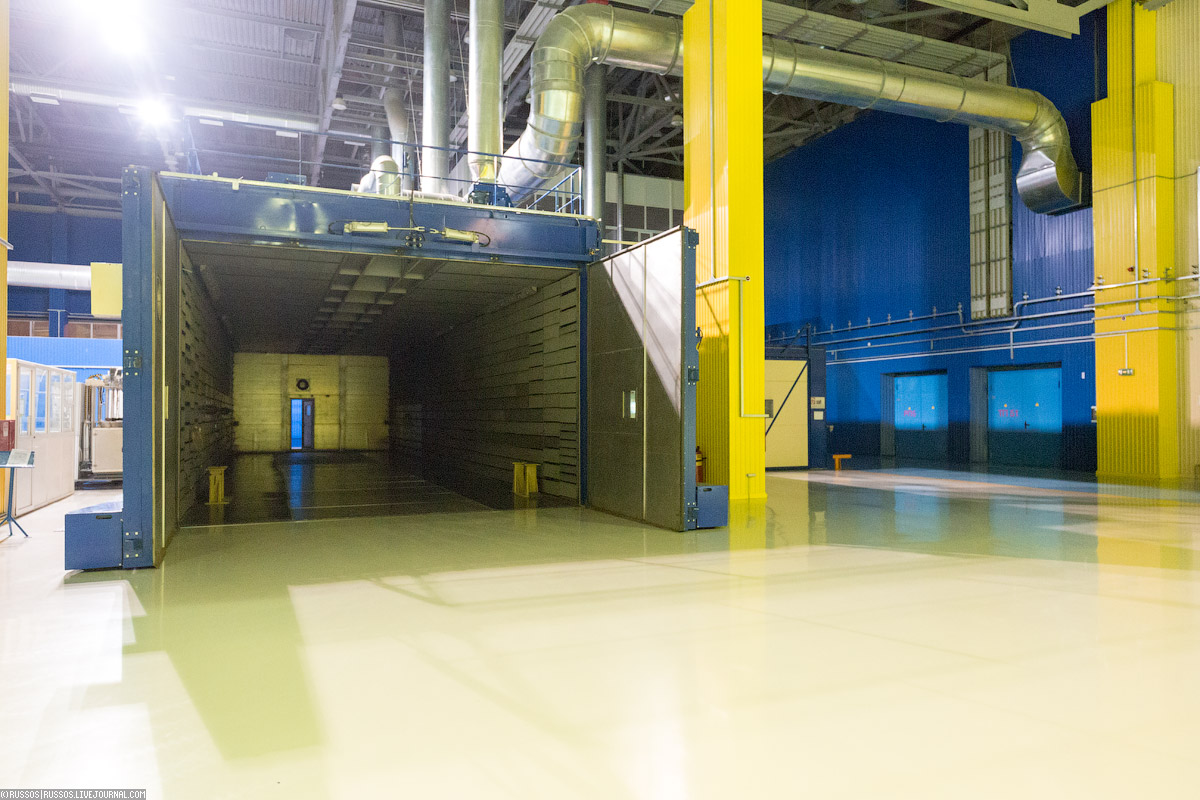
11. На снимке монолитные элементы после выхода из термоинфузионного центра. Слева — панель консоли крыла. Справа — панель центроплана.
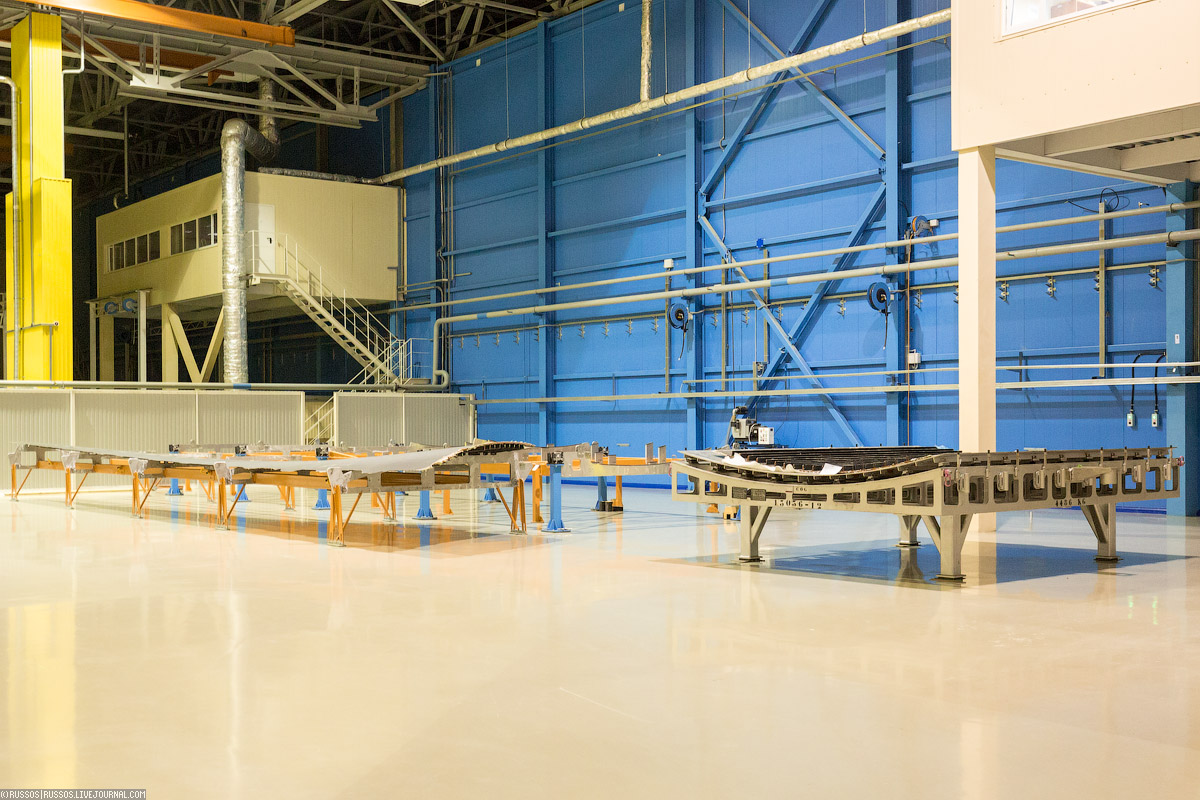
12. Заместитель начальника композитного производства Павел Дягилев рассказывает об особенностях технологического процесса. Рядом с ним — композитная панель консоли крыла самолета перед механической обработкой. Это длинномерный монолит.
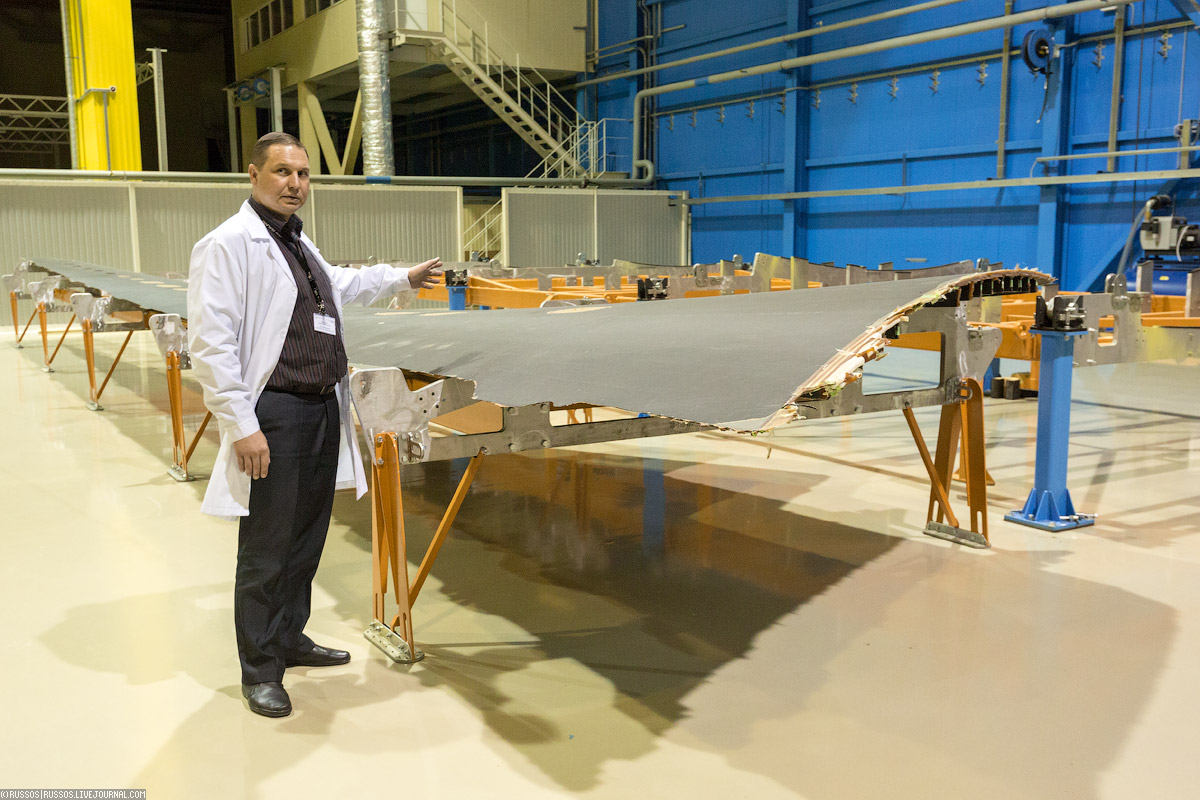
13. Пятикоординатный фрезерный центр позволяет выполнять механическую обработку как мелких, так и крупногабаритных изделий (18 метров в длину) сложной геометрии.
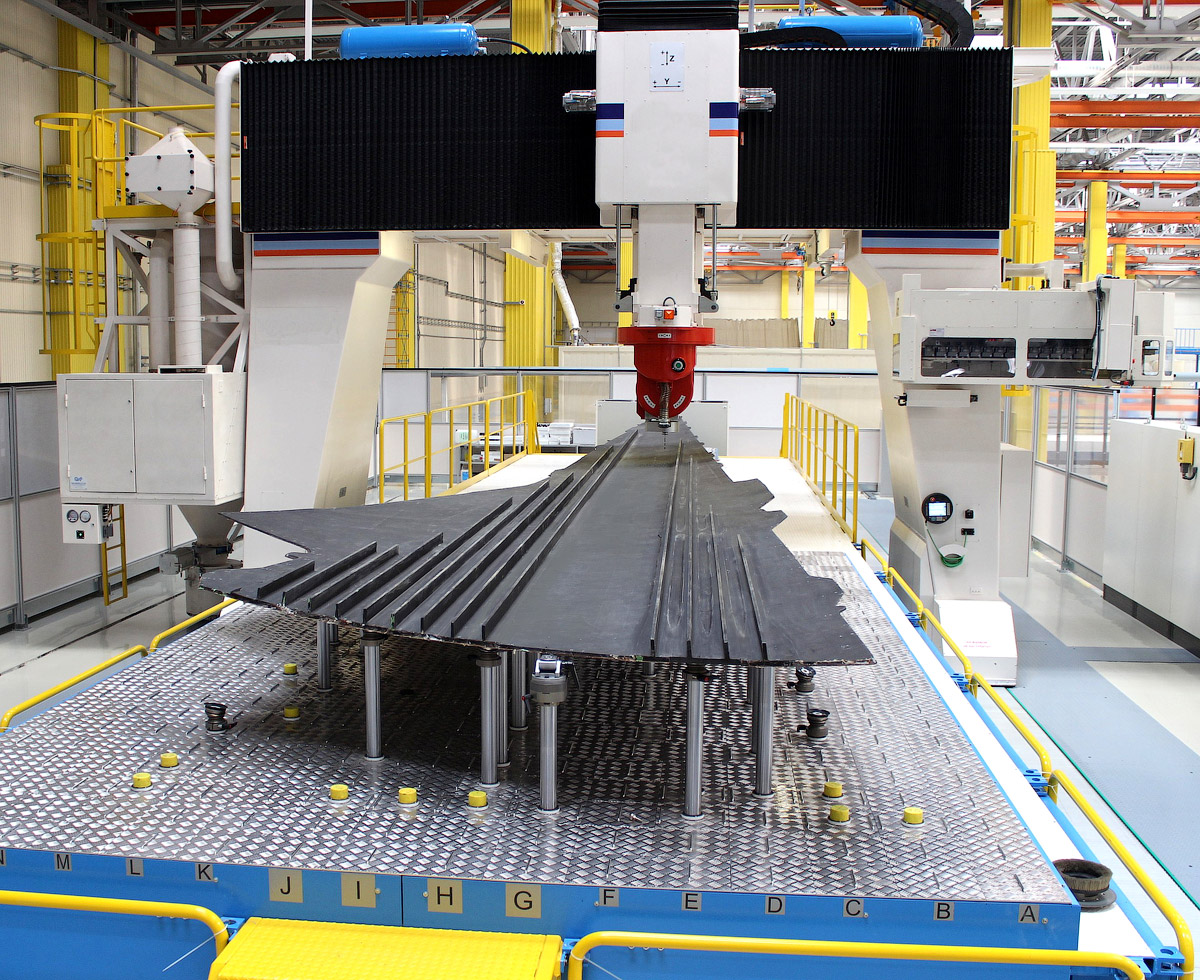
(с) фото пресс-службы АэроКомпозита.
14. Верхняя панель консоли крыла и лонжерон на участке проведения неразрушающего контроля.
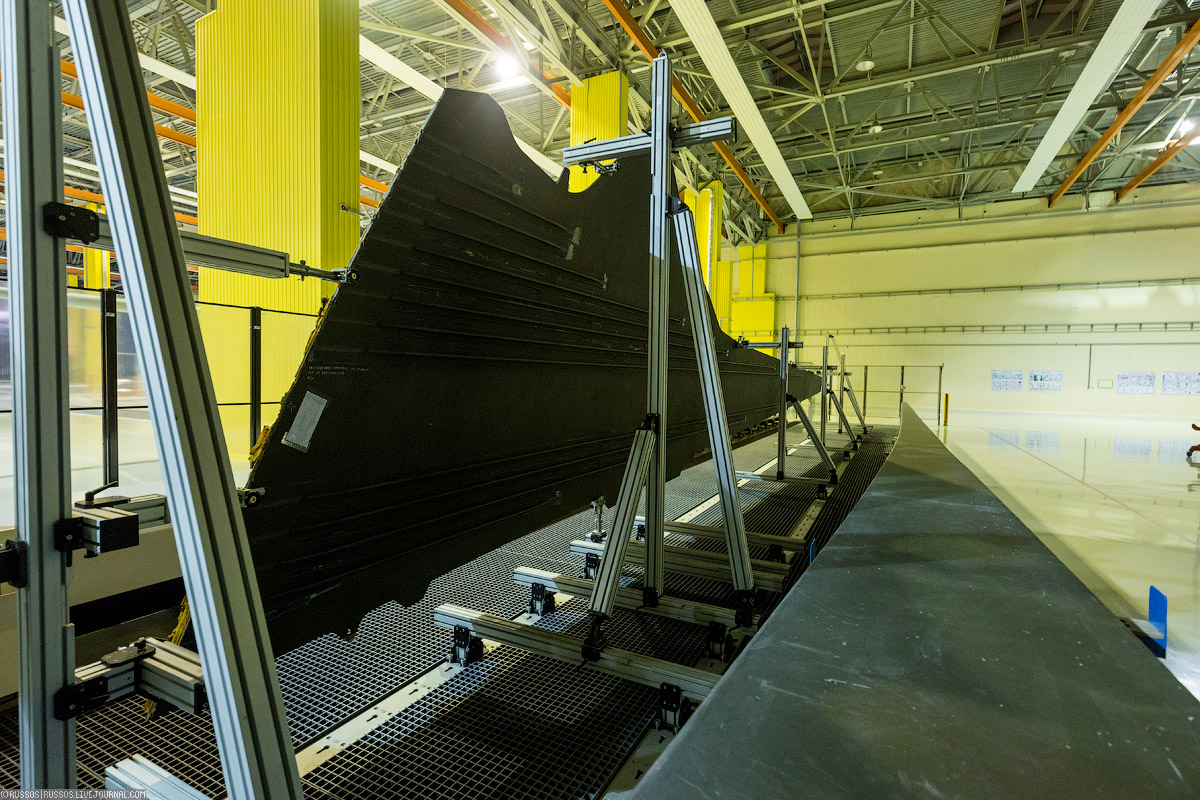
15. Ультразвуковое исследование лонжерона крыла.
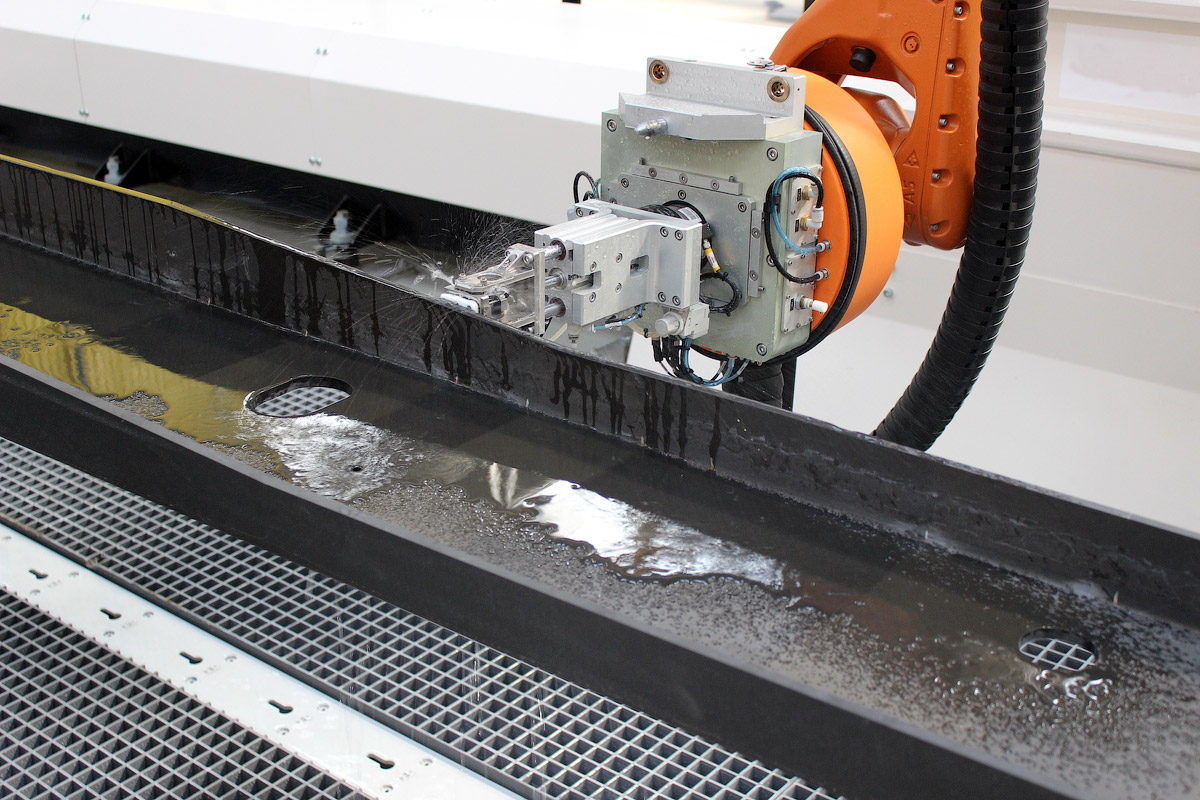
(с) фото пресс-службы АэроКомпозита.
16. К сожалению, когда я там был, готовые консоли крыла были уже доставлены на Иркутский авиационный завод, где полным ходом идет сборка первого самолета МС-21. Но сборочный участок и станции впечатляют.
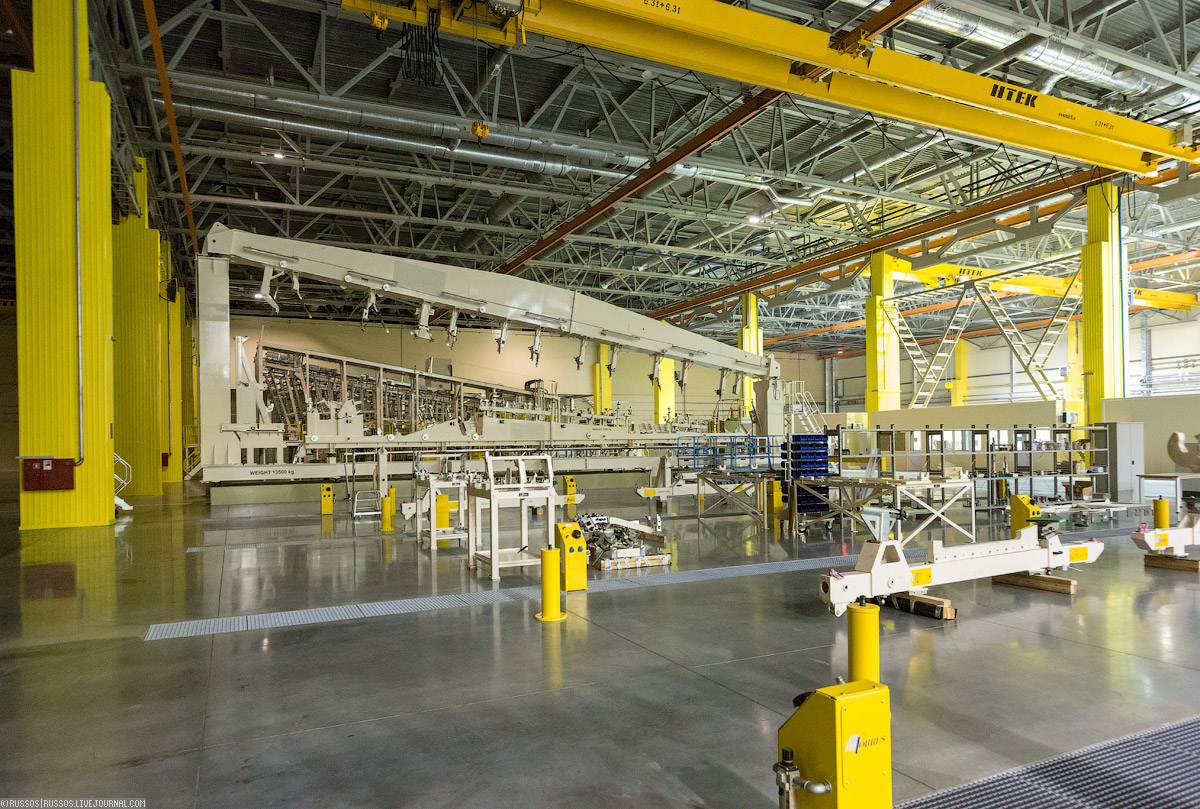
17. Две панели центроплана на сборочной станции.
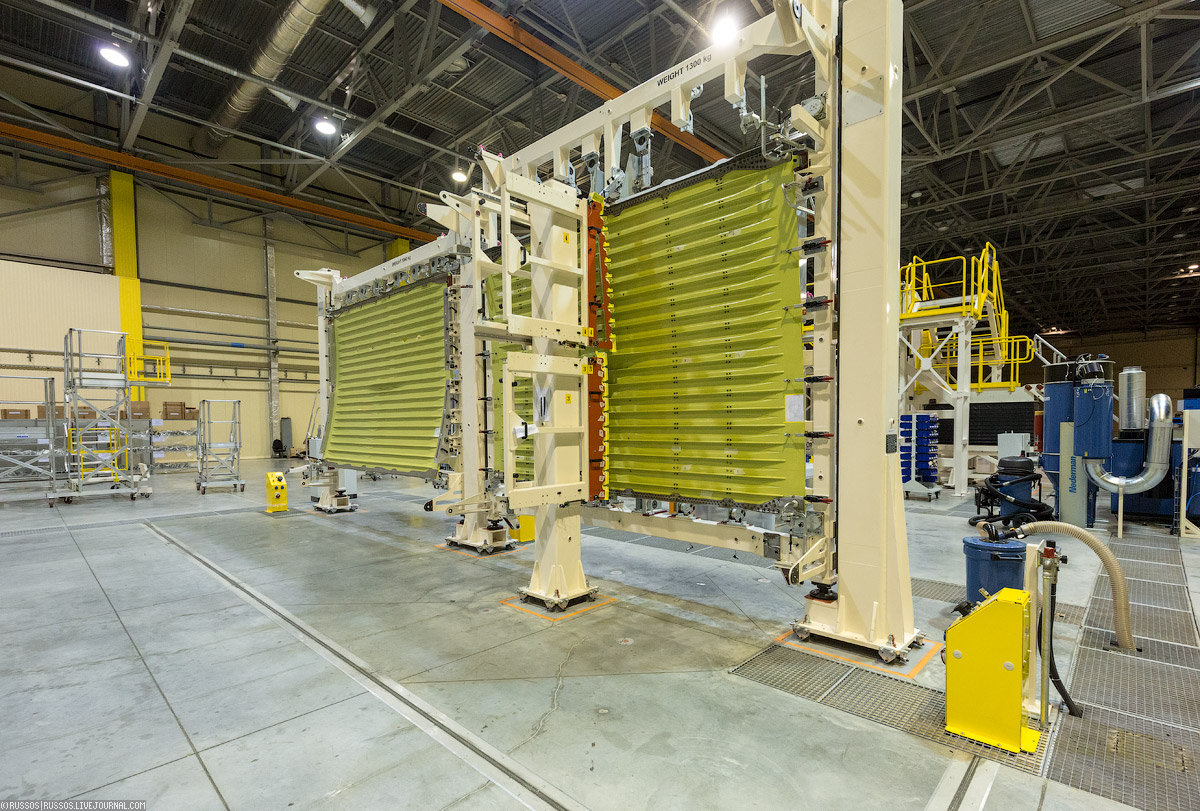
18. Установка компенсаторов нервюр. Они соединяют обшивку с нервюрами и позволяют обеспечить заданную форму профиля поверхности.
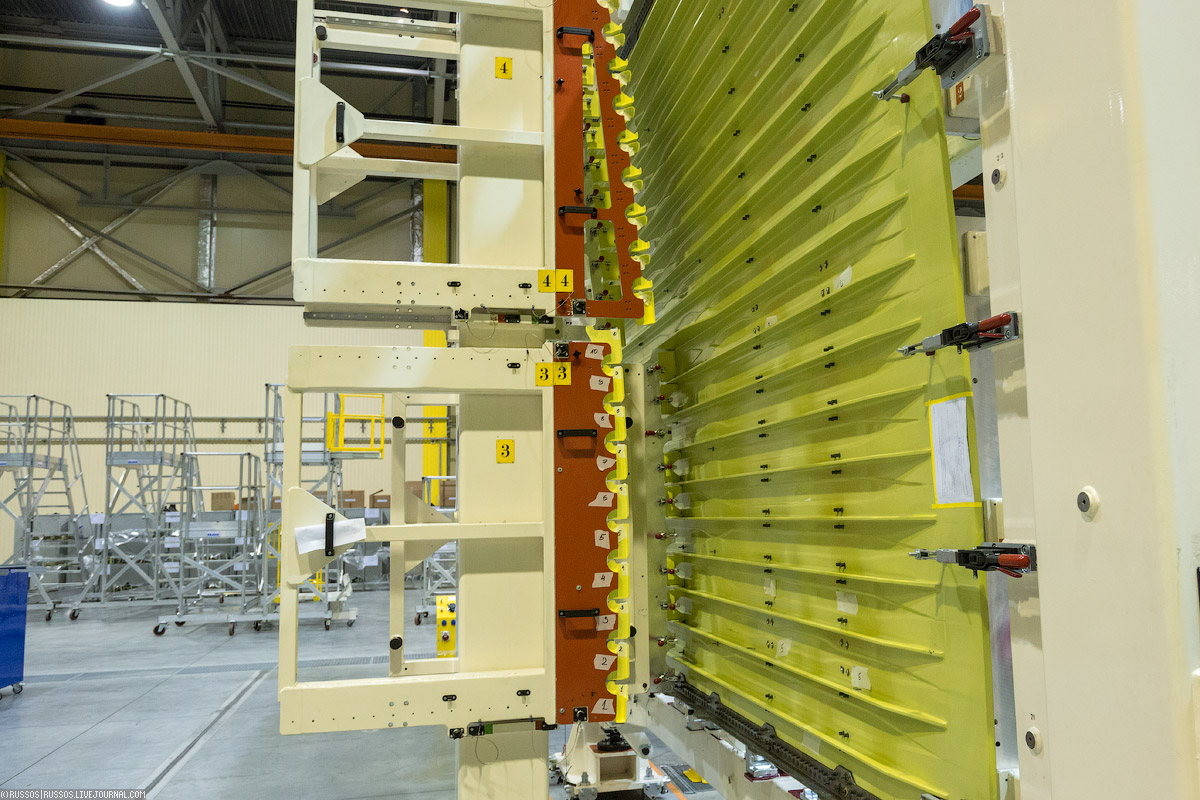
19. На предприятии готовятся к установке стенда для предварительной стыковки консолей крыла лайнера с центропланом.
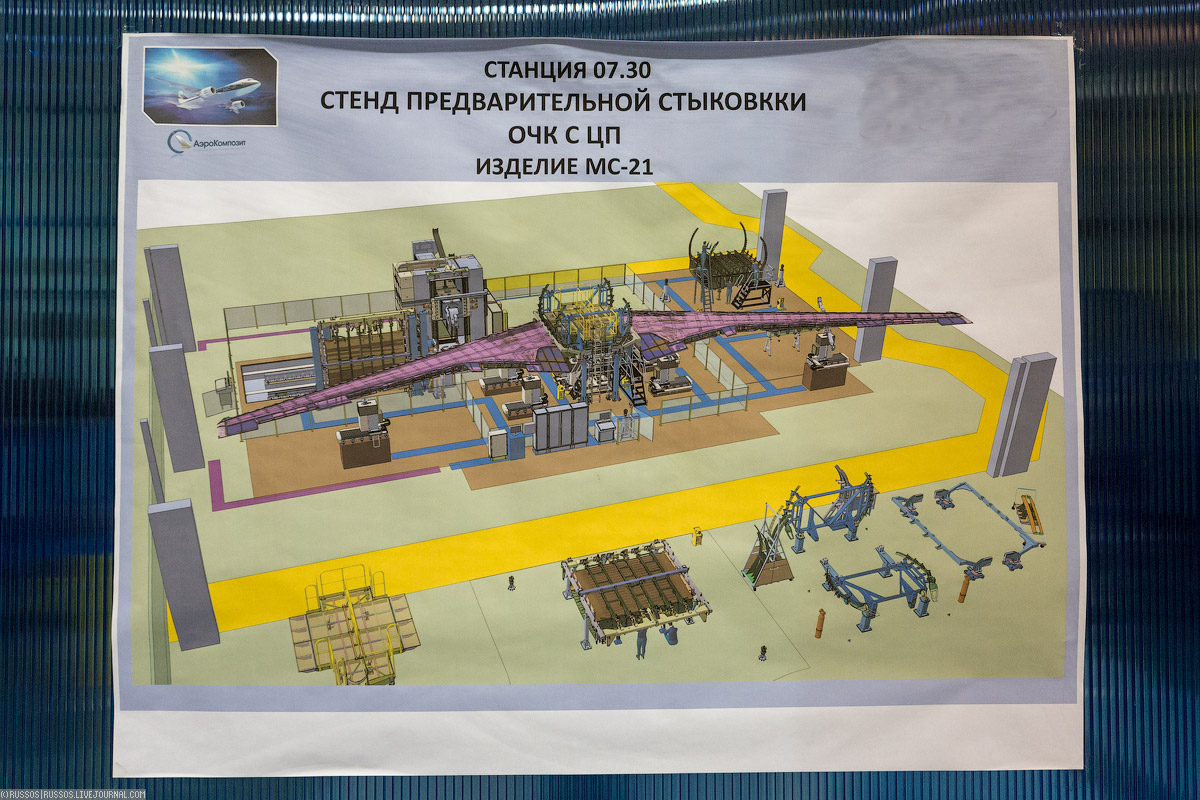
20. Рядом собирают предкрылки консоли крыла.
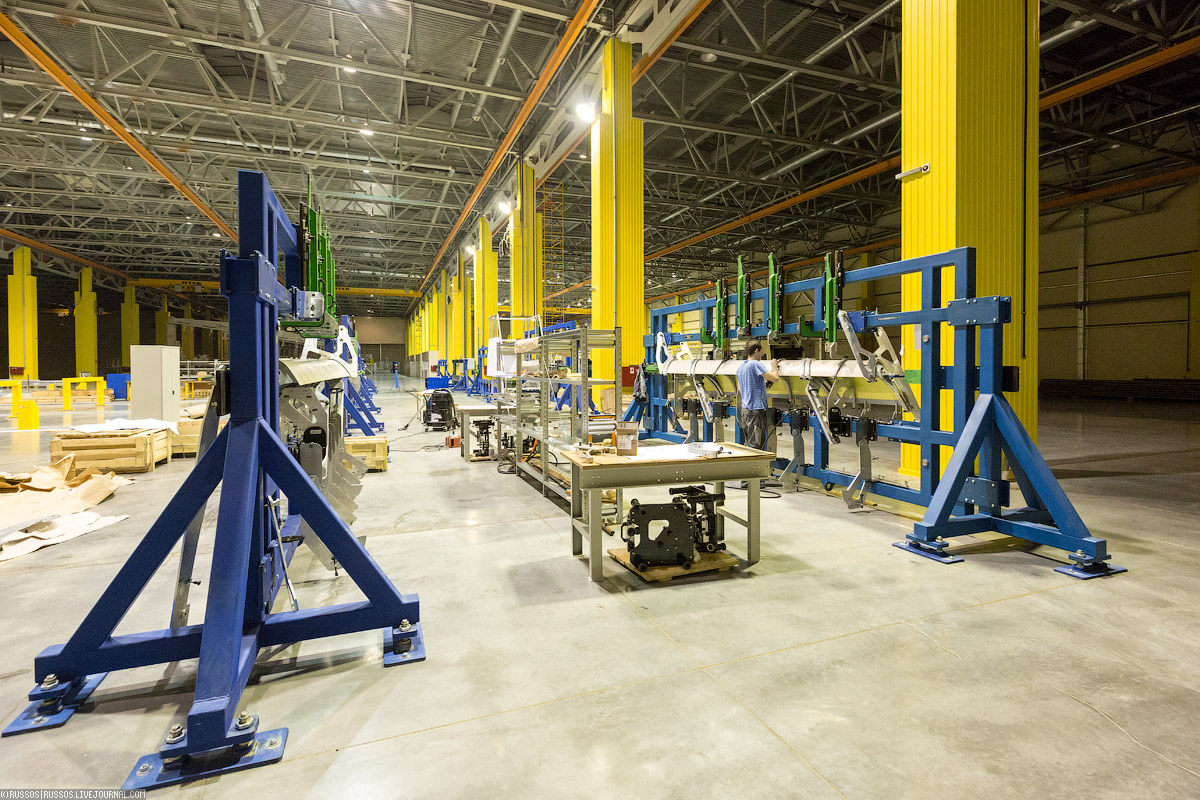
Друзья, первый полет МС-21 уже почти реальность. Он должен состоятся уже в этом году. Да даже, если в следующем — это будет грандиозное событие в отечественном авиастроении.
Огромное спасибо сотрудникам компании «АэроКомпозит» за помощь в подготовке материала.
Взято: bmpd.livejournal.com
Комментарии (0)
{related-news}
[/related-news]